Contents
AISI 4330 Alloy Steel | UNS J24045 | AMS 6411 Supplier
- John
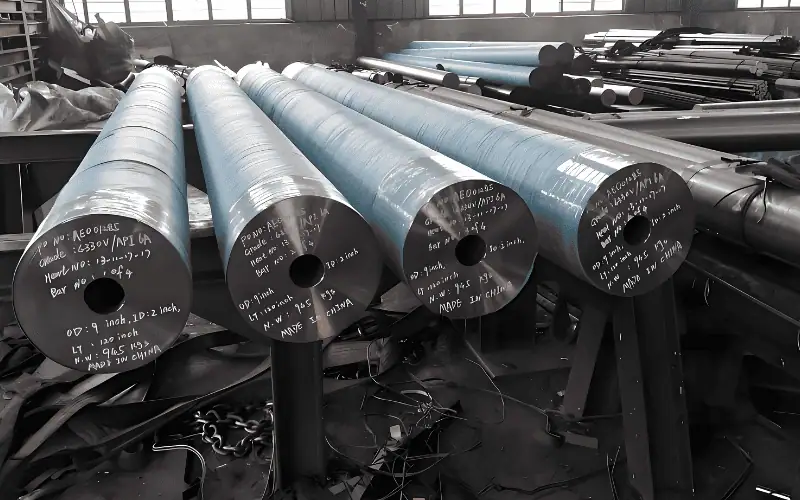
4330 steel is used in jet engine components, deep oil drilling, and heavy machinery, offering exceptional strength. At SteelPro Group, we have spent decades refining this alloy to provide precision-engineered solutions that excel under extreme conditions.
This guide will explore 4330 steel’s unique combination of toughness, machinability, and fatigue resistance. We’ll also highlight how our ISO-certified processes turn raw alloy into reliable, mission-critical components.
What Is AISI 4330 Steel?
AISI 4330 steel is a high-strength, low-alloy steel engineered to thrive in extreme mechanical and thermal environments. Classified under AMS 6411, it combines chromium, nickel, and molybdenum to deliver:
- Structural Resilience: Tensile strengths up to 1,380 MPa (200 ksi) after heat treatment.
- Impact Resistance: Nickel-enhanced toughness for shock absorption in subzero conditions.
- Fabrication Flexibility: Cold-work compatibility and weldability are rare in high-strength alloys.
Unlike generic steels, 4330’s optimized carbon content (0.28–0.33%) balances hardenability with reduced quench cracking risks. At SteelPro Group, we refine this alloy into components for aerospace actuators, offshore drilling tools, and high-stress automotive systems—where failure tolerance is zero.
4330 Steel Chemical Composition
Elements | Content |
Iron (Fe) | Balance |
Nickel (Ni) | 1~1.5% |
Manganese (Mn) | ≤ 1.0% |
Silicon (Si) | ≤ 0.80% |
Chromium (Cr) | 0.40~0.60% |
Molybdenum (Mo) | 0.30~0.50% |
Carbon (C) | 0.20~0.30% |
4330 Steel Mechanical Properties
Properties | Metric | Imperial |
Tensile strength | ≥ 860 MPa | ≥ 125000 psi |
Yield strength | ≥ 690 MPa | ≥ 100000 psi |
Elongation at break (In 50 mm) | ≥ 15.0 % | ≥ 15.0 % |
Hardness, Brinell | 285 | 285 |
4330 Steel Physical Properties
Properties | Metric | Imperial |
Density | 7.85 g/cm³ | 0.284 lb/in³ |
Melting Point | 1425°C | 2600°F |
Thermal Conductivity | 42 W/m·K | 24 BTU·in/h·ft²·°F |
Coefficient of Thermal Expansion | 11.5 µm/m·K | 6.39 µin/in·°F |
4330 Steel Applications
AISI 4330 steel’s synergy of strength, fatigue resistance, and adaptability makes it indispensable across industries where failure is catastrophic. Key applications include:
- Aerospace Actuators & Landing Gear: Withstands repeated high-impact loads in aircraft retraction systems (AMS 6411 compliant).
- Oil & Gas Drill Collars: Resists bending and torsional stress in directional drilling at depths exceeding 3,000 meters.
- High-Performance Automotive: Crankshafts, drive shafts, and suspension components for racing and heavy-duty vehicles.
- Hydraulic Fracturing Tools: Manages cyclic pressures up to 15,000 psi in fracking pumps and valve bodies.
- Defense Systems: Armored vehicle components and artillery parts requiring ballistic impact resistance.
4330 Steel Product Forms and Size
Our AISI 4330 steel is supplied in versatile forms to meet rigorous industrial demands, adhering to globally recognized specifications. SteelPro Group offers the following product configurations:
Product Type | Dimensions |
Round Bars | Diameter: 12mm–600mm (0.5″–24″)Length: ≤12m (40 ft) |
Flat Bars & Plates | Thickness: 6mm–250mm (0.25″–10″)Width: ≤3m (10 ft) |
Seamless Tubes | Outer Diameter (OD): 20mm–400mm (0.8″–16″)Wall Thickness: 3mm–50mm (0.12″–2″) |
Our 4330 steel is supplied in annealed, normalized, or quenched & tempered (Q&T) conditions, with customizable sizes available upon request.
4330 Steel Forging
AISI 4330 steel’s exceptional hardenability and ductility make it a top choice for high-integrity forged components. At SteelPro Group, we forge 4330 alloys within the optimal range of 982–1204°C (1800–2200°F) to refine grain structure and minimize residual stresses.
4330 Steel Heat Treatment
AISI 4330 steel’s performance hinges on precise thermal processing to balance strength, toughness, and fatigue resistance. SteelPro Group’s heat treatment protocols adhere to AMS 2759 and leverage decades of metallurgical expertise to optimize this alloy for critical applications:
1. Annealing
- Process: Full annealing at 816–899°C (1500–1650°F) followed by furnace cooling.
- Outcome: Reduces hardness to 200–230 HB, enhancing machinability for complex CNC operations.
2. Normalizing
- Temperature: 899°C (1650°F) for grain refinement before hardening.
- Benefit: Uniform microstructure ideal for components requiring isotropic mechanical properties.
3. Quenching
- Austenitizing: Heated to 829°C (1525°F) to dissolve carbides.
- Medium: Rapid oil quenching achieves martensitic transformation with minimal distortion.
4. Tempering
- Low-Strength Applications: 454–635°C (850–1175°F) for 125–200 ksi tensile strength.
- High-Strength Applications: 218–260°C (425–500°F) for 260–280 ksi tensile strength.
- Critical Note: Avoid 220–260 ksi ranges to prevent impact strength degradation.
5. Case Hardening (Optional)
Carburizing or nitriding to surface hardness ≥60 HRC for wear-prone components like gears or valve seats.
At SteelPro Group, our digitally controlled furnaces and cryogenic stabilization systems ensure repeatable results for 4330 steel—whether producing drill collars for sour gas wells or aerospace actuators demanding >1,000 MPa fatigue endurance.
4330 Steel Process
Machinability
4330 steel achieves optimal machinability in annealed or normalized states (200–230 HB).
Welding Performance
4330’s weldability outperforms many high-strength alloys but demands strict protocols:
- Preheat/Post-Heat: Mandatory for sections >25mm to avoid hydrogen cracking (150–200°C / 302–392°F).
- Critical Joints: Post-weld tempering at 595°C (1103°F) ensures fracture toughness in offshore rig components.
Hot & Cold Work
- Cold Forming: Ideal for bolts, pins, and flanges via cold heading (≤30% reduction) or drawing.
- Hot Work Limitation: Rarely applied due to 4330’s superior cold workability; reserved for oversized blanks (>500mm diameter).
Precision-Engineered 4330 Steel Solutions
At SteelPro Group, we don’t just supply 4330 steel—we engineer resilience. Our vertically integrated facility transforms raw alloy into mission-critical components trusted by aerospace OEMs, energy giants, and defense contractors.
Whether you are retrofitting offshore rigs or prototyping hypersonic vehicle components, our metallurgists and engineers partner with you to optimize 4330 steel’s performance—balancing strength, weight, and lifecycle costs.