Contents
Coating Defects Of Galvanized Steel: Types And Solutions
- John
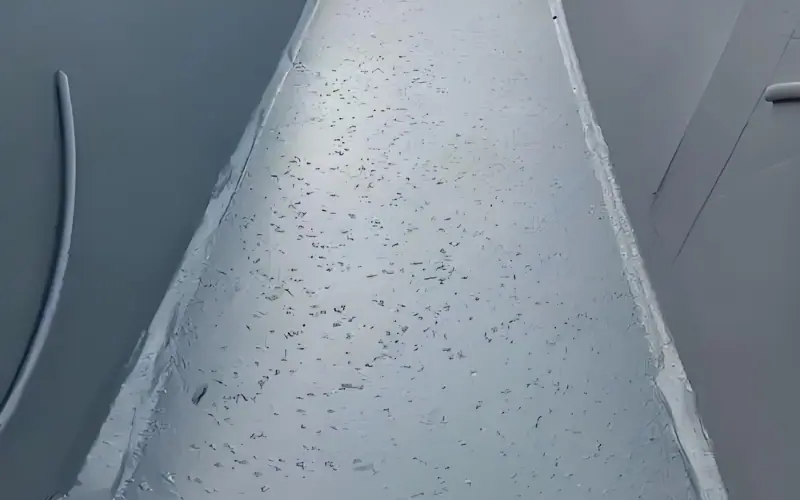
The primary purpose of galvanizing is to provide a durable, corrosion-resistant coating that extends the life of steel in challenging environments. However, despite advancements in galvanizing technology, coating defects can still occur.
This article delves into the common coating defects observed in various galvanized layers, shedding light on their causes and practical solutions.
Common Galvanizing Defects
In galvanized steel, coating defects range from minor aesthetic issues to significant flaws that weaken performance. Below, these defects are categorized based on their impact on appearance and functionality.
Acceptable Defects
- Weld-Area Discoloration
- Ash Staining
- Dull Gray or Mottled Coatings
Unacceptable Defects
- Bare Patches
- Black Spots
- Zinc Drip Defects
- Dross Pimples/Inclusions
- Blisters and Pinholes
Surface Preparation Defects Of Galvanizing Coating
Bare Patches
Bare spots in galvanized coatings are areas where the steel surface lacks a proper coating or has a skinny layer. These defects compromise the coating’s integrity and lower the material’s corrosion resistance.
Causes
Bare spots often result from inadequate surface preparation before galvanizing. Effective pre-treatment steps—like pickling, cleaning, and fluxing—are critical for coating quality. When the steel surface is not fully cleaned, oxides, rust, or other residues can block the coating from adhering, resulting in uncoated or thinly coated patches.
Preventive Measures
- Maintain strict control over pre-treatment steps like pickling and fluxing to ensure all contaminants are removed, allowing for uniform coating adhesion.
- Inspect the steel surface to catch any potential contamination or imperfections before coating.
Black Spots
Black spots appear as dark or black patches on the coated steel surface. These spots can impact both the appearance and the corrosion resistance of the coating, as they often indicate areas where zinc adherence is incomplete or inconsistent.
Causes
Black spots primarily result from issues with flux during the pre-treatment process. When flux residues remain on the steel surface due to insufficient rinsing or heating, they can react with zinc, leading to dark discolorations.
Preventive Measures
- Ensure complete flux activation by heating the steel to the correct temperature in the galvanizing bath.
- Rinse thoroughly after fluxing to remove any excess residue from the surface.
Weld-Area Discoloration
It is characterized by dark, often uneven discoloration that appears near welded areas. Although this staining does not necessarily affect the coating’s corrosion resistance, it does reduce the aesthetic quality of the galvanized finish.
Causes
Welding processes can leave behind chemical residues, such as flux or oxides, that react with the molten zinc during galvanizing. These reactions create darkened areas near the welds where the coating fails to form a uniform color.
Silicon and phosphorus are elements that accelerate the zinc-iron alloying process. Welds with high concentrations of these elements are more prone to dark staining as the galvanizing process produces excess alloy layers near the welds.
Preventive Measures
- Before galvanizing, it is essential to remove all residues from the weld, including flux, oxides, and other contaminants.
- Using low-silicon, low-phosphorus welding rods can reduce the likelihood of dark staining.
Zinc Drip Defects
Zinc drip defects appear as uneven zinc accumulations, often seen as drips, spikes, or puddles on the surface of galvanized steel. These irregularities create a rough, inconsistent finish that can impact both the appearance and handling of the product.
Causes
Zinc drip defects typically occur when excess zinc fails to drain properly from the steel surface after dipping. Poor positioning or inadequate drainage can cause zinc to collect in certain areas. Additionally, low bath temperatures can cause zinc to solidify too quickly, leading to spikes or thick spots before it flows off the steel.
Preventive Measures
- Position the steel at an optimal angle for drainage to ensure excess zinc flows off evenly.
- Maintain appropriate bath temperatures to allow proper zinc fluidity.
- Monitor and adjust dipping and lifting speeds to promote even coating distribution.
Process Defects Of Galvanizing Coating
Ash Staining
Ash staining appears as a dull, grayish residue or patches on the galvanized surface, giving it a less uniform and unclean appearance. This defect can affect the coating’s visual quality, although it usually does not compromise corrosion resistance.
Causes
Ash staining is caused by zinc oxide particles that form in the galvanizing bath when zinc reacts with oxygen. If these particles are not properly skimmed from the bath, they adhere to the steel surface during dipping, leaving a grayish stain. Excessive ash formation can result from high oxygen levels or poor bath maintenance.
Preventive Measures
- Regularly skim ash from the galvanizing bath to keep it free of zinc oxide particles.
- Control oxygen levels below 0.3% in the bath to reduce ash formation.
Dull Gray or Mottled Coatings
Dull gray or mottled coatings appear as inconsistent, patchy gray areas rather than a bright, even finish, impacting both appearance and uniformity.
Causes
Steel with elevated levels of silicon or phosphorus can react more quickly with zinc, leading to thicker, dull gray coatings.
Uneven cooling after galvanizing can also cause inconsistent textures in the coating. Rapid cooling may produce patches with different finishes, resulting in a mottled effect.
Preventive Measures
- Use low-silicon, low-phosphorus steel to minimize the reaction that causes dull coatings.
- Maintain consistent cooling rates to prevent uneven solidification and textural variation.
Dross Pimples/Inclusions
Dross pimples or inclusions appear as small, rough bumps or raised spots on the galvanized surface. These imperfections are caused by solid particles embedded in the zinc coating, giving it a coarse, uneven texture.
Causes
Dross in the galvanizing bath, formed by zinc-iron compounds, can lead to inclusions if not managed properly. Excessive movement or agitation during dipping stirs up dross particles from the bottom of the bath. As these particles accumulate in the bath, they embed within the coating, creating rough, raised spots known as dross pimples.
Preventive Measures
- Regularly filter the galvanizing bath to keep it free of zinc-iron particles.
- Maintain proper bath temperature to reduce dross formation.
- Minimize movement during dipping to prevent dross from settling on the surface.
Blisters and Pinholes
Blisters appear as raised bubbles, while pinholes are tiny holes in the galvanized coating. Both defects disrupt the smooth surface of the coating.
Causes
Blisters and pinholes often form due to trapped gases or moisture on the steel surface during galvanizing. When moisture or contaminants are present, they vaporize in the high heat, creating bubbles or holes as the zinc solidifies.
Preventive Measures
- Ensure thorough cleaning and drying of the steel surface before galvanizing to remove any moisture or contaminants.
- Control the dipping speed to allow trapped gases to escape gradually.
Peeling or Flaking
It appears as sections of the galvanized coating separating from the steel surface, leaving exposed areas vulnerable to rust. This defect weakens the coating’s adherence, compromising its durability and protective function.
Causes
This defect is primarily due to an overly thick coating or inadequate adhesion. Coatings that exceed 250 microns are prone to delamination, especially when subjected to impact. Additionally, products with a very smooth surface finish may prevent the zinc layer from adhering properly, increasing the likelihood of peeling.
Preventive Measures
- Ensure the coating thickness remains below the recommended 250-micron limit.
- Use pre-treatment methods to roughen overly smooth surfaces, enhancing zinc adhesion.
White Rust
White rust appears as a white, powdery substance on the surface of galvanized coatings, often forming in patches. This defect affects the coating’s appearance and, if left untreated, can gradually weaken the zinc layer’s protective quality.
Causes
White rust occurs when freshly galvanized surfaces are exposed to moisture or condensation before they have fully dried. The zinc reacts with water and oxygen to form zinc hydroxide, which appears as a white powder. This is common when galvanized items are stacked closely, preventing air circulation, or stored in humid conditions.
Repair Methods
- Clean the affected areas with a soft brush or cloth to remove the white rust.
- For mild cases, apply a diluted vinegar solution to neutralize and remove the white residue, then rinse with water.
- For severe cases, use a specialized zinc cleaner to restore the coating’s appearance.
Preventive Measures
- Allow freshly galvanized items to fully dry before stacking or storing them.
- Store galvanized products in a dry, well-ventilated area to reduce moisture exposure.
- Use protective covers during storage to prevent condensation from forming on the surface.
Premium Galvanized Coatings for Lasting Quality
Discover the unmatched quality of Steel Pro Group’s galvanized steel products. Our superior coatings provide reliable, long-lasting protection, with a range of surface finish options to meet your specific needs. Trust in our commitment to durability and appearance, ensuring every product not only performs but looks its best. For a tailored quote, click here.