Contents
How To Galvanize Steel? Different Methods Explained
- John
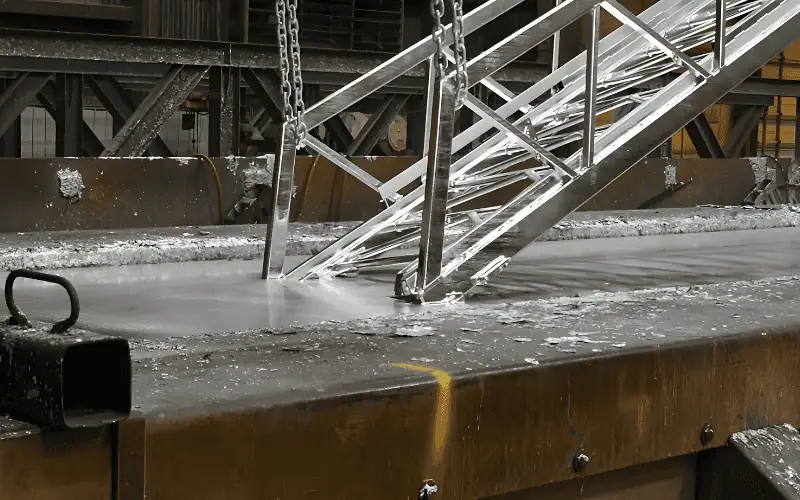
Galvanizing Steel can be done using various methods. Hot-dip galvanizing involves dipping steel into molten zinc for a thick, durable coating. Electro-galvanizing applies a fine, uniform layer of zinc through an electric current. Other techniques, like continuous galvanizing, sherardizing, and mechanical plating, offer unique benefits for specific applications.
This article will introduce each method and offer guidance on preparation work and post-treatment.
What Is Galvanization?
Galvanization is the process of adding a protective zinc layer to steel or iron to guard against corrosion. There are three main types of galvanizing: hot-dip galvanizing, electro-galvanizing, and galvannealing. Among these, hot-dip galvanizing is the most widely used due to its robust, long-lasting protection.
Preparation Before Galvanization
Degreasing or Cleaning
Steel parts are first immersed in a hot alkaline solution, often with added detergents, to break down and dissolve any contaminants. Organic solvents can be employed to remove tougher oils or grease.
After this cleaning, the steel is rinsed thoroughly with water to remove any remaining detergents or cleaning agents. This step is critical, as any leftover oils, greases, or residues could prevent the zinc coating from bonding effectively to the steel surface.
Pickling
Once the steel is clean, it goes into an acid bath, typically with hydrochloric or sulfuric acid. This pickling process removes rust, mill scale, and other oxides that may have formed on the surface.
During the process, the steel is closely observed to guarantee it is fully cleaned without risking any harm. A visual inspection follows to confirm that all rust and scale are fully removed, which is essential for strong adhesion of the zinc layer.
Rinsing
Immediately after pickling, the steel undergoes a complete rinse in clean water to wash away any residual acid. Sometimes, multiple rinses are performed to ensure no traces of acid remain on the surface.
Rinsing is vital in all galvanizing methods, as leftover acid could lead to coating defects or weaken the zinc layer, compromising the quality of the final product.
How Clean Does Steel Need to Be Before Galvanizing?
Steel needs to be thoroughly cleaned before galvanizing. All traces of oil, grease, dirt, rust, or any oxide layers on the surface need to be thoroughly eliminated. Even small traces of these contaminants can prevent the zinc from bonding properly, leading to uneven coating and weak spots.
Hot-Dip Galvanizing Process Steps
- Ensure the steel is completely clean by following degreasing, pickling, and rinsing procedures to remove any oils, rust, or scale.
- Allow the steel to dry fully, either through air drying or using a drying oven, to prevent any moisture from affecting the coating process.
- Dip the steel in a flux solution to remove any remaining oxides and to prevent oxidation before dipping in zinc.
- (Optional) Preheat the steel to a temperature close to the molten zinc bath to reduce thermal shock and improve the coating process.
- Lower the steel into a bath of molten zinc, heated to around 450°C (842°F). Ensure that the steel is fully submerged for an even coating.
- Keep the steel in the bath until the zinc fully bonds to the surface, forming a protective layer. This process takes several minutes depending on the thickness of the steel.
- Slowly lift the steel out of the bath, allowing excess zinc to drain back into the bath. Gentle shaking or vibrating may be applied to reduce excess zinc.
- Allow the steel to cool, either in air or by dipping it in a quenching solution, to harden the zinc coating and prepare it for handling.
- Check the galvanized steel for uniformity and coating thickness, ensuring it meets quality standards.
The Role of Fluxing
Fluxing is an essential step in hot-dip galvanizing. It typically uses zinc ammonium chloride as a flux solution to prevent oxidation before galvanizing. It allows the molten zinc to bond smoothly and uniformly with the steel, creating a reliable and consistent protective layer.
Electro-Galvanizing Process Steps
- Clean the steel thoroughly by degreasing, pickling, and rinsing to ensure the surface is free from oils, rust, or other contaminants.
- Prepare the electrolyte bath with a zinc salt solution like zinc sulfate or zinc chloride, adjusting concentration and temperature for optimal coating.
- Attach the steel to the negative terminal (cathode) of the power source and connect zinc anodes to the positive terminal (anode). Place them in the electrolyte bath for even distribution.
- Submerge the steel fully in the electrolyte bath, ensuring complete immersion for a uniform coating.
- Apply a direct current through the bath, allowing zinc ions to deposit onto the steel’s surface.
- Remove the steel from the bath, then rinse thoroughly to remove any electrolyte residue that could affect the coating.
- Dry the steel completely to finalize the coating and prepare it for inspection and handling. Inspect the zinc coating for evenness and thickness.
Galvannealing Process Steps
- Begin with hot-dip galvanizing by cleaning the steel, applying flux, and dipping it in molten zinc for a complete coating.
- Transfer the galvanized steel directly to an annealing furnace to begin the alloying process.
- Heat the steel in the furnace to around 500-550°C (932-1022°F) to allow the zinc and iron to react.
- Maintain the steel at this temperature to allow the zinc and iron to react, forming an alloyed layer.
- Remove the steel from the furnace and let it cool gradually in air or by controlled cooling methods.
- Inspect the surface for a smooth, matte finish, ensuring a uniform alloy layer that meets quality standards.
Other Galvanizing Methods
Sherardizing
Sherardizing, also known as vapor galvanizing, coats steel by heating it with zinc powder in a sealed, rotating drum. At high temperatures, the zinc vaporizes and bonds to the steel, forming a uniform, matte finish.
This method produces a tough coating that withstands abrasion well and offers moderate corrosion resistance, making it suitable for small, detailed components like bolts, nuts, and fasteners.
Mechanical Plating
Mechanical plating uses zinc powder and a tumbling process to coat steel surfaces. In this method, zinc adheres to the steel through friction and impact, without the need for high heat or electric currents.
It works well for precision components needing a controlled coating thickness without risking structural like screws, nails, and springs.
Spray Galvanizing
Spray galvanizing, also known as zinc metalizing, applies molten zinc to steel surfaces by spraying. It allows for adjustable coating thicknesses, providing flexibility in protection levels. This method is particularly effective for large structures or localized repairs where dipping is impractical.
Post Treatment In Galvanizing Processes
Passivation
Passivation is a process that adds a thin protective layer to the zinc-coated surface to enhance corrosion resistance. It helps prevent the formation of white rust, especially in humid environments.
It is commonly used for hot-dip galvanizing and electro-galvanizing.
Quenching
It is done by dipping the steel in water or a chemical solution immediately after galvanizing it to cool it quickly and harden the coating.
It is particularly common in hot-dip galvanizing to rapidly cool the thick zinc layer.
Oiling
It involves applying a light oil coating to the galvanized surface. This provides a temporary protective layer, preventing storage stains or surface corrosion during handling and storage.
It is more common in electro-galvanizing, where the thin zinc coating can be more susceptible to staining or scratches.
Coating or Painting
For enhanced corrosion resistance and aesthetic purposes, galvanized steel may undergo additional coating or painting.
This is often done with galvannealed steel, as its matte finish and iron-rich surface bond well with paints or other coatings.
Producing Perfect Galvanized Steel
SteelPRO Group excels in providing top-quality galvanized steel products, including galvanized steel coils (SGCC, DX51D) and galvanized steel sheets (Z275), all designed for superior durability and corrosion resistance.
Our galvanized products come in various sizes and specifications to meet your specific needs, whether it’s for construction, automotive, or industrial applications. With a commitment to precision, we ensure our materials arrive ready for immediate use.