Contents
Does Galvanized Wire Rust?
- John
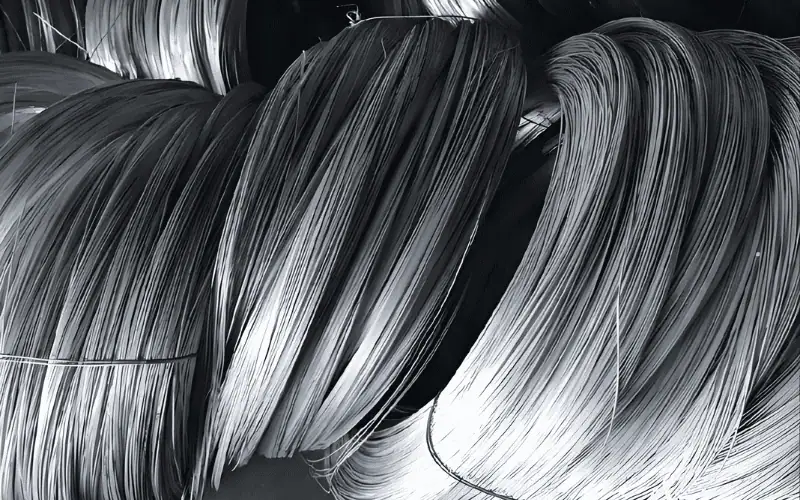
Yes, galvanized wire does rust, but it does so at a much slower rate than non-galvanized wire. The galvanized coating acts as a protective layer, reacting with oxygen and moisture before the steel rusts, thus delaying rusting. However, in harsh environments or when the coating is damaged, it will eventually rust on the underlying steel.
Why Does Galvanized Steel Wire Rust or Corrode?
The main reason galvanized wire rusts or corrodes is the breakdown of the protective zinc layer. While the zinc coating effectively shields the steel from oxygen and moisture, delaying corrosion, uneven coating, defects, or prolonged exposure to humid environments (such as coastal areas, industrial acid rain zones, and agricultural irrigation areas) can expose the steel to air, leading to oxidation and rusting.
How Long Before Galvanized Wire Starts to Rust?
The time before galvanized wire begins to rust depends on environmental exposure. In wet or highly corrosive areas, rust may appear in 3-10 years. In dry, controlled environments, rusting can be delayed for 50-100 years or more.
Environment | Description | Expected Time Before Initial Rusting |
Wet or Soaked | Constant water exposure (e.g., submerged or consistently wet areas) | ~5-10 Years |
High Humidity (100%) | Sustained 100% humidity (e.g., tropical regions, greenhouses) | ~15-34 Years |
Moderate Humidity (60-80%) | Humid but not saturated environments (e.g., temperate coastal areas) | ~20-50 Years |
Low Humidity (30-60%) | Dry climates (e.g., inland areas with moderate to low rainfall) | ~50-100 Years |
Very Low Humidity (<30%) | Arid or semi-arid regions (e.g., deserts, climate-controlled indoor spaces) | ~100+ Years |
Industrial Polluted Areas | Exposure to acid rain or pollutants (e.g., factories, high industrial regions) | ~10-20 Years |
Marine Coastal Zones | Constant salt exposure near oceans (e.g., coastal structures, piers) | ~3-5 Years |
Cold, Dry Environments | Cold climates with minimal precipitation (e.g., mountainous, alpine regions) | ~100+ Years |
Agricultural Irrigation Areas | Exposed to fertilizers and water spray (e.g., crop fields, greenhouses) | ~10-25 Years |
Causes of Galvanized Wire Rust
Galvanized wire rusts due to factors like zinc coating quality, environmental exposure, and handling. Recognizing these causes can help extend its lifespan.
1. Zinc Coating Thickness
- A thicker zinc coating offers better rust protection; 100-150 microns is recommended for high-corrosion areas.
- Thin coatings (<50 microns) wear down quickly, exposing steel to rust sooner.
- For moderate conditions, 50-85 microns generally provide sufficient protection.
2. Damage to the Zinc Coating
- Scratches or impacts expose steel, increasing rust risk by 20-30%.
- Protecting the zinc layer from physical damage is essential for corrosion resistance.
3. Environmental Factors
- Humidity and saltwater exposure accelerate rust, with corrosion rates up to 50% higher in coastal areas.
- Acid rain and industrial pollutants degrade zinc coatings faster, creating pathways for rust.
4. Quality of Galvanization
- High-quality galvanization can resist rust 2-3 times better due to uniform coating.
- Poorly applied coatings may peel, leaving steel exposed and susceptible to corrosion.
5. Time
- Over time, even thick zinc layers naturally wear down, allowing rust to eventually develop.
- In dry conditions, rust may take 50-100 years to appear, but in humid areas, initial rust may form in 10-20 years.
6. Chemical Reactions
- Fertilizers and chemicals accelerate rusting, reducing protection by 30-40%.
- Avoid storing galvanized wire near strong acids or alkaline substances, which quickly degrade zinc.
7. Wire Diameter
- Thicker wire diameters retain more zinc, slowing rust onset.
- Thin wires have less zinc and degrade faster; 12-16 gauge is generally more resistant than thinner gauges.
8. Contact with Dissimilar Metals
- Contact with metals like copper leads to galvanic corrosion, often doubling the rate of rust formation.
- Insulation between dissimilar metals is crucial in moist or corrosive settings, where zinc loss can increase by up to 50%.
How to Prevent Galvanized Wire from Rusting
Rust prevention for galvanized wire depends on a few critical practices. The wire’s lifespan can be extended by following protective measures, even in harsh conditions.
Choose a quality galvanized manufacturer
Opt for manufacturers like SteelPRO Group that uphold high standards to ensure the zinc coating adheres well, enhancing resistance to peeling and flaking over time.
Our hot-dip galvanized steel wire is specifically made to withstand demanding environments, offering reliable corrosion resistance and extended lifespan in applications like construction and agriculture.
Apply Protective Coatings and Use Corrosion Inhibitors
A protective coating, with a zinc thickness of 85-100 microns for regular use or 100-150 microns for high-corrosion areas, helps prevent rust.
Adding corrosion inhibitors provides an extra layer of defense, especially in humid or salty areas. Reapply coatings and inhibitors periodically in tough environments to maintain long-lasting protection.
Store in a Dry Environment
Keep storage areas dry, as humidity accelerates rusting. If outdoor storage is unavoidable, cover the wire well and use desiccants to absorb moisture in enclosed storage areas. Consider storing galvanized wire indoors whenever possible for environments with over 80% humidity to prevent premature corrosion.
Avoid Contact with Dissimilar Metals
Contact with metals like copper accelerates corrosion through galvanic reactions. Insulate between different metals to prevent this. In wet environments, design installations to keep galvanized wire separated from incompatible metals for optimal durability.
Minimize Mechanical Damage
Scratches or dents make galvanized wire vulnerable to rust, so gentle handling is key. Use padding during transport and avoid dragging to keep the coating strong.
Regular Maintenance and Inspection
Check the wire regularly, especially in tough conditions, and clean off dirt or chemicals that can speed up rust. A quick inspection can catch early wear and keep the zinc layer doing its job longer.
Select Appropriate Wire Diameter
For outdoor or heavy-duty uses, thicker wires (10-14 gauge) hold up better. They’ve got more zinc coverage, so they weather rough conditions longer than thinner wires—ideal for exposed setups.
Will Galvanized Wire Rust Outside?
Yes, the galvanized wire will rust outside eventually, but the zinc coating delays this process significantly. Rust develops faster if the coating is damaged or in harsh weather conditions.
How Long Will Galvanized Wire Last Outside?
Galvanized wire can last from 10 to 50 years outdoors, depending on humidity, salt exposure, and coating thickness. Coastal areas reduce lifespan, while dry environments extend it.
Application of Galvanized Wire in Corrosion-Prone Environments
Galvanized wire is built to endure corrosive environments where standard steel would quickly rust. Its zinc coating offers a strong barrier, making it ideal for applications exposed to moisture, salt, and chemicals. Here are key scenarios where galvanized wire performs well, even in tough conditions.
- Coastal and Marine Construction: Piers and docks, bridge reinforcements, sea wall ties, coastal scaffolding, marine rebar ties
- Agriculture in Fertilized or Humid Areas: Field fencing exposed to fertilizers, greenhouse frames in humid climates, trellises for vineyards with high chemical exposure, plant stakes in irrigated zones, livestock pens in damp environments
- Industrial Settings with Chemical Exposure: Wire mesh in chemical processing plants, conveyor belts for outdoor facilities, protective cable armoring for exposed equipment, filter screens in acid-prone areas, packaging ties in polluted or humid environments
- Outdoor Telecommunications Infrastructure: Guy wires for antenna masts in salt-rich air, signal towers near coastlines, cable supports for open-air lines, transmission structures in industrial zones
- Marine Applications: Mooring lines, fishing traps exposed to seawater, saltwater-resistant netting, dock railings, buoy anchors
- Electrical Installations in Humid or Chemical Environments: Cable shielding in high-humidity areas, grounding wire in marine or industrial settings, suspension wires for exterior use, conduit support near chemicals, transformer cores in outdoor substations
- Household Applications in Humid Outdoor Environments: Clotheslines in rainy regions, outdoor garden fencing, picture hanging wire for patios, rust-resistant storage baskets, curtain rods for patios
Galvanized Wire Manufacturer with Multiple Services
SteelPRO Group supplies galvanized wire in multiple formats—Coil, Spool, Rope, and Mesh—with finishes like anti-fingerprint and skin pass to meet diverse environmental needs. Our wire is available in gauges from 8 to 24 and comes in both hot-dip galvanized steel wire and electro-galvanized steel wire options. With multiple advanced plants and high-grade raw materials, we ensure efficient production, quick delivery, and reliable quality.