Contents
Does Carbon Steel Rust?
- John
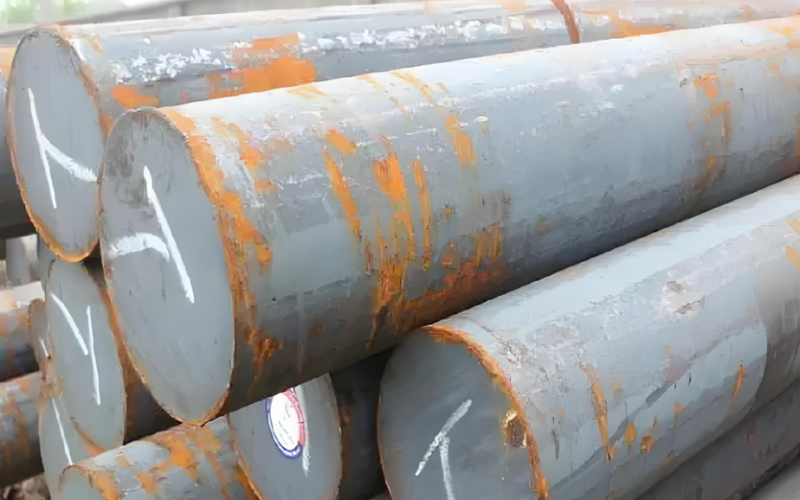
YES. One major drawback of carbon steel is its susceptibility to rust. Reading our article will help you understand why carbon steel rusts, how to prevent rust, and what metals or alloys are less likely to rust, helping you make informed decisions about the use and maintenance of the material.
What is Carbon Steel?
Carbon steel is a type of steel composed mainly of iron and carbon, with carbon content usually ranging from 0.02% to 2.1%, and its performance characteristics are optimized by adjusting the carbon content. However, carbon steel can also mean alloy steel except stainless steel.
Types of carbon steel
Low Carbon Steel (0.05% to 0.25% Carbon): Low carbon steel has good plasticity and toughness, but low strength. This steel is softer and easier to process, suitable for uses that require good weldability, such as building structures and automobile bodies.
Medium Carbon Steel (0.25% to 0.60% Carbon): Medium carbon steel has good overall properties, but poor weldability. This steel has high strength and hardness and is suitable for manufacturing mechanical parts and structural parts, such as bearings and gears.
High Carbon Steel (Over 0.60% Carbon): High carbon steel is very brittle and difficult to weld, but it has excellent hardness and wear resistance and is often used to produce high-strength parts like knives, tools, and springs.
Is Carbon Steel Rust Proof?
No, carbon steel is not rust-proof. Carbon steel is highly susceptible to rust and corrosion when exposed to moisture or humid environments because it lacks sufficient chromium content, which is necessary to form a protective oxide layer that prevents rust.
Does high carbon steel rust?
Yes, high carbon steel is susceptible to rust. Like other types of carbon steel, it lacks significant amounts of chromium (which is present in stainless steel), so it does not form a protective oxide layer to prevent rust. When exposed to moisture, humidity, or corrosive environments, high carbon steel will oxidize and form rust.
To prevent rust, high carbon steel is often coated, painted, or treated with protective finishes, or regular maintenance is required to minimize corrosion.
Does carbon steel rust in water?
Yes, carbon steel will rust in water, especially if it is not protected with a coating or finish. When carbon steel is exposed to water, particularly if oxygen is present, it reacts to form iron oxide (rust). This process accelerates in saltwater or other corrosive environments because of the higher conductivity, which promotes oxidation.
To prevent rusting, carbon steel can be coated, painted, or treated with rust inhibitors when used in environments where water exposure is common.
Will carbon steel rust outside?
Yes, carbon steel will rust when exposed to outdoor environments, especially if it is not properly protected. Outdoor conditions, including moisture, rain, humidity, and oxygen, create an ideal environment for the formation of rust (iron oxide) on carbon steel.
Factors that accelerate rusting outdoors include:
- Rain and humidity: These introduce moisture, which speeds up oxidation.
- Temperature fluctuations: Condensation can form when temperatures change, further increasing moisture exposure.
- Salt (in coastal environments): Saltwater or salt-laden air greatly accelerates corrosion.
To prevent rust, carbon steel used outdoors is often coated with protective layers such as paint, galvanization, or other rust-resistant finishes.
Does carbon steel pan rust?
Yes, a carbon steel pan can rust if it is not properly seasoned or maintained. Carbon steel, like cast iron, is prone to rust when exposed to moisture or if it is not dried thoroughly after washing.
To prevent rust on a carbon steel pan:
- Season the pan: A protective layer of oil is baked onto the pan through seasoning, creating a non-stick surface and protecting it from moisture.
- Dry immediately: After washing, the pan should be dried thoroughly to remove any residual moisture.
- Apply oil: A light layer of oil should be applied after each use to help prevent rust.
If rust does form, it can usually be removed with steel wool or scrubbing, followed by re-seasoning the pan.
Why Carbon Steel Rusts?
The rust problem of carbon steel is mainly related to its chemical composition and environmental conditions. The main component of carbon steel is iron, which is prone to oxidation in a humid or oxygen-containing environment.
Oxidation reaction
Iron reacts with oxygen under the action of oxygen and moisture to form iron oxide (rust). Iron oxide further oxidizes to form reddish-brown rust.
Rust extension
Once rust is formed, it will further absorb moisture and oxidize, causing the corrosion process to continue. Rust not only damages the original beauty of the metal, but also gradually corrodes its material, causing the metal thickness to gradually decrease, ultimately weakening the metal’s load-bearing capacity and durability.
Environmental impact
Environmental conditions have a great impact on the corrosion of carbon steel. For example, high humidity, salt spray, acidic environment, etc. will accelerate the corrosion process.
Carbon Steel Corrosion Types
Uniform corrosion
Uniform corrosion refers to the uniform distribution of corrosion on the metal surface, usually caused by long-term contact between the metal and corrosive media (such as water or acidic gasses). Uniform corrosion will cause the metal thickness to gradually decrease, affecting its structural strength.
Local corrosion
Local corrosion includes pitting and crevice corrosion. Pitting usually appears as small holes on the metal surface, while crevice corrosion occurs in cracks or gaps on the metal surface. Local corrosion tends to be concentrated in certain specific areas, which may be caused by local protective layer damage or uneven corrosion environment.
Stress corrosion cracking
This type of corrosion happens on metal surfaces subjected to external stress, particularly when exposed to corrosive environments. Stress corrosion cracking may cause brittle cracking and fracture of the material, seriously affecting its performance.
Hydrogen embrittlement
Hydrogen embrittlement refers to the accumulation of hydrogen inside the metal, which reduces the toughness of the material and then causes brittle fracture. This phenomenon usually occurs in metals in hydrogen environments, such as metal materials used in hydrogen compression equipment.
Galvanic corrosion
Galvanic corrosion refers to a localized corrosion phenomenon in which when two metals with different potentials come into contact with each other in a corrosive medium, the metal with a lower potential (anode) will corrode faster due to the potential difference, while the metal with a higher potential (cathode) will corrode slower.
Carbon Steel Rust Removal
Mechanical removal
Using mechanical tools such as sandpaper, wire brushes or grinding wheels can effectively remove rust from the surface. Suitable for light rust. Mechanical removal methods are fast and effective, but may leave tiny scratches that affect the appearance of the metal.
Chemical removal
Soaking or wiping the metal surface with a chemical rust remover or an acidic cleaner (such as phosphoric acid or hydrochloric acid) can dissolve rust. When using chemical removers, be careful to avoid damage to the metal surface and operate according to the instructions. Chemical removal methods are suitable for large areas or severe rust.
Electrolytic rust removal
Rust is removed by using electrolyte and electric current through the electrolytic process. This method is suitable for metal parts with complex shapes and can effectively remove deep rust. Electrolytic rust removal requires special equipment and technology, but can achieve good rust removal results.
Sandblasting
The use of high-speed sprayed sand particles to treat the metal surface can effectively remove rust and roughened the metal surface to enhance the adhesion of subsequent coatings. Sandblasting is suitable for large-scale cleaning operations, but requires professional equipment.
How to Prevent Carbon Steel from Rusting?
Coating protection
Applying a layer of rust-proof paint or protective layer, such as paint, zinc plating, etc., on the surface of carbon steel can effectively prevent oxygen and moisture from contacting the metal surface, thereby reducing corrosion. This method is effective in various applications, especially outdoors and in harsh environments. Commonly used coating protections include hot-dip galvanizing, electrogalvanizing, and spray painting.
Use rust inhibitors
Applying rust preventive agent or rust preventive oil on the surface of carbon steel can form a protective film and delay the corrosion process. This method is suitable for metal parts that need temporary protection. Rust preventive agents can be divided into lubricating type, protective type and inhibitory type. You should choose the appropriate rust preventive agent.
Regular maintenance
Regularly inspect and clean carbon steel parts, remove rust and corrosive substances in time, and keep the metal surface dry and clean. This includes removing accumulated water and sediments, and checking for damaged protective layers. Regular maintenance can effectively extend the service life of carbon steel parts.
Avoid contact with corrosive substances
When designing and using carbon steel products, try to avoid exposing them to corrosive chemicals such as acids and alkalis. For example, in chemical treatment plants or salt water environments, appropriate protective measures should be taken, such as using anti-corrosion materials and installing sealing devices.
Use suitable alloys
When necessary, alloys containing anti-corrosion elements (such as nickel, chromium, etc.) can be selected to enhance the corrosion resistance of the material. For example, using galvanized steel can improve corrosion resistance. The alloying method can effectively improve the corrosion resistance of carbon steel.
Prevent galvanic corrosion
Isolate different metals: Take steps to isolate metals at different potentials so that they do not come into direct contact. If it cannot be avoided, insulating materials can be used to separate them to prevent galvanic corrosion. Insulating gaskets and coatings can effectively prevent galvanic corrosion.
Choose the right combination of metals: Using the same metal materials for contact parts can reduce the possibility of galvanic corrosion.
Regular inspection and maintenance: Regularly inspect areas where galvanic corrosion may occur to ensure that no battery effect occurs, and perform necessary maintenance and repairs. Using a potential difference tester can help detect and identify potential galvanic corrosion problems.
What Metals or Alloys are not easy to Rust?
Stainless steel: Stainless steel can form a protective film on the surface due to its high content of chromium, thus effectively resisting corrosion. In many applications, stainless steel is used, especially where high corrosion resistance is required.
Aluminum and its alloys: A natural aluminum oxide protective film will form on the aluminum surface, which has good corrosion resistance. Suitable for aviation, automotive and construction.
Galvanized steel: A protective layer is formed by coating the surface of carbon steel with zinc to effectively prevent oxygen and moisture from contacting the steel. Widely used in construction and manufacturing.
Titanium and its alloys: Titanium metal exhibits excellent corrosion resistance in most environments and is not easy to rust. It has been widely used in aerospace and medical fields.
Copper and its alloys: Copper forms a layer of green patina (patina) in the atmosphere, which prevents further corrosion. Copper and its alloys such as brass and bronze also have good corrosion resistance and are widely used in construction and decoration.
Carbon Steel vs Stainless Steel
The difference between carbon steel and stainless steel is:
Composition and alloy content: Carbon steel consists mainly of carbon and iron, and contains no or only small amounts of alloying elements. In addition to iron and carbon, stainless steel also contains high levels of alloying elements such as chromium (Cr) and nickel (Ni), usually with a chromium content of more than 12%.
Physical properties:
- Stainless steel contains more alloying elements, so its appearance is mostly silver and smooth. Carbon steel, on the other hand, is mainly the color of iron, which is relatively dark, and its surface may not be as smooth as stainless steel.
- Carbon steel usually has a higher density than stainless steel.
- Stainless steel is more resistant to corrosion, while carbon steel is less so.
Magnetism: Carbon steel is magnetic and can be attracted by magnets, while the magnetism of stainless steel varies depending on the type. Ferrite (F) and martensite (M) stainless steels are magnetic, while austenite (A) stainless steels are non-magnetic.
Corrosion resistance: Compared with stainless steel, carbon steel has weaker corrosion resistance. In an environment rich in oxygen and humidity, carbon steel is very susceptible to rust, so additional anti-corrosion measures are often required to maintain its surface integrity. Stainless steel keeps its material stability and durability despite harsh environments.
Other properties: Carbon steel has high strength, good processability and weldability, and relatively low production cost advantages, but it lacks wear resistance, high temperature resistance, and corrosion resistance. In contrast, in addition to excellent corrosion resistance, stainless steel also has the characteristics of high temperature resistance, beautiful appearance, easy processing, environmental protection, and wear resistance.
Does carbon steel rust faster than stainless steel?
Yes, carbon steel rusts significantly faster than stainless steel. This is because carbon steel lacks the protective chromium oxide layer that forms on stainless steel, which prevents rust and corrosion.
- Carbon Steel: Contains primarily iron and carbon, making it highly prone to rust when exposed to moisture and oxygen. Without a protective coating or treatment, it will begin to rust quickly.
- Stainless Steel: Contains at least 10.5% chromium, which reacts with oxygen to form a thin, invisible layer of chromium oxide. This layer protects the steel from rusting and can self-heal if damaged.
As a result, carbon steel requires more maintenance (coatings, drying, oiling) to prevent rust, while stainless steel is much more rust-resistant, especially in environments with moisture or exposure to the elements.
Related reading: Will Stainless Steel Rust and How Can You Solve It?
Get Satisfactory Steel!
As an experienced steel supplier, we will wholeheartedly provide you with the products and solutions that best suit your needs. If you have trouble choosing steel or need professional advice, please feel free to contact us.