Contents
Rebar Essentials: Rebar Sizes, Types, Grades, and Uses
- John
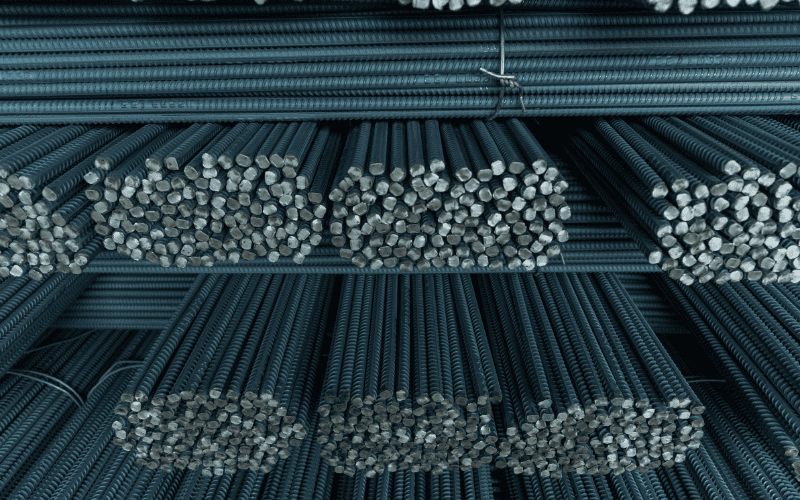
Steel bars are everywhere in our lives, but we rarely see rebar. This is because it’s an essential element in construction and is used to reinforce concrete structures to withstand immense pressure.
This article will provide in-depth insights into the composition, manufacture, types, grades, sizes, and future trends of rebar to help you deepen your understanding of it, allow you to make informed decisions about your construction practices.
What is Rebar?
Rebar, also named reinforcing bar or reinforcement bar, is a solid steel bar made of 99% iron and 1% carbon. Rebar is typically produced through hot rolling, and its ribbed surface improves bonding with concrete. Its tensile strength, durability, and thermal expansion properties reduce temperature variation issues, enhancing concrete structural strength. Rebar comes in various types and sizes, applicable in various building structures.
History of Rebar
- 1850s: French gardener Joseph Monier invented reinforced concrete, using steel to strengthen concrete flower pots.
- Early 1900s: Twisted rebar was invented by Ernest L. Ransome, improving the bond between steel and concrete.
- Mid-20th Century: Improved steel quality and production methods expanded rebar use in major infrastructure projects.
- Late 20th Century: Epoxy-coated and stainless steel rebar were introduced for better corrosion resistance.
- 21st Century: Fiber-reinforced polymer (FRP) rebar emerged as a corrosion-resistant, lightweight alternative.
How Is Rebar Made
Rebar is primarily made from recycled steel, making it highly eco-friendly.
- Melting: The process begins with scrap steel being melted in an electric arc furnace, converting solid metal into liquid form.
- Molten Steel: The molten steel is then prepared for purification, ensuring impurities are removed for quality.
- Purification: Once molten, the steel is purified and then cast into billets, forming the initial shape for further processing.
- Heating: The billets are heated to an elevated temperature to soften them for rolling, rendering them malleable for shaping.
- Rolling: The heated billets are passed through a series of rolling mills, and gradually rolled into round bars of the desired diameter. This process is called hot rolling.
- Cooling and Cutting: The rebar is cooled naturally on beds or rapidly with water, then cut to the desired length, typically 12 meters or more.
- Surface Treatment: During rolling, ribs or other deformations are pressed onto the rebar’s surface to enhance its bonding with concrete.
Despite being made from recycled materials, the performance of rebar remains uncompromised. It retains its strength and durability and can be recycled again after its lifecycle in construction.
Types of Rebar
Rebar types include carbon steel, epoxy-coated, GFRP, and stainless steel rebar, with GFRP and stainless steel rebar offering the best corrosion resistance for harsh environments.
Carbon Steel Rebar
Carbon steel rebar, also known as black bar, is the predominant type of rebar utilized in construction. It is highly versatile, cost-effective, and provides outstanding tensile strength and durability. However, it is susceptible to rusting when exposed to moisture and chemicals.
Epoxy-Coated Rebar
Epoxy-coated rebar is carbon steel rebar featuring an epoxy coating for corrosion prevention. This type is ideal for environments with high moisture and chloride levels, such as marine structures and bridges. The coating significantly extends the lifespan of the rebar, but extra care is needed during transportation to avoid damage.
Stainless Steel Rebar
Stainless steel rebar is highly resistant to rust and is frequently used in structures exposed to demanding environmental conditions, such as coastal areas and chemical plants. Although more expensive than other types, its durability and long-term performance can justify the cost in critical applications.
Galvanized Rebar
Galvanized rebar consists of carbon steel rebar coated with zinc to shield it from corrosion. This variety provides superior resistance to rust compared to epoxy-coated rebar and finds frequent use in applications requiring extended durability, such as highway construction and marine environments.
Glass Fiber Reinforced Polymer (GFRP) Rebar
GFRP rebar is crafted from high-strength glass fibers encased in a polymer matrix. It is lightweight, non-corrosive, and non-conductive, making it suitable for use in structures exposed to electromagnetic fields, such as MRI rooms and electrical substations. Its excellent strength-to-weight ratio also facilitates easier handling and installation.
Welded Wire Fabric (WWF) Rebar
Welded wire fabric rebar, also referred to as welded wire mesh, comprises a lattice of steel wires fused together at intersections. It is commonly used for reinforcing concrete slabs, walls, and pavements. WWF rebar provides uniform strength and easy installation, making it a popular choice for a wide range of construction projects.
High-Strength Deformed Bars
High-strength deformed bars (HSD bars) feature surface indentations for enhanced concrete adhesion. They offer superior tensile strength and durability, ideal for heavy-duty construction like high-rise buildings and bridges. The deformations ensure a stronger grip with concrete, enhancing structural integrity.
Basalt Rebar
Basalt rebar, made from basalt rock fibers, offers high tensile strength and excellent corrosion and alkali resistance. It is lighter than steel rebar, easing transport and handling. As a new material, it is ideal for concrete reinforcement in harsh environments. The growing demand for low-maintenance construction materials is expected to boost its usage.
Primary Rebar and Secondary Rebar Reinforcement in Structural Design
Rebar reinforcement is divided into primary and secondary types. Primary rebar provides the main structural support, while secondary rebar enhances durability by preventing cracks and resisting temperature-related stresses.
Primary Reinforcement: This rebar ensures the structure can support the designed load, providing essential strength in key areas like beams and columns.
Secondary Reinforcement: Distribution or thermal rebar limits cracking from shrinkage and temperature changes, improving durability and appearance.
Additional Applications: In masonry, rebar is placed in mortar joints or hollow blocks to strengthen the structure, similar to reinforced concrete.
Seismic Reinforcement: Circular rebar designs are added in modern structures to prevent failures during earthquakes, enhancing structural safety.
Size of Rebar
Selecting the appropriate size of rebar is essential for the structural strength of a building. Factors such as load-bearing capacity can affect the effective selection and placement of rebar:
Factors Determining the Choice of Rebar Size
Rebar size is determined by the structure’s load-bearing capacity and design specifications. Concrete cover thickness and rebar spacing also influence size selection.
Strength Requirements
Rebar size directly correlates with the required load-bearing capacity of the structure. Larger diameters, such as 32mm, 40mm, or 50mm, are often used to withstand heavier loads.
Structural Design
Different structural components have varying requirements for rebar sizes. For instance, foundations and columns, which bear significant loads, may necessitate larger diameters. In contrast, non-load-bearing walls or floor slabs might utilize smaller diameter rebars.
Concrete Cover
The diameter of rebars affects the thickness of the concrete cover required to prevent corrosion. Ensuring adequate cover depth is essential for maintaining structural durability.
Spacing and Placement
The spacing and arrangement of rebars influence sizing decisions. Closer spacing and intricate layouts often require smaller rebar diameters to fit within designated spaces without compromising reinforcement effectiveness.
How to Measure Rebar Size
To measure the size of reinforcing bars, typically the diameter is measured, there are several methods can be employed:
- Vernier Caliper Method: Use a vernier caliper to directly gauge the diameter of the rebar. Ensure the caliper is calibrated and apply it perpendicular to the axis of the rebar for accurate measurement.
- Weight Method: Measure the weight of a known length of rebar and use a formula to calculate the diameter based on the weight per unit length, as per national standards.
- Internal Diameter Measurement: Insert a gauge into the rebar to measure its internal diameter, comparing the result against national standards for accuracy.
- Other Methods: Additional methods include using ultrasonic thickness gauges to indirectly measure rebar diameter by detecting changes in ultrasonic waves passing through the material.
These methods offer different choices based on the equipment at hand and the accuracy needed for the measurement.
Popular Rebar Size Chart
Choosing the correct rebar size is crucial. Imperial rebar sizes are typically denoted by numbers, starting from #3. Each successive number increases the diameter by 1/8 inch, up to #8.
Understanding this pattern facilitates quick estimation of the diameters of different numbered rebars. Below is a chart we have compiled for your convenience, providing a clear reference for the information you need.
Imperial Bar Size | Weight (lb/ft) | Weight (kg/m) | Nominal Diameter (in) | Nominal Diameter (mm) | Nominal Area (in²) | Nominal Area (mm²) |
#3 | 0.376 | 0.561 | 0.375 | 9.525 | 0.11 | 71 |
#4 | 0.668 | 0.996 | 0.5 | 12.7 | 0.2 | 129 |
#5 | 1.043 | 1.556 | 0.625 | 15.875 | 0.31 | 200 |
#6 | 1.502 | 2.24 | 0.75 | 19.05 | 0.44 | 284 |
#7 | 2.044 | 3.049 | 0.875 | 22.225 | 0.6 | 387 |
#8 | 2.67 | 3.982 | 1 | 25.4 | 0.79 | 509 |
#9 | 3.4 | 5.071 | 1.128 | 28.65 | 1 | 645 |
#10 | 4.303 | 6.418 | 1.27 | 32.26 | 1.27 | 819 |
#11 | 5.313 | 7.907 | 1.41 | 35.81 | 1.56 | 1006 |
#14 | 7.65 | 11.41 | 1.693 | 43 | 2.25 | 1452 |
#18 | 13.6 | 20.27 | 2.257 | 57.33 | 4 | 2581 |
Rebar sizes from #3 to #18 are commonly employed in construction for a range of applications. Here are five popular sizes and their common uses:
- #3 Rebar: Used in light-duty applications such as sidewalks, small concrete slabs, and residential construction.
- #4 Rebar: Commonly found in footings, walls, and light structural supports in buildings.
- #5 Rebar: Used in medium to heavy-duty applications, including concrete floors, driveways, and foundation walls.
- #6 Rebar: Found in larger concrete structures like bridges, heavy foundation mats, and retaining walls.
- #8 Rebar: Typically used in high-load applications such as columns, piers, and heavy industrial construction.
These sizes cater to a range of structural needs, ensuring durability and strength in various concrete projects.
Grades of Rebar
Rebar grades, defined by ASTM standards, specify crucial properties like yield strength and elongation, guiding the selection of reinforcement for optimal structural integrity in construction projects.
What are the Rebar Grades?
Rebar grades in the US, defined by ASTM standards, specify minimum yield strengths, chemical composition, and elongation. Common grades like 40, 60, and 75 are named based on their minimum yield strength in ksi (1000 psi). Understanding these standards is crucial for selecting reinforcement to ensure structural safety and strength.
The following provides a more in-depth overview of the industry’s regulatory standards:
- ASTM Standards: ASTM A615/A615M specifies carbon-steel bars (deformed and plain), while ASTM A706/A706M covers low-alloy steel bars. Both standards detail minimum yield strength, chemical composition, and elongation requirements.
Rebar Deformation Standards
Deformation requirements, found in ASTM A615 and ASTM A706, specify the spacing and height of ribs or lugs on rebar surfaces. These deformations improve the bond between rebar and concrete, enhancing the structure’s overall strength and stability.
Common rebar grades are defined by minimum yield strength, with examples including Grade 40, Grade 60, and Grade 75. Understanding these standards is essential for choosing the right rebar to maintain structural safety and performance.
Common Grades Chart and Applications
This chart provides a clear comparison of these grades, aiding in the precise choice of rebar for various structural requirements in building and infrastructure projects.
Standard | Grade | Yield Strength (MPa / ksi) | Tensile Strength (MPa / ksi) | Elongation (%) |
ASTM A615/A615M | Grade 40 | 280 / 40.6 | 420 / 60.9 | 7 |
ASTM A615/A615M | Grade 60 | 420 / 60.9 | 620 / 89.9 | 9 |
ASTM A615/A615M | Grade 75 | 520 / 75.4 | 690 / 100.0 | 11 |
ASTM A706/A706M | Grade 60 | 420 / 60.9 | 550 / 79.8 | 14 |
ASTM A706/A706M | Grade 80 | 550 / 79.8 | 690 / 100.0 | 14 |
ASTM A615/A615M | Grade 100 | 690 / 100.0 | 830 / 120.3 | – |
Below are different application scenarios for various grades of rebar:
Grade 40 Rebar
Grade 40 rebar is frequently employed in lightly loaded structures and residential building projects. It is suitable for applications such as sidewalks, small concrete slabs, and low-rise buildings where moderate strength is sufficient.
Grade 60 Rebar
Grade 60 rebar offers increased strength and durability, making it suitable for medium to heavy-loaded structures. It is commonly used in commercial buildings, bridges, and highway pavements.
Grade 75 Rebar
Grade 75 rebar provides enhanced strength and is designed for heavy-loaded structures and high-rise buildings. It is suitable for applications requiring superior structural performance, such as industrial facilities and large-scale infrastructure projects.
Grade 80 Rebar
Grade 80 rebar is primarily used in seismic applications where resilience and strength are critical. It is suitable for structures in earthquake-prone regions, ensuring structural integrity under dynamic loading conditions.
Grade 100 Rebar
Grade 100 rebar is used in specialized applications requiring extremely high strength and durability. It finds applications in heavy industrial constructions like offshore platforms, dams, and nuclear power plants, where robust reinforcement is essential to withstand extreme conditions.
These different grades of rebar cater to a wide range of structural requirements, ensuring safety, durability, and performance across various construction projects.
How to Identifying Marks on Reinforcing Bars
Once you have a complete understanding of rebar ratings, you also need to master recognizing the markings on the rebar. Manufacturers’ marks, like production dates and batch numbers, ensure traceability and quality assurance, crucial for structural integrity and compliance with standards.
Grades Markings
Rebar grades are typically marked on the surface, such as “40” for Grade 40, indicating the minimum yield strength of the steel.
Diameter Markings
Rebar diameter is often indicated on the surface by numbers or lines, like three parallel lines for #3 rebar (9.5 mm diameter) or six parallel lines for #6 rebar (19 mm diameter).
Standard Identification
Each rebar carries a standard designation, such as ASTM A615 or ISO 6935-2, ensuring compliance with specific manufacturing and performance standards.
Manufacturers may also imprint their specific marks, including production dates and batch numbers, to track quality and ensure traceability throughout the supply chain.
How to Examine Rebar and What to Check For
When receiving reinforcing bars, it’s important to distinguish them from regular steel due to their manufacturing process and appearance.
Visual Inspection
Inspect the surface for any rust, corrosion, or physical damage that could compromise structural integrity. This ensures the rebar’s surface is free from defects that could weaken its performance over time.
Specification Verification
Check the rebar’s diameter, length, and shape to confirm it meets the required design criteria. Proper specification verification guarantees that the rebar will fit and function correctly within the construction project.
Sampling Testing
Random sampling tests will be conducted to evaluate characteristics such as yield strength and elongation. This quality control measure ensures that the rebar batch meets the expected performance standards and durability requirements.
Finally, store rebar in a dry, rust-free environment, elevated from the ground, until ready for use.
Rebar Oxidation and Corrosion
Causes:
- Environmental Factors: Rebar is more prone to oxidation in moist or saline environments. The presence of water and oxygen accelerates corrosion.
- Concrete pH: Concrete typically has a high pH, which forms a protective passive layer on rebar. However, the presence of chloride ions can break down this layer, leading to corrosion.
- Surface Treatment: Untreated rebar, such as uncoated or non-galvanized steel, is more susceptible to corrosion.
Consequences:
- Structural Integrity: Corroded rebar weakens, reducing its load-bearing capacity and compromising the structure’s overall safety.
- Economic Impact: Corrosion-related repairs and reinforcements can be costly, especially in large infrastructure projects.
- Cracking and Spalling: As rust expands, it generates internal pressure, causing concrete to crack and spall, which can lead to structural failure.
Prevention Methods:
- Anti-Corrosion Coatings: Applying coatings like epoxy on rebar surfaces can prevent moisture and oxygen from reaching the steel.
- High-Resistance Rebar: Using stainless steel or corrosion-resistant alloys greatly improves rebar durability.
- Optimized Concrete Mix: Reducing chloride content in concrete and adding corrosion inhibitors can minimize the risk of rebar corrosion.
- Maintenance: Regular inspection and maintenance help identify early signs of corrosion, allowing for timely intervention to extend the structure’s lifespan.
How to Prevent Rebar Pullout in Concrete
Proper placement and structural reinforcement are key to prevent rebar from being pulled out under high stress.
- Embedment Depth: The Rebar should be deeply embedded into adjacent structural elements, typically 40-60 times the rebar diameter. This increases the friction holding the bar in place.
- Hooks and Bends: Bending and hooking rebar at the ends lock it within the concrete, utilizing its compressive strength to prevent pullout.
- Use of Stirrups and Ties: Adding stirrups and ties around the rebar increases confinement and distributes loads more evenly, reducing the risk of slippage.
- Rebar Coating: Applying surface treatments like epoxy coatings can improve bonding with concrete and enhance grip.
Each method helps ensure the rebar remains securely anchored, preventing structural failures.
How Rebar Handles Corrosive Environments
In highly corrosive environments, such as bridges exposed to road salt or marine applications, various rebar options can be used to combat corrosion:
- Uncoated Corrosion-Resistant Alloys: Low-carbon/chromium microcomposite rebar.
- Silicon Bronze: Offers excellent corrosion resistance.
- Epoxy-Coated Rebar: Protects against moisture and salt exposure.
- Cathodic Protection: Prevents corrosion through electrochemical methods.
- Galvanized or Stainless Steel: More costly initially, but significantly reduces long-term maintenance costs.
Do You Need Rebar for 4-inch Driveway?
Yes, rebar is typically not required for a 4-inch driveway, as driveways of this thickness generally do not experience significant structural stress that would necessitate reinforcement with rebar.
What is Type 1 and Type 2 rebar?
Type 1 rebar is plain round bar, while Type 2 rebar has deformations for better adhesion with concrete.
What is the Difference Between Grade 75 and Grade 60 Rebar?
Grade 75 rebar is stronger than Grade 60 rebar, offering higher tensile strength for more demanding applications.
When Should I Use Rebar?
Rebar is typically used to reinforce concrete in areas prone to cracking or structural stress, such as driveways, foundations, and structural beams.
Difference Between Rebar and Steel Bar?
Steel bar is a steel rod or steel strip in various shapes and sizes used in construction, manufacturing, and industry. Rebar is a specific type of steel bar designed to reinforce concrete structures. While rebar strengthens concrete, steel bars have broader uses. Visit SteelPRO Group’s steel bar page for more details.
Capturing Future Trends in Rebar Technology
Advanced Materials: Future trends in rebar include enhanced alloys and composites for better strength-to-weight ratios and corrosion resistance.
Sustainability: There’s a shift towards using recycled materials and reducing carbon footprints in rebar production.
Coatings: Epoxy-coated and galvanized rebar are increasingly popular for their durability in corrosive environments.
Technology: Innovations like digital tracking and sensors are improving quality control during rebar production and installation.
SteelPRO Group offers high-quality rebar for concrete and construction rebar that ensures the durability and resilience of your construction projects while aligning with sustainable development goals. For more information on the role of rebar in building a resilient and environmentally conscious future, please visit our blog page. Contact us today to place your order and join us in this sustainable journey!