Contents
A2 Vs O1 Tool Steel Comparison Guide
- John
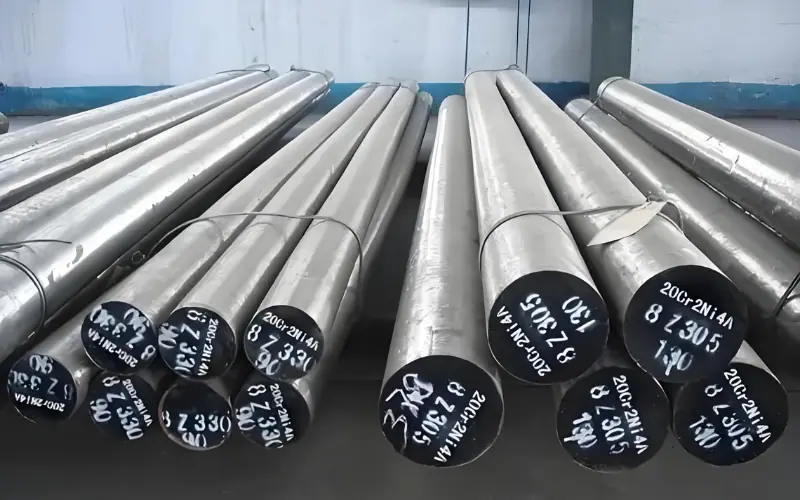
Both O1 and A2 are cold work tool steels, but their differences are far from subtle.
A2 offers superior wear resistance, toughness, and durability, ideal for high-stress applications. O1, while easier to sharpen and maintain, tends to wear out faster and is better suited for precision tools where frequent sharpening is acceptable.
In short, A2 is preferred for long-lasting, high-performance tools, while O1 is chosen for ease of sharpening and precision. If you are still unsure which material is right for your application, SteelPro Group is here to help you understand your options and make an informed decision.
A2 And O1 Tool Steel Different Properties
Wear Resistance
- A2: Offers better wear resistance, making it ideal for tools that face a lot of wear and tear over time.
- O1: Doesn’t resist wear as well, so it may need sharpening more often, especially with heavy use.
Edge Retention
- A2: Keeps its sharp edge for longer, even under tough conditions.
- O1: Sharper out of the gate but dulls faster, requiring more frequent maintenance.
Toughness
- A2: Tougher overall, meaning it can withstand more stress and is less likely to chip or break under pressure.
- O1: Less tough compared to A2, so it’s better suited for tasks that don’t involve heavy impact or stress.
Machinability
- A2: A bit harder to machine and shape because of its tougher, more wear-resistant nature.
- O1: Easier to machine and sharpen, making it a good choice for tools that need precise shaping and fine-tuning.
Dimensional Stability
- A2: Holds its shape better during heat treatment, which is great for keeping your tools precise over time.
- O1: Less stable during heat treatment, but it’s easier to manage when working on smaller or intricate parts.
Chemical Composition of O1 Vs A2 Tool Steel
Element | O1 Composition (%) | A2 Composition (%) |
Carbon (C) | 0.90 – 1.00 | 1 |
Manganese (Mn) | 0.30 – 0.50 | 0.75 |
Chromium (Cr) | 0.40 – 0.60 | 5 |
Molybdenum (Mo) | 0.15 – 0.30 | 1 |
Silicon (Si) | 0.10 – 0.35 | 0.3 |
Vanadium (V) | — | 0.25 |
Nickel (Ni) | — | ≤ 0.30 |
Phosphorus (P) | ≤ 0.030 | ≤ 0.03 |
Sulfur (S) | ≤ 0.030 | ≤ 0.03 |
Compared to O1 tool steel, A2 contains higher amounts of alloying elements, which form carbides that enhance its hardenability, wear resistance, toughness, and dimensional stability. The trace amount of chromium in A2 also provides some corrosion resistance, though not as much as stainless steel.
O1 tool steel has a lower concentration of alloying elements. The small amount of manganese in O1 ensures uniform hardening depth and consistency during oil quenching. The simpler composition also makes it easier to machine and sharpen.
A2 And O1 Tool Steel Different Applications
A2’s strength and long-lasting sharpness make it perfect for tools that see a lot of use, while O1’s ease of sharpening and precision make it ideal for tasks that require frequent maintenance and fine detail.
Applications of A2 Tool Steel
- High-volume dies and punches
- Cutting tools like machine knives and shear blades
- Precision tools (gauges, lamination tools)
- Stamping and forming dies
- Heavy-duty machine parts
Applications of O1 Tool Steel
- Precision cutting tools (jigs, cutters, stamps)
- Molds and dies
- Hand tools (chisels, punches, saws)
- Fixtures and guides
- Machine components requiring frequent sharpening
O1 And A2 Tool Steel: How To Choose?
At SteelPro Group, we understand that selecting the right tool steel is crucial for the success of your projects. Whether you need the durability of A2 or the precision of O1, we’re here to help you make an informed choice that best suits your specific needs.
1. Assess Your Tool Usage
- High-Stress Applications: If your tools will endure heavy use and require long-lasting performance, A2 is the optimal choice. Its superior wear resistance and toughness ensure that your tools remain durable and reliable over time.
- Precision and Detail Work: For tasks that demand high precision and frequent sharpening, O1 is ideal. Its ease of sharpening and ability to achieve a keen edge makes it perfect for fine-detail work where maintaining sharpness is crucial.
2. Consider Maintenance Preferences
- Low Maintenance: Choose A2 if you prefer tools that hold their edge longer and require less frequent sharpening. This is beneficial for projects where minimizing maintenance saves time and effort.
- Frequent Sharpening: Opt for O1 if you don’t mind sharpening your tools regularly. Its simpler composition allows for easier and quicker sharpening, which is ideal for users who enjoy maintaining their tools frequently.
3. Evaluate Dimensional Stability Needs
- Consistency and Precision: A2 offers excellent dimensional stability, making it suitable for tools that must maintain precise dimensions even after extensive use and heat treatment.
- Flexibility in Shaping: O1 is easier to machine and shape, which is advantageous for projects that require intricate detailing and frequent adjustments.
4. Budget Considerations
- Long-Term Investment: While A2 may have a higher upfront cost due to its alloy content, its durability can lead to cost savings over time by reducing the need for frequent replacements.
- Cost-Effective Precision: O1 provides a more affordable option for precision tools, especially for projects that require detailed work without the need for long-term wear resistance.
Get the Perfect A2 vs O1 Tool Steel
Ready to select the perfect tool steel for your needs? SteelPro Group is here to help you make an informed decision. Contact us today to explore our high-quality A2 and O1 tool steels, tailored to meet your project’s demands.