Contents
Tool Steel Common Grades Guide: Properties, Uses, Comparison
- John
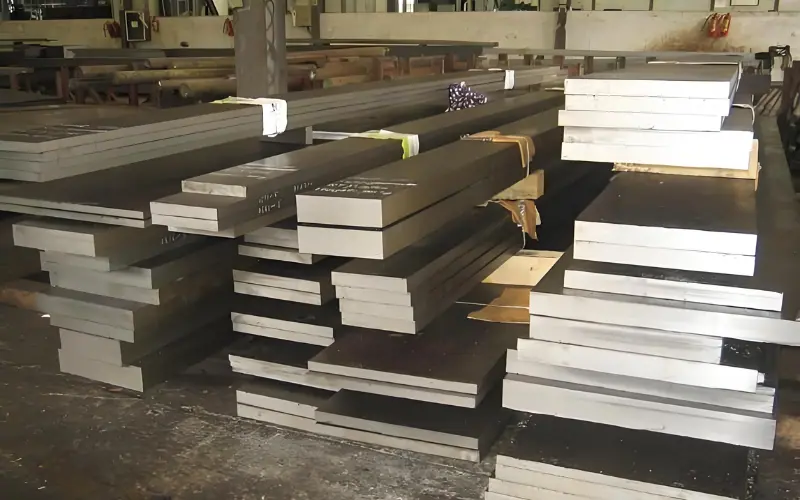
Genuine tool steel is a specially formulated steel alloy. These alloys maintain high hardness, strength, and wear resistance even under extreme mechanical stress and high temperatures, specifically designed for manufacturing and metalworking. The everyday hammers, common files, and chisels we use in our daily lives are not made from true tool steel.
The world of tool steels is diverse. As a tool steel supplier with over a decade of production experience, SteelPro Group is here to introduce you to common tool steel grades and help you truly understand this material.
Tool Steel Common Types
Water-Hardening Tool Steel (W-Series)
These steels are cost-effective and are hardened by quenching in water. They offer moderate hardness but have limited resistance to wear, heat, and corrosion compared to higher-alloy steels.
Applications: Commonly used for general-purpose tools, such as hand tools, low to medium-stress cutting tools, and chisels.
Cold-Working Tool Steel (O-, A-, D-Series)
These steels are hardened in oil or air, providing excellent wear resistance and high hardness retention at low temperatures. They contain alloying elements like chromium, vanadium, and molybdenum to enhance toughness and wear resistance.
- O-Series: Offers good toughness and machinability, suitable for moderate wear applications.
- A-Series: Provides improved wear resistance with high stability in use.
- D-Series: Excels in wear resistance and hardness retention, ideal for die-casting and stamping dies.
Applications: Well-suited for tools subject to moderate stresses and wear, including punches, dies, shear blades, and stamping tools.
Hot-Working Tool Steel (H-Series)
Formulated to maintain hardness at high temperatures, these steels are often alloyed with chromium, molybdenum, and tungsten to enhance resistance to heat deformation. They can be hardened by air or oil, depending on the specific grade.
Applications: Commonly used in die-casting, extrusion dies, and hot-forging processes, where high operating temperatures are the norm.
High-Speed Tool Steel (T-Series)
These steels contain high amounts of tungsten, molybdenum, and vanadium, allowing them to retain hardness even at very high temperatures. They’re specifically designed for cutting tools and machines operating at high speeds and temperatures.
Applications: Ideal for drills, milling cutters, and other high-speed cutting tools.
Shock-Resisting Tool Steel (S-Series)
Engineered to absorb and endure rapid impacts and jolts without fracturing or shattering. They typically contain nickel and chromium to increase toughness and impact resistance.
Applications: Used for tools requiring resistance to sudden or cyclic shock, such as hammers, chisels, and striking tools.
Tool Steel Common Grades Comparison
The table below outlines the essential characteristics of several widely used tool steel grades, assisting you in comparing various materials.
Grade | Melting Point (°C) | Hardness (HRC) | Yield Strength (MPa) | Impact Toughness (J) |
H13 | 1,350 | 50-55 | 1,500-1,800 | Medium |
W1 | 1,420 | 55-64 | 1,200-1,400 | Low |
A2 | 1,200 | 57-62 | 1,400-1,600 | Medium |
O1 | 1,200 | 58-64 | 1,200-1,400 | Low |
D2 | 1,250 | 58-62 | 1,600-2,000 | Low |
M2 | 1,410 | 62-65 | 1,800-2,200 | Medium |
M42 | 1,470 | 64-66 | 2,100-2,400 | Medium |
Key Characteristics of Common Tool Steel Grades
W1 (Water-Hardening Tool Steel)
W1 tool steel is easy to harden and is used for general-purpose tools. It contains a significant amount of carbon, which enhances its hardness, but it is more prone to fragility in comparison to other grades.
Applications: Ideal for simple, low-stress tools such as chisels, punches, and cutting tools for light-duty applications.
O1 (Oil-Hardening Tool Steel)
O1 is a highly adaptable tool steel. It provides a favorable combination of hardness and toughness, along with excellent machinability. It is commonly used in tools that demand moderate abrasion resistance and general mechanical characteristics.
Applications: Commonly used in cutting tools, dies, punches, and shear blades.
A2 (Air-Hardening Tool Steel)
A2 tool steel is air-hardenable and provides a good balance of toughness and wear resistance. It experiences minimal distortion during heat treatment, which makes it perfect for intricate tooling.
Applications: Dies, punches, and tools require a combination of toughness and wear resistance.
D2 (Cold-Work Tool Steel)
D2 is known for its superior wear resistance due to its high carbon and chromium content. It is extremely hard but more brittle compared to A2. D2 has high abrasion resistance, making it ideal for cutting tools.
Applications: Used for high-wear tools such as blanking punches, dies, and cutting tools.
H13 (Hot-Work Tool Steel)
H13 offers excellent resistance to thermal fatigue and high temperatures. It retains its hardness and toughness even under elevated temperatures, making it ideal for hot-working applications.
Applications: Common in hot-forming applications, such as dies for forging, extrusion dies, and plastic molds.
M2 (High-Speed Tool Steel)
M2 is a type of tool steel that maintains its hardness and resistance to wear even at higher temperatures. It is known for its ability to maintain cutting-edge performance at higher speeds compared to other tool steels.
Applications: Widely used for high-speed cutting tools such as drills, taps, milling cutters, and reamers.
M42 (High-Speed Tool Steel)
M42 is a cobalt-alloyed high-speed steel that provides superior wear resistance and toughness, especially at high cutting speeds. Its high cobalt content enhances its performance in high-temperature environments.
Applications: Ideal for high-performance cutting tools, including saw blades, drills, and milling cutters.
How to Select the Ideal Tool Steel Grades for Your Project?
As an experienced metallurgist at SteelPro Group, I have helped numerous clients navigate the complex process of selecting the right tool steel for their needs. Allow me to share some expert advice to assist you in making a well-informed choice for your project:
Evaluate Operating Temperature
If your tool will be working in high-temperature environments, focus on hot-working steels like H13. For room temperature applications, cold-working steels such as D2 or O1 might be more suitable.
Assess Wear Resistance Needs
For applications involving abrasive materials or repetitive friction, prioritize steels with high wear resistance. D2 and M2 grades excel in this area.
Consider Toughness Requirements
If your tool will be subjected to impact loads or sudden stresses, look into shock-resistant grades like S7. These steels offer superior toughness without sacrificing hardness.
Factor in Machinability
Remember, some high-performance steels can be challenging to machine. If your project requires intricate shapes or fine details, consider grades like O1 or A2, which offer good machinability.
Balance Performance and Cost
While it’s tempting to opt for the highest-performing steel, it’s crucial to balance performance with cost-effectiveness.
Sometimes, a mid-range steel can provide adequate performance at a more reasonable price point. A higher-grade steel might have a higher upfront cost but could offer significant savings in terms of tool life and reduced downtime.
Consult with Experts
Every project is unique. Don’t hesitate to reach out to tool steel experts like our team at SteelPro Group. We can provide tailored advice and custom solutions to meet your requirements.
Choose the Right Tool Steel Grades With Our Help
At SteelPro Group, we offer a wide range of tool steel products tailored to your specific needs. Our team of experts is here to help you choose the perfect material for your project—whether you’re manufacturing cutting tools, dies, or custom components. Let SteelPro Group support you in achieving exceptional performance and durability with the right tool steel grade.