Contents
Air Hardening A10 Tool Steel: Properties, Heat Treat, Uses
- John
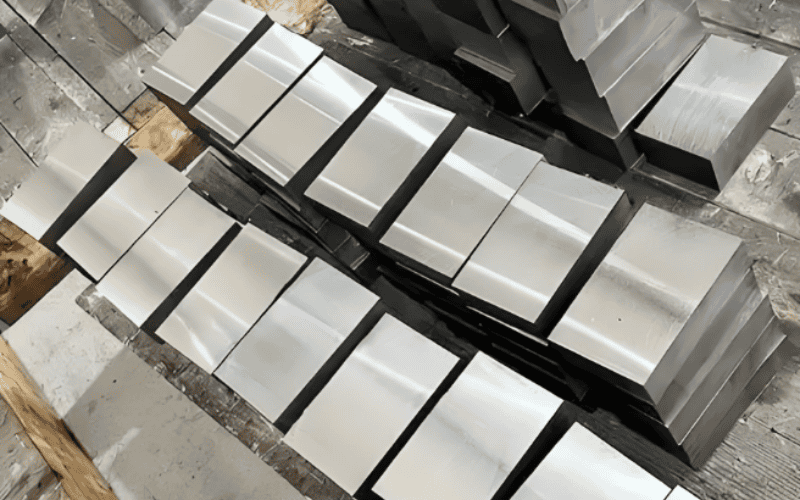
A10 Tool Steel is recognized for its outstanding wear resistance, superior hardness, and reduced distortion during heat treatment. This article explores its characteristics, heat treatment methods, and typical uses to assist you in making the most informed decision for your requirements.
What Is A10 Tool Steel?
A10 is an air-hardening, medium-alloy, cold-work steel, equivalent to UNS T30110, and meets ASTM A681 and FED QQ-T-570 standards. SteelPro Group offers A10 tool steel in various product forms, including bars, plates, rounds, forgings, and flat bars, with customizable sizes to meet your specific requirements.
A10 tool steel offers excellent wear resistance, high hardness (over 60 Rockwell C), and self-lubricating properties due to its graphite particles. It can achieve deep hardening without quenching, minimizing distortion. It is commonly used for cold-forming dies, thread gauges, and punching dies, but has moderate toughness, limiting its use in high-impact applications.
Chemical Composition of A10 Tool Steel
A10 tool steel’s high carbon, chromium, and molybdenum content give it excellent wear resistance, hardness, and toughness. With controlled levels of manganese and silicon, it’s well-suited for heavy loads and abrasive wear.
Below is the chemical composition of A10 tool steel.
Element | Composition |
Carbon (C) | 1.25 – 1.5 % |
Iron (Fe) | 92 %, as balance |
Manganese (Mn) | 1.85 % |
Molybdenum (Mo) | 1.5 % |
Nickel (Ni) | 1.65 % |
Phosphorus (P) | ≤ 0.030 % |
Silicon (Si) | 1.25 % |
Sulfur (S) | ≤ 0.030 % |
Mechanical Properties of A10 Tool Steel
A10 tool steel combines hardness, strength, and toughness for high-performance applications, maintaining stability under heavy loads and resistance to wear. Its shear and bulk modulus ensure effective stiffness and energy absorption.
Below is the table of A10 tool steel’s mechanical properties.
Properties | Metric | Imperial |
Hardness (HRC) | 52.0 – 62.0 | 52.0 – 62.0 |
Bulk modulus | 140 GPa | 20300 ksi |
Shear modulus | 80.0 GPa | 11600 ksi |
Elastic modulus | 190 – 210 GPa | 27557 – 30457 ksi |
Poisson’s ratio | 0.27 – 0.30 | 0.27 – 0.30 |
Machinability | 0.65 | 0.65 |
Physical Properties of A10 Tool Steel
A10 tool steel offers high density, strong thermal conductivity, and low thermal expansion, ensuring durability under thermal stress. Its specific heat and electrical resistivity also contribute to stability in high-temperature environments.
Below is the table of A10 tool steel’s physical properties.
Properties | Metric | Imperial |
Density | 7.8 g/cm³ | 0.282 lb/in³ |
Melting point | 1450°C | 2642°F |
Thermal conductivity | 45 W/m·K | 31.1 BTU·in/hr·ft²·°F |
Specific heat | 460 J/kg·K | 0.11 BTU/lb·°F |
Coefficient of thermal expansion | 11.5 µm/m·K | 6.4 x 10⁻⁶ in/in·°F |
Electrical resistivity | 0.61 µΩ·m | 0.61 µΩ·in |
A10 Tool Steel Heat Treatment
The heat treatment of A10 is designed to enhance its wear resistance, toughness, and machinability, ensuring it meets the stringent requirements of industries such as manufacturing and tooling.
At SteelPro Group, we ensure that A10 tool steel undergoes a precise heat treatment process to optimize its performance. By carefully controlling the temperature and cooling rates during processes , we deliver a steel that balances durability and ease of machining.
Annealing
After hot working and before re-hardening, annealing is required to relieve stresses.
Heating rate: 100°F (56°C) per hour until 1200°F (649°C), then 200°F (111°C) per hour.
Annealing temperature: 1450°F (788°C).
Soak time: 2 hours per 25.4mm (1 inch) of thickness.
Cooling rate: Furnace cooling at 25°F (14°C) per hour until 1000°F (538°C), then air cooling.
Hardness after annealing: Typically 235-260 HB.
Hardening
Preheating: For tools with complex geometries, preheating is recommended to prevent thermal shock. Preheat to 1200°F (649°C).
Austenitizing temperature: 1750°F (954°C) to maximize toughness and 1850°F (1010°C) for maximum wear resistance.
Soak time: Hold at temperature for 10-15 minutes per 25.4mm (1 inch) of thickness.
Quenching medium: Air.
Hardness after quenching: Typically 58-62 HRC, depending on section thickness and cooling rate.
Tempering
Soak time: 1 hour per 25.4mm (1 inch) of thickness.
Secondary tempering: For reducing brittleness and achieving further hardness, a secondary tempering at 600°F (316°C) for 1 hour per 25.4mm (1 inch) is recommended.
Hardness after tempering: Typically 55-60 HRC, depending on the tempering temperature.
Softening for Reworking
To soften A10 tool steel for reworking, heat to 1250°F (677°C) at a rate of 200°F (111°C) per hour, followed by air cooling. This process reduces hardness, making the material easier to machine while preserving its overall properties.
Other Process of A10 Tool Steel
Forging
A7 tool steel has a narrow forging temperature range, between 1875°F (1024°C) and 1650°F (899°C). Avoid forging below 1600°F (871°C) as it may lead to excessive grain growth, reducing the steel’s toughness and overall mechanical properties.
Forming
A10 is formed using hot forging within the 1875°F (1024°C) to 1650°F (899°C) range. Machining is typically done in the annealed state.
Welding
Welding A10 tool steel requires preheating to 1000°F (538°C) to reduce cracking risk. Post-weld heat treatment (PWHT) at 1100°F (593°C) for 1 hour per 25.4mm (1 inch) is recommended to relieve stresses and soften the heat-affected zone (HAZ).
Cold working
A10 is cold worked in its annealed state (235-260 HB), using traditional methods like bending and punching. Cold working at higher hardness levels should be avoided due to increased difficulty and risk of strain hardening.
Cutting
When A10 in its softer (annealed) state, conventional tools like HSS or carbide inserts can be used effectively.
A10 Tool Steel Product Forms
This section outlines the available product forms and corresponding dimensions of A10 tool steel. If you need custom sizes or dimensions outside the standard range, we can accommodate special requirements to meet your specific needs. We are committed to providing tailored solutions that ensure optimal performance for any application.
Product Form | Dimension Type | Size (Metric) | Size (Imperial) |
Bars | Diameter | 20 mm – 300 mm | 0.8 in – 12 in |
Length | 300 mm – 6000 mm | 12 in – 236 in | |
Plates | Thickness | 5 mm – 100 mm | 0.2 in – 4 in |
Width | 50 mm – 1200 mm | 2 in – 47 in | |
Length | 200 mm – 3000 mm | 8 in – 118 in | |
Rounds | Diameter | 25 mm – 250 mm | 1 in – 10 in |
Length | 100 mm – 4000 mm | 4 in – 157 in | |
Forgings | Thickness | 30 mm – 250 mm | 1.2 in – 10 in |
Length | 200 mm – 3000 mm | 8 in – 118 in | |
Flat Bars | Thickness | 10 mm – 100 mm | 0.4 in – 4 in |
Width | 50 mm – 1200 mm | 2 in – 47 in | |
Length | 100 mm – 4000 mm | 4 in – 157 in |
A10 Tool Steel Applications
A10 tool steel’s high toughness and excellent dimensional stability under heat treatment make it ideal for tooling applications that experience moderate wear and high stress. Its strength is more suitable for applications that require durability and toughness rather than extreme hardness.
- Cold Forming Dies: Used for blanking, bending, and stamping operations.
- Plastic Molds: Ideal for plastic injection molds due to its durability during high-volume molding.
- Cutting Tools: Used in the production of shear blades, punches, and dies for medium-duty cutting tasks.
- Forming Rolls: Applied in shaping processes, including automotive and aerospace manufacturing.
- Gauges and Measuring Tools: Utilized for thread gauges, standard gauges, and other precision instruments.
- Cams and Bushings: Common in automotive and industrial components.
- Roller Dies: Employed for high-precision parts in automotive and other industries.
- Machine Tool Parts: Includes mandrels, sleeves, and bar feed rails.
Tailored A10 Tool Steel Solutions for Your Needs
At SteelPro Group, we specialize in A10 Tool Steel, available in various forms such as bars, plates, rounds, and forgings. Our team works closely with clients to provide customized sizes and solutions tailored to their specific needs.
In addition to our high-quality products, we offer precise heat treatment services that enhance the steel’s performance, ensuring optimal hardness, toughness, and wear resistance.