Contents
M2 High Speed Tool Steel: Properties, Process, Uses
- John
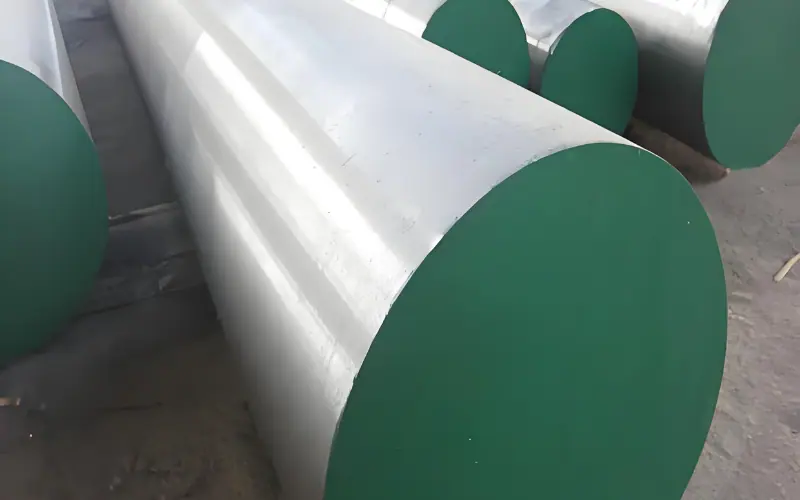
What Is M2 Tool Steel?
M2 tool steel is a high-speed steel (HSS) alloy made of tungsten and molybdenum, known for its combination of toughness, wear resistance, and red hardness. It is commonly used in cutting tools like drill bits, end mills, taps, and saw blades, as well as cold work punches and dies. Compared to T1 tool steel, M2 offers superior performance, especially in high-speed and light cutting applications.
Our M2 tool steel is engineered for high performance in demanding applications, offering superior hardness and durability. It is specifically designed to excel in high-speed cutting, punching, and molding, ensuring reliable and precise results.
What Is M2 Tool Steel Equivalent To?
The table below lists the equivalent codes for M2 tool steel across multiple specifications.
Standard | Equivalent Code |
GB | W6Mo5Cr4V2 |
ISC | T66542 |
ASTM | M2 |
UNS | T11302 |
DIN EN/DIN | 1.3343 |
Chemical Composition of M2 Tool Steel
The chemical composition of M2 tool steel is designed to optimize hardness, wear resistance, and high-temperature performance. Its high tungsten (W) and molybdenum (Mo) content enhance heat resistance, while chromium (Cr) and vanadium (V) improve hardness and wear properties.
The table below provides the detailed chemical composition of M2 tool steel.
Element | Composition (%) |
Carbon (C) | 0.78 – 0.88 (Reg C) |
0.95 – 1.05 (High C) | |
Chromium (Cr) | 3.75 – 4.5 |
Iron (Fe) | 78 – 82.4 |
Manganese (Mn) | 0.15 – 0.40 |
Molybdenum (Mo) | 4.5 – 5.5 |
Nickel (Ni) | ≤ 0.30 |
Silicon (Si) | 0.20 – 0.45 |
Tungsten (W) | 5.5 – 6.75 |
Vanadium (V) | 1.75 – 2.2 |
The high-carbon (0.95 – 1.05%) version of M2 offers increased hardness and wear resistance, while the regular carbon (0.78 – 0.88%) version provides improved toughness and impact resistance.
Physical Properties of M2 Tool Steel
M2 tool steel offers high density and good thermal stability, making it suitable for high-temperature applications. Its relatively low thermal expansion and electrical resistivity further enhance its performance in precision tools and molds. The table below outlines the key physical properties of M2 tool steel.
Property | Metric | Imperial |
Density | 8.14 g/cm³ | 0.294 lb/in³ |
Melting Point | 1,420 – 1,470°C | 2,588 – 2,678°F |
Specific Heat Capacity | 460 J/kg·K | 0.110 BTU/lb·°F |
Thermal Conductivity | 25 W/m·K | 17.2 BTU/hr·ft·°F |
Coefficient of Thermal Expansion | 5.5 × 10⁻⁶ /°C | 3.1 × 10⁻⁶ /°F |
Electrical Resistivity | 0.58 µΩ·m | 0.58 µΩ·m |
Mechanical Properties of M2 Tool Steel
M2 tool steel is known for its high strength and hardness, making it resistant to deformation and wear. It also offers good toughness and flexibility, helping it perform well under impact and stress. The table below shows the mechanical properties of M2 tool steel.
Property | Metric | Imperial |
Hardness (HRC) | 62 – 65 HRC | 62 – 65 HRC |
Tensile Strength | 1,800 – 2,100 MPa | 261,000 – 304,500 psi |
Yield Strength | 1,400 – 1,700 MPa | 203,000 – 246,500 psi |
Elongation | 4 – 8 % | 4 – 8 % |
Modulus of Elasticity | 210 GPa | 30,500 ksi |
Poisson’s Ratio | 0.27 – 0.30 | 0.27 – 0.30 |
Impact Toughness (Charpy V-Notch) | 10 – 30 J | 7.4 – 22.1 ft-lb |
Heat Treatment of M2 Tool Steel
SteelPro Group follows a precise and standardized heat treatment process for M2 tool steel, ensuring optimal hardness, toughness, and wear resistance to meet industry demands for durability and precision. The following sections outline the key stages of the M2 tool steel heat treatment process, from annealing to quenching and tempering.
Annealing
Heat at a rate not exceeding 222°C per hour (400°F per hour) to 829-843°C (1525-1550°F), and hold at this temperature for 1 hour per 25.44mm (1 inch) of thickness, with a minimum of 2 hours.
After holding, slowly cool in the furnace at a rate not exceeding 28°C per hour (50°F per hour) until reaching 538°C (1000°F), then continue cooling in the furnace or in air until ambient temperature is reached.
Hardening
Preheating
For Complex Shaped Tools: Heat at a rate not exceeding 222°C per hour (400°F per hour) to 593°C (1100°F), then continue heating evenly to 788-843°C (1450-1550°F).
For Simple Shaped Tools: Directly heat to 800℃ at a uniform speed.
Austenizing
After preheating, M2 tool steel is heated to the desired austenizing temperature to optimize its properties. Lower temperatures maximize toughness, while higher temperatures enhance hot hardness for better performance at high temperatures.
For Maximum Toughness:
To achieve the best toughness without focusing on hot hardness, the steel should be heated to slightly lower temperatures:
- Furnace Heating: Heat to 2075°F to 2175°F (1175°C to 1191°C).
- Salt Bath Heating: Heat to 2050°F to 2150°F (1121°C to 1177°C).
This range ensures the steel is tough and resilient, ideal for tools like punches and dies where impact resistance is key.
For Enhanced Hot Hardness:
If the goal is to maximize hot hardness (the ability to maintain hardness under high temperatures), you should heat the steel to the higher end of the temperature range:
- Furnace Heating: Heat to 2200°F to 2250°F (1204°C to 1232°C).
- Salt Bath Heating: Heat to 2175°F to 2225°F (1191°C to 1218°C).
This ensures the steel retains its hardness and performance under heat, making it ideal for cutting tools that face high temperatures during operation.
Quenching
Pressurized Gas:
Quenching in pressurized gas requires a rapid quenching rate, maintained below 538°C (1000°F). This ensures a fast cooling rate, promoting martensite formation and improving hardness.
Oil:
Quench to black (around 482°C or 900°F), then cool in still air to 66-51°C (150-125°F). Oil quenching offers a controlled cooling rate that minimizes distortion and cracking.
Salt Bath:
Quench in a salt bath held at temperatures between 538-593°C (1000-1100°F), then cool in still air to 150-125°F (66-51°C).
Tempering
Tempering should be performed immediately after quenching, as it relieves internal stresses and reduces brittleness. Heat to 552-566°C (1025-1050°F) and hold for at least 1 hour per 25.44mm (1 inch) of thickness. The final hardness after tempering will be in the range of HRC 59-62, depending on the specific tempering temperature.
M2 Tool Steel Product Forms
The following section provides a reference for the common product forms and size ranges of M2 tool steel. We also specialize in producing custom sizes beyond the typical ranges, offering flexibility to meet your specific dimensional requirements with tight tolerances for maximum precision.
Bars
Diameter: 10 mm to 300 mm (0.4 in to 12 in)
Length: 100 mm to 3000 mm (4 in to 236 in)
Plates
Thickness: 5 mm to 100 mm (0.2 in to 4 in)
Width: 100 mm to 1000 mm (4 in to 40 in)
Length: 100 mm to 3000 mm (4 in to 118 in)
Rounds
Diameter: 10 mm to 150 mm (0.4 in to 6 in)
Length: 100 mm to 3000 mm (4 in to 157 in)
Flat Bars
Thickness: 5 mm to 100 mm (0.2 in to 4 in)
Width: 50 mm to 300 mm (2 in to 12 in)
Tool Blanks
Thickness: 10 mm to 100 mm (0.4 in to 4 in)
Width: 50 mm to 300 mm (2 in to 12 in)
M2 Tool Steel Applications
M2 is commonly used in die casting molds, hot forging and extrusion dies, injection molding tools, trimming and shearing dies, plastic molds, roller dies, turbine blade production, and heat treatment tools.
M2 Tool Steel Products and Services
At SteelPro Group, we offer a wide range of M2 tool steel products, including bars, rods, and custom parts. We also provide tailored processing options such as precision cutting, grinding, and heat treatment to ensure your components meet the highest standards.
In addition to M2, we offer H13 steel for high-heat applications, providing enhanced toughness and durability. With our expert support and reliable solutions, we help you optimize production and reduce downtime.