Contents
Water Hardened W1 Tool Steel: Properties, Process and Uses
- John
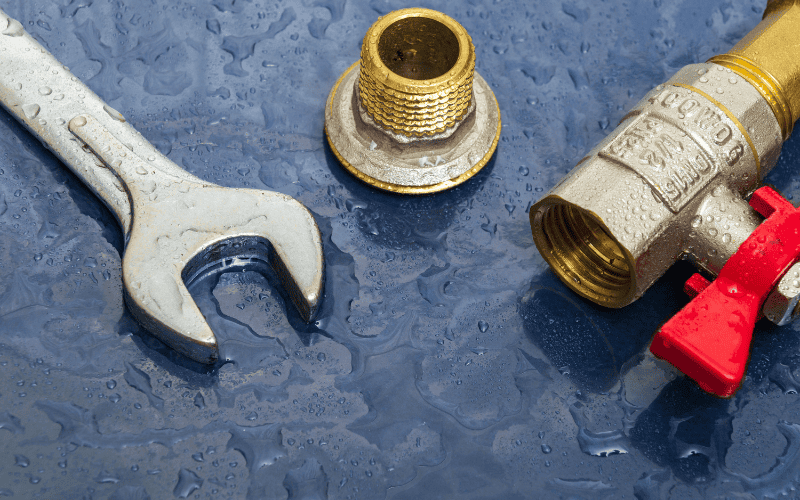
W1 tool steel is a great choice if you need a material that’s both tough and easy to machine. It is perfect for tools like cutting edges, pins, and shafts, offering solid wear resistance and the ability to harden quickly.
In this article, we will explore the key features, applications, and heat treatment steps for W1 tool steel. Whether you are just getting started or want to get the most out of this versatile material, we’ve got you covered.
What Is W1 Tool Steel?
W1 tool steel is a high-carbon steel composed with 0.70–1.50% carbon. It is part of the water-hardening tool steel group and is commonly categorized as cold-work tool steel. W1 is commonly used in the form of drill rods, bars, or rounds, and is meet standards like ASTM A686 and EN ISO 4957. Known for its good machinability and high hardness, W1 is often used in applications like shafts, pins, blacksmithing tools, and short-term wear tooling.
What Is W Grade Steel?
W grade steel is a group of water-hardening tool steels, primarily composed of carbon, with small amounts of alloying elements like chromium and vanadium. Common grades include W1, W2, and W3.
What Is The Difference Between W1 And W2 Steel?
W1 tool steel has a higher carbon content (0.70–1.50%) compared to W2 (0.90–1.10%), making W1 harder and more wear-resistant. However, W2 has slightly more manganese, which enhances its toughness and resistance to cracking. It performs better under higher temperature stresses than W1.
What Is The Difference Between W1 And 1095?
W1 steel has higher alloy content (manganese, silicon) for better wear resistance and toughness, making it ideal for cold work tooling. 1095 is a simpler carbon steel, mainly used for blades and cutting tools, with excellent edge retention but lower toughness compared to W1.
Equivalents Grades of W1 Tool Steel
Here is a helpful overview of the equivalent grades for W1 tool steel, recognized across various standards and specifications in different regions.
Standards | Grades |
UNS | T72301 |
SAE J437 | W108, W109, WhO, W112 |
SAE J438 | W108, W109, W110, W112 |
EN ISO 4957 | 1.1545 / C105U |
Chemical Composition of W1 Tool Steel
Here’s a typical steel ladle analysis for W1 tool steel, showing the precise chemical composition that ensures the steel meets the required specifications for your projects:
Element | Composition (%) |
Carbon (C) | 0.70 – 1.50 |
Manganese (Mn) | 0.10 – 0.40 |
Silicon (Si) | 0.10 – 0.40 |
Chromium (Cr) | 0.15 |
Nickel (Ni) | 0.2 |
Molybdenum (Mo) | 0.1 |
Tungsten (W) | 0.15 |
Vanadium (V) | 0.1 |
Copper (Cu) | 0.2 |
Phosphorus (P) | Max 0.025 |
Sulfur (S) | Max 0.025 |
Physical Properties of W1 Tool Steel
Here is a quick reference table for the physical properties of W1 tool steel cross both metric and imperial systems.
Property | Metric Unit | Imperial Unit |
Density | 7.83 g/cm³ | 0.283 lb/in³ |
Melting Point | 1435°C | 2615°F |
Thermal Conductivity | 30–40 W/m·K | 17.5–23.0 BTU·ft/h·ft²·°F |
Specific Heat Capacity | 0.48 J/g·K | 0.115 BTU/lb·°F |
Electrical Resistivity | 0.0007 Ω·cm | 0.0003 Ω·in |
Hardness (HRC) | 50 HRC to 55 HRC | 50 HRC to 55 HRC |
Coefficient of Thermal Expansion | 11–12 µm/m·°C | 6.1–6.7 µin/in·°F |
Mechanical Properties of W1 Tool Steel
This table provides a comparison of the key mechanical properties of W1 tool steel, giving you a clear view of its performance.
Property | Metric Unit | Imperial Unit |
Ultimate Tensile Strength | 1680 MPa | 244,000 psi |
Yield Tensile Strength | 1500 MPa | 218,000 psi |
Hardness (after heat treatment) | 50–55 HRC | 50–55 HRC |
Impact Toughness | 10–20 J (Charpy V-notch) | 7.4–14.8 ft-lb |
Bulk Modulus | ~140 GPa | ~20,000 ksi |
Shear Modulus | ~80 GPa | ~11,600 ksi |
Elastic Modulus | 200 GPa | 29,000 ksi |
Poisson’s Ratio (25°C) | 0.27–0.30 | 0.27–0.30 |
Fatigue Strength | 600 MPa | 87,000 psi |
Key Features of W1 Tool Steel
Outstanding Hardness
W1 tool steel offers excellent hardness due to its high carbon content (0.70–1.50%), making it highly resistant to wear. This makes it ideal for cutting tools, shafts, and pins that need to hold up against friction over time.
- Limitation: The same hardness makes W1 more prone to brittleness, especially in thicker sections, meaning it can crack or break under heavy impact or shock loads.
Moderate Toughness for Low-to-Medium Stress
W1 offers a solid balance between hardness and toughness, making it ideal for applications with moderate stress or where the material will not face excessive impact.
- Limitation: If your project requires high impact resistance, a tougher steel like S7 might be a better fit.
Good Machinability in Annealed Condition
W1 steel is relatively easy to machine when in its annealed state, making it an excellent choice for precise cuts or tight tolerances.
- Limitation: Compared to lower-carbon steels like 1045, W1 is harder to machine in its hardened form.
Water-Hardening for Efficient Heat Treatment
W1 is a water-hardening steel, meaning it can be hardened quickly and cost-effectively with water quenching. This makes it a popular choice for mass production and high-volume applications.
- Limitation: The fast quenching process can cause warping or distortion, particularly in thicker parts. Compared to air-hardening steels like A2, W1 is more sensitive to dimensional changes during heat treatment.
Fabrication and Process of W1 Tool Steel
Forging And Forming
W1 tool steel can be forged effectively within the temperature range of 1900°F to 1550°F (1038°C to 843°C). It is critical to avoid forging below 1500°F (815°C), as doing so can compromise the steel’s structural integrity. Also avoid overheating, as excessive temperatures can lead to grain growth and loss of toughness.
W1 is difficult to form due to its hardness, but can be shaped effectively when in the annealed state.
Heat Treatment
Annealing
Annealing softens W1 tool steel, making it much easier to machine and helping relieve any internal stresses. It’s the first step if you plan on machining before hardening.
- Heating: Heat the steel to 1350°F to 1450°F (732°C to 788°C). This allows the steel to heat evenly.
- Soaking: Keep the steel at this temperature for about 1 to 2 hours, depending on how thick the material is.
- Cooling: After soaking, cool the steel slowly in a furnace to avoid warping, then let it air cool to room temperature. This helps to relieve internal stresses without damaging the steel.
Hardening
This is where the steel becomes harder and more resistant to wear, giving it the durability needed for cutting and tooling applications.
- Preheating: First, heat the steel to about 1200°F (649°C) to ensure even heating before hardening.
- Hardening: Then, heat it to 1425°F to 1475°F (774°C to 802°C) for about 30 minutes per inch of thickness. This ensures the heat penetrates the material fully.
- Quenching: Once you’ve reached the target temperature, quench the steel quickly in water or brine (brine is better for achieving harder steel). Make sure to quench at the right temperature to avoid excessive distortion.
Tempering
Tempering is essential to reduce brittleness and achieve the final hardness. It’s done after hardening to fine-tune the steel’s properties.
- After hardening, temper the steel at temperatures between 300°F and 1200°F (149°C to 649°C) based on the hardness you want to achieve. Soak for 1 to 2 hours, then air cool.
- If the steel experiences excessive stress or distortion during heating or quenching, a second annealing cycle may be performed. This can reduce brittleness even further.
Machining
W1 tool steel has good machinability, comparable to other high-carbon tool steels like O1 or A2, but it is more difficult to machine than low-carbon steels. It is typically machined in its annealed state to enhance ease of cutting. Standard high-speed steel (HSS) or carbide tools are commonly used to achieve smooth cuts and extend tool life.
Welding
W1 tool steel is not easily weldable due to its high carbon content, which increases the risk of cracking. If welding is necessary, it’s important to preheat the steel to around 500°F to 1200°F (260°C to 649°C) to reduce thermal shock.
Post-welding heat treatment, such as tempering or stress relieving, is recommended to restore the material’s properties.
Applications of W1 Tool Steel
W1 tool steel is commonly used in tooling and precision parts in industries such as automotive, machinery, and manufacturing. It is particularly suited for small to medium-scale production where high hardness and wear resistance are needed.
Cutting Tools
W1 is used to make drill rods, taps, reamers, and dies, providing excellent edge retention and wear resistance for general cutting tasks.
Forming and Shaping Tools
It is also used for blades, cutting edges, and form tools to shape materials like wood, plastic, and mild metals, maintaining sharpness even under moderate stress.
Punches and Dies
W1 is ideal for punches, dies, and stamping tools that require high hardness and durability, especially in the automotive and manufacturing industries.
Jigs and Fixtures
The steel’s toughness makes it a good choice for jigs, fixtures, and specialized tooling that need both precision and resistance to wear.
Other Tooling Applications
W1 is also used for blacksmithing tools, pins, and shafts in various mechanical and production processes.
- Is W2 Steel Good for Knives?
Yes, W2 steel is great for knives. It offers excellent edge retention, wear resistance, and toughness, making it ideal for sharp, durable blades that can handle stress without chipping.
Products Forms of W1 Tool Steel
W1 tool steel is available in several standard forms to ensure its versatility for different applications. Below are the most common forms and their typical applications:
Drill Rods
Uses: Ideal for precision drilling and cutting, W1 drill rods are often used in the production of small tools, jigs, and fixtures.
Bars
Uses: W1 tool steel bars are commonly used for making dies, punches, and other cutting tools that require durability and wear resistance.
Rounds
Uses: Round bars are often used for manufacturing shafts, pins, and other cylindrical components.
Get the Right W1 Tool Steel for Your Needs
Are you looking for W1 tool steel that delivers consistent quality and performance for your applications? At SteelPro Group, we supply drill rods, bars, and rounds in W1 steel, all meeting industry standards like ASTM A686 and EN ISO 4957.
In addition to premium materials, SteelPro Group provides custom sizing, precise cutting, and tailored heat treatment services. We also offer fast shipping and technical support to help you make the most out of your W1 steel, regardless of project size or complexity.
If you require D2 tool steel with enhanced wear resistance, SteelPro Group can also provide high-quality products.