Contents
High Speed Tool Steel Guide
- John
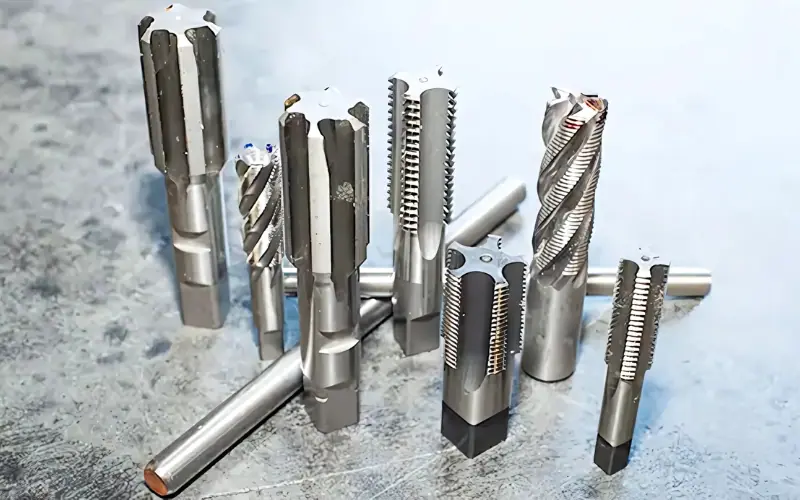
High-speed steel (HSS) has revolutionized the world of machining. At SteelPro Group, we specialize in providing high-quality HSS solutions tailored to your needs.
What Is High Speed Steel?
High-speed steel is an alloy tool steel renowned for maintaining hardness and wear resistance at elevated temperatures. Classified into tungsten-based (T-series), molybdenum-based (M-series), and cobalt-based (K-series) types, it exhibits exceptional hardness, wear resistance, and heat resistance. With superior red hardness compared to traditional carbon steel tools, it achieves 62-65 HRC after heat treatment. Primarily utilized in high-speed machining operations, it’s ideal for cutting tools like drills and end mills.
Why Is It Called High Speed Steel?
It is called “high-speed steel” because it retains its hardness at high cutting speeds, even when heated to around 1100°F (593°C). This ability, known as red hardness, allows it to perform at speeds much higher than traditional carbon steels.
What Are The Properties of High Speed Steel?
High Alloy Content: High-speed steel contains a mix of elements like tungsten, molybdenum, chromium, vanadium, and sometimes cobalt.
High Hardness: After heat treatment, HSS typically achieves a hardness range of 62-65 Rockwell C (HRC). It retains its hardness at elevated temperatures.
Exceptional Wear Resistance: The carbide content (mainly tungsten, molybdenum, and vanadium carbides) in HSS significantly enhances wear resistance. It maintains cutting edge much longer than other tool steels.
Balanced Toughness: HSS has a good balance between hardness and toughness. While not as tough as cold work tool steels, it is tougher than carbide tools, which are brittle in comparison.
Relatively High Cost: High-speed steel is more expensive than conventional carbon steel due to its alloying elements and specialized heat treatment. However, the cost is offset by its ability to perform at higher speeds.
Overview of High-Speed Steel Types And Grades
To meet the diverse needs of cutting and machining operations, HSS is classified into several categories based on its alloying elements and performance characteristics. Below are the primary classifications:
Tungsten-Based (T-Series)
Known for its high tungsten content, it provides excellent wear resistance and red hardness, ideal for high-temperature cutting tools like milling cutters.
- M1: A general-purpose HSS suitable for interrupted cutting, offering consistent performance across various applications.
- M7: A N-modified HSS grade with excellent hardness, commonly used for twist drills and other precision tools.
Molybdenum-Based (M-Series)
With a higher molybdenum content, it is more cost-effective than T-Series while delivering comparable performance, widely used for general-purpose tools such as drills and taps.
- M2: The most widely used HSS, balancing durability, cutting efficiency, and cost, ideal for general-purpose tools.
- M2 EUR: A high-C variant of M2, commonly used in Europe, offering slightly higher hardness with a small reduction in toughness.
- M3-1: Designed with increased C and V content, providing better wear resistance and maintaining properties under high-temperature conditions.
- M3-2: Features higher C and V than M3-1, significantly enhancing cutting performance and tool life.
- M4: Known for high wear resistance due to a large volume of hard VC, making it ideal for demanding cutting applications.
Cobalt-Based (K-Series or Subset of M-Serie)
Enhanced with cobalt (e.g., M35, M42), it offers superior red hardness and heat resistance, perfect for cutting hard materials like stainless steel.
- M35: A Co-enhanced version of M2, improving hardness and red hardness, widely used for cutting tools in Europe.
- M42: A super HSS with high Co content, delivering exceptional hardness and wear resistance, relying on hardness rather than large VC amounts.
- CPM Rex76/M48: A premium PM HSS designed for long production runs, heavy-duty machining, and abrasive materials, commonly used for hob tools.
High-speed steel also includes two unique type as follows:
CPM grades like CPM M4 and CPM T15 are made using powder metallurgy, ensuring a uniform microstructure that enhances wear resistance and toughness. Their advanced manufacturing process makes them more expensive but ideal for high-stress precision applications.
- CPM4: A PM variant of M4 that offers superior toughness and reliability, particularly in cold-work applications like punches and dies.
- CPMT15: A PM variant of T15 with greatly improved toughness and grindability, making it a popular choice for broaching tools.
- PM30: A Co-enhanced PM variant of M3-2 that combines high toughness with excellent cutting efficiency, suitable for high-performance applications.
Intermediate high-speed steel has less tungsten and molybdenum, making it more affordable while still strong and tough. It is often used in aerospace and industrial parts where high-speed cutting or extreme heat resistance is not needed, and easier processing is preferred.
- M50: A cost-effective intermediate HSS, suitable for tools like twist drills and woodworking equipment where red hardness is less critical.
Chemical Composition of High Speed Steel Grades
Type | Grades | C | Mn | Si | Cr | W | Mo | V | Co |
T-Series | M1 | 0.82 | 0.25 | 0.4 | 3.75 | 1.55 | 8.5 | 1.15 | – |
M-Series | M2 | 0.85 | 0.25 | 0.3 | 4.15 | 6 | 4.8 | 1.85 | – |
M-Series | M2 EUR | 0.91 | 0.25 | 0.3 | 4 | 6.15 | 4.85 | 1.75 | – |
M-Series | M3-1 | 1.04 | 0.25 | 0.3 | 3.9 | 5.9 | 4.9 | 2.35 | – |
M-Series | M3-2 | 1.21 | 0.25 | 0.3 | 4.1 | 6 | 5.5 | 2.9 | – |
M-Series | M4 | 1.33 | 0.25 | 0.3 | 4.5 | 5.5 | 5.5 | 3.85 | – |
PM-Series | CPM M4 | 1.45 | 0.25 | 0.3 | 4.5 | 5.5 | 5.5 | 3.85 | – |
T-Series | M7 | 1 | 0.3 | 0.4 | 3.6 | 1.6 | 8.55 | 1.9 | – |
Co-Series | M35 | 0.93 | 0.3 | 0.3 | 4.2 | 6.25 | 5 | 1.9 | 4.9 |
Co-Series | M42 | 1.08 | 0.3 | 0.45 | 3.85 | 1.5 | 9.5 | 1.2 | 8 |
Co-Series | CPM Rex 76/M48 | 1.55 | 0.2 | 0.4 | 4 | 10 | 5.25 | 3.1 | 9 |
Int-Series | M50 | 0.83 | 0.3 | 0.3 | 4.1 | 1.15 | 4.5 | 1.05 | – |
Int-Series | M52 | 0.9 | 0.3 | 0.3 | 4.2 | 1.15 | 4.5 | 1.95 | – |
PM-Series | CPMT15 | 1.6 | 0.3 | 0.3 | 4.25 | 12.25 | 0.75 | 5 | 5 |
PM-Series | PM30 | 1.28 | 0.3 | 0.3 | 4.2 | 6.4 | 5 | 3.1 | 8 |
Performance Comparison of High Speed Steel Grades
Grades | HRC | Machinability |
M1 | 55 | 65 |
M2 | 50 | 65 |
M2 EUR | 50 | 65 |
M3-1 | 40 | 66 |
M3-2 | 35 | 66 |
M4 | 35 | 65 |
CPM4 | 45 | 65 |
M7 | 45 | 66 |
M35 | 45 | 65 |
M42 | 35 | 68 |
CPM Rex76/M48 | 15 | 69 |
M50 | 65 | 63 |
CPMT15 | 25 | 67 |
PM30 | 30 | 67 |
What Is High Speed Steel Used For?
- Drill Bits
- End Mills
- Taps and Dies
- Reamers
- Saw Blades
- Lathe Tools
- Gear Cutters
- Broaches
- Punches
When Was High Speed Steel Invented?
High-speed steel (HSS) was invented in 1910 by Frederick Winslow Taylor and Maunsel White. This marked a breakthrough in cutting tool technology. The following is a brief overview of the key milestones in the history of high-speed steel.
1868: Robert Forester Mushet developed Mushet steel, the precursor to modern HSS. It contained 2% C, 2.5% Mn, and 7% W, and hardened upon air cooling.
1899–1900: Frederick Winslow Taylor and Maunsel White at Bethlehem Steel improved tool steels like Mushet steel through experiments. Their heat treatment process allowed steel to retain hardness at high temperatures, tripling cutting speeds. This became the Taylor-White process, showcased at the 1900 Paris Exhibition.
1910: The first officially classified HSS, AISI T1, was introduced and patented by Crucible Steel Co.
WWII Era: Material shortages led to the development of molybdenum-based HSS, such as AISI M1 and M2, offering cost-effective alternatives to tungsten-based HSS. These grades became widely used.
High-Speed Steel vs. Carbon Steel
If durability and cutting efficiency are your priorities, HSS outperforms carbon steel by a wide margin.
HSS is designed for high-temperature operations, maintaining its hardness and cutting ability even when heated to around 1100°F (593°C). This makes it ideal for machining tools like drills and taps, especially at high speeds.
In contrast, carbon steel, while more affordable and easier to sharpen, loses its hardness and edge retention under high heat, limiting it to low-speed or hand-tool applications.
High-Speed Steel vs. Carbide
Carbide offers higher performance for specific tasks. HSS remains a versatile, cost-effective option for a broader range of uses.
Carbide tools excel in high-speed, high-precision machining and can cut harder materials with superior wear resistance. However, carbide is brittle, making it less suitable for interrupted cuts or impact-prone operations.
HSS, on the other hand, is tougher and more forgiving, making it ideal for general-purpose tools and applications requiring durability under stress.
Partner with SteelPro Group for High-Speed Steel Excellence
SteelPro Group is committed to delivering top-grade HSS products and expert guidance to help you achieve your goals. Whether you’re upgrading your tools or planning new projects, contact us today to discover how our solutions can make a difference. Let’s build your success together!