Contents
High-strength Low-alloy Steel Overview: Grades, Properties And Uses
- John
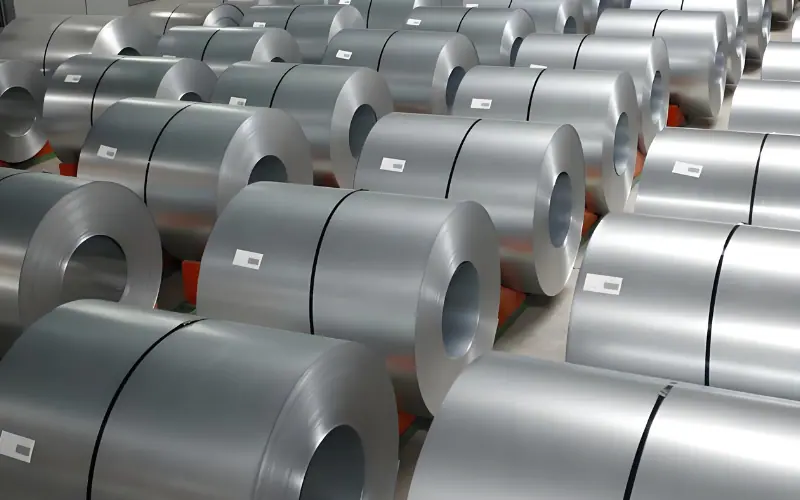
High-strength low-alloy (HSLA) steel has become a revolutionary material in contemporary industrial uses. With its superior strength-to-weight ratio, exceptional durability, and cost efficiency, HSLA steel is steadily replacing traditional carbon steel in numerous sectors.
This guide delves into its chemical composition, various grades, manufacturing processes, and why choosing SteelPro Group HSLA steel can significantly enhance your projects.
What Is High-strength Low-alloy (HSLA) Steel?
High-strength low-alloy (HSLA) steel is a type of alloy steel that is stronger and more resistant to corrosion than regular carbon steel. Unlike other steel types, HSLA is defined by its mechanical performance rather than chemical composition. With carbon content ranging from 0.05% to 0.25%, it maintains both formability and weldability.
Small amounts of alloying elements, including vanadium, niobium, and titanium, strengthen HSLA steel by refining its microstructure. As a result, it offers yield strengths of 250 to 590 MPa (36,000 to 86,000 psi). This combination of properties makes HSLA steel ideal for structural applications such as truck frames, crane booms, and railcars.
Key Properties of HSLA Steel
- High Strength and Low Weight: Achieves 50% higher strength than carbon steel while reducing weight.
- Outstanding Resistance to Corrosion: Elements such as copper, chromium, and nickel safeguard against oxidation.
- Improved Weldability: Unlike traditional high-strength steels, HSLA steel maintains easy fabrication properties.
- Superior Ductility and Toughness: Withstands high-impact forces and extreme temperatures without cracking.
- Cost Efficiency: Reduces material usage and transportation costs due to lighter weight.
Common Types of HSLA Steel and Their Uses
Weathering Steel (COR-TEN®)
- Applications: bridges, construction, and outdoor structures.
This steel’s exceptional atmospheric corrosion resistance comes from its ability to form a stable, protective patina over time. This characteristic eliminates the need for painting or other corrosion-prevention coatings, reducing maintenance costs while ensuring long-term structural integrity.
Microalloyed Steel
- Applications: automotive frames and pressure vessels.
By adding small amounts of elements like vanadium and niobium, microalloy steel gains high strength and toughness while keeping its carbon content low. These properties make it ideal for automotive structures and industrial equipment that require a balance of strength, ductility, and lightweight performance.
Dual-phase HSLA Steel
- Applications: automotive crash structures.
Dual-phase steel features a microstructure of soft ferrite and hard martensite, allowing it to absorb significant amounts of energy during impact. This makes it particularly well-suited for vehicle crash zones and other safety-critical components.
Acicular Ferrite HSLA Steel
- Applications: oil pipelines and shipbuilding.
The fine, needle-like microstructure of acicular ferrite HSLA steel ensures exceptional toughness and resistance to crack propagation. These properties make it highly reliable for applications exposed to high pressures and harsh environmental conditions, such as pipelines and maritime structures.
High-strength Low-alloy Steel Chemical Composition
Element | Typical Range (%) |
Carbon (C) | 0.05–0.25 |
Manganese (Mn) | 0.50–1.65 |
Vanadium (V) | 0.01–0.10 |
Niobium (Nb) | 0.02–0.10 |
Titanium (Ti) | 0.01–0.05 |
Copper (Cu) | 0.20–0.50 |
Chromium (Cr) | 0.30–0.50 |
Nickel (Ni) | 0.10–0.40 |
Role of Each Element
- Carbon (C)
Carbon content is kept low to maintain weldability and formability while providing adequate strength. This balance ensures that the steel remains easy to shape without sacrificing its mechanical properties.
- Manganese (Mn)
Manganese contributes to toughness and hardenability. It also helps in refining the microstructure, which enhances the uniformity of the steel’s strength and toughness.
- Vanadium (V), Niobium (Nb), and Titanium (Ti)
These microalloying elements improve the steel’s strength through precipitation hardening and grain refinement. Vanadium and niobium improve tensile strength, while titanium boosts weldability and lowers the likelihood of fractures.
- Copper (Cu), Chromium (Cr), and Nickel (Ni)
Copper significantly improves corrosion resistance, making the steel more durable in outdoor and marine environments. Chromium and nickel further enhance the material’s resistance to corrosion and improve toughness, particularly at low temperatures.
- Zirconium (Zr), Calcium (Ca), and Rare Earth Elements
These trace elements are used to control the shape and distribution of sulfide inclusions. By modifying sulfides, they improve the steel’s formability, making it easier to process and shape into complex components.
HSLA Steel Grades and Mechanical Properties
Grade | Yield Strength (MPa/ksi) | Tensile Strength (MPa/ksi) | Applications | Notes |
A36 | ≥250 / 36 | ≥400 / 58 | General construction, including buildings and bridges. | Common mild steel. |
A572 | 290–450 / 42–65 | 415–485 / 60–70 | Bridge construction, building frames, and structural components. | Includes grades 42, 50, 55, etc. |
A588 | ≥345 / 50 | ≥485 / 70 | Outdoor structures such as bridges and facades. | – |
A606 | ≥345 / 50 | ≥485 / 70 | Roofing, siding, and building panels. | – |
A709 | 250–485 / 36–70 | 400–690 / 58–100 | Bridge decks, girders, and load-bearing structures. | Includes 50W and HPS 70W. |
A514 | ≥690 / 100 | ≥760 / 110 | Heavy construction and mining equipment. | Different hardness levels. |
S355 | 355 / 51.5 | 470–630 / 68–91 | European building frames, bridges, and offshore structures. | Includes S355J2, S355K2, etc. |
S500 | 500 / 72.5 | 590–700 / 85.5–101.5 | High-strength structural components. | – |
M270 | 250–485 / 36–70 | 400–690 / 58–100 | Bridge construction under AASHTO guidelines. | Often certified to A709 sp |
High-strength Low-alloy Steel Manufacturing Processes
SteelPro Group’s advanced production methods set a high standard for the manufacturing of high-strength low-alloy (HSLA) steel. Combining years of experience with state-of-the-art technology, we ensure each step in the process delivers precision, consistency, and superior performance.
Continuous Casting
Molten steel is cast into slabs or billets using our advanced continuous casting process. This ensures a uniform chemical composition, reduced impurities, and a high-quality material base for further processing.
Thermomechanical Controlled Processing (TMCP)
Our TMCP approach uses precise temperature control and deformation during rolling. By producing a fine-grained microstructure, we achieve exceptional toughness and strength while reducing the need for additional heat treatments.
Precipitation Strengthening:
We incorporate vanadium, niobium, and titanium to form fine precipitates, enhancing the steel’s strength and toughness without compromising ductility. These proprietary alloying techniques enable our HSLA steel to excel in both formability and durability.
Controlled Cooling and Accelerated Cooling (ACC)
Using innovative cooling systems, we ensure consistent microstructural transitions that improve ductility, toughness, and resistance to stress. This phase enhances the steel’s reliability for structural applications.
Direct Rolling and Final Forming
Our direct rolling process eliminates unnecessary reheating steps, ensuring the steel’s uniform microstructure and consistent mechanical properties. This results in cost savings and higher efficiency for our clients.
Advanced Welding Techniques (if applicable)
SteelPro Group employs specialized welding methods that retain the steel’s high strength and toughness. These advanced techniques reinforce the integrity of welded areas, ensuring long-lasting, high-performance results.
FAQs
What Is The Difference Between The Carbon Steel And HSLA Steel?
HSLA steel is designed to be stronger, lighter, and more corrosion-resistant than traditional carbon steel.
This is achieved by incorporating small amounts of alloying elements, which refine the grain structure and enhance mechanical properties. In contrast, carbon steel relies on higher carbon content to increase strength, often sacrificing ductility and weldability. As a result, HSLA steel offers better performance in applications requiring superior strength-to-weight ratios and environmental durability.
What Is The Difference Between Structural Steel And HSLA Steel?
HSLA steel is a type of structural steel that offers enhanced strength and toughness through alloying, whereas standard structural steel is primarily defined by its mechanical properties and shapes.
By using controlled amounts of alloying elements, HSLA steel achieves a higher strength-to-weight ratio and improved corrosion resistance. Standard structural steel grades often rely on simpler chemical compositions and may lack the advanced mechanical properties and environmental durability of HSLA steel.
Best HSLA Steel Solutions From SteelPro Group
SteelPro Group’s high-strength low-alloy (HSLA) steel offers exceptional performance benefits supported by detailed specifications and proven results:
- Cost Savings Through Material Efficiency: Our HSLA steel is 20–30% lighter than comparable carbon steels at the same strength levels, reducing material costs and transportation expenses.
- Superior Structural Performance: With yield strengths exceeding 345 MPa (50 ksi) and tensile strengths reaching up to 485 MPa (70 ksi), our steel consistently meets and surpasses industry requirements.
- Extended Service Life: Enhanced corrosion resistance reduces maintenance cycles and increases the longevity of structures, saving on long-term upkeep costs and preserving investment value.
- Optimized Fabrication Efficiency: Our steel’s excellent formability and weldability streamline production processes, reducing fabrication time and allowing for faster project completion.
SteelPro Group goes beyond providing top-quality HSLA steel by offering additional services that ensure project success:
- Tailored Processing: Precision cutting, shaping, and forming services ensure your project receives materials that match your exact specifications.
- Surface Treatments: We provide shot blasting, protective coatings, and galvanizing to enhance the steel’s durability and resistance to wear and corrosion.
- High-precision Manufacturing: With advanced production facilities and rigorous quality control, SteelPro Group ensures every batch meets the highest standards, delivering reliable and consistent performance.