Contents
A2 Vs D2 Tool Steel: Cold Work Steel Comparison
- John
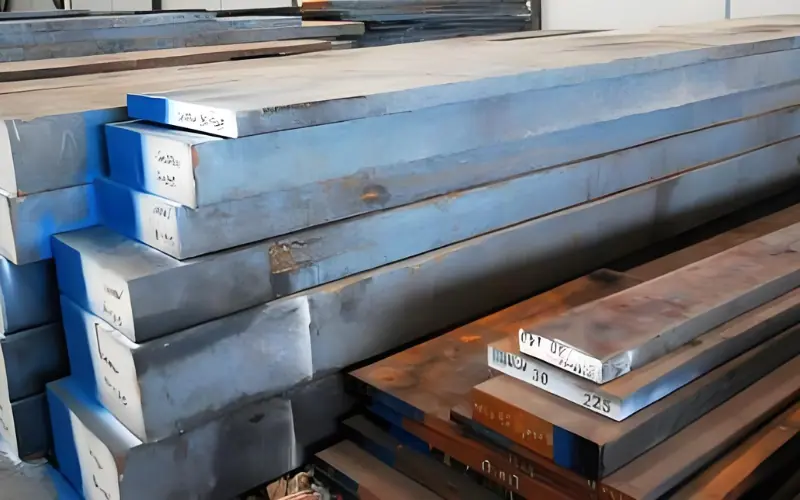
A2 and D2 tool steels are both cold work tool steel with high-carbon, high-chromium content.A2 provides a good balance of toughness and wear resistance, making it ideal for tools that require moderate wear resistance and high impact toughness.
In contrast, D2 is designed for uses that require enhanced hardness and resistance to abrasion. Its higher carbon and chromium content gives it exceptional edge retention and performance in high-wear environments. Compared to A2, it sacrifices some toughness.
Based on SteelPro Group’s experience working with other companies, both A2 and D2 tool steels are essential in cold work applications such as cutting tools, punches, and molds. If you’re unsure which one to choose, the decision ultimately depends on whether you prioritize toughness(A2) or wear resistance and hardness(D2).
A2 And D2 Tool Steel Different Properties
To help you better understand the differences between A2 and D2 tool steels, the following table compares their key properties.
Property | A2 Tool Steel | D2 Tool Steel |
Hardness | 57-62 HRC | 58-64 HRC |
Corrosion Resistance | Moderate | Superior (higher chromium content) |
Wear Resistance | Moderate | Superior (higher carbon and chromium content) |
Toughness | Higher toughness, better shock resistance | Lower toughness, more brittle |
Machinability | Better machinability in an annealed state | More difficult to machine due to higher carbide content |
Heat Treatment | Simpler heat treatment, less prone to distortion | More complex heat treatment, a higher risk of distortion |
Dimensional Stability | Good dimensional stability during heat treatment | Prone to size change during heat treatment |
Edge Retention | Good edge retention | Excellent edge retention, superior to A2 |
Cost | Generally less expensive | More expensive due to higher alloy content |
Chemical Composition of A2 Vs D2 Tool Steel
Element | A2 Tool Steel (%) | D2 Tool Steel (%) |
Carbon (C) | 1.00% | 1.4 – 1.6% |
Manganese (Mn) | 0.75% | ≤ 0.60% |
Silicon (Si) | 0.30% | ≤ 0.60% |
Chromium (Cr) | 5.00% | 11 – 13% |
Molybdenum (Mo) | 1.00% | 0.70 – 1.2% |
Vanadium (V) | 0.25% | ≤ 1.1% |
Nickel (Ni) | 0.30% Max | – |
Phosphorus (P) | 0.03% Max | ≤ 0.030% |
Sulfur (S) | 0.03% Max | ≤ 0.030% |
Cobalt (Co) | – | ≤ 1.0% |
- Different Carbon Content
A2 contains 1.00% carbon, while D2 has a higher range of 1.4% to 1.6%. The higher carbon in D2 enhances its hardness and resistance to abrasion. A2’s lower carbon content provides better toughness while still maintaining effective wear resistance.
- Different Alloy Composition
A2 has 5.00% chromium, while D2 contains 11% to 13%. D2 contains more chromium, offering enhanced protection against wear and corrosion compared to A2. Additionally, D2’s increased molybdenum and vanadium improve its toughness and high-temperature performance.
A2 offers a versatile solution for applications where both toughness and wear resistance are necessary.
Applications of A2 Vs D2 Tool Steel
A2 Tool Steel Uses
- Punches and Dies: For applications involving moderate impact, such as forming and punching tools.
- Cutting Tools: For knives, reamers, and chisels, where some impact resistance is required.
- Blanking Dies: Used in blanking operations where high toughness is needed without extreme wear resistance.
- Molds for Low-Volume Production: Suitable for small production runs where toughness and moderate wear resistance are key.
- Tooling for Stamping and Extrusion: For tools exposed to moderate wear and intermittent stress.
D2 Tool Steel Uses
- Cutting Tools: For cold-forming dies, slitters, and shear blades, where exceptional edge retention and abrasion resistance are critical.
- Punches and Dies: For heavy-duty stamping and die-cutting applications that experience high wear.
- Molds for High-Volume Production: Ideal for plastic molding and die casting, where long-lasting durability is required.
- Abrasive Machining Tools: Used for tools that face extreme abrasion, like grinding and cutting tools in high-wear environments.
In essence, choose A2 when your tool needs to absorb shock and resist cracking, like in heavy-duty forming operations. Opt for D2 when your priority is keeping a sharp edge for a long time, especially in high-volume cutting or forming processes where wear resistance is critical.
Different Process of A2 and D2 Tool Steel
Heat Treatment
A2 tool steel is easier to heat treat. It heats up and cools down with less risk of warping. This makes A2 ideal for tools that need to stay accurate after hardening. D2, however, requires more careful heat treatment because its higher carbon and chromium content can cause it to change shape during cooling.
Machining
Before hardening, A2 is easier to machine. Its composition allows for smoother cutting and shaping, which speeds up production and reduces tool wear. D2 is tougher to machine because it forms hard particles that can wear down cutting tools faster.
A2 and D2 Tool Steel for Your Manufacturing Needs
Whether you’re looking for toughness and moderate wear resistance with A2 or superior hardness and edge retention with D2 steel, SteelPro Group can help you make the best decision.
With tailored solutions and extensive industry expertise, SteelPro Group provides precise processing services for A2 and D2 tool steels, including heat treatment, machining, and custom sizing to meet your specific requirements.