Contents
What Is Alloy Steel? Properties, Types, Applications & More
- John
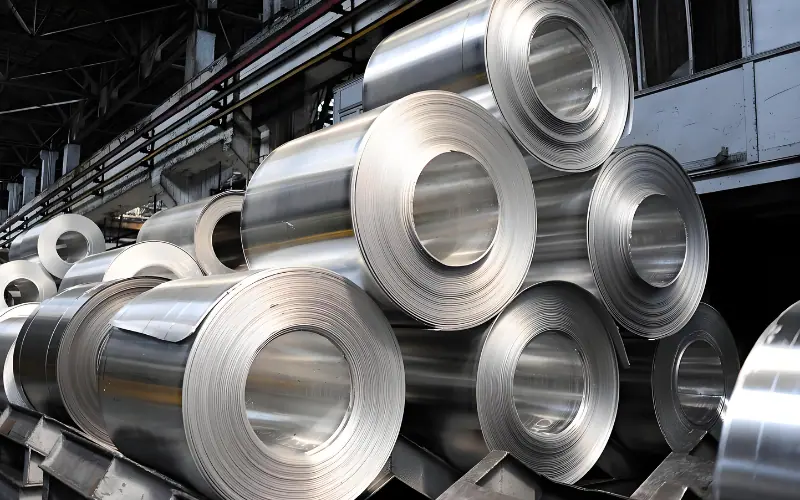
Over 60% of industrial machinery worldwide relies on alloy steel for essential parts. As various sectors require tougher, lighter, and more resilient materials, alloy steel has emerged as a fundamental component of contemporary engineering.
At SteelPro Group, we specialize in precision-engineered alloy steel trusted by automotive giants, aerospace leaders, and energy innovators. Let’s explore why this material dominates high-performance applications.
What Is Alloy Steel?
Alloy steel is an iron-carbon-based metal enhanced with strategic additions of elements like chromium, nickel, or molybdenum (1–50% content) to achieve superior mechanical properties. Unlike plain carbon steel, it balances:
- Strength: 2-4x higher tensile strength than mild steel
- Versatility: Customizable for specific thermal/chemical environments
- Cost Efficiency: Longer service life reduces replacement costs
Common applications include aircraft landing gear (e.g., 4340 steel), crusher jaws (manganese steel), and chemical reactor vessels (316 stainless).
Alloy Steel Properties
Alloying transforms steel into a high-performance material with:
- Outstanding Durability: Withstands significant weight and intense stress without warping or losing shape.
- Superior Corrosion Resistance: Resists rust, oxidation, and exposure to chemicals.
- Enhanced Temperature Stability: Retains structural integrity in extreme heat or sub-zero conditions.
- Improved Wear Resistance: Resists abrasion in high-friction applications.
- Optimized Machinability: Balances hardness with cutting, drilling, or welding ease.
Alloy Steel Chemical Composition: Elements & Roles
- Chromium (Cr) — Corrosion resistance, high-temperature oxidation resistance, hardenability.
Chromium reacts with oxygen to form a passive chromium oxide (Cr₂O₃) layer on the steel’s surface, blocking oxygen diffusion. At concentrations >12%, it enables stainless steel grades.
- Nickel (Ni) — Low-temperature toughness, fatigue resistance, austenite stabilization.
Nickel stabilizes the austenitic phase at low temperatures, refining grain boundaries and lowering the ductile-to-brittle transition temperature (DBTT).
- Molybdenum (Mo) — Creep resistance, high-temperature strength, weldability.
Molybdenum forms stable carbides (Mo₂C) that resist coarsening at elevated temperatures (>500°C), improving strength and weldability.
- Vanadium (V) — Strength, wear resistance, grain refinement.
Vanadium precipitates as V(C, N) particles during cooling, pinning grain growth, and enhancing strength and wear resistance through the Hall-Petch effect.
- Manganese (Mn) — Hardenability, deoxidation, hot workability.
Manganese combines with sulfur to form MnS inclusions, reducing hot shortness during forging and improving hot workability.
- Tungsten (W) — High-temperature hardness, wear resistance.
Tungsten forms ultra-hard tungsten carbides (WC) in tool steels, retaining hardness and wear resistance at temperatures between 600–800°C.
- Cobalt (Co) — Magnetic properties, red-hardness (hot hardness).
Cobalt inhibits carbide coarsening in high-speed steels (e.g., M42 grade), improving the steel’s magnetic properties and red-hardness for high-stress applications.
Common Alloy Steel Grades & Mechanical Properties
Grade | Tensile (MPa) | Yield (MPa) | Hardness | Best For |
1018 | 370–530 | 220–410 | 80–90 HRB | Structural steel, automotive parts |
1045 | 570–700 | 330–540 | 15–20 HRC | General machining |
4130 | 655–930 | 415–655 | 28–32 HRC | Aircraft and motorsports parts |
4140 | 655–1020 | 415–655 | 28–32 HRC | Hydraulic cylinders |
4340 | 745–1280 | 470–930 | 35–39 HRC | Aircraft components |
316L | 485–620 | 170–310 | 70–90 HB | Seawater pipelines |
8620 | 655–860 | 415–775 | 20–30 HRC | Gears, shafts |
D2 Tool | 1800–2200 | 1500–1800 | 58–62 HRC | Metal stamping dies |
52100 | 850–1050 | 500–800 | 60–65 HRC | Bearings, tool steels |
SteelPro stocks 100+ grades with same-day shipping from global hubs.
Alloy Steel Types
Alloy steels are classified primarily by their total alloy content (non-iron elements) and intended applications. While the low/medium/high alloy system focuses on composition, specialized steels are grouped by industry-specific performance requirements.
Low-Alloy Steel
Low-alloy steel contains up to 5% alloying elements, balancing cost and performance. It is used in applications needing higher strength but not extreme corrosion or high-temperature resistance. Common uses include oil and gas drilling tools, aircraft landing gears, and heavy-duty gears.
- Grades: AISI 4140, SAE 4340, EN 1.7225
Medium-Alloy Steel
Medium-alloy steel contains 5-10% alloying elements and targets specific mechanical properties. It improves durability, resistance to fatigue, and wearability. It is ideal for demanding applications like wind turbine axles, hydraulic machinery, and precision ball bearings.
- Grades: 52100, 6150, 8620
High-Alloy Steel
High-alloy steel contains more than 10% alloying elements, making it suitable for extreme environments. It is known for its exceptional corrosion resistance and high-temperature strength. It is commonly utilized in chemical manufacturing, aerospace, and food sectors.
- Grades: 304 Stainless, Toolox 44, Maraging 250
Other Alloy Steel Types
In addition to low, medium, and high-alloy steels, there are specialized types for specific needs:
- Stainless Steel: Offers excellent corrosion resistance, typically with at least 10.5% chromium.
- Tool Steel: Known for high hardness and wear resistance, ideal for cutting tools and molds.
- HSLA Steel (High-Strength Low-Alloy Steel): Contains micro alloys like Nb and V for strength without heat treatment. It is used in bridges and truck frames.
- AHSS Steel (Advanced High-Strength Steel): Features a multi-phase microstructure for high strength and energy absorption. It is used in automotive applications.
How Alloy Steel Is Made: Manufacturing Process
- Raw Material Preparation
Alloy steel begins with high-purity iron ore (≥98% Fe), which is smelted in blast furnaces to create base iron. Alloying agents, like chromium, nickel, or molybdenum, are prepared in powder or pellet form and mixed with the base iron. Up to 30% recycled steel scrap is also added to reduce cost and environmental impact.
- Alloy Design and Composition
Blending elements in liquid form is easier, but is more challenging in solid form. SteelPro engineers optimize steel compositions using Finite Element Method (FEM) simulations, ensuring precise material properties tailored for specific applications.
- Melting & Alloying
In this stage, materials are melted in an Electric Arc Furnace (EAF) at temperatures between 1,600–1,700°C using graphite electrodes. For smaller batches, induction furnaces provide tighter composition control.
After melting, deoxidizers like aluminum and silicon are used to remove oxygen. Calcium oxide (CaO) is added to improve ductility. Finally, alloying elements like chromium and nickel are introduced to achieve the steel’s required properties.
- Thermomechanical Processing
The steel is rolled at controlled temperatures. This process refines its grain structure and improves strength, toughness, and directional strength. These properties are essential for applications that require durability in high-stress environments.
- Heat Treatment
Heat treatment hardens the steel, enhancing its tensile strength and wear resistance.
- Ferritic and austenitic grades don’t respond to heat treatment.
- Carbon-rich steels are quenched between 760°C and 1300°C to achieve the necessary hardness.
- Martensitic steels, which have higher carbon content, are especially easy to harden.
Alloy Steel Forms & Applications
Alloy steel is available in various forms, such as bars, sheets, plates, pipes, tubes, wire, forgings, and castings. The specific form chosen depends on the intended application and required properties.
The common applications of alloy steel include:
- Automotive: Engine parts, transmission components, suspension systems.
- Aerospace: Aircraft components, turbine blades, structural elements.
- Construction: Structural beams, reinforcement bars, heavy machinery.
- Energy: Power plant components, oil drilling equipment, turbines.
- Tooling & Manufacturing: Molds, dies, cutting tools.
- Marine: Seawater pipelines, ship hulls, maritime equipment.
- Heavy Machinery: Mining, construction, and agricultural equipment.
- Medical: Surgical instruments, implants, medical devices.
FAQs About Alloy Steel
Q: Is Alloy Steel Magnetic?
A: Most grades are magnetic, but austenitic stainless steels (e.g., 304) lose magnetism when cold-worked.
Q: Does Alloy Steel Rust?
A: Alloy steel can rust if exposed to moisture and oxygen, though certain alloys, such as stainless steel, offer increased corrosion resistance.
Q: Is Alloy Steel Strong?
A: Yes, alloy steel is known for its high strength, which can be further enhanced by adjusting its composition and undergoing heat treatment.
Q: How Does Alloy Steel Compare To Aluminum?
A: Alloy steel offers 3x higher strength but weighs 2.8x more. We help clients optimize material selection.
Q: Why Choose SteelPro Group?
A: With over 50 years of expertise, SteelPro Group offers 24/7 technical support and holds ASTM/EN/DIN certifications.
Alloy Steel Solutions with Expert Support
Alloy steel powers innovation, from skyscraper beams to microsurgical tools. SteelPro Group leads the way in alloy steel solutions, combining advanced metallurgy with exceptional service to meet your needs.