Contents
Different Steel Types Used In The Automotive Industry
- John
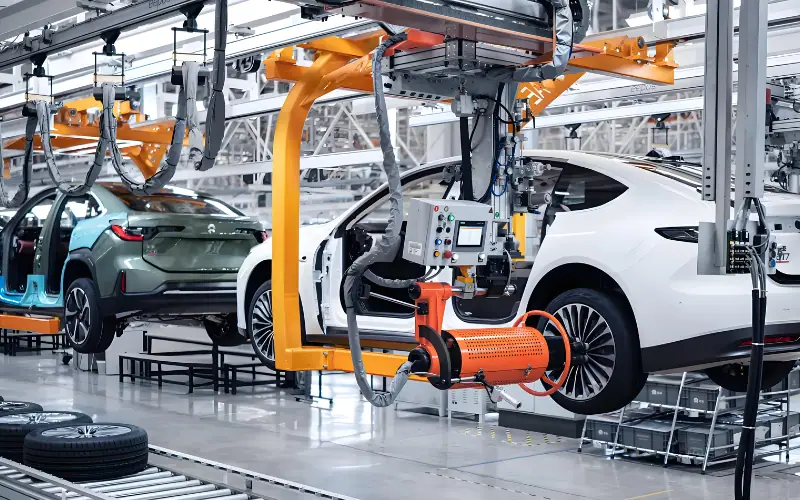
Steel has served as the foundation of vehicle production for more than a hundred years, prized for its robustness, longevity, and ability to ensure safety. As the industry evolves, automakers continuously refine their material choices to enhance fuel efficiency, reduce emissions, and improve crash resistance.
SteelPro Group delivers high-quality automotive steel solutions, guaranteeing that producers have the appropriate materials available. In this article, we’ll explore the key steel types used in cars and their specific applications, helping you understand their critical role in modern automotive engineering.
What Type of Steel is Used in Cars?
There are five categories of steel, each fulfilling a specific function in automobile manufacturing. Low-carbon steel offers flexibility, high-carbon steel provides superior durability, stainless steel resists corrosion, galvanized steel prevents rust, and Advanced High-Strength Steel (AHSS) enhances safety while reducing weight. Together, these materials shape the performance, lifespan, and cost efficiency of modern cars.
The Evolution of Steel in Automotive Manufacturing
The use of steel in cars dates back to the early 20th century when manufacturers transitioned from wood and iron to more durable metal structures. As vehicle designs became more advanced, the demand for stronger and lighter materials increased. The introduction of high-strength steels in the late 20th century revolutionized automotive engineering, making modern cars safer, more fuel-efficient, and structurally sound.
Today, advancements in metallurgy continue to refine steel’s properties, allowing automakers to enhance crash protection while reducing overall vehicle weight.
Steel Types, Grades, and Auto Applications: Quick Overview
The table below outlines the main characteristics and typical uses of each type of steel in the automotive industry:
Steel Type | Typical Grades | Applications |
Low-Carbon Steel | 1010, 1018, 1020 | Chassis, body panels, fuel tanks |
High-Carbon Steel | 1060, 1080, 1095 | Suspension springs, high-stress drivetrain parts |
Stainless Steel | 304, 409, 430 | Exhaust systems, heat shields, fuel lines |
Galvanized Steel | DX51D, DX53D, Z275 | Outer body panels, underbody structures, doors |
AHSS (Advanced High-Strength Steel) | DP780, DP980, TRIP 690 | Safety cages, impact beams, structural reinforcements |
Low-Carbon Steel: The Backbone of Car Frames
Low-carbon steel is one of the most commonly used materials in automotive manufacturing due to its high ductility, ease of forming, and cost-effectiveness. With a carbon percentage between 0.05% and 0.25%, it is comparatively pliable and ductile, making it perfect for forming into sizable structural parts.
Key Properties of Low-Carbon Steel in Cars
- High Ductility – Easily molded into various shapes without cracking.
- Excellent Weldability – Simplifies the joining process for car assembly.
- Good Impact Resistance – Absorbs energy in crashes, enhancing vehicle safety.
- Cost-Effective – More affordable than higher-carbon steels, reducing production costs.
Low-carbon steel is widely used in automotive construction, especially for chassis, body panels, and fuel tanks, where flexibility and cost efficiency are crucial. It effectively absorbs shocks while preserving its structural strength, making it an essential material for automotive frames. Although not as strong as other steel types, it is often reinforced with high-strength materials in critical areas to enhance performance and safety.
High-Carbon Steel: Strength for Critical Components
High-carbon steel is known for its exceptional hardness, wear resistance, and strength, making it essential for high-stress automotive components. With a carbon content between 0.6% and 1.0%, it is significantly harder and more brittle than low-carbon steel, offering superior durability for parts exposed to heavy loads and constant friction.
Key Properties of High-Carbon Steel in Cars
- High Strength and Hardness – Resists deformation under extreme stress.
- Superior Wear Resistance – Perfect for parts exposed to constant rubbing and collision.
- Lower Ductility – Less flexible than low-carbon steel, making it unsuitable for forming large body panels.
Due to these properties, high-carbon steel is primarily used in suspension springs, drivetrain components, and high-stress structural parts that require rigidity and durability. While its brittleness limits its use in load-bearing structures, it plays a crucial role in reinforcing areas that experience heavy wear over time.
Stainless Steel: Corrosion Resistance and Aesthetic Appeal
Stainless steel is extensively utilized in vehicle production due to its resistance to rust, long-lasting properties, and ability to withstand high temperatures. In contrast to regular steel, it has a minimum of 10.5% chromium, which creates a protective oxide coating that shields it from corrosion and oxidation.
Key Properties of Stainless Steel in Cars
- Excellent Corrosion Resistance – Withstands exposure to water, road salt, and extreme weather.
- High Durability – Maintains structural integrity under high temperatures and mechanical stress.
- Aesthetic Appeal – Provides a polished, high-quality finish for visible components.
Stainless steel is commonly used in exhaust systems, heat shields, and fuel lines, where resistance to rust and extreme temperatures is essential. It is also found in decorative trim and certain fasteners, enhancing both performance and aesthetics. While heavier and more expensive than other steel types, its longevity and resistance to environmental damage make it an essential material in modern automotive engineering.
Galvanized Steel: Enhanced Rust Protection
Galvanized steel is a commonly utilized material in vehicle production because of its excellent resistance to rust and long-lasting strength. It is created by applying a coating of zinc onto steel, which serves as a shield against water, salt from roads, and other damaging substances. This process significantly extends the lifespan of steel components, making it essential for vehicles exposed to harsh environmental conditions.
Key Properties of Galvanized Steel in Cars
- High Corrosion Resistance – The zinc layer stops rust from developing, even if the surface is damaged.
- Cost-Effective Longevity – Provides extended durability at a lower cost than stainless steel.
- Excellent Structural Integrity – Maintains strength while offering protection from environmental damage.
Galvanized steel is commonly used in outer body panels, underbody structures, and doors, where rust prevention is crucial. Its ability to withstand exposure to water, dirt, and chemicals helps maintain vehicle integrity over time. While not as strong as high-carbon or AHSS, its balance of affordability, formability, and rust resistance makes it a preferred choice for many automakers.
Advanced High-Strength Steel (AHSS): Lightweight and Safe
Advanced High-Strength Steel (AHSS) is among the most important breakthroughs in contemporary vehicle production. It offers exceptional strength while remaining lightweight, making it a crucial material for improving both vehicle safety and fuel efficiency. AHSS is engineered through specialized heat treatments and alloying techniques, resulting in a steel type that is far stronger than conventional steel without excessive weight.
Key Properties of AHSS in Cars
- High Strength-to-Weight Ratio – Increases crash protection while reducing vehicle weight.
- Superior Energy Absorption – Enhances safety in collisions by distributing impact forces effectively.
- Improved Fuel Efficiency – Helps automakers meet emissions regulations by reducing overall vehicle mass.
AHSS is primarily used in safety cages, impact beams, and structural reinforcements, where its ability to withstand extreme forces is essential. As automakers continue to prioritize vehicle safety and sustainability, AHSS is becoming a dominant material in car design, enabling manufacturers to produce stronger, lighter, and more fuel-efficient vehicles.
Advantages of Steel as an Automotive Material
Structural Integrity and Safety
Steel provides the rigid framework needed for crash protection, absorbing and distributing impact forces to enhance occupant safety. Advanced High-Strength Steel (AHSS) reinforces crumple zones and side structures, improving a vehicle’s ability to withstand collisions.
Cost-Effectiveness and Availability
Steel is more affordable and readily available than lightweight alternatives, making it the most practical choice for mass production. Its well-established global supply chain ensures cost stability and consistent quality.
Durability and Corrosion Resistance
Steel’s high resistance to wear, heat, and corrosion extends the lifespan of key automotive components. Stainless steel and galvanized steel further enhance protection against rust, reducing maintenance needs and improving vehicle longevity.
Recyclability and Sustainability
Steel, with a recycling rate of nearly 90%, supports eco-friendly vehicle production while reducing waste. Automakers rely on recycled steel to meet sustainability targets and lower their environmental footprint.
Better Steel for Stronger and Safer Cars
As automakers strive to build lighter, stronger, and more fuel-efficient vehicles, advancements in steel technology continue to shape the industry.
SteelPro Group provides high-quality automotive steel, including HX420LAD, HC500LA, DP600, and DP800. These steels improve vehicle strength, safety, and weight reduction, helping manufacturers build better, more efficient cars.