Contents
CPM 15V Tool Steel Powder Metal
- John
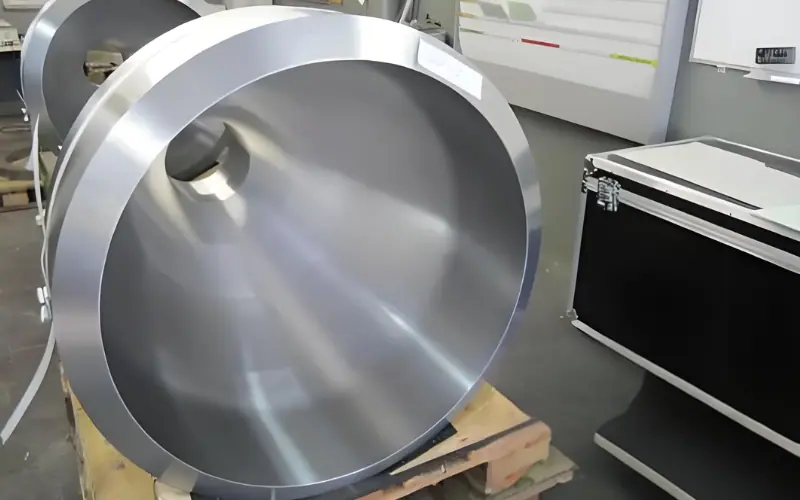
At SteelPro Group, we are proud to be a trusted supplier of high-performance CPM 15V tool steel. Focusing on excellence and dependability, we offer customized solutions designed to address your most challenging industrial requirements. Allow us to propel your projects ahead with accuracy.
What Is CPM 15V Steel?
CPM 15V steel is a high-performance powder metallurgy tool steel developed by Crucible. It contains 50% more vanadium carbide than CPM 10V, offering improved wear resistance and longer tool life. The steel’s uniform microstructure, achieved through the CPM process, ensures excellent dimensional stability, grindability, and toughness.
CPM 15V is ideal for replacing solid carbide in applications where carbide tools fail due to fracture or complex designs. It is primarily used in cold work tooling and other high-wear applications.
CPM 15V Steel Products Forms And Supply Range
Our CPM 15V tool steel meets industry-standard requirements, including those from ASTM, SAE, and JIS, ensuring reliable performance in high-wear applications. Below, we provide a range of product forms and sizes, with the flexibility to accommodate custom dimensions to meet specific project needs.
Bars and Rods:
- Diameter: 6 mm to 300 mm (0.24 inch to 11.81 inch)
- Length: 500 mm to 3,000 mm (19.69 inch to 118.11 inch)
Flat Stock:
- Thickness: 3 mm to 100 mm (0.12 inch to 3.94 inch)
- Width: 50 mm to 300 mm (1.97 inch to 11.81 inch)
- Length: 200 mm to 3,000 mm (7.87 inch to 118.11 inch)
Rounds:
- Diameter: 10 mm to 250 mm (0.39 inch to 9.84 inch)
- Length: 300 mm to 3,000 mm (11.81 inch to 118.11 inch)
CPM 15V Steel Chemical Composition
Element | Content (%) |
Carbon (C) | 3.4 |
Chromium (Cr) | 5.25 |
Iron (Fe) | 75.55, as balance |
Molybdenum (Mo) | 1.3 |
Vanadium (V) | 14.5 |
CPM 15V Steel Physical Properties
Property | Metric Value | Imperial Value |
Density | 7.25 g/cc | 0.262 lb/in³ |
Melting Point | 1,340°C | 2,443°F |
Thermal Conductivity | 25.3 W/m·K | 17.5 BTU·ft/hr·°F·ft² |
Specific Heat | 0.46 J/g·K | 0.11 BTU/lb·°F |
CPM 15V Steel Mechanical Properties
Property | Metric Value | Imperial Value |
Hardness (HB) | 255 – 277 | 255 – 277 |
Hardness (HRC) | 61 – 63 | 61 – 63 |
Modulus of Elasticity | 235 GPa | 34,100 ksi |
Charpy Impact (Austenitizing Temp – 1175°C) | 11.0 J | 8.11 ft-lb |
Charpy Impact (Austenitizing Temp – 1120°C) | 12.0 J | 8.85 ft-lb |
CPM 15V Steel Heat Treatment
Annealing
To reduce internal stresses and obtain a consistent microstructure, CPM 15V should undergo annealing at 1600°F (870°C) for 2 hours. Afterward, the steel should be slow-cooled at a maximum rate of 30°F (15°C) per hour down to 1000°F (540°C), followed by air or furnace cooling. This results in a hardness of BHN 255/277.
Stress Relieving
After machining, CPM 15V should undergo stress relieving to reduce residual stresses. This is achieved by heating the material to a temperature range of 1100-1300°F (595-740°C) and maintaining it for 2 hours, then allowing it to cool in air or a furnace.
Hardening
Preheating
Start by heating the steel to 1500-1550°F (816-845°C) and allowing it to stabilize. We recommend a second preheating stage at 1850-1900°F (1010-1040°C), especially for vacuum or atmospheric hardening, to ensure optimal results.
Austenitizing
Heat the steel rapidly from the preheat, typically by transferring it to a second furnace. The high heat austenitizing stage should be done in a furnace or salt bath at 1950-2150°F (1065-1175°C) for 10-30 minutes, ensuring the steel reaches the desired temperature and uniformity.
Quenching
After austenitizing, CPM 15V must be quenched to achieve maximum hardness. Depending on the section thickness:
For sections under 3 inches thick, natural cooling in air is adequate to achieve the highest hardness.
For thicker sections, quenching must be done using a faster method such as pressurized gas, warm oil, or salt to attain the desired hardness.
- To ensure proper hardness, pressurized gas requires a minimum quench pressure of 4 bars and a critical quench rate of below 1000°F (538°C).
- For oil quenching, cool until the steel turns black at about 900°F (482°C), then allow it to cool in still air to 150-125°F (66-51°C).
- Salt quenching should be performed in a bath maintained at 1000-1100°F (538-593°C).
Tempering
Finally, CPM 15V should undergo tempering to attain the desired balance of hardness and toughness. After hardening, temper the steel at a temperature between 400-1000°F (204-538°C), depending on the specific application requirements. The standard recommendation for achieving a hardness of 60-62 HRC is to temper at a higher range.
CPM 15V Steel Applications
Cold Work Tooling
- Punches and Dies: Used in stamping and punching operations where high wear resistance is required.
- Extrusion Dies: For forming materials under high pressure while maintaining tool integrity.
- Shear Blades: Used in shearing applications where durability is critical.
- Slitting Blades: For cutting or slitting metals and other materials in high-speed processes.
Cutting Tools
- Drills: Designed for boring through tough materials, such as stainless steel and high-strength metals.
- Reamers: For finishing holes with high precision and minimal wear.
- Taps: In threading operations for materials requiring high cutting-edge durability.
- End Mills: For machining a variety of materials with high wear resistance at the cutting edge.
Forming Tools
- Forging Dies: Used in hot or cold forging processes to shape metal parts.
- Stamping Dies: Stamping Molds: Used for high-volume manufacturing of metal components, especially in the automotive and aerospace sectors.
- Compression Molds: For shaping parts through compression in molding processes.
Wear Parts
- Rollers: Used in conveyor systems or other machinery where continuous movement of materials occurs.
- Liners: For machinery exposed to heavy wear, such as crushers and mills.
- Wear Plates: Installed equipment to resist abrasive wear during high-stress operations.
- Pins and Bushings: In mechanical systems that endure frequent wear and tear.
Sintering and High-Temperature Tooling
- Sintering Dies: Used in the powder metallurgy process to form components from metal powders.
- Hot Pressing Tools: For pressing materials at high temperatures during manufacturing.
- Die Inserts: In high-temperature forming processes where high wear resistance and thermal stability are required.
CPM 15V VS M390
CPM 15V excels in wear resistance, and M390 is better for resisting corrosion.
CPM 15V is a high wear-resistant tool steel, ideal for applications that require exceptional abrasion resistance, like cold work tools. M390, however, is a premium stainless steel known for excellent corrosion resistance and edge retention, making it more suitable for knives and tools exposed to moisture or corrosive environments.
CPM 15V VS S30V
CPM 15V shines in wear resistance, and S30V excels in overall toughness and corrosion resistance.
CPM 15V offers superior wear resistance due to its high vanadium content, making it great for tooling applications. S30V, however, is a high-performance stainless steel that balances wear resistance and corrosion resistance, making it ideal for knives and tools used in harsher, moisture-rich environments.
CPM 15V Tool Steel Solutions for Every Need
At SteelPro Group, we offer CPM 15V tool steel in various forms, including bars, rods, and flat stock, as well as hot work, cold work, and high-speed tool steels. We also provide surface treatments and grinding services to meet your specific requirements.
Whatever your project needs, we’re here to deliver the right steel with precision and reliability. Contact us today and let’s get started!