Contents
M1 High Speed Tool Steel: Properties, Process, Uses
- John
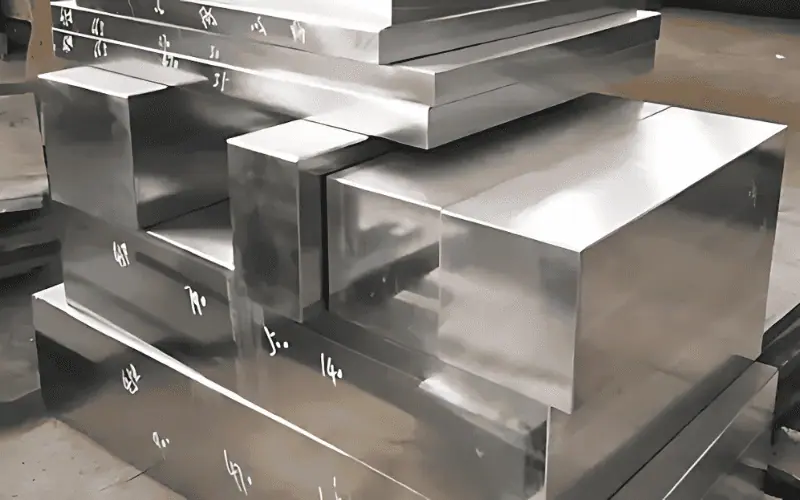
M1 is one of the most affordable high-speed steels. SteelPro Group offers M1 tool steel products that are both cost-effective and quality assured. Our materials meet international standards such as ASTM A600, FED QQ-T-590, SAE J437, and SAE J438, making them a trusted choice.
What Is M1 Tool Steel?
M1 tool steel is a molybdenum-based high-speed steel. It has good wear resistance, high hardness, and stability at high temperatures. M1 is commonly used for cutting tools, molds, and dies that need durability. M1 is made through electroslag remelting (ESR), which improves its purity and uniformity. However, M1 is susceptible to carbon loss during heat treatment unless it is hardened in a salt bath or a furnace with a controlled atmosphere.
What Is M1 Tool Steel Equivalent To?
M1 tool steel has several equivalents across different international standards. These include:
- AISI/SAE: M1
- UNS: T11301
- DIN (Germany): 1.3355
- BS (British Standard): BS 4659/105M
- JIS (Japan): SKH51
M1 Tool Steel Chemical Composition
M1 tool steel is a high-carbon, high-alloy material. The presence of chromium and molybdenum significantly improves its ability to withstand high-stress conditions, while tungsten and vanadium provide excellent strength retention at elevated temperatures. The following table outlines its chemical composition.
Element | Chemical (%) |
Iron (Fe) | 84.3, as balance |
Carbon (C) | ≤ 0.80 |
Chromium (Cr) | 3.75 |
Molybdenum (Mo) | 8.7 |
Tungsten (W) | 1.25 |
Vanadium (V) | 1.15 |
M1 Tool Steel Physical Properties
M1 tool steel is recognized for its high density, good heat resistance, and low expansion under temperature changes. It also offers strong stiffness and moderate ability to store heat. The table below summarizes the key physical properties of M1 tool steel.
Property | Metric | Imperial |
Density | 7.89 g/cc | 0.285 lb/in³ |
Melting Point | 1,400 – 1,500 °C | 2,552 – 2,732 °F |
Thermal Conductivity | 27 W/m·K | 18.7 BTU·in/hr·ft²·°F |
Specific Heat Capacity (at 25°C) | 460 J/kg·K | 0.110 BTU/lb·°F |
Coefficient of Thermal Expansion | 6.9 × 10⁻⁶ /°C | 3.83 × 10⁻⁶ /°F |
M1 Tool Steel Mechanical Properties
M1 tool steel is tough and durable, with high strength that makes it great for demanding tasks. It withstands abrasion and retains its form effectively, even when subjected to stress. The table below highlights the key mechanical properties of M1 tool steel.
Property | Metric | Imperial |
Tensile Strength | 1,350 MPa | 196,000 psi |
Yield Strength | 1,200 MPa | 174,000 psi |
Elongation at Break | 10% | 10% |
Hardness (Rockwell C) | 60 – 65 HRC | 60 – 65 HRC |
Impact Toughness (Charpy V-Notch) | 20 J | 14.8 ft-lb |
Fatigue Strength | 1,100 MPa | 160,000 psi |
Modulus of Elasticity | 210 GPa | 30.5 × 10⁶ psi |
Poisson’s Ratio | 0.27 – 0.30 | 0.27 – 0.30 |
M1 Tool Steel Heat Treatment
Through rigorous production management, we provide M1 steel in various conditions, including processed and hardened states, to meet the specific needs of our industrial clients.
Annealing
Heat M1 gradually to a temperature between 1500-1550°F. Once this temperature is reached, cool it slowly in the furnace at a rate of 30°F per hour until it reaches 1000°F, then increase the cooling rate.
To prevent excessive carburizing or decarburizing during the process, it’s essential to use protective atmospheres or coatings.
Stress Relieving
Heat the steel slowly to a temperature between 1150-1250°F and let it stabilize. After that, cool it in still air. This process helps to reduce internal stresses and improve the material’s overall stability.
Hardening
- Preheating
Start by evenly heating M1 tool steel to a temperature of 1350-1500°F. This helps to reduce thermal shock when austenitizing.
- Austenitizing
Heat the steel to 2100-2200°F to fully transform the steel into austenite.
- Quenching
Pressurized Air: Cool the steel in pressurized air at 1000-1100°F. This method is effective in maintaining dimensional accuracy and minimizing distortion.
Oil: For oil quenching, it is best to remove the steel from the oil bath around 1000°F to interrupt the quenching process. Let the steel cool in still air to complete the process. This is a common method for maintaining hardness while reducing the risk of cracking.
Salt Bath: In a salt bath, the steel should be placed in the molten salt until it reaches temperature equilibrium. Once this is achieved, remove the steel and cool it in air. The salt bath provides a uniform cooling rate, reducing thermal gradients and minimizing distortion.
Straightening: Any necessary straightening should be done during cooling between 850-450°F. Ensure the steel cools to about 150°F or to a temperature where it can be safely handled before proceeding to tempering.
Tempering
Tempering should be performed in the range of 1000-1100°F to relieve stresses induced by quenching. Double tempering is recommended for improved toughness and stability. After tempering, M1 tool steel can achieve a hardness of 60-62 HRC, depending on the specific conditions used.
M1 Tool Steel Product Forms
SteelPro Group offers M1 tool steel products in the following standard specifications. We also provide special dimensions beyond these standard ranges to meet specific customer requirements.
Product Form | Size Range (Metric) | Size Range (Imperial) |
Round Bars | Diameter: 10 mm to 300 mm | Diameter: 0.4 in to 12 in |
Square Bars | Side length: 10 mm to 250 mm | Side length: 0.4 in to 10 in |
Flat Bars | Thickness: 5 mm to 100 mm | Thickness: 0.2 in to 4 in |
Width: 20 mm to 300 mm | Width: 0.8 in to 12 in | |
Forged Blocks | Thickness: 50 mm to 500 mm | Thickness: 2 in to 20 in |
Width: 200 mm to 800 mm | Width: 8 in to 31 in | |
Length: 200 mm to 1200 mm | Length: 8 in to 47 in | |
Plates&Sheets | Thickness: 5 mm to 150 mm | Thickness: 0.2 in to 6 in |
Width: 100 mm to 2000 mm | Width: 6 in to 79 in | |
Length: 200 mm to 4000 mm | Length: 8 in to 157 in |
M1 Tool Steel Applications
The primary uses of M1 tool steel are as follows:
Cutting Tools
- Drill Bits: Used for precise drilling in metals and other hard materials.
- Saw Blades: Employed in cutting applications requiring high durability.
Molds and Dies
- Injection Molds: Used in the injection molding process for creating complex shapes.
- Stamping Dies: Essential for shaping and cutting metal sheets in production.
- Extrusion Dies: Utilized in the extrusion process to form materials into desired profiles.
Industrial Machinery Components
- Gear Blanks: Manufactured as precursors for gears in machinery.
- Knives and Blades: Employed in industrial cutting applications for their precision.
Precision Instruments
- Measuring Tools: Used in the fabrication of tools that require high accuracy.
- Template Tools: Essential for creating precise templates in manufacturing.
What Are The Differences Between M1 and M2 Tool Steel?
M1 tool steel has higher molybdenum and tungsten content, providing superior wear resistance and thermal stability, making it ideal for molds and die-casting tools. M2 tool steel, with more chromium and vanadium, offers better toughness and edge retention, making it suitable for high-speed cutting tools like drills and mills.
M1 Tool Steel Products and Processing Services
At SteelPro Group, we provide high-quality M1 tool steel products in a variety of forms, including round bars, square bars, forged blocks, and plates, all tailored to meet your specific needs. We also have other high speed tool steel like T1.
Beyond offering top-grade materials, we ensure precision with our processing services, including cutting, machining, heat treatment (annealing, hardening, tempering), and straightening. We understand the demands of your industry and are here to deliver the right solutions quickly and reliably, with no compromise on quality.