Contents
M7 High Speed Tool Steel: Properties, Process, Uses
- John
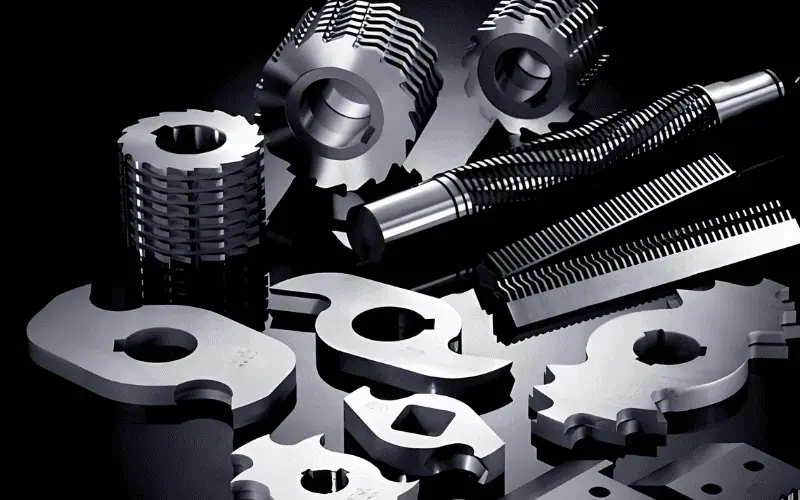
M7 tool steel is widely used in industries requiring durable and high-quality tools, especially for hard materials. This article explores the properties, applications, and heat treatment of M7 tool steel.
At SteelPro Group, we offer M7 tool steel in various forms, ensuring precision and customizable solutions to meet your specific industrial needs.
What Is M7 Tool Steel?
M7 is a high-speed tool steel with a tungsten-molybdenum base and cobalt enhancement, known for its exceptional wear resistance, red hardness, and toughness at high temperatures. It excels in cutting tools, especially for hard materials like stainless steel and high-carbon alloys.
Compared to M2, M7 offers superior heat resistance and cutting performance due to its higher cobalt content. Its deep hardening ability ensures longer tool life and reduced replacement frequency.
What Is M7 Tool Steel Equivalent To?
The common equivalents to M7 tool steel include:
- ISO 1.3343 (International)
- GB W18Cr4V (China)
- DIN 1.3343 (Germany)
- UNS T11307 (USA)
- BS HS6-5-2C (UK)
- JIS SKH2 (Japan)
SteelPro Group provides M7 tool steel products that comply with international standards such as ASTM A600 and FED QQ-T-590. We maintain strict tolerance requirements and ensure quality through rigorous testing and control processes.
M7 Tool Steel Chemical Composition
The high molybdenum, tungsten, and chromium content provides exceptional red hardness, wear resistance, and high-temperature performance. As a molybdenum-based tool steel, the Mo content enhances toughness but requires more precise control during hardening to avoid overheating.
The table below details the chemical composition of M7 tool steel.
Element | Chemical Composition |
Carbon (C) | 0.97 – 1.05 % |
Chromium (Cr) | 3.5 – 4.0 % |
Copper (Cu) | ≤ 0.25 % |
Iron (Fe) | 79.8 – 83.8 % |
Manganese (Mn) | 0.15 – 0.40 % |
Molybdenum (Mo) | 8.2 – 9.2 % |
Nickel (Ni) | ≤ 0.30 % |
Phosphorus (P) | ≤ 0.030 % |
Silicon (Si) | 0.20 – 0.55 % |
Sulfur (S) | ≤ 0.030 % |
Tungsten (W) | 1.4 – 2.1 % |
Vanadium (V) | 1.75 – 2.25 % |
M7 Tool Steel Physical Properties
M7 tool steel is known for its excellent thermal stability, high strength, and superior thermal conductivity. It has a comparatively low thermal expansion coefficient, which improves its performance when exposed to temperature changes. The table below summarizes the key physical properties of M7 tool steel.
Property | Metric | Imperial |
Density | 7.94 g/cm³ | 0.287 lb/in³ |
Melting Point | 2,800°C | 5,072°F |
Thermal Conductivity | 28 W/m·K | 19.4 BTU/h·ft·°F·in |
Coefficient of Thermal Expansion (20–100°C) | 11.0 µm/m·°C | 6.1 x 10⁻⁶ in/in·°F |
Specific Heat Capacity | 460 J/kg·K | 0.11 BTU/lb·°F |
M7 Tool Steel Mechanical Properties
The high molybdenum, tungsten, and chromium content provides M7 steel with exceptional red hardness, wear resistance, and high-temperature performance. As a molybdenum-based tool steel, the Mo content enhances toughness but requires more precise control during hardening to avoid overheating.
The table below presents the key mechanical properties of M42 tool steel.
Property | Metric | Imperial |
Hardness (HRC) | 42 – 66 | 42 – 66 |
Elastic modulus | 207 GPa | 30000 ksi |
Elongation | 8% | 8% |
Poisson’s Ratio | 0.29 | 0.29 |
Machinability | 45% – 50% | 45% – 50% |
M7 tool steel undergoes significant changes in hardness and toughness when subjected to different heat treatment conditions. As the hardening temperature increases, the hardness of the material also rises, peaking around 1,250°C (2,282°F). Additionally, tempering further enhances the toughness of M7 tool steel.
M7 Tool Steel Heat Treatment
At SteelPRO Group, we offer expert heat treatment services for M7 tool steel to enhance its performance across various applications. Whether you need M7 steel in an annealed, hardened, or tempered state, our advanced facilities ensure precise treatment, delivering products tailored to meet your operational needs.
Annealing
M7 tool steel should be annealed by heating it to a temperature between 843°C and 871°C (1550°F and 1600°F). Once at this temperature, hold the steel for at least one hour per 25.4mm (1 inch) thickness, ensuring that it is uniformly heated.
After soaking, the steel should be cooled slowly in the furnace at a rate of no more than 4°C (40°F) per hour until it reaches 538°C (1000°F), and then continue to cool at room temperature.
This process softens the steel and helps relieve internal stresses, preparing it for further machining or heat treatment.
Hardening
Hardening is a critical process for enhancing the strength and wear resistance of M7 tool steel. The steps involved include pre-heating, austenizing, and quenching.
- Preheating
A double pre-heating process is recommended to reduce the risk of distortion and minimize stresses in large or complex tools. The steel should first be heated to 593°C (1100°F) at a rate not exceeding 4°C (40°F) per hour, followed by a secondary heating to a temperature between 788°C and 843°C (1450°F and 1550°F). For smaller tools, only the second temperature range is necessary for pre-heating.
- Austenitizing
Once the steel has been pre-heated, it should be rapidly heated to the austenizing temperature range of 1191°C to 1216°C (2175°F to 2220°F) in a furnace.
For maximum toughness, use the lower end of the temperature range, while for maximum red hardness, use the higher end. The steel should be soaked at this temperature for 2 to 5 minutes to ensure uniformity.
- Quenching
M7 tool steel can be quenched using pressurized gas, oil, or salt. The quenching process involves the following specific temperatures for each medium:
- Pressurized Gas: Quenching is done below 538°C (1000°F) to achieve the required performance. The controlled cooling rate is essential to avoid distortion.
- Oil: After austenizing, quench the steel until it reaches around 482°C (900°F) and then cool it in still air until it reaches 66-51°C (150-125°F).
- Salt: For salt quenching, maintain the temperature between 538°C and 593°C (1000°F and 1100°F), balancing it before cooling the steel to 66-51°C (150-125°F) in still air.
These quenching methods ensure that the steel reaches the desired hardness while minimizing any risk of deformation or cracking.
Tempering
After quenching, tempering is crucial to adjust the hardness and relieve any residual stresses. M7 tool steel should be tempered immediately after quenching. The typical tempering temperature range is between 551°C and 565°C (1025°F and 1050°F), where the steel should be held for 2 hours before air cooling to room temperature.
Double tempering is required to ensure optimal mechanical properties and triple tempering is recommended for large cross-sectional parts or tools subjected to wire EDM (electrical discharge machining). Tempering increases the toughness of the steel while retaining its hardness, making it suitable for demanding applications.
M7 Tool Steel Product Forms
SteelPRO Group offers a variety of M7 tool steel products, including round bars, square bars, flat bars, forgings, and drill rods. In addition to the standard size ranges listed below, we also provide custom dimensions to meet specific customer requirements.
Product Form | Size Range (Metric) | Size Range (Imperial) |
Round Bars | Diameter: 5 mm to 300 mm | Diameter: 0.20 in to 11.81 in |
Square Bars | Side length: 5 mm to 200 mm | Side length: 0.20 in to 7.87 in |
Flat Bars | Thickness: 5 mm to 100 mm | Thickness: 0.20 in to 3.94 in |
Width: up to 500 mm | Width: up to 19.69 in | |
Forgings | Round: Diameter: 25 mm to 600 mm | Round: 0.98 in to 23.62 in |
Custom: up to 1,000 mm | Custom: up to 39.37 in | |
Sheet & Plate | Thickness: 2 mm to 100 mm | Thickness: 0.08 in to 3.94 in |
Width: up to 1,500 mm | Width: up to 59.06 in | |
Length: up to 3,000 mm | Length: up to 118.11 in | |
Drill Rods | Diameter: 3 mm to 50 mm | Diameter: 0.12 in to 1.97 in |
Length: up to 3,000 mm | Length: up to 118.11 in |
M7 Tool Steel Applications
SteelPRO Group provides M7 tool steel products suitable for various industrial uses. Known for its strength and wear resistance, M7 is commonly used in cutting tools, forming tools, and molds. Below, we outline its most common applications.
Category | Common Uses |
Cutting Tools | Drills, milling cutters, reamers, taps, and other cutting tools used for material cutting. |
Forming Tools | Punches, extrusion dies, bending dies for metal forming and plastic deformation. |
Molds and Dies | Injection molds, compression molds, blow molds for plastic and rubber molding. |
Wear Parts | Shear blades, abrasion-resistant plates for high-wear environments in metal processing. |
Cold Work Tooling | Cold forging dies, cold punching dies for precision tools in cold processing. |
Precision M7 Tool Steel Solutions and Expert Services
At SteelPRO Group, we specialize in high-quality M7 tool steel, offering products like round bars, square bars, and custom forgings. Our materials are perfect for cutting tools, molds, and cold work tooling, known for their durability and high-temperature resistance. Our products also include D2, T1, and H13 tool steel.
We also provide precision machining and heat treatment services, including annealing, hardening, and tempering. Let us be your partner in achieving excellence.