Contents
Galvanized vs. Non-Galvanized Steel
- John
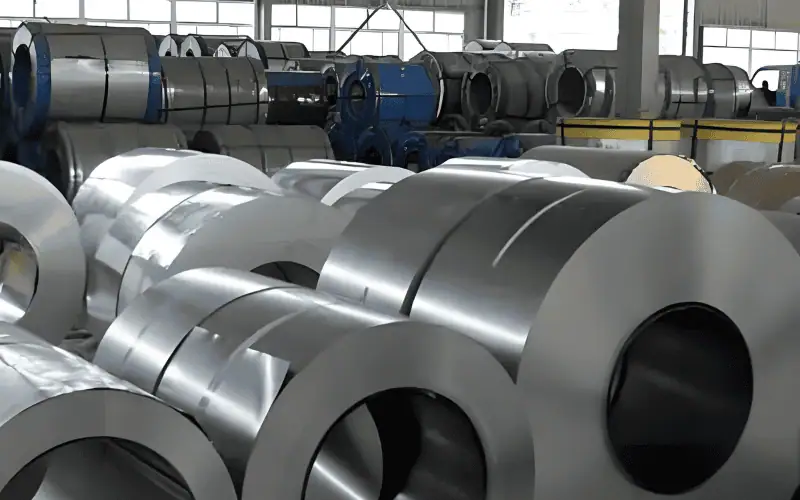
Galvanized steel is coated with a layer of zinc to resist corrosion, while non-galvanized steel lacks this protective coating and is more prone to corrosion.
If you would like to learn more about the detailed differences between galvanized and non-galvanized steel, please continue reading the rest of this article for a deeper understanding.
Different Characteristics of Galvanized and Non-Galvanized Steel
Corrosion Resistance
- Galvanized Steel: Zinc coating provides superior corrosion resistance. It acts as a moisture barrier and sacrificial anode, extending its lifespan.
- Non-Galvanized Steel: No protective coating. Susceptible to rust, especially in humid, salty, or chemically aggressive environments. It needs additional protective treatments.
Galvanized steel generally offers superior corrosion resistance. Its zinc coating helps extend the steel’s lifespan, especially in environments prone to dampness or mild chemical exposure.
Non-galvanized steel lacks any protective coating, making it much more susceptible to corrosion under various conditions. To ensure its durability, non-galvanized steel requires additional protective treatments, such as rust-resistant paint or primer.
However, the zinc layer has its limitations. Overextended exposure to saltwater, strong acids, or abrasive conditions, the protective zinc layer can degrade or wear down. Once this layer is compromised, the underlying steel becomes exposed to direct corrosion.
Heat Resistance
- Galvanized Steel: Zinc coating degrades at temperatures above 200°C, making it unsuitable for high-heat applications like cookware.
- Non-Galvanized Steel: Can withstand higher temperatures and is suitable for heat-sensitive uses.
Galvanized steel is unsuitable for environments like ovens, heat exchangers, or other machinery where temperatures exceed 200°C.
The heat resistance of non-galvanized steel varies depending on the specific steel grade. For instance, carbon steel and stainless steel grades can withstand higher temperatures without compromising their structural integrity.
Appearance
- Galvanized Steel: Surface varies depending on the process. Hot-dip galvanized steel has a spangled finish; electro-galvanized steel is smooth.
- Non-Galvanized Steel: Offers a wider variety of finishes, from silver-gray to matte or shiny, depending on the processing.
Non-galvanized steel offers a wider variety of appearances based on its type and processing. For instance, untreated steel generally has a silver-gray or dark-gray color. Hot-rolled steel has a rougher, matte surface. Cold-rolled steel boasts a smooth and shiny surface.
These various finishes give non-galvanized steel a more flexible range of appearances, making it suitable for applications requiring different visual and texture options
Weight
- Galvanized Steel: Slightly heavier due to the zinc coating.
- Non-Galvanized Steel: Lighter, with a weight depending more on the steel’s thickness and type.
Different Processing of Galvanized and Non-Galvanized Steel
Formability
- Galvanized Steel: More prone to coating damage during shaping. Best to bend before galvanizing.
- Non-Galvanized Steel: More flexible and adaptable during processing, as it has no coating to damage.
Welding
- Galvanized Steel: More challenging due to toxic fumes from the zinc coating. Requires removal of the coating before welding.
- Non-Galvanized Steel: Easier to weld, with fewer precautions needed.
Before welding galvanized steel, it is advisable to remove the zinc coating from the areas that will be welded. This can be done through grinding or using chemical solutions to improve weld integrity. Additionally, proper ventilation is also essential when welding galvanized materials.
Because of these complexities, galvanized steel parts are often connected using methods such as mechanical fasteners or bolting. In contrast, welding non-galvanized steel is simpler, as it only requires addressing the specific welding needs of the different steel grades.
Other Differences Between Galvanized and Non-Galvanized
Applications
Galvanized steel is ideal for outdoor applications due to its excellent corrosion resistance, making it suitable for structures exposed to moisture and weather.
- Construction and Infrastructure: Used in structural beams, roofing materials, and support frames due to its corrosion resistance.
- Automotive Industry: Commonly applied in car bodies and parts to prevent rust from road salt and moisture exposure.
- Outdoor Furniture and Fixtures: Ideal for park benches, fencing, and playground equipment, where exposure to weather elements is frequent.
- Electrical Equipment: Used in cable trays, wiring conduits, and electrical poles to protect against corrosion and weather damage.
- Agricultural Equipment: Utilized for fencing, animal enclosures, and irrigation systems due to its durability in outdoor, humid environments.
- HVAC Systems: Found in ductwork and ventilation systems to resist moisture-related corrosion.
In contrast, non-galvanized steel is best suited for indoor use or environments where exposure to corrosive elements is limited.
- Indoor Structural Applications: Used in beams, columns, and internal framing in buildings where corrosion is less of a concern.
- Machinery and Industrial Parts: Employed in gears, engines, and machine components where strength and machinability are prioritized.
- Tools and Hardware: Common in tool manufacturing, such as wrenches, hammers, and fasteners that are kept indoors or in tool storage.
- Decorative Metalwork: Used in furniture frames, interior décor, and other design elements where the metal can be painted or treated.
Maintenance and Cost
- Galvanized Steel: Low maintenance due to the durable zinc coating. Higher upfront cost, but long-term savings.
- Non-Galvanized Steel: Requires regular rust prevention measures, such as painting. Lower initial cost but higher long-term maintenance.
Galvanized steel has a higher initial cost due to the galvanizing process. However, it requires less maintenance over time. If the protective coating is scratched or damaged, simply applying a zinc-rich paint or touch-up compound can restore its protective properties.
In contrast, non-galvanized steel requires regular maintenance to prevent rust, especially in outdoor or humid environments. It demands more frequent inspections and protective treatments to maintain its durability.
How To Choose Between Galvanized and Non-Galvanized Steel?
- Galvanized Steel: For projects requiring long-term durability and minimal upkeep.
- Non-Galvanized Steel: For budget-conscious applications in less demanding environments.
Galvanized steel is ideal for outdoor exposure, coastal areas, and humid environments where prolonged moisture contact is common. However, galvanized steel is less suitable for high-temperature applications or environments with extreme abrasion, as the zinc layer can degrade under such conditions.
Non-galvanized steel is best suited for indoor applications or controlled environments where corrosion risk is minimal.
High-quality Steel Solutions
Steel Pro Group offers a wide range of hot-dip galvanized steel products, including sheets, coils, pipes, and mesh. Whether for construction, infrastructure, or agriculture, our steel ensures durability and corrosion resistance, minimizing maintenance and maximizing performance. Please browse here to find galvanized steel products tailored to your specifications.