Contents
Galvanized Steel Grades and Grades Chart
- John
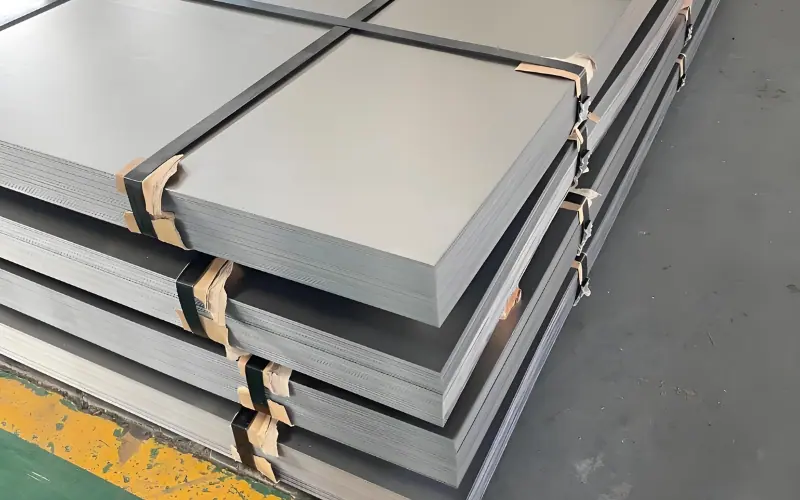
Galvanized steel grades come in many types, we know choosing the right grade can be tricky. That’s why we’ve organized this guide by coating process—like hot-dip and electro-galvanized—so you can easily match grades to your needs. Our chart breaks down key properties, helping you quickly find the best option for your application.
Type of Galvanized Steel Grades
Galvanized steel grades are classified by coating process, strength, and application. he main types include hot-dip galvanized (HDG), electro-galvanized (EG), galvannealed (GA), and zinc-aluminum-magnesium (ZAM) coated steel. Grades also differ in yield strength, tensile strength, and coating thickness (e.g., G30, G90, G235).
Keep reading as we break down each type, helping you find the best grade for your specific needs in construction, automotive, and appliance applications.
1. Hot-Dip Galvanized Steel (HDG) Grades
DX Series Grades
DX-Series grades are classified based on the EN 10346 standard and are widely used in cold-forming applications. The naming follows this structure:
- D: Indicates that the steel is flat steel for cold forming.
- X, C, or D: “X” = Unspecified substrate rolling state. “C” = Specifies a cold-rolled substrate. “D” = Specifies a hot-rolled substrate.
- 51-57: The two-digit number represents the steel grade serial number (higher numbers indicate better formability).
- D: Indicates that the material is hot-dip galvanized.
DX51D+Z
DX51D+Z is a cost-effective, reliable choice for general-use galvanized steel, offering even coating and good corrosion resistance. Ideal for roofing, insulation panels, and appliance casings, it balances performance and budget, making it a better low-strength option than G90. The JIS equivalent SGCC is similarly popular.
DX52D+Z
With superior ductility, DX52D+Z is crafted for processes like bending and stamping, fitting well in automotive bodywork and light machinery. Its formability surpasses S250GD+Z, making it ideal for more intricate shaping.
DX53D+Z
With enhanced ductility, DX53D+Z is suited for deep drawing applications in automotive body parts, appliances, and complex profiles. Its ductility outperforms DX51D+Z, while DX54D+Z can be used for even more demanding applications.
DC01
Known for its excellent formability and surface quality, DC01 is commonly used in applications requiring precision shaping, such as automotive panels, household appliances, and other components. For greater strength, DX51D+Z is a comparable alternative.
S Series Grades
S-Series grades are classified based on minimum yield strength and are commonly used for structural applications. The naming follows this structure:
- S: Indicates structural steel.
- 250, 350, 550: Represents the minimum yield strength in MPa.
- GD: Galvanized steel.
S350GD+Z
S350GD+Z is tailored for structural integrity in heavy-duty projects, such as steel frames and bridge components. It features high yield strength for demanding applications. For greater strength, consider S450GD+Z, which provides better load-bearing capabilities and greater resilience under stress.
S250GD+Z
Balancing strength and corrosion resistance, S250GD+Z is a go-to for construction frameworks and roofing systems. This grade is particularly suitable for buildings and infrastructure that need a combination of moderate strength and weather resistance. If higher load-bearing is needed, S350GD+Z offers more strength without compromising corrosion resistance.
S550GD+Z
S550GD+Z excels in high-stress, heavy-duty environments like construction frameworks and container structures. For even tougher applications, S600GD+Z can handle greater loads.
ASTM A653 Grades
The ASTM A653 standard classifies hot-dip galvanized steel based on coating thickness and strength levels. The key parameters include:
- G30, G60, G90, G235 – Represent the coating weight in oz/ft².
- CS, FS, DDS – Indicate the steel’s formability.
- SS Grades – Structural steel grades with yield strength in ksi.
G90
G90’s thicker coating provides robust, long-term protection in outdoor and harsh settings. It excels in structural applications like billboards and agricultural facilities. In more aggressive environments, G115 can offer added protection.
G235
G235’s thick coating makes it ideal for long-term exposure in demanding conditions, such as coastal facilities and outdoor furniture. It provides a significant upgrade over G90 in terms of corrosion resistance.
HX-Series Grades (High-Strength Cold-Forming)
The HX-Series includes high-strength low-alloy steels, optimized for automotive and industrial applications. The naming convention follows:
- H: High-strength cold-forming steel.
- X340, X420, X500, etc.: Indicates minimum yield strength in MPa.
- LAD: Low-alloy steel with improved ductility.
HX340LAD
Known for combining strength with formability, HX340LAD is a staple in automotive chassis and industrial equipment. It offers better workability than HX420LAD, making it perfect for complex shapes.
HX500LAD
HX500LAD strikes a balance between ultra-high strength and formability, widely used in automotive structural components. For cost-effective solutions without compromising on strength, it’s a solid choice compared to HX550LAD.
2. Electro-Galvanized Steel (EG) Grades
SE Series Grades
SE-series grades follows the JIS (Japanese Industrial Standard) classification.
- “C” = Commercial Quality.
- “D” = Drawing Quality.
- “E” = Extra Deep Drawing Quality.
SECC
SECC is prized for its smooth, paint-friendly surface, making it perfect for high-visibility products like electronics and appliances. It offers superior finish quality over SECD, ideal for standard coating applications.
SECD
SECD stands out for its formability, perfect for complex shaping in appliances and industrial casings. For even finer detailing, consider SECE.
SECE
Grades SECE excels in ductility and finish, ideal for deep-drawn parts like automotive components and electronic casings. It outperforms SECC and SECD when precise, intricate shaping is required.
3. Galvannealed Steel (GA) Grades
The naming system for GA grades follows a strength-based classification. The number represents the minimum yield strength in MPa.
GA340
GA340 offers top-notch weldability and paintability, widely used for automotive panels and home appliances. For projects requiring more strength, GA420 is a robust alternative.
GA420
GA420 provides enhanced strength while maintaining good formability, ideal for heavier automotive parts and structural components. It bridges the gap between standard grades and high-strength needs, making it a versatile choice for demanding applications.
GA590
GA590 combines higher strength with reliable formability, suitable for precision-engineered automotive parts. If strength requirements are lower, GA340 remains an excellent option.
GA780
GA780 delivers ultra-high strength, tailored for critical automotive components that demand both strength and precision, such as impact beams and safety structures. For less demanding parts, GA590 offers a balanced alternative.
4. Zinc-Aluminum-Magnesium Coated Steel (ZAM) Grades
ZM310
ZM310 is engineered for unmatched corrosion resistance, thriving in harsh, long-term conditions. Ideal for coastal infrastructure and industrial machinery, ZM430 can offer further enhanced protection if needed.
ZM430
ZM430 builds on the benefits of ZM310 with a thicker coating, providing superior defense against extreme corrosion, especially in marine and industrial settings. It’s a top choice for projects requiring maximum longevity, such as solar panel mounts and offshore structures.
5. Aluminum-Zinc Coated Steel (Aluzinc/GL) Grades
The coating composition typically consists of 55% aluminum, 43.4% zinc, and 1.6% silicon, offering superior reflectivity, durability, and formability.
AZ150
AZ150 excels in high-temperature and harsh environments, making it a go-to for roofing, insulation panels, and industrial equipment. For tougher settings, it outperforms G90.
AZ200
With an even thicker coating, AZ200 ensures superior durability in extreme conditions, ideal for solar reflectors and cladding. For highly corrosive or hot environments, AZ200 remains superior to G115.
Procurement Recommendations
To help you make the best choice for your needs, we’ve put together a selection guide for galvanized steel based on different environments and applications.
Hot-Dip Galvanized Steel: Versatile across applications, from low to ultra-high strength. Choose the right coating (e.g., G90, G235) and strength level (e.g., DX51D, S550GD) based on your environment. G235 is ideal for coastal and industrial areas.
Electro-Galvanized Steel: Best for aesthetic-focused products. SECC works well for home appliances, while SECD handles more complex shaping.
Galvannealed Steel: Ideal for welding and coating, especially in automotive and appliance sectors. GA340 or GA590 can be chosen depending on strength needs.
Zinc-Aluminum-Magnesium Coated Steel: Designed for harsh environments, ZM310 suits industrial and marine setups, with ZM430 available for extreme conditions.
Aluminum-Zinc Coated Steel: Superior corrosion and heat resistance, with AZ150 and AZ200 perfect for construction and industrial gear. These are the preferred choice when durability is critical.
What Are the Different Types of Galvanized Steel?
The main types are hot-dip galvanized (HDG), electro-galvanized (EG), galvannealed (GA), and zinc-aluminum-magnesium (ZAM).
Common Galvanized Steel Grades Chart
This chart highlights key grades, properties, and uses, guiding optimal steel selection.
Standard | Grades | Material Number | Chemical Composition (Typical, %) | Chemical Treatment | Surface Finish (Possible) | Yield Strength (MPa) | Tensile Strength (MPa) | Elongation (%) |
EN | DX51D+Z | 1.0226 | C≤0.12, Mn≤0.6, P≤0.1, S≤0.045 | Non-passivated | Z, ZF, ZA, ZM | ≥140 | ≥270 | ≥22 |
JIS | SGCC | SGCC-01 | C≤0.15, Mn≤0.6, P≤0.05, S≤0.05 | Non-passivated | Z, ZF, ZA | ≥205 | ≥270 | ≥20 |
ASTM | G65 | A653-G65 | C≤0.2, Mn≤0.6, P≤0.04, S≤0.04 | Non-passivated | Z, ZF, ZA, AS | ≥200 | ≥280 | ≥18 |
EN | DX52D+Z | 1.035 | C≤0.1, Mn≤0.5, P≤0.1, S≤0.045 | Non-passivated | Z, ZF, ZA | ≥180 | ≥340 | ≥26 |
EN | S250GD+Z | 1.0242 | C≤0.2, Mn≤1.4, P≤0.1, S≤0.045 | Passivated | Z, ZF, ZA, AS | ≥250 | ≥330 | ≥19 |
ASTM | G90 | A653-G90 | C≤0.2, Mn≤0.6, P≤0.04, S≤0.04 | Passivated | Z, ZF, ZA, AS | ≥230 | ≥300 | ≥18 |
EN | S350GD+Z | 1.0547 | C≤0.2, Mn≤1.5, P≤0.1, S≤0.045 | Passivated | Z, ZF, ZA, ZM | ≥350 | ≥420 | ≥18 |
EN | HX340LAD | 1.097 | C≤0.12, Mn≤1.5, Si≤0.5, Al≤0.05 | Non-passivated | Z, ZF, ZM | ≥340 | ≥440 | ≥20 |
ASTM | G235 | A653-G235 | C≤0.25, Mn≤0.7, P≤0.04, S≤0.04 | Passivated | Z, ZF, ZA, ZM | ≥275 | ≥350 | ≥18 |
EN | S550GD+Z | 1.0947 | C≤0.2, Mn≤1.6, P≤0.1, S≤0.045 | Passivated | Z, ZF, ZA | ≥550 | ≥600 | ≥15 |
EN | HX500LAD | 1.0948 | C≤0.15, Mn≤1.7, Si≤0.5, Nb/V/Ti traces | Non-passivated | Z, ZF, ZM | ≥500 | ≥650 | ≥12 |
JIS | SECC | SECC-01 | C≤0.12, Mn≤0.6, P≤0.05, S≤0.05 | Non-passivated | Z, ZF | ≥140 | ≥270 | ≥28 |
JIS | SECD | SECD-01 | C≤0.1, Mn≤0.5, P≤0.04, S≤0.04 | Non-passivated | Z, ZF | ≥180 | ≥330 | ≥26 |
JIS | SECE | SECE-01 | C≤0.08, Mn≤0.4, P≤0.03, S≤0.03 | Non-passivated | Z, ZF | ≥190 | ≥350 | ≥30 |
EN | GA340 | 1.0338 | C≤0.2, Mn≤1.4, Al-Si alloy coating | Passivated | Z, ZA, AS | ≥340 | ≥420 | ≥20 |
EN | GA420 | 1.0374 | C≤0.22, Mn≤1.5, Al-Si alloy coating | Passivated | Z, ZA, AS | ≥420 | ≥490 | ≥15 |
EN | GA590 | 1.0379 | C≤0.15, Mn≤1.8, Si≤0.5, Al-Si coating | Passivated | Z, ZA, AS | ≥590 | ≥650 | ≥12 |
EN | GA780 | 1.0981 | C≤0.12, Mn≤2.0, Al≤0.05, Si≤0.6 | Passivated | Z, ZA, AS | ≥780 | ≥850 | ≥10 |
JIS | JSC270C | JSC270C-01 | C≤0.15, Mn≤0.5, P≤0.04, S≤0.04 | Non-passivated | Z, ZF, ZM | ≥200 | ≥270 | ≥30 |
JIS | JSC270D | JSC270D-01 | C≤0.12, Mn≤0.4, P≤0.03, S≤0.03 | Non-passivated | Z, ZF, ZM | ≥210 | ≥310 | ≥28 |
JIS | SECE-P | SECE-P01 | C≤0.1, Mn≤0.5, P≤0.04, S≤0.03 | Passivated | Z, ZF, AS | ≥210 | ≥340 | ≥32 |
JIS | SECD-P | SECD-P01 | C≤0.12, Mn≤0.5, P≤0.04, S≤0.03 | Passivated | Z, ZF, AS | ≥180 | ≥330 | ≥26 |
JIS | SECE-M | SECE-M01 | C≤0.08, Mn≤0.4, P≤0.03, S≤0.02 | Non-passivated | Z, ZF, ZM | ≥190 | ≥350 | ≥30 |
EN | ZM310 | 1.0298 | C≤0.2, Mn≤1.2, Al≤1.0, Mg≤2.5 | Passivated | ZM, ZF | ≥310 | ≥410 | ≥25 |
EN | ZM430 | 1.0302 | C≤0.2, Mn≤1.5, Al≤1.0, Mg≤3.0 | Passivated | ZM, ZF | ≥310 | ≥420 | ≥18 |
What is grade 2 galvanized?
Grade 2 galvanized steel refers to a coating thickness standard, offering moderate corrosion resistance, typically used for general indoor applications.
What is special about galvanized steel?
It has a zinc coating that protects the steel from rust, extending its lifespan and making it ideal for harsh environments.
Applications of Galvanized Steel Grades
We understand that different sectors have unique needs for galvanized steel. That’s why we not only highlight key applications but also compare grades, guiding you to the best choice for each specific use.
1. Construction
Galvanized steel is essential for building frames, roofing, and structural parts.
SGCC Grade vs. DX51D+Z Grade
SGCC offers superior corrosion protection, making it ideal for external structures. DX51D+Z, being cost-effective, is best for internal framework. SteelPRO Group recommends SGCC for harsh environments due to its thicker coating.
2. Automotive
Used in chassis, car body panels, and undercarriage parts, ensuring durability.
HX340LAD vs. GA590
HX340LAD excels in formability, suitable for detailed parts. GA590 is stronger, ideal for structural components. Choose HX340LAD for flexibility; GA590 for robustness.
3. Home Appliances
Common in washing machines, refrigerators, and ovens, providing long-term use.
SECC vs. SECD
SECC offers a smoother finish, ideal for visible appliance parts. SECD is more flexible for complex designs. We suggest SECC for aesthetics, and SECD when shaping is key.
4. Agricultural Equipment
Essential in greenhouses, storage silos, and irrigation systems.
G235 vs. ZM310
G235 has high resistance, perfect for silos and barns. ZM310 offers enhanced anti-corrosion properties, better for coastal or high-moisture environments.
5. Infrastructure
Used in bridges, guardrails, and street lighting poles for durability and safety.
G90 vs. S350GD+Z
G90 is excellent for corrosion protection in standard conditions, making it suitable for street poles. S350GD+Z, with higher strength, is better for load-bearing structures like bridges. Choose G90 for typical exposure, and S350GD+Z for heavy-duty requirements.
6. Electronics
Found in cases, battery covers, and other components requiring precise shaping.
SECC vs. SECE
SECC provides a smoother surface, ideal for electronics casings. SECE offers more ductility, perfect for detailed, intricate parts. SteelPRO Group suggests SECC when surface quality matters, and SECE for complex designs.
7. Renewable Energy
Applied in solar panel frames, wind turbine parts, and support structures.
DX52D+Z vs. ZM430
DX52D+Z offers good flexibility, making it ideal for versatile applications. ZM430 has superior anti-corrosion traits, perfect for outdoor, long-term use. For coastal or offshore projects, ZM430 is the recommended choice.
SteelPRO Group—Reliable Galvanized Steel Manufacturer
Our guide has highlighted the versatility and key applications of various galvanized steel grades, helping you make informed choices.
At SteelPRO Group, we offer a wide range of popular grades like DX51D+Z, SGCC, G90, and ZM310, tailored to meet different industry needs. Our products are available in multiple shapes, including galvanized sheets, galvanized coils, and custom profiles, and we provide additional processing services like cutting, bending, and coating to match your specifications.
Let us help you streamline your projects, take advantage of our expert support in selecting the ideal galvanized steel grade!