Contents
Maraging 250 Alloy Steel AMS 6512 | UNS K92890
- John
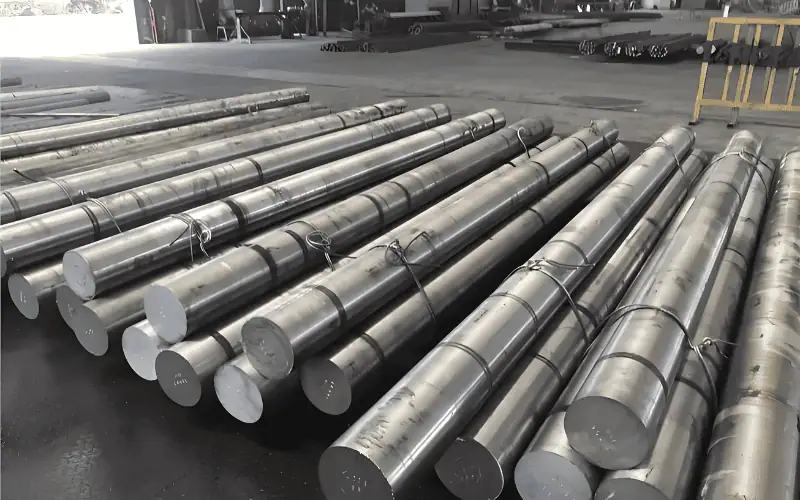
Looking for a steel that combines extreme strength with precision?
Maraging 250 Alloy Steel offers unmatched durability for aerospace and industrial applications. At SteelPro Group, we are your trusted source for premium maraging steel solutions.
In this guide, we’ll cover its composition, heat treatment benefits, machining tips, and real-world applications—helping you optimize performance and reliability.
What Is Maraging 250 Steel?
Maraging 250 Steel is an 18% nickel, cobalt-strengthened alloy known for its exceptional strength-to-weight ratio and toughness. Its carbon-free composition, processed with VIM + VAR methods, ensures low impurities. Unlike Maraging 300, Maraging 250 focuses on fracture toughness rather than peak strength, making it ideal for dynamic loads. It is also enhanced with titanium, molybdenum, and aluminum to improve precipitation hardening. It is highly effective in jet engine components, precision tooling, and military systems that demand fatigue resistance.
SteelPro Group maraging 250 Steel is delivered in a soft, machinable annealed state (RC 30-35). It reaches high strength (up to 1800 MPa) with a simple aging process at 900°F, offering a balance of ductility and crack resistance.
Maraging 250 Alloy Steel Advantages
Inherent Material Superiority
- Ultra-High Strength: Delivers exceptional yield and tensile strength while remaining lightweight, surpassing conventional steels.
- Thermal Stability: Low thermal expansion minimizes distortion, making it ideal for precision tooling and aerospace components.
- Corrosion & Wear Resistance: Outperforms standard tool steels, resisting pitting and degradation in harsh environments.
Fabrication Flexibility
- Machining Ease: The soft annealed state (RC 30-35) allows for complex shaping without needing intermediate annealing.
- Crack-Resistant Forming: Supports cold, warm, and hot forming with minimal risk of micro-cracking.
- Seamless Welding & Finishing: Requires no pre/post-heat treatment and can achieve a mirror-like polish for molds or optical components.
Long-Term Performance Edge
- Fatigue & Impact Resilience: Withstands cyclic stresses, ideal for aerospace actuators and high-load tooling.
- Lifecycle Adaptability: Can be easily re-aged or repaired to restore properties, lowering lifecycle costs.
- Environmental Versatility: Performs well in extreme conditions, from marine atmospheres to high-temperature die casting.
Maraging 250 Steel Chemical Composition
Element | Content |
Aluminum (Al) | 0.10 % |
Boron (B) | 0.0030 % |
Carbon (C) | ≤ 0.030 % |
Cobalt (Co) | 7.5 % |
Iron (Fe) | 68 % |
Manganese (Mn) | ≤ 0.10 % |
Molybdenum (Mo) | 4.8 % |
Nickel (Ni) | 18.5 % |
Phosphorus (P) | ≤ 0.010 % |
Silicon (Si) | ≤ 0.10 % |
Sulfur (S) | ≤ 0.010 % |
Titanium (Ti) | 0.40 % |
Zirconium (Zr) | 0.010 % |
Maraging 250 Steel Mechanical Properties
Property | Metric Units | Imperial Units |
Tensile Strength | 965 MPa | 140,000 psi |
Yield Strength | 655 MPa | 95,000 psi |
Elastic Modulus | 190 GPa | 27.6 × 10⁶ psi |
Poisson’s Ratio | 0.3 | 0.3 |
Elongation at Break | 0.17 | 0.17 |
Hardness (Annealed) | 30 HRC | 30 HRC |
Hardness (Aged) | 48-52 HRC | 48-52 HRC |
Maraging 250 Steel Physical Properties
Property | Metric Units | Imperial Units |
Density | 8.00 g/cm³ | 0.289 lb/in³ |
Thermal Conductivity | 25.3 W/m·K | 176 BTU·in/(hr·ft²·°F) |
Coefficient of Thermal Expansion | 11.2 × 10⁻⁶/°C | 6.2 × 10⁻⁶/°F |
Maraging 250 Steel Bars | Plate | Sheet Dimensions
We stock and customize Maraging 250 (AMS 6512) in versatile forms to meet your project’s exact needs—from standard inventory sizes to tailor-made dimensions. All materials comply with global certifications for guaranteed performance.
Product Form | Metric Dimensions | Imperial Dimensions |
Round Bars | Diameter: 5–300 mm | Diameter: 0.2–12 in |
Flat Bars | Thickness: 10–150 mm | Thickness: 0.4–6 in |
Width: 50–600 mm | Width: 2–24 in | |
Plates | Thickness: 6–150 mm | Thickness: 0.25–6 in |
Length/Width: Up to 4 m | Length/Width: Up to 13 ft | |
Sheets | Thickness: 0.5–6 mm | Thickness: 0.02–0.25 in |
Length/Width: Up to 3 m | Length/Width: Up to 10 ft |
Maraging 250 Steel Applications
Aerospace & Defense:
- Jet engine shafts, landing gear components, and rocket motor casings.
- Satellite structural frames requiring lightweight durability in extreme thermal cycles.
Precision Tooling:
- Die-casting molds and injection molding tools resistant to thermal fatigue.
- High-polish stamping dies for automotive or consumer electronics production.
Military & Marine Systems:
- Submarine hull fittings and torpedo tubes demanding corrosion resistance.
- Armor plating and ordnance components needing impact toughness.
Nuclear & Energy:
- Reactor core components and fuel rod cladding with radiation stability.
- Turbine blades and compressor parts for high-stress power generation.
Medical & Optics:
- Surgical instrument hinges and robotic arms requiring fatigue resistance.
- Precision optical mounts with low thermal expansion for laser systems.
Maraging 250 Steel Manufacturing & Processing
1. Melting & Casting
The alloy begins with a double vacuum melting process (VIM + VAR). Vacuum induction melting (VIM) precisely controls the 18% nickel and 7.5% cobalt composition, while vacuum arc remelting (VAR) eliminates impurities like oxygen and sulfur. Ultra-low carbon content (≤0.03%) prevents grain boundary brittleness, ensuring weldability and toughness.
2. Heat Treatment
Annealing
- Supplied in a soft, machinable annealed state (RC 30-35).
- Process: 1500–1525°F (815–830°C) for 1 hour per inch of thickness.
Aging Hardening
- Standard Aging: 900–925°F (482–496°C) for 6 hours, achieving HRC 48-52.
- Tooling-Specific Aging: 980–1000°F (527–538°C) enhances thermal fatigue resistance for die-casting molds.
3. Forming & Shaping
Maraging 250’s crack-resistant structure allows cold, warm, or hot forming without intermediate annealing. Precision rolling produces sheets/plates with tolerances as tight as ±0.05 mm, ideal for aerospace frames and high-stress tooling blanks.
4. Machining Techniques
Turning & Milling
- Annealed State: Carbide tools at 80–475 ft/min cutting speeds (tool-dependent).
- Coolants: Soluble oil (1:20) or highly chlorinated oils to avoid work hardening.
Drilling & Tapping
- High-speed steel drills at 0.005 in/rev feed with sulfurized oils.
- Threads: 75% engagement to minimize stress concentration.
5. Welding & Surface Finishing
TIG/MIG welding with nickel-based fillers requires no preheating. Post-weld aging restores properties seamlessly. Mirror polishing achieves Ra 0.1μm finishes for optical molds, while electroless nickel coatings enhance corrosion resistance in marine environments.
6. Lifecycle Optimization
Worn components are re-annealed, re-machined, and re-aged to restore >90% strength—a cost-effective alternative to traditional steel replacement.
Unlock Maraging 250 Steel Full Potential
At SteelPro Group, we don’t just supply materials—we deliver solutions engineered for success. Whether you’re prototyping a next-gen aerospace component or optimizing high-volume tooling, our expertise ensures your Maraging 250 (AMS 6512) performs flawlessly from design to delivery.
We offer:
- Precision Machining: Pre-drilled, threaded, or contoured parts to reduce your lead time.
- Certified Traceability: Full material test reports (MTRs) and AMS 6512 compliance documentation.
- Technical Partnership: Free metallurgical guidance on heat treatment, machining strategies, or weld optimization.
Your mission-critical projects demand more than a supplier; they require a collaborator who understands the stakes. Let’s turn your toughest engineering challenges into competitive advantages.