Blanking
SteelPRO Group offers expert blanking services, providing precise and efficient cutting of metal sheets into specific shapes for a wide range of industries. We ensure high material utilization and production efficiency tailored to your needs.
What is Blanking?
Blanking is a metalworking process that cuts metal sheets into predetermined shapes using a stamping and die system. The result is a metal piece in the desired shape. This efficient method is ideal for large-scale production, allowing for the rapid manufacture of many identical parts with high precision. Blanking maximizes material utilization, minimizing waste, as the cut-out part is the final product.
Common materials for blanking include carbon steel, stainless steel, and aluminum. Blanking is commonly used in the automotive, aerospace, and appliance industries for various metal components.
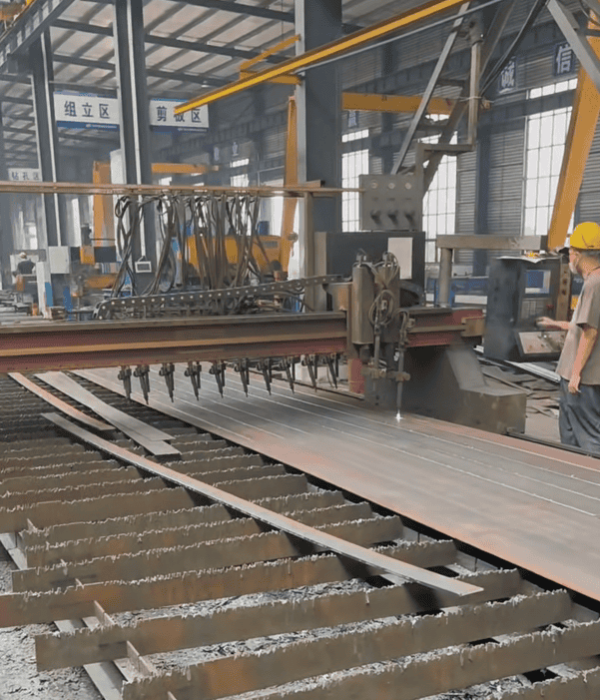
Types of Blanking
- Continuous Strip Blanking: Feeds metal sheets continuously into a stamping machine for high-volume production of items like medals and bottle caps.
- Fine Blanking: Compresses the metal sheet before cutting to reduce fractures and burrs, achieving tighter tolerances and less post-processing.
- Compound Die Stamping: Used for manufacturing complex steel parts quickly and accurately with automated processes.
- Conventional Blanking: Cuts desired shapes using a single downward force, typically resulting in more waste material.
- Square Sheared Blanking: Produces blanks with square edges using specialized tools, ideal for panels and square components.
- Progressive Die Stamping: Involves multiple steps through a series of dies for producing complex shapes in a single operation.
Differences Between Punching and Blanking
- Definition: Blanking removes a shape from a sheet, while punching creates holes or features in the material.
- End Product: Blanking produces the desired part as the final product; punching leaves a hole and discards the cut material.
- Material Usage: Blanking maximizes material utilization since the cut-out part is used; punching may result in waste if not properly planned.
- Applications: Blanking is used for parts like plates and panels; punching is typically used for creating holes in metal sheets for assembly.
- Process Goals: Blanking focuses on shape and size, while punching emphasizes hole size and spacing.
These differences highlight the distinct purposes and outcomes of punching and blanking in metal fabrication.
Differences Between Blanking, Cut-to-Length, Slitting, and Shearing
- Blanking: Cuts a shape from sheet metal to create a specific part.
- Cut-to-Length: Cuts long sheets or coils into shorter, specified lengths.
- Slitting: Cuts wide coils into narrower strips lengthwise.
- Shearing: Uses straight blades to cut metal sheets or strips, creating straight edges.
The main difference lies in the type of cut and the equipment used. Blanking uses a punch and die for specific shapes, cut-to-length slices coils into set lengths, slitting narrow coils, and shearing uses blades for straight cuts.
Why Choose Us for Blanking
- High Precision and Efficiency
We use advanced equipment to deliver accurate, high-quality blanks quickly, ensuring minimal waste and tight tolerances. - Expertise with Various Materials
We handle a wide range of materials, including carbon steel, stainless steel, and aluminum, for different industries and applications. - Comprehensive Additional Services
Beyond blanking, we offer slitting, shearing, cut-to-length, and beveling services, providing a full range of metal processing solutions. - Cost-Effective Solutions
Our process optimizes material usage and production speed, helping to reduce costs while maintaining top quality.
FAQ
How do you minimize material waste in blanking?
Optimizing the layout of parts on the sheet maximizes material usage, reducing scrap.
What causes burrs in blanking, and how can they be reduced?
Burrs are caused by dull tools or improper clearance. Using sharp tools and maintaining correct die clearance helps reduce them.
How do you handle distortion during blanking?
Using the right tool design and material support during cutting minimizes distortion.
How can blanking achieve high precision for complex shapes?
High-quality dies and precise press controls ensure tight tolerances, even for intricate designs.
How do you ensure consistent quality in large orders?
We use precise tools and automated systems to maintain quality across all parts, even in high-volume production.
What is the lead time for blanking services?
Lead time depends on the project size, but we focus on fast turnaround while maintaining accuracy.
Can you handle complex shapes with tight tolerances?
Yes, our advanced equipment and skilled team can produce complex shapes with high precision and minimal deviation.
What is multi-blanking?
Multi-blanking is a process where a metal coil is simultaneously cut into multiple blanks of different widths and lengths in a single pass. This method increases efficiency by producing multiple parts in one operation, reducing waste and setup time.