Contents
Main Stainless Steel Grades and Grades Chart
- John
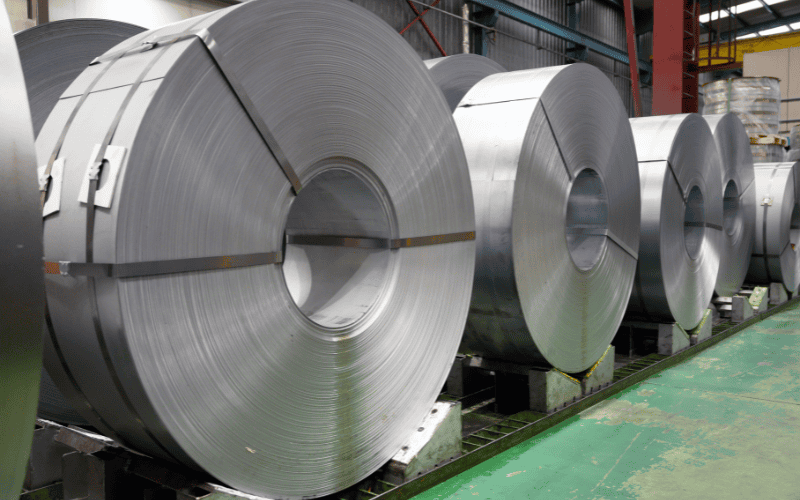
Stainless steel is divided into five main families: austenitic, ferritic, martensitic, duplex, and precipitation hardening. Those families have different grades, like 300 series and 400 series. And 304 and 316 are the most common grades.
We will introduce you to the common grades of each family and their properties and applications. We also make a comparison chart of their properties to help you conveniently choose the right grades.
Click here to go to the Stainless Steel Chart.
Different Grading Systems of the Stainless Steel Grades
There are many different systems in different organizations, such as the American Iron and Steel Institute (AISI), Chinese Standards (GB), and European Standards (EN).
Now, the Society of Automotive Engineers International (SAE) system is the most common one. It uses 3 numbers to name the different grades. The first number means the alloy type, and the others explain its rate, such as 304. Common stainless steel grades, including the 200, 300, 400, 500, 600, and 900 series, are also from SAE.
The American Iron and Steel Institute (AISI) also developed a system. The system is similar to SAE, so they didn’t use it anymore.
Each system has a different approach, resulting in the same grade of stainless steel being given different names in different systems. Take SAE Grade 304 as an example; it may have different names in other standards:
UNS | S30400 |
Chinese Standards (GB) | 06Cr19Ni10 |
German Standards (DIN) | X5CrNi18-9, X5CrNi18-10, X5CrNi19-9 |
EN number | 1.4305 |
European Standards (EN) | X8CrNiN18-9 |
Japanese Industrial Standards (JIS) | SUS 304, SUS 304-CSP |
British Standards (BS) | 304S 15, 304S 16, 304S 18, 304S 25, En58E |
Austenitic Stainless Steel Grades
Austenitic stainless steel contains at least 16% chromium and 6% nickel, is non-magnetic when annealed, and has excellent heat, cold, and corrosion resistance. It cannot be hardened by heat treatment. It is often used in food and healthcare applications, as well as in manufacturing outdoor enclosures and cryogenic pressure vessels. Austenitic mainly includes 200 series and 300 series.
Grade 304——Most Commonly Used and Widely Used
- 304 stainless steel, named 18/8 (18% Cr and 8% Ni), has excellent corrosion resistance and performs well at high and low temperatures. It is one of the food-grade stainless steels often used as cookware. However, it is not recommended to be in contact with salt water for a long time because it has poor tolerance to salt water.
Grade 316——Marine and Food Grade Stainless Steel
- 316 stainless steel has excellent resistance to chloride ion corrosion and is used in marine applications and surgical instruments. Its corrosion resistance is better than 304, especially in chloride environments. There are several different types of 316 stainless steel, including L, F, N, and H variants, each with slightly different properties and uses. For example, 316L stainless steel is a low-carbon version of 316 stainless steel that minimizes carbide precipitation during welding.
Grade 201
- 201 stainless steel has good corrosion resistance, high strength, and low nickel content, is suitable for cold working, and is often used in appliances and kitchen appliances. It has a lower nickel (5%) content and is cheaper than 304 (8%).
Grade 202
- 202 stainless steel has good corrosion resistance, is suitable for cold working, and is used in food processing equipment. It has a higher manganese content and higher strength than 201.
Grade 205
- 205 stainless steel has excellent corrosion resistance and high hardness, is suitable for cold working, and is used in automotive interiors and washing machines. It has a higher manganese content and strength than 201.
Grade 301
- 301 stainless steel is a modified version of 304-grade stainless steel, containing less chromium and nickel, which increases its work hardening range but has similar corrosion resistance. It is strong, ductile, and corrosion-resistant in mildly corrosive environments at room temperature and is often used in automotive interiors and cookware.
Grade 302
- 302 stainless steel has good strength and toughness and is used for springs, washers, etc. It has better corrosion resistance than type 301, and its carbon content is a little higher than that of type 304.
Grade 303
- With a high sulfur content, 303 stainless steel is easier to cut and machine. However, its corrosion resistance and toughness are reduced, and it is not as good as other chrome-nickel grades, such as 304 or 316, for fasteners and fittings.
Grade 304
- SAE 304 stainless steel is the most common stainless steel. It is an austenitic stainless steel containing iron, carbon, chromium and nickel and is non-magnetic. It has higher corrosion resistance than ordinary steel, is easily formed, and is used in a variety of household and industrial applications.
Grade 305
- 305 stainless steel has a low work hardening rate and is easier to form and draw. It has excellent formability and outstanding corrosion resistance. It is commonly used in electronic components, kitchen equipment, household appliances, and automotive parts.
Grade 308
- 308 stainless steel, which is primarily composed of 20% chromium and 10% nickel, is known for its excellent weldability and is often used as a filler material, such as welding rod or wire, especially for welding 304 or similar types of stainless steel.
Grade 309
- 309 stainless steel was developed specifically for high-temperature corrosion-resistant applications for furnace components and furnace linings. It is oxidation resistant up to 1900°F at constant temperature and has better high-temperature properties than 304.
Grade 314
- 314 stainless steel has extremely high-temperature oxidation resistance and is used in furnace parts and kiln linings. It has better high-temperature performance than 309.
Grade 316
- 316 stainless steel has excellent resistance to chloride ion corrosion due to the addition of molybdenum and is used in marine applications and surgical instruments. Its corrosion resistance is better than 304, especially in chloride environments.
Grade 317
- 317 stainless steel has higher chloride ion corrosion resistance than 316 and is used in chemical processing equipment.
Grade 321
- 321 stainless steel has titanium added to improve its resistance to intergranular corrosion and high-temperature resistance and is used in aerospace components and exhaust systems.
Grade 347
- 347 stainless steel has niobium added to it, giving it good general corrosion resistance comparable to 304. It can withstand temperatures of 800 – 1500°F (427 – 816°C) and is used in chemical processing equipment.
Grade 904L
- 904L stainless steel has high nickel and chromium content and is designed to provide corrosion and pitting resistance in a variety of process environments. It resists attack by warm seawater and chlorides and can be used in chemical processing and seawater handling.
Grade A2
- A2 stainless steel has a silvery, slightly reflective surface. Its corrosion resistance is very good. And it has a balance of durability and workability. Its common uses include kitchen equipment, building elements, automotive parts and chemical containers.
Grade 18/8
- 18/8, also known as 304, is mainly composed of 18% chromium and 8% nickel. Its most notable feature is its excellent corrosion resistance and is often used in kitchen utensils, medical equipment, food processing, etc.
Grade 18/10
- 18/10 stainless steel, also known as 304 stainless steel, contains 18% chromium and 10% nickel. It is corrosion resistant, strong and tough and is used in kitchenware, tableware, medical devices, industrial applications, construction and jewelry.
Ferritic Stainless Steels Grades
Ferritic stainless steel contains 10.5% to 27% chromium, little or no nickel, and is lower cost. It is magnetic, non-hardenable by heat treatment, and has good corrosion resistance. Additions of niobium, titanium, and zirconium improve weldability. It is used in automotive exhaust pipes, building and structural applications, blades, and power plates in solid oxide fuel cells. Ferrite includes some models in the 400 series.
Grade 405
- 405 stainless steel is cheaper than austenitic steel. It has good acid corrosion resistance and is magnetic. It is used in steam generator pipes, annealing boxes, etc.
Grade 408
- 408 stainless steel has good resistance to most oxidizing acids and salt spray, is magnetic, and is used in heat exchangers and furnace parts. Corrosion resistance is lower than austenitic steel.
Grade 409
- 409 stainless steel has good corrosion resistance and magnetism. Used in automotive exhaust systems, it is inexpensive and has lower corrosion resistance than 430.
Grade 414
- 414 stainless steel has good corrosion resistance and magnetism. It has better high-temperature performance than 409 and is used in agricultural equipment.
Grade 429
- 429 stainless steel has good corrosion resistance and magnetism and is used in automotive interiors and kitchen equipment. It has better resistance to nitric acid than 430.
Grade 430
- 430 stainless steel is magnetic, and its corrosion resistance is close to that of 304 stainless steel, but its weldability is poor due to its high carbon content and lack of stabilizing elements. It is used for decorative trims and automotive parts and is the most widely used ferritic stainless steel.
Grade 434
- 434 stainless steel has excellent pitting resistance and magnetism and is used in automotive interiors and kitchen equipment. Adding molybdenum enhances pitting resistance.
Grade 436
- 436 stainless steel has excellent resistance to citric and nitric acid corrosion, is magnetic, and is used in kitchen equipment and automotive interiors. Adding molybdenum provides better acid resistance.
Grade 442
- 442 stainless steel has good corrosion resistance, is magnetic, and is used in furnace parts and heat exchangers. It has better oxidation resistance than 430.
Grade 444
- 444 stainless steel has molybdenum added to improve its resistance to pitting and crevice corrosion, has good oxidation resistance and magnetic properties, and is used in hot water tanks and solar water heaters.
Grade 18/0
- 18/0 stainless steel is composed of 18% chromium and 0% nickel and is equivalent to 430 (AISI). It has good oxidation and corrosion resistance, particularly in mildly corrosive environments. It is widely used in kitchen utensils, sinks, and appliances.
Martensitic Stainless Steel Grades
Martensitic stainless steel contains 10.5%-18% Cr, 0.15%C, and 0.1%Mn. It is magnetic, has moderate corrosion resistance, and can be hardened by heat treatment. It is used in blades, surgical instruments, razor blades, hydraulic turbines, and applications requiring high strength and toughness. Martensite mainly includes some models in the 400 series.
Grade 410
- 410 stainless steel has very low to zero nickel content (0–0.75%), has good corrosion resistance to air, water, and some chemicals, and is magnetic. It is the most widely used hardenable stainless steel and can be hardened by heat treatment for use in valves and cookware.
Grade 410S
- 410S stainless steel has good oxidation resistance, is magnetic, and has a lower carbon content than 410, resulting in better weldability and less cracking sensitivity. Used in petrochemical applications.
Grade 416
- 416 stainless steel has poor chloride resistance, good acid, alkali, and freshwater resistance, is magnetic, and is easier to machine due to its higher sulfur content. Used in fasteners, gears, and pump shafts.
Grade 420
- 420 stainless steel is resistant to weak acids, alkalis, and water after hardening, is magnetic, has a higher carbon content, and can be hardened by heat treatment. Used for surgical instruments and cutlery.
Grade 422
- 422 Stainless steel has limited corrosion resistance, is magnetic, and has high hardness at high temperatures. It has better high-temperature performance than 410 and is widely used in high temperatures up to 1200°F, such as turbine blades and high-temperature fasteners.
Grade 431
- 431 stainless steel has nickel added to it, has excellent corrosion resistance and toughness, is magnetic, and can be heat treated to high strength. Used for aircraft parts, bolts, and nuts.
Grade 440
- 440 stainless steel is hard due to its high carbon content and can be heat treated to very high strength. However, it has limited corrosion resistance, is magnetic, and is used for cutting tools and blades.
Duplex Stainless Steels Grades
Duplex stainless steel is a two-phase, ferritic, austenitic alloy containing 19% to 32% chromium, up to 5% molybdenum, and lower nickel content. Duplex stainless steel has excellent corrosion resistance and has a yield strength of about twice that of austenitic stainless steel. It is used in the oil and gas industry, chemical and petrochemical plants, heat exchangers, construction, and water industry applications.
Precipitation Stainless Steels Grades
Precipitation hardening (PH) stainless steels contain 17% chromium and 4% nickel, as well as other elements such as titanium, aluminum, and niobium. They have corrosion resistance comparable to austenitic varieties and are able to achieve high strength through precipitation hardening. They are magnetic and can achieve high strength through simple heat treatment. Used in nuclear waste drums, turbine blades, aerospace industry, and pulp and paper industry equipment. 630 is the most common PH stainless steel, commonly known as 17-4.
Grade 630
- 630 Stainless steel has corrosion and heat resistance comparable to 304, high hardness, is magnetic and can be precipitation hardened. However, due to its precipitation-hardening properties, it is difficult to machine and is used in aerospace and chemical processing.
Stainless Steel Grades Chart
Below is more specific information about each stainless steel grade.
Grade | Chemical composition | Tensile Strength | Maximum Use Temp | Melting Point | Ductility (%) | Hardness (HB) | Magnetic |
Austenitic | |||||||
201 | 16-18% Cr, 3.5-5.5% Ni, 5.5-7.5% Mn | 515 MPa (75 Ksi) | 700˚C (1292˚F) | 1400-1450°C (2552-2642°F) | 40% | 250 | No |
202 | 17-19% Cr, 4-6% Ni, 7.5-10% Mn | 515 MPa(75 Ksi) | 800˚C (1472˚F) | 1400-1450°C (2552-2642°F) | 40% | 250 | No |
205 | 16.5-18% Cr, 1-1.75% Ni, 14-15% Mn | 515 MPa(75 Ksi) | 800˚C (1472˚F) | 1400-1450°C (2552-2642°F) | 40% | 250 | No |
301 | 16-18% Cr, 6-8% Ni | 515 MPa(75 Ksi) | 871 °C (1600 °F) | 1399-1421°C (2550-2590°F) | 40% | 201 | No |
302 | 17-19% Cr, 8-10% Ni | 585 MPa (85 Ksi) | 870˚C (1598˚F) | 1400-1420°C (2550-2590°F) | 40% | 201 | No |
303 | 17-19% Cr, 8-10% Ni, 0.15-0.35% S | 690 MPa(100 Ksi) | 760˚C (1,400˚F) | 1400-1420°C (2550-2590°F) | 35% | 262 | No |
304 | 18-20% Cr, 8-10.5% Ni | 621 MPa (90 Ksi) | 870˚C (1598˚F) | 1399-1454°C (2550-2650°F) | 45% | 201 | No |
305 | 17-19% Cr, 10-13% Ni | 515 MPa (75 ksi) | 815°C (1500°F) | 1375-1425°C (2507-2597°F) | 40% | 205 | No |
308 | 19-21% Cr, 9-11% Ni | 620 MPa (90 ksi) | 870˚C (1598˚F) | 1400-1425°C (2552-2597°F) | 35% | 217 | No |
309 | 23% Cr, 13% Ni | 620 MPa (89 Ksi) | 1000˚C (1,832˚F) | 1400-1455°C (2550-2651°F) | 25% | 180 | No |
314 | 24-26% Cr, 19-22% Ni | 620 MPa(90 Ksi) | 1100˚C (2012˚F) | 1399-1421°C (2550-2590°F) | 45% | 217 | No |
316 | 16-18% Cr, 10-14% Ni, 2-3% Mo | 579 MPa (84 Ksi) | 800˚C (1,472˚F) | 1371-1399°C (2500-2550°F) | 45% | 217 | No |
317 | 18-20% Cr, 11-15% Ni, 3-4% Mo | 585 MPa(85 Ksi) | 816˚C (1,500˚F) | 1370-1400°C (2500-2550°F) | 40% | 217 | No |
321 | 17-19% Cr, 9-12% Ni, 0.7% Ti | 620 MPa(90 Ksi) | 816˚C (1,500˚F) | 1400-1425°C (2550-2600°F) | 45% | 217 | No |
347 | 17-19% Cr, 9-12% Ni, 0.8% Nb | 690 MPa(101 Ksi) | 816˚C (1,500˚F) | 1400-1425°C (2550-2600°F) | 45% | 217 | No |
904L | 19-23% Cr, 23-28% Ni, 4.5% Mo | 490 MPa (71 Ksi) | 400˚C (752˚F) | 1350-1400°C (2462-2552°F) | 35% | 200 | No |
A2 | 18% Cr, 8% Ni (Equivalent to 304) | 505 MPa (73 ksi) | 870˚C (1598˚F) | 1400-1450°C (2552-2642°F) | 40% | 123 | No |
18/8 | 18% Cr, 8% Ni | 505 MPa (73 ksi) | 870˚C (1598˚F) | 1400-1450°C (2552-2642°F) | 40% | 123 | No |
18/10 | 18% Cr, 10% Ni | 520 MPa (75 ksi) | 870˚C (1598˚F) | 1400-1450°C (2552-2642°F) | 40% | 129 | No |
Ferritic | |||||||
405 | 11.5-14.5% Cr | 585 MPa (85 Ksi) | 815˚C (1,499˚F) | 1480-1530°C (2700-2790°F) | 20% | 200 | Yes |
408 | 11% Cr, 8-10% Ni | 505 MPa (73 Ksi) | 815˚C (1,499˚F) | 1400-1455°C (2550-2651°F) | 25% | 170 | Yes |
409 | 10.5-11.75% Cr | 448 MPa (65 Ksi) | 815˚C (1,499˚F) | 1425-1510°C (2597-2750°F) | 25% | 180 | Yes |
414 | 11.5-13% Cr | 500 MPa (73 Ksi) | 650˚C (1202˚F) | 1425-1510°C (2597-2750°F) | 20% | 250 | Yes |
429 | 14-16% Cr | 450 MPa (65 Ksi) | 815˚C (1,499˚F) | 1425-1510°C (2597-2750°F) | 25% | 200 | Yes |
430 | 16-18% Cr | 450 MPa (65 Ksi) | 815˚C (1,499˚F) | 1425-1510°C (2597-2750°F) | 25% | 200 | Yes |
434 | 16-18% Cr,1% Mo | 540 MPa (78 Ksi) | 815˚C (1,499˚F) | 1426-1510°C (2600-2750°F) | 25% | 200 | Yes |
436 | 17% Cr、1.25% Mo | 459 MPa (67 Ksi) | 815˚C (1,499˚F) | 1425-1510°C (2600-2750°F) | 25% | 200 | Yes |
442 | 18-23% Cr | 515-550 MPa(77-80 Ksi) | 925-980˚C (1,700/1,800˚F) | 1065-1120°C (1950-2048˚F) | 20% | 250 | Yes |
444 | 17-20% Cr、1.8-2.5% Mo | 415 MPa (60 Ksi) | 950˚C (1,752˚F) | 1405-1495°C (2561-2723°F) | 25% | 200 | Yes |
18/0 | 18% Cr, 0% Ni | 450 MPa (65 ksi) | 760°C (1400°F) | 1425-1510°C (2597-2750°F) | 30% | 200 | Yes |
Martensitic | |||||||
410 | 11.5-13.5% Cr、0.15% C | 500-1400 MPa (73-203 Ksi) | 650˚C (1202˚F) | 1482-1532°C (2700-2790°F) | 15% | 250 | Yes |
410S | 11.5-13.5% Cr、0.08% C | 444 MPa (64 Ksi) | 705˚C (1300˚F) | 1482-1532°C (2700-2790°F) | 20% | 250 | Yes |
416 | 12-14% Cr、0.15-0.35% S | 517 MPa (75 Ksi) | 760˚C (1,400˚F) | 1480-1530°C (2696-2786°F) | 25% | 250 | Yes |
420 | 12-14% Cr、0.15-0.45% C | 586 MPa (85 Ksi) when annealed | 650˚C (1202˚F) | 1454-1510°C (2649-2750°F) | 20% | 250 | Yes |
422 | 11.5-14% Cr、0.20-0.25% C | 760 MPa (110 Ksi) | 760˚C (1,400˚F) | 1483°C (2700°F) | 15% | 250 | Yes |
431 | 15-17% Cr、1.25-2.5% Ni | 500-1500 MPa (73-217 Ksi) | 650˚C (1202˚F) | 1482-1532°C (2700-2790°F) | 20% | 250 | Yes |
440 | 16-18% Cr、0.75-1.20% C | 758 MPa (110 Ksi) | 760˚C (1,400˚F) | 1483°C (2700°F) | 15% | 250 | Yes |
Precipitation | |||||||
630 | 16-17% Cr、4-5% Ni、3-5% Cu | 1103 MPa (160 Ksi) | 316˚C (600˚F) | 1404-1440°C (2560-2625°F) | 15% | 350 | Yes |
Download the Stainless Steel Grades Chart PDF
Comparison of Common Stainless Steel Grades
Common stainless steel grades are 200 series, 300 series, and 400 series. Although the 200 series and 400 series are, to some extent, alternatives to the 300 series, their chemical composition, corrosion resistance, mechanical properties, and application areas are different.
200 Series VS 300 Series
Chemical composition:
200 series: mainly composed of chromium, manganese, and nitrogen, with a lower nickel content. The addition of nitrogen increases the hardness and strength of the 200 series.
300 series: mainly composed of chromium and nickel. 304 stainless steel contains about 18% chromium and 8% nickel and is the most common in the 300 series. 316 stainless steel contains 2-3% molybdenum, which enhances its corrosion resistance.
Corrosion resistance:
200 series: 200 series stainless steel is prone to corrosion in chemical environments due to its lower nickel content and is not as corrosion resistant as 300 series.
300 series: has excellent corrosion resistance, especially in environments containing chlorides and other chemicals. 316 stainless steel exhibits stronger salt and acid resistance due to the addition of molybdenum.
Mechanical properties:
200 series: higher hardness and strength, but not as good as 300 series in ductility and formability.
300 series: has good ductility and formability and can maintain excellent mechanical properties in low and high-temperature environments.
Application areas:
200 series: commonly used in washing machines, tableware, kitchen equipment, and other fields. It is widely used due to its economy and high hardness.
300 series: more widely used, covering food processing, chemical equipment, medical equipment, architectural decoration, and other fields. It has been widely adopted due to its excellent comprehensive performance.
300 Series VS 400 Series
Chemical composition:
300 series: mainly composed of chromium and nickel, it is austenitic stainless steel. 304 and 316 are the main grades of stainless steel.
400 series: mainly composed of chromium and manganese, it is ferritic and martensitic stainless steel, containing no or very little nickel.
Corrosion resistance:
300 series: Excellent corrosion resistance, especially in wet and chemical environments. 316 stainless steel exhibits stronger resistance to chloride corrosion due to its molybdenum content.
400 series: Not as corrosion resistant as 300 series, but still performs well in some specific environments. 400 series is more suitable for dry environments and has a lower corrosion risk.
Mechanical properties:
300 Series: They have a stable state and cannot be hardened by heat treatment, but they have good ductility and toughness and are suitable for a wide range of applications.
400 Series: They have high hardness and strength, so they are suitable for high strength and wear resistance applications. They can also be hardened by heat treatment but have poor ductility and toughness.
Magnetism:
300 series: Usually non-magnetic due to its high nickel content.
400 series: Magnetic, especially martensitic stainless steels such as 410 stainless steel.
Application areas:
300 series: Suitable for applications requiring high corrosion resistance and high toughness, such as food processing, chemical equipment, and architectural decoration.
400 Series: Suitable for applications requiring high hardness and wear resistance, such as automotive parts and agricultural equipment.
Is 304 or 316 Stainless Steel Better?
The key difference between 304 and 316 stainless steel is corrosion resistance. 304 contains 18% chromium and 8% nickel, while 316 has 2-3% molybdenum, which improves resistance to saltwater and harsh chemicals, making 316 ideal for marine and industrial applications.
For general use, 304 is more common due to its lower cost and sufficient corrosion resistance for most environments. Both are highly formable and used in food processing, kitchenware, and architecture, but 316 is preferred in more corrosive conditions.
Read articles about 304 vs 316!
Which is Better, 304 or 420 Stainless Steel?
304 stainless steel offers better corrosion resistance and ductility, making it suitable for a wide range of uses like kitchen appliances and chemical processing. It’s non-magnetic and part of the 300 series.
420 stainless steel, a martensitic grade, is harder due to its higher carbon content and can be heat treated, making it ideal for knives and tools. However, it lacks the corrosion resistance of 304, limiting its use in environments where rust is a concern.
Which is Better, 18-8 or 304 Stainless Steel?
18-8 and 304 stainless steel are nearly identical in composition, both containing 18% chromium and 8% nickel. 304 is a specific grade of 18-8 and is the most widely used for general applications like kitchen equipment and construction.
Although 304 may have tighter specifications for carbon content, both perform similarly in terms of corrosion resistance and strength. 18-8 is common in fasteners, while 304 is preferred for more industrial or commercial applications.
Which is Better 18-0 or 18-10 Stainless Steel?
The main difference between 18-0 and 18-10 stainless steel is nickel content. Both contain 18% chromium for corrosion resistance, but 18-10 has 10% nickel, enhancing durability and rust resistance, making it ideal for higher-end cookware and cutlery.
18-0, with no nickel, is more affordable and often used in budget cookware. While it’s less resistant to rust, it still performs well for everyday kitchen items that don’t face heavy exposure to moisture.
Is 420 Stainless Steel Better Than 316?
420 stainless steel is known for its hardness and is ideal for cutting tools, such as knives and surgical instruments. However, it has lower corrosion resistance compared to 316, which contains molybdenum and excels in corrosive environments like saltwater or chemicals.
While 420 is better for applications requiring wear resistance, 316 is preferred in environments where corrosion protection is critical, such as marine, chemical, and medical industries.
You may also want to know:
What Are the 4 Types of Stainless Steel?
The four main types are austenitic, ferritic, martensitic, and duplex. Austenitic is the most common, known for excellent corrosion resistance (e.g., 304, 316). Ferritic offers moderate corrosion resistance and is magnetic. Martensitic is hard and used in cutlery. Duplex combines properties of austenitic and ferritic for superior strength and resistance.
Which Grade Is the Food Grade Stainless Steel?
Grades 304 and 316 are commonly used for kitchen equipment and cookware due to their good corrosion resistance, ease of cleaning, and durability.
Is 304 SS Marine Grade?
No, 304 stainless steel is not considered marine grade. While it has good corrosion resistance, it lacks the molybdenum that enhances resistance to saltwater environments. For marine applications, 316 stainless steel is preferred due to its superior corrosion resistance, especially against chloride and salt exposure.
What Is the Best Grade Stainless Steel?
The best grade depends on the application. For general-purpose corrosion resistance, 304 is widely used. However, 316 is considered the best in harsh environments, especially marine or chemical settings, due to its added molybdenum, providing better resistance to corrosion.
What Is the Most Expensive Grade of Stainless Steel?
Grade 904L is among the most expensive types of stainless steel. It contains high levels of chromium, nickel, and molybdenum, making it extremely resistant to corrosion, especially in acidic environments. This premium material is used in luxury industries like high-end watches and chemical plants.
How Do I Choose Stainless Steel Grades?
Choosing the right stainless steel grades involves evaluating corrosion resistance, mechanical properties, temperature tolerance, and cost. For general use, 304, with its high strength and high corrosion resistance, is ideal. For harsher environments, choose 316, which has better chemical and salt resistance. The 400 series offers higher strength and hardness but less corrosion resistance. Consider the specific environmental conditions and mechanical requirements, consult technical resources, and balance costs to ensure optimal performance for your application.
Get Satisfactory Stainless Steel!
We specialize in high-quality stainless steel to meet the needs of a wide range of industries. To learn more about stainless steel or other steel types, check out our blog or contact one of our metals experts. If you want to make your next project even better, feel free to contact us for a quote.
- Stainless Steel Grades
- 300 Series Stainless Steel
- 303 Stainless Steel
- 304 Stainless Steel
- 305 Stainless Steel
- 308 Stainless Steel
- 316 Stainless Steel
- 316N Stainless Steel
- 409 Stainless Steel
- 410 Stainless Steel
- 416 Stainless Steel
- 420 Stainless Steel
- 430 Stainless Steel
- 410HT And 410L Stainless Steels
- 410S Stainless Steel
- 440 Stainless Steel
- 436 Stainless Steel
- 301 Stainless Steel
- 201 Stainless Steel
- 202 Stainless Steel
- 444 Stainless Steel
- 405 Stainless Steel
- 302 Stainless Steel
- 309 Stainless Steel
- 314 Stainless Steel
- 321 Stainless Steel
- 347 Stainless Steel
- 408 Stainless Steel
- 422 Stainless Steel
- 431 Stainless Steel
- 434 Stainless Steel
- 414 Stainless Steel
- 430FR Stainless Steel
- 13-8 PH Stainless Steel
- 317 | 317L Stainless Steel
- 616 Stainless Steel
- 630 Stainless Steel
- 904L Stainless Steel
- A2 Stainless Steel
- 304 vs 304L Stainless Steel
- 304 VS 316 Stainless Steel
- 304 vs 409 Stainless Steel
- 304 vs 430 Stainless Steel
- 410 Stainless Steel vs 304
- 18/0 vs 18/10
- 18/0 Stainless Steel
- 18/8 Stainless Steel
- 18/10 Stainless Steel
Comparisons