Contents
Austenitic Stainless Steel: Definition, Composition, Properties, Grades, Applications and More
- John
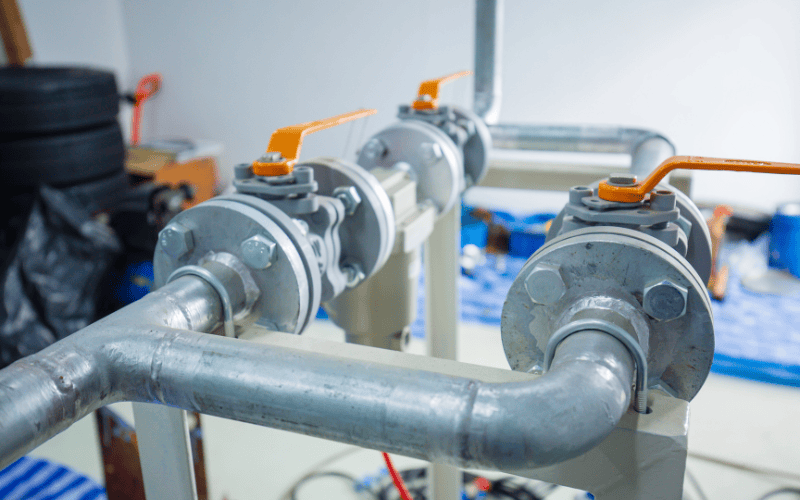
What Is Austenitic Stainless Steel?
Austenitic stainless steel is one of the five major classes of stainless steel defined by crystalline structure with a face-centered cubic (FCC) crystalline structure, primarily composed of 15-32% chromium and 8-37% nickel, with a balance of other elements such as manganese and nitrogen. Austenitic stainless steel has excellent corrosion resistance and formability, high toughness and ductility, and is non-magnetic. Common grades include 304, 316, and 310. Austenitic stainless steel is widely used in food, chemical, and medical industries.
Crystal Structure of Austenitic Stainless Steel
Austenitic stainless steel has a face-centered cubic (FCC) crystal structure. It is a type of crystal arrangement. Imagine a cube with an atom at each of its eight corners and an additional atom in the center of each face. This arrangement is highly compact, with atoms positioned closely together, making the material more stable and less prone to breaking when deformed.
This structure grants austenitic stainless steel:
- High plasticity, toughness, and ductility
- Good mechanical properties at high and low temperatures
- Strong corrosion resistance and oxidation resistance
- Non-magnetic properties
How Does Austentic Structure Form in Stainless Steel?
Austenitic stainless steels achieve their unique structure through the addition of alloying elements like nickel and chromium.
In pure iron or plain-carbon steel, the austenitic (face-centered cubic) structure is stable only at high temperatures—around 1340°F (727°C) or higher. However, when approximately 18% chromium and 8% nickel are added to the steel, this austenitic structure becomes stable across the entire temperature range, from room temperature up to the melting point.
Nickel acts as an austenite stabilizer, allowing the face-centered cubic lattice to persist even at lower temperatures. Chromium not only enhances corrosion resistance but also contributes to the stability of the austenitic phase. This combination of elements helps maintain an austenitic structure, offering benefits like improved ductility and excellent corrosion resistance.
Chemical Composition of Austenitic Stainless Steel
Austenitic stainless steel is primarily composed of chromium, nickel, and carbon, along with other elements that enhance specific properties.
- Chromium (Cr) (15-32%) provides corrosion resistance by forming a passive chromium oxide layer that self-heals when exposed to air or moisture.
- Nickel (Ni) (8-37%) stabilizes the austenitic structure, improving toughness, ductility, formability, and corrosion resistance.
- Carbon (C) is kept very low, typically below 0.08%, especially in low-carbon grades like 304L and 316L (below 0.03%), to minimize carbide precipitation during welding, thus reducing the risk of intergranular corrosion.
In addition,
- Manganese (Mn) can partially replace nickel in certain alloys, particularly in the 200 series, acting as an austenite stabilizer and increasing nitrogen solubility and tensile strength while also reducing production costs.
- Molybdenum (Mo) (2%-3%) is added to enhance resistance to pitting and crevice corrosion, particularly in chloride-rich environments such as seawater.
- Nitrogen (N) increases strength and enhances resistance to localized corrosion, particularly in high-performance alloys.
- Copper (Cu) is occasionally added, especially in specialized alloys, to improve resistance to corrosion in specific acidic environments, such as sulfuric and phosphoric acid.
*Austenitic stainless steel may also contain trace elements such as silicon (Si), phosphorus (P), sulfur (S), titanium (Ti), niobium (Nb), and cobalt (Co), but we do not discuss them in detail here.
Properties of Austenitic Stainless Steel
Here are three major reasons that make austenitic stainless steel unique:
- Excellent corrosion resistance in many environments.
- High toughness and ductility, even at low temperatures.
- Non-magnetic and can only be hardened by cold working.
Check the table below for the key properties of austenitic stainless steel:
Property | Description | Performance | Remarks |
Corrosion Resistance | Ability to resist corrosion and oxidation. | Excellent in oxidizing environments due to high chromium and nickel content. | Molybdenum enhances corrosion resistance in chloride-rich environments. |
Mechanical Properties | Includes strength, toughness, hardness, and ductility. | Strong, tough, with good ductility and moderate hardness. | High strength and toughness help resist deformation under high stress, while good ductility prevents cracking under stress. |
Heat Resistance | Ability to withstand high temperatures without degradation. | Good resistance to oxidation at high temperatures. | Prolonged exposure to extreme heat can cause scaling. |
Low-Temperature Performance | Material performance in cold environments. | Exceptional toughness, resistant to brittle fractures. | Suitable for cryogenic applications where preventing brittleness is crucial. |
Formability | Ease of shaping through mechanical processes. | Excellent formability, suitable for both cold and hot working processes. | High malleability makes it ideal for producing complex shapes. |
Weldability | Ability to be welded without loss of strength. | Highly weldable while retaining corrosion resistance. | Post-weld heat treatment is typically unnecessary, making it ideal for applications in construction and automotive industries. |
Machinability | Ease of cutting, shaping, or finishing the material. | Moderate; work hardening and tool wear can be managed through optimization. | Using sharp tools and lower cutting speeds can improve machinability. Cold working may increase hardness. |
Magnetic Properties | Tendency to exhibit magnetic behavior. | Non-magnetic, but slight magnetism may develop after cold working. | Cold working may induce slight magnetism, which could impact non-magnetic applications. |
Advantages and Disadvantages of Austenitic Stainless Steel
Austenitic stainless steel provides the following benefits and advantages:
- Excellent corrosion resistance in a wide range of environments.
- High ductility, making it easy to form and weld.
- Maintains strength at high temperatures.
- Resists oxidation, even in moist air.
- Non-magnetic in the annealed condition.
It also faces challenges and disadvantages listed below:
- Higher cost due to the use of alloying elements like nickel.
- Susceptible to stress corrosion cracking in certain conditions.
- Difficult to machine due to its work-hardening properties.
- Lower strength compared to other stainless steel types.
- Poor resistance to wear and galling.
Subgroups of Austenitic Stainless Steel
Austenitic stainless steel is divided into two subgroups of AISI 200 Series and the AISI 300 Series. Both series are recognized by the American Iron and Steel Institute (AISI), the American Society for Testing and Materials (ASTM), and other organizations worldwide. The main difference is that the 200 Series uses manganese and nitrogen with less nickel, while the 300 Series relies on higher levels of chromium and nickel.
AISI 200 Series
AISI 200 Series stainless steel forms its austenitic structure by adding manganese and nitrogen with a reduced amount of nickel. Manganese and nitrogen maintain the austenitic structure and enhance strength. Common grades include 201 and 202. It is commonly used in kitchenware, automotive trim, and food processing equipment due to its cost-effectiveness.
AISI 300 Series
AISI 300 Series stainless steel forms its austenitic structure by adding higher levels of chromium and nickel. Chromium resists corrosion, while nickel adds ductility and toughness. Common grades like 304 (18/8 or A2) and 316 (A4) are widely used. The 300 series is commonly used in construction, chemical processing, and medical equipment because of its durability and corrosion resistance.
Austenitic Stainless Steel Grades
Take a look at the common grades in the austenitic stainless steel family:
Grade | Equivalent Grade (UNS/EN) | Description | Common Applications |
302 | S30200 / 1.4300 | General purpose 18-8 | Springs, washers, nuts, bolts, automotive trim |
202 | S20200 / 1.4373 | N and Mn partly replace Ni | Kitchen utensils, automotive components, railway cars, sinks |
201 | S20100 / 1.4372 | N and Mn partly replace Ni | Kitchen utensils, appliance structures, railway coaches, hoses |
305 | S30500 / 1.4303 | Ni increased to lower work hardening | Deep-drawn parts, electronic components, kitchen sinks, springs |
304 | S30400 / 1.4301 | Lower C for better corrosion resistance in welded structures | Chemical containers, kitchen equipment, architectural panels, tanks |
304L | S30403 / 1.4306, 1.4307 | C reduced for as-welded corrosion resistance | Structural components in high-temperature environments, heat exchangers, oil refinery parts, chemical processing equipment |
304N | S30451 / 1.4315 | N added to increase strength | Structural components, automotive exhaust systems, chemical tanks, marine equipment |
304NL | S30453 / 1.4311 | N added to increase strength | Structural components in corrosive environments, welded components, marine parts, pressure vessels |
303 | S30300 / 1.4305 | S added for machinability | Screws, nuts, bolts, shafts, valves |
303Se | S30323 / 1.4300 | Se added for better machinability | High-precision machining parts, electrical switchgear, valves, connectors |
S30430 | S30430 / 1.4567 | Cu added to improve cold working | Automotive heat exchangers, pressure vessels, pipes, architectural applications |
316 | S31600 / 1.4401 | Mo added to increase corrosion resistance | Medical instruments, marine hardware, chemical containers, food processing equipment |
316L | S31603 / 1.4404, 1.4435 | C reduced for as-welded corrosion resistance | Pharmaceutical equipment, marine applications, chemical processing tanks, food preparation surfaces |
316N | S31651 / 1.4429 | N added to increase strength | High-strength parts in corrosive environments, pressure vessels, marine components, medical devices |
316LN | S31653 / 1.4429 | C reduced, N added to increase strength | Nuclear reactor components, cryogenic vessels, chemical processing equipment, high-pressure piping |
316F | S31620 / 1.4436 | S and P added to improve machinability | Pump parts, valve components, shafts, precision-machined fittings |
317 | S31700 / 1.4449 | More Mo and Cr added for better corrosion resistance | Chemical process equipment, marine applications, pharmaceutical equipment, petrochemical refineries |
317L | S31703 / 1.4438 | C reduced for better welding characteristics | Pulp and paper industry equipment, chemical tanks, marine structures, flue gas desulfurization systems |
310, 310S | S31000, S31008 / 1.4840, 1.4845 | More Cr and Ni for even better heat resistance | Kiln linings, furnace components, combustion chambers, heat exchangers |
309, 309S | S30900, S30908 / 1.4828, 1.4833 | Cr and Ni increased for heat resistance | Furnace parts, heat exchangers, kiln liners, refinery equipment |
314 | S31400 / 1.4841 | Si increased for highest heat resistance | Furnace parts, gas burners, combustion chambers, heat exchangers |
330 | N08330 / 1.4886 | Ni added to resist carburization and thermal shock | Furnace parts, gas turbine components, heat exchangers, chemical process equipment |
302B | S30215 / – | Si added to increase scaling resistance | Furnace components, heat exchangers, automotive manifolds |
308 | S30800 / 1.4332 | Higher Cr and Ni, used primarily for welding | Welding rods, filler materials, high-temperature exhaust systems, furnace linings |
321 | S32100 / 1.4541 | Ti added to prevent carbide precipitation | Aircraft exhaust systems, thermal oxidizers, furnace parts, heat exchangers |
347 | S34700 / 1.4550 | Nb and Ta added to prevent carbide precipitation | Aerospace components, high-temperature equipment, welded boiler parts, gas turbine engines |
348 | S34800 / 1.4551 | Ta and Co restricted for nuclear applications | Nuclear reactor parts, high-temperature aircraft components, power generation components, heat exchangers |
205 | S20500 / – | N and Mn partly replace Ni | Commercial food processing equipment, kitchen appliances, storage tanks, welded structures |
384 | S38400 / – | More Ni to lower work hardening | Deep drawn parts, screws, bolts, springs, fasteners |
329 | S32900 / 1.4460 | (Duplex: Austenite + Ferrite) Cr increased and Ni reduced for stress corrosion cracking resistance | Oil and gas piping, marine equipment, chemical tanks, pressure vessels |
What Is the Best Grade of Austenitic Stainless Steel?
There isn’t a one-size-fits-all “best” grade of austenitic stainless steel. It depends on various factors. For general purposes, 304 stainless steel is common due to its good corrosion resistance and ease of fabrication. For higher corrosion resistance, such as in marine environments, 316 stainless steel is better because it contains molybdenum. For high-temperature applications, 310 stainless steel is suitable due to its excellent heat resistance. Each grade has its own strengths, so the best choice varies based on specific needs.
Applications of Austenitic Stainless Steel
Check the table below for key industries and applications where austenitic stainless steel is most commonly used:
Industry | Application |
Food & Beverage | Tanks, Pipelines, Storage Vessels, Processing Equipment |
Medical & Pharmaceutical | Surgical Instruments, Implantable Devices, Sterilization Trays, Diagnostic Equipment |
Chemical Processing | Heat Exchangers, Reactors, Pumps, Valves |
Oil & Gas | Piping, Offshore Platforms, Pressure Vessels, Heat Exchangers |
Automotive | Exhaust Systems, Fuel Tanks, Trim Components, Sensors |
Aerospace | Engine Components, Fasteners, Structural Parts, Exhaust Systems |
Construction | Roofing, Facade Panels, Railings, Structural Supports |
Power Generation | Boilers, Turbines, Flue Gas Desulfurization Units, Nuclear Reactor Components |
Austenitic vs. Martensitic vs. Ferritic vs. Duplex vs. Precipitation Hardened Stainless Steel
Compare the five classes of stainless steel in the table below:
Property | Austenitic Stainless Steel | Martensitic Stainless Steel | Ferritic Stainless Steel | Duplex Stainless Steel | Precipitation Hardened |
Crystal Structure | Austenitic (FCC) | Martensitic (BCT) | Ferritic (BCC) | Austenitic + Ferritic, usually 50% + 50% | Martensitic or Austenitic + Precipitation Hardening |
Mechanical Strength | High toughness, good ductility | High strength, high hardness | Moderate strength, good toughness | High strength, superior fracture resistance | Very high strength after heat treatment |
Corrosion Resistance | Excellent, especially in acidic and chloride environments | Moderate, prone to corrosion in harsh environments | Good, especially in oxidizing environments | Excellent, especially in chloride and marine environments | Good, but less than austenitic or duplex types |
Weldability | Excellent, minimal impact from welding | Poor, requires pre- and post-heat treatment | Moderate, post-weld heat treatment required | Good, but cooling rate must be controlled | Good, but heat treatment required after welding |
Heat Treatment | Cannot be hardened by heat treatment, cold work can strengthen | Quenching and tempering to adjust hardness | Not heat-treatable, can be strengthened by cold work | Maintains good properties after heat treatment | Strengthened by precipitation hardening heat treatment |
Typical Applications | Food processing, chemical equipment, medical devices | Blades, shafts, mechanical components | Automotive exhaust systems, heat exchangers | Marine engineering, oil and gas pipelines | Aerospace, nuclear, high-strength applications |
What You Might Also Concern
Now that you have a deeper understanding of austenitic stainless steel, there are still some common issues that deserve your attention:
What Is the Difference Between Stainless Steel and Austenitic Stainless Steel?
Stainless steel refers to a family of iron-based alloys known for their corrosion resistance. Austenitic stainless steel is a specific type within this group, known for its high chromium and nickel content, which enhances corrosion resistance and toughness. It is also the most commonly used type of stainless steel, making up about 70% of all stainless steel production.
What Are Other Types of Stainless Steel Apart From Austenitic Stainless Steel?
Other types of stainless steel include ferritic stainless steel, martensitic stainless steel, duplex stainless steel, and precipitation-hardening stainless steel.
Will Austenitic Stainless Steel Get Rusted?
Austenitic stainless steel is highly resistant to rust. However, it can still rust under extreme conditions, such as prolonged exposure to saltwater or harsh chemicals, or if the protective layer is damaged or worn away.
Related Reading
Will Stainless Steel Rust and How Can You Solve It?
Is Austenitic Stainless Steel Magnetic?
Austenitic stainless steel is generally non-magnetic. However, it can become slightly magnetic after cold working, such as bending or forming, due to the transformation of some austenite to martensite.
Related Reading
Is Stainless Steel Magnetic?
Is Austenitic Stainless Steel Safe for Cooking?
Yes, austenitic stainless steel is safe for cooking and is commonly used in kitchenware and food processing equipment. Its corrosion resistance and non-reactive nature make it ideal for use with food and beverages, preventing contamination and preserving flavor.
Summary & Furthermore
This article briefly explains the definition, composition, properties, grades, applications, and other important aspects of austenitic stainless steel. To learn more about stainless steel or other steel types, check out our blog or contact our metal experts.
As a leading manufacturer and solutions provider of specialty steel, SteelPRO delivers multi-industry application solutions and customized services. We guarantee 100% product quality and are committed to growing together with our customers. Visit our website to learn more, or send us an inquiry. We will contact you shortly!
- Stainless Steel Grades
- 300 Series Stainless Steel
- 303 Stainless Steel
- 304 Stainless Steel
- 305 Stainless Steel
- 308 Stainless Steel
- 316 Stainless Steel
- 316N Stainless Steel
- 409 Stainless Steel
- 410 Stainless Steel
- 416 Stainless Steel
- 420 Stainless Steel
- 430 Stainless Steel
- 410HT And 410L Stainless Steels
- 410S Stainless Steel
- 440 Stainless Steel
- 436 Stainless Steel
- 301 Stainless Steel
- 201 Stainless Steel
- 202 Stainless Steel
- 444 Stainless Steel
- 405 Stainless Steel
- 302 Stainless Steel
- 309 Stainless Steel
- 314 Stainless Steel
- 321 Stainless Steel
- 347 Stainless Steel
- 408 Stainless Steel
- 422 Stainless Steel
- 431 Stainless Steel
- 434 Stainless Steel
- 414 Stainless Steel
- 430FR Stainless Steel
- 13-8 PH Stainless Steel
- 317 | 317L Stainless Steel
- 616 Stainless Steel
- 630 Stainless Steel
- 904L Stainless Steel
- A2 Stainless Steel
- 304 vs 304L Stainless Steel
- 304 VS 316 Stainless Steel
- 304 vs 409 Stainless Steel
- 304 vs 430 Stainless Steel
- 410 Stainless Steel vs 304
- 18/0 vs 18/10
- 18/0 Stainless Steel
- 18/8 Stainless Steel
- 18/10 Stainless Steel
Comparisons