Contents
Titanium vs Stainless Steel: Which is Suitable for Your Project?
- John
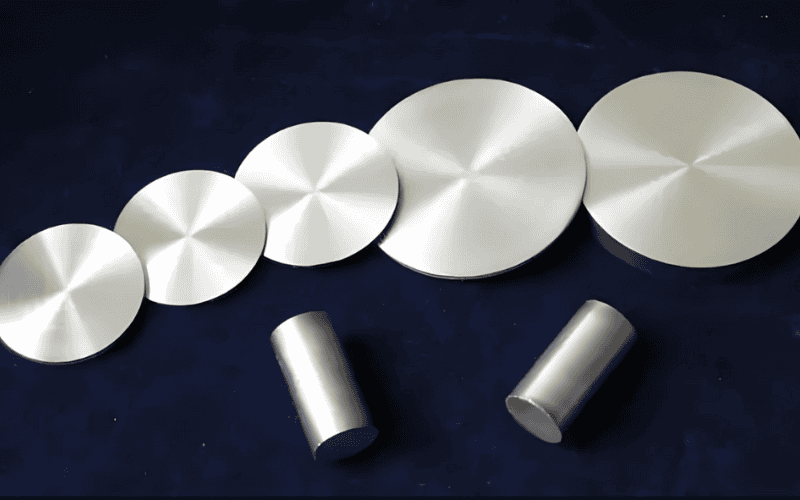
When selecting the ideal material for your project, the discussion between titanium and stainless steel is more than merely a decision between reflective metals. Titanium’s lightweight and strength make it perfect for high-performance applications, while stainless steel’s versatility and affordability make it a go-to for a wide range of uses. Dive into our guide to uncover which metal might be your best fit.
An Overview of Titanium
Titanium, with the chemical symbol Ti, is a low-density, rare transition metal. It is usually silver-white and recognized for its low weight, strong durability, and resistance to corrosion. Titanium is widely used in aerospace, medical implants, and high-performance engineering. It is frequently shaped using techniques like forging, machining, and casting. It is categorized into commercially pure titanium and titanium alloys, each tailored for specific applications and performance needs.
An Overview of Stainless Steel
Stainless steel (inox steel, CRES, or rustless steel) is a corrosion-resistant iron alloy composed of iron, at least 10.5% chromium, and other elements like molybdenum and carbon. The chromium content boosts rust and corrosion resistance, making it durable, easy to clean, and self-healing in oxygen. It’s ideal for construction, automotive parts, medical devices, and kitchenware, with each type suited for specific uses.
The Properties Difference Between Titanium vs Stainless Steel
After reading the overviews of titanium and stainless steel, we’ll find that both metals share many common features. Now, let’s take a closer look at how titanium and stainless steel compare in terms of their general properties to determine which metal excels in various aspects. Please note that titanium here refers to titanium alloys.
Physical Property of Titanium vs Stainless Steel
When contrasting titanium and stainless steel, grasping their physical characteristics is essential. Each of these properties influences their suitability for different applications.
Property | Titanium | Stainless Steel |
Density | 4.51 g/cm³ (0.163 lb/in³) | 7.75 g/cm³ (0.280 lb/in³) |
Melting Point | 1,668 °C (3,034 °F) | 1,370 °C (2,500 °F) |
Boiling Point | 3,287 °C (5,949 °F) | 2,750 °C (4,982 °F) |
Electrical Conductivity | 2.4 × 10⁻⁶ S/m | 1.4 × 10⁻⁶ S/m |
Thermal Conductivity | 21.9 W/(m·K) | 15-25 W/(m·K) |
Coefficient of Thermal Expansion | 8.6 × 10⁻⁶ /K | 16-20 × 10⁻⁶ /K |
Magnetism | Non-magnetic | Generally non-magnetic |
Resistivity | 4.2 × 10⁻⁶ Ω·m | 0.73 × 10⁻⁶ Ω·m |
Specific Heat Capacity | 0.523 J/(g·K) | 0.500 J/(g·K) |
Density
Titanium has a lower density compared to stainless steel. Titanium’s density is around 4.5 g/cm³, while stainless steel typically ranges from 7.75 to 8.1 g/cm³. This renders titanium considerably lighter, which can be beneficial in situations where weight is a vital consideration.
Thermal Conductivity
Titanium possesses less thermal conductivity than stainless steel. Titanium’s thermal conductivity is around 21.9 W/m·K, while stainless steel varies from 15 to 25 W/m·K based on the alloy. This means stainless steel can conduct heat more effectively, making it suitable for heat-exchange applications.
Melting Point
Titanium features a greater melting point compared to stainless steel. Titanium melts at about 1,668°C (3,034°F), while stainless steel melts between 1370°C (2,500°F). This higher melting point allows titanium to perform well in extreme temperatures, where stainless steel might start losing its strength.
Magnetism
Titanium is generally non-magnetic. This makes it suitable for applications where magnetic interference is a concern. In contrast, stainless steel is typically non-magnetic, but some grades, such as 430 ferritic stainless steel, can be magnetic. This difference can affect material selection for various applications.
Chemical Properties of Titanium vs Stainless Steel
Examining the chemical properties of titanium and stainless steel provides insight into their performance in various environments. Let’s explore how these factors compare between the two metals.
Element | Titanium (Ti) | Stainless Steel (SS) |
Titanium (Ti) | 90-99% | / |
Iron (Fe) | / | 0.1-1.0% |
Chromium (Cr) | / | 10.5-30% |
Nickel (Ni) | / | 0-35% |
Molybdenum (Mo) | / | 0-7% |
Aluminum (Al) | 0-6% | / |
Vanadium (V) | 0-5% | / |
Carbon (C) | / | 0.03-1.0% |
Silicon (Si) | / | 0.5-3.0% |
Manganese (Mn) | / | 0-2.0% |
Phosphorus (P) | / | 0-0.045% |
Sulfur (S) | / | 0-0.03% |
Nitrogen (N) | / | 0-0.1% |
Corrosion Resistance
Titanium offers excellent corrosion resistance due to its strong oxide layer that protects against acids and salts. Stainless steel is also resistant but less effective in extreme conditions. To enhance stainless steel’s resistance, using alloys with more chromium and molybdenum can help.
Reactivity
Titanium is highly reactive with oxygen, which forms a protective layer but can be challenging in some settings. Stainless steel is less reactive, making it stable in various chemicals. To address this, protective coatings or selecting specific stainless steel grades can improve performance in reactive environments.
Oxidation Resistance
Titanium resists oxidation well due to its protective oxide layer that forms at high temperatures. Stainless steel resists oxidation too but may degrade over time under extreme conditions. For better performance, high-temperature-resistant grades or protective treatments can be used.
Mechanical Property of Titanium vs Stainless Steel
Comparing the mechanical properties of titanium and stainless steel reveals their strengths and limitations in various applications.
Properties | Titanium | Stainless Steel |
Tensile Strength | 900-1,200 MPa (130-174 ksi) | 480-1,100 MPa (70-160 ksi) |
Yield Strength | 800-1,100 MPa (116-160 ksi) | 240-800 MPa (35-116 ksi) |
Vickers Hardness | 180-400 HV | 150-300 HV |
Brinell Hardness | 250-350 HB | 150-400 HB |
Rockwell Hardness | 30-40 HRC | 20-40 HRC |
Elongation | 10-30% | 30-50% |
Elastic Modulus | 110-120 GPa (16-17.4 Mpsi) | 200-210 GPa (29-30.5 Mpsi) |
Tensile Strength
Titanium has a tensile strength of 900 to 1,200 MPa, making it very strong. Stainless steel ranges from 480 to 1,100 MPa. Some stainless steel grades like 316, 904l can match titanium’s strength, but many do not. This makes titanium a better choice for high-strength applications.
Yield Strength
Titanium’s yield strength is 800 to 1,100 MPa. This means it resists permanent deformation well. Stainless steel has a yield strength of 240 to 800 MPa. In high-stress situations, titanium maintains its shape better than stainless steel.
Hardness
Titanium’s hardness ranges from 300 to 400 HV. This provides good wear resistance. Standard stainless steel has a hardness of 150 to 300 HV, while hardened types can exceed 700 HV. Although titanium usually performs better in wear resistance, some hardened stainless steels such as 440C can be very tough.
Fatigue Resistance
Titanium excels in fatigue resistance, enduring repeated stress effectively. In inert or oxygen-free environments, titanium also maintains strong ductility, making it suitable for various applications. Stainless steel also resists fatigue but may perform worse under high stress. For cyclic loading applications, titanium is often a more reliable choice.
In summary, titanium generally offers higher strength and better resistance to deformation and fatigue than standard stainless steel. However, specific stainless steel grades can also be designed for high performance.
Pros and Cons of Titanium vs Stainless Steel
Assessing the advantages and disadvantages of titanium and stainless steel aids in deciding which material is optimal for your project considering performance, expense, and usage needs.
Pros of Titanium
- Lightweight: Titanium is significantly lighter than stainless steel, perfect for applications sensitive to weight.
- High Strength: It offers a high strength-to-weight ratio, making it both strong and durable.
- Corrosion Resistance: Titanium is exceptionally resistant to corrosion, even in harsh conditions.
- Biocompatibility: Titanium is non-toxic and highly biocompatible, making it an ideal material for medical implants and devices.
- Recyclability: Titanium is highly recyclable, reducing environmental impact.
Cons of Titanium
- Cost: Titanium is costlier than stainless steel, which may be a concern for budget-sensitive projects.
- Machining Difficulty: It is hard to machine and demands specialized equipment and methods.
- Limited Availability: Titanium alloys may not be as readily available as standard stainless steel grades.
- Environmental Impact: The mining and production of titanium can cause considerable environmental effects.
- Softness: Titanium can be relatively soft compared to some stainless steels, making it more prone to scratching.
- Brittleness: Under certain conditions, such as high hydrogen content, titanium may become brittle, affecting its structural integrity.
Pros of Stainless Steel
- Cost-Effective: Stainless steel is generally more affordable than titanium, making it a budget-friendly choice for many applications.
- Versatility: It exists in multiple types and grades, providing a variety of characteristics for diverse applications.
- Good Corrosion Resistance: Though not as resistant as titanium, stainless steel still provides outstanding corrosion protection in most settings.
- Ease of Fabrication: Stainless steel is simpler to machine and weld than titanium, making it more accessible for production.
Cons of Stainless Steel
- Heavier: Stainless steel is notably heavier than titanium, which can be a drawback in weight-critical applications.
- Lower Biocompatibility: While stainless steel is less biocompatible than titanium, some medical-grade stainless steels, like 316L, 304, and 317, are still used for implants.
- Thermal Conductivity: Stainless steel has lower thermal conductivity than many alloys but is better than titanium, making it suitable for some heat-sensitive applications.
- Rust Formation: Stainless steel can develop surface rust, especially in harsh environments, if not properly maintained.
Titanium is lighter, tougher, and more corrosion-resistant but is pricier and more challenging to process. Stainless steel is more affordable, versatile, and easier to fabricate, though it is heavier, has a lower strength-to-weight ratio, and is less biocompatible. Selecting between them relies on aspects such as expense, weight, strength demands, and particular application needs.
Titanium and Stainless Steel Processing Performance Comparison
Casting
Titanium:
- Processing Method: Titanium is typically cast using vacuum or argon-arc melting techniques. The melting temperature is around 1,660 °C (3,020 °F).
- Quality and Effects: Cast titanium generally has good strength but may show porosity.
Stainless Steel:
- Processing Method: Stainless steel is often cast using investment casting or sand casting. The melting temperature ranges from 1,370 to 1,540 °C (2,500 to 2,800 °F).
- Quality and Effects: Stainless steel casting usually results in good surface finishes and structural integrity.
Machining
Titanium:
- Processing Method: Machining titanium requires lower cutting speeds (around 20-40 m/min) and high feed rates due to its toughness.
- Quality and Effects: Machining produces strong components but may lead to increased tool wear.
Stainless Steel:
- Processing Method: Stainless steel machining can be done at higher speeds (up to 100 m/min) depending on the grade.
- Quality and Effects: It offers a smooth finish when processed correctly, maintaining structural properties.
Plastic Working
Titanium:
- Processing Method: Titanium is hot-worked at temperatures between 800 to 1,200 °C (1,470 to 2,190 °F).
- Quality and Effects: Hot working enhances ductility, improving formability.
Stainless Steel:
- Processing Method: Stainless steel can be cold-worked easily at room temperature, with hot working done at 1,100 to 1,200 °C (2,012 to 2,192 °F).
- Quality and Effects: It exhibits good ductility and strength after processing.
Welding
Titanium:
- Processing Method: Titanium is typically welded using gas tungsten arc welding (GTAW) in an inert gas environment.
- Quality and Effects: Proper welding results in strong joints with excellent corrosion resistance.
Stainless Steel:
- Processing Method: Stainless steel can be welded using various methods, including MIG and TIG welding.
- Quality and Effects: It is easier to weld than titanium and achieves reliable joint integrity.
Surface Treatment
Titanium:
- Processing Method: Common treatments include anodizing and sandblasting to enhance surface properties.
- Quality and Effects: Anodizing improves corrosion resistance and aesthetics.
Stainless Steel:
- Processing Method: Surface treatments often involve passivation, polishing, and coating.
- Quality and Effects: These methods enhance resistance to corrosion and improve appearance.
Type of Titanium and Stainless Steel
Various types of both titanium and stainless steel exist, each with distinct properties tailored to particular uses. Evaluating these types will assist in selecting the appropriate material.
Types of Stainless Steel
There are 5 types of stainless steel, each with unique properties.
Austenitic Stainless Steel
Austenitic stainless steel (grades 304 and 316) is non-magnetic and highly corrosion-resistant, commonly used in kitchenware and medical devices.
Ferritic Stainless Steel
Ferritic stainless steel (grades 430 and 409) is magnetic and often used in automotive exhausts and appliances.
Martensitic Stainless Steel
Martensitic stainless steel (grades 410 and 420) has high hardness but lower corrosion resistance, making it suitable for knives and turbine blades.
Duplex Stainless Steel
Duplex stainless steel (grades 2205 and 2507) merges strength with corrosion resistance, making it perfect for chemical facilities and marine environments.
Precipitation-Hardening Stainless Steel
Precipitation-hardening stainless steel (grades 17-4 PH and 15-5 PH) combines high strength and excellent corrosion resistance, often used in aerospace, chemical, and military applications.
Types of Titanium
Titanium comes in two main types: commercially pure titanium and titanium alloys. Each type has specific properties and uses.
Commercially Pure Titanium
Commercially pure titanium is highly corrosion-resistant and has excellent biocompatibility. It is extensively employed in medical implants, aerospace parts, and chemical production. Common grades include Grade 1, Grade 2, Grade 3, and Grade 4, each offering varying levels of strength and ductility.
Titanium Alloys
Titanium alloys are combined with elements such as aluminum, vanadium, and molybdenum to improve strength and functionality. These alloys are applied in the aerospace, defense, and industrial sectors. Popular types include:
- Alpha Alloys: Includes aluminum and provides strong weldability and corrosion protection. Frequently utilized in aerospace uses.
- Beta Alloys: Contains elements like vanadium and are known for high strength and toughness. Used in high-stress components like aircraft parts.
- Alpha-Beta Alloys: Combine properties of both alpha and beta alloys, providing a balance of strength, ductility, and corrosion resistance. Examples include Ti-6Al-4V, widely used in aerospace and medical devices.
Titanium and stainless steel each offer distinct types tailored to different needs. Titanium’s alloys excel in extreme environments and specific applications, and stainless steel’s diverse types provide versatility for a wide range of industrial and commercial uses.
Grades of Titanium and Stainless Steel
Both titanium and stainless steel come in specific grades, each with unique properties suited for different applications and performance requirements.
Grades of Titanium
Titanium classifications are split into commercially pure titanium and titanium alloys. Commercially pure titanium (Grades 1 to 3) offers great corrosion resistance and ductility but lower strength. Titanium alloys (Grades 5, 6, and 9) are enhanced with elements to provide higher strength and performance for demanding uses.
Sub-Classification | Grade | Description |
Commercially Pure Titanium | Grade 1 | Unalloyed titanium with excellent ductility and corrosion protection. Applied in chemical production and medical implants. |
Grade 2 | Somewhat stronger than Grade 1, with comparable corrosion protection. Common in aerospace and marine applications. | |
Grade 3 | Higher strength and ductility compared to Grades 1 and 2. Employed in situations needing medium strength and corrosion protection. | |
Titanium Alloy (Alpha-Beta) | Grade 5 | Known as Ti-6Al-4V, this alloy offers high strength and good fatigue resistance. Used in aerospace components and medical devices. |
Grade 9 | Known as Ti-3Al-2.5V, it provides a balance of strength and formability. Used in aircraft frames and high-performance automotive parts. | |
Grade 6 | Known as Ti-5Al-2.5Sn, it has high strength and good corrosion resistance. Often used in aerospace and marine environments. |
Grades of Stainless Steel
Stainless steel grades, like titanium, are categorized into four types based on their specific alloying elements and properties.
Classification | Grade | Description |
Austenitic | 304 | Versatile and widely used with excellent corrosion resistance and good formability. Typical in cookware and medical instruments. |
316 | Provides exceptional corrosion protection, particularly in marine settings. Common in chemical processing and medical implants. | |
310 | High-temperature resistant with good oxidation resistance. Used in furnace parts and high-temperature equipment. | |
Ferritic | 430 | Moderate corrosion resistance with good formability. Frequently applied in automotive and kitchen uses. |
409 | Provides good resistance to exhaust gases. Common in automotive exhaust systems. | |
439 | Enhanced corrosion resistance and heat resistance. Used in automotive and industrial applications. | |
Martensitic | 410 | High hardness and strength, with moderate corrosion resistance. Used in cutlery and industrial equipment. |
420 | Higher hardness than Grade 410, suitable for cutting tools and surgical instruments. | |
440C | Very high hardness and wear resistance. Used in high-quality knives and bearings. | |
Duplex | 2205 | Strong and superb corrosion protection, perfect for chemical production and marine conditions. |
2507 | Exceptional strength and defense against pitting and crevice corrosion. Used in oil and gas industries and seawater applications. | |
2304 | Good strength and resistance to stress corrosion cracking. Used in industrial and chemical processing applications. |
You can compare the detailed information of these grades to find the best one for your project. Currently, stainless steel is generally easier to obtain than titanium.
Applications of Stainless Steel vs Titanium
Stainless steel and titanium are utilized in various industries, each with distinct advantages. While both are corrosion-resistant, their differences make them suited for different applications. Understanding these uses will help you choose the right material.
Applications of Titanium
- Aerospace: Aircraft parts, rocket components, and space vehicles because of their strength-to-weight ratio and resistance to corrosion.
- Medical Devices: Implants, prosthetics, and surgical tools because of their biocompatibility and resistance to corrosion.
- Marine: Vessel parts, underwater apparatus, and offshore structures due to its outstanding resistance to seawater corrosion.
- Sports Equipment: High-performance bicycles, golf clubs, and tennis rackets, leveraging its lightweight and strength properties.
- Chemical Processing: Containers, pipelines, and reactors for its resistance to aggressive chemicals and elevated temperatures.
Applications of Stainless Steel
- Construction: Building frames, handrails, and roofing materials for its durability and corrosion resistance.
- Automotive: Exhaust systems, engine parts, and structural components because of their durability and resistance to high temperatures.
- Kitchenware: Utensils, pots, and sinks due to their easy-to-clean surfaces and rust resistance.
- Medical Instruments: Surgical tools, sterilization equipment, and diagnostic devices for its cleanliness and resistance to corrosion.
- Industrial Equipment: Pumps, valves, and machinery components due to its strength, resistance to wear, and ability to handle various chemicals.
Titanium excels in aerospace, medical devices, and marine environments. Stainless steel is extensively utilized in building, automotive components, kitchen tools, and medical devices. Select the material that most suits your project’s particular needs.
How to Identify Whether a Metal is Titanium or Stainless Steel?
Titanium and stainless steel can be hard to distinguish, not just by color but in other ways too. We provide a step-by-step guide, from easy to more detailed methods, to help you tell them apart.
- Weight Test: Titanium has a lower density and is about 25% lighter than stainless steel.
- Color and Finish: Although titanium is also a silver-colored metal, it generally has a darker hue and a more matte finish compared to stainless steel.
- Magnet Test: Titanium is never magnetic, while some stainless steel grades, such as ferritic stainless steel, can be magnetic.
- Corrosion Resistance Test: Titanium typically provides exceptional corrosion resistance, particularly in harsh environments.
- Spark Test: Titanium produces long, bright white sparks when ground, whereas stainless steel generates dull orange sparks that are less intense.
Which is Better, Titanium or Stainless Steel?
It depends on the application. Titanium is more lightweight, has greater corrosion resistance, and is stronger than stainless steel, making it suitable for aerospace and medical devices. Stainless steel is less expensive, simpler to machine, and appropriate for various applications such as construction and kitchenware.
What Lasts Longer, Stainless Steel or Titanium?
Titanium generally lasts longer in harsh environments due to its superior corrosion resistance. However, the longevity of both materials depends on the specific conditions and uses.
Does titanium scratch more than stainless steel?
Titanium is typically more resistant to scratches than stainless steel, though it may reveal scratches more clearly because of its darker finish.
Does Titanium Rust?
No, titanium does not corrode. It is highly resistant to oxidation, even in harsh conditions.
Does Titanium Fade?
Titanium does not fade easily. Its color can remain stable over time, though surface treatments might alter its appearance.
Is Titanium Stronger Than Steel?
Yes, titanium is stronger than steel in terms of strength-to-weight ratio. It’s lighter yet has comparable strength, making it ideal for aerospace and military applications. However, steel is often more cost-effective and easier to work with.
Which Metal Is Right for Your Project?
Choosing the right metal for your project depends on specific needs like strength, weight, corrosion resistance, and budget. Titanium excels in extreme conditions and lightweight applications, and it is suitable for the aerospace, medical, and marine sectors. Stainless steel offers versatility and cost-effectiveness for construction, automotive, and kitchenware.
To guarantee you choose the optimal material for your project, seek advice from specialists. SteelPRO Group, a top professional steel provider, is available to offer expert guidance and premium solutions customized to your project’s needs. Contact us now for a quote that will satisfy you.
- Stainless Steel Grades
- 300 Series Stainless Steel
- 303 Stainless Steel
- 304 Stainless Steel
- 305 Stainless Steel
- 308 Stainless Steel
- 316 Stainless Steel
- 316N Stainless Steel
- 409 Stainless Steel
- 410 Stainless Steel
- 416 Stainless Steel
- 420 Stainless Steel
- 430 Stainless Steel
- 410HT And 410L Stainless Steels
- 410S Stainless Steel
- 440 Stainless Steel
- 436 Stainless Steel
- 301 Stainless Steel
- 201 Stainless Steel
- 202 Stainless Steel
- 444 Stainless Steel
- 405 Stainless Steel
- 302 Stainless Steel
- 309 Stainless Steel
- 314 Stainless Steel
- 321 Stainless Steel
- 347 Stainless Steel
- 408 Stainless Steel
- 422 Stainless Steel
- 431 Stainless Steel
- 434 Stainless Steel
- 414 Stainless Steel
- 430FR Stainless Steel
- 13-8 PH Stainless Steel
- 317 | 317L Stainless Steel
- 616 Stainless Steel
- 630 Stainless Steel
- 904L Stainless Steel
- A2 Stainless Steel
- 304 vs 304L Stainless Steel
- 304 VS 316 Stainless Steel
- 304 vs 409 Stainless Steel
- 304 vs 430 Stainless Steel
- 410 Stainless Steel vs 304
- 18/0 vs 18/10
- 18/0 Stainless Steel
- 18/8 Stainless Steel
- 18/10 Stainless Steel
Comparisons