Contents
414 Stainless Steel: Definition, Properties, and Applications
- John
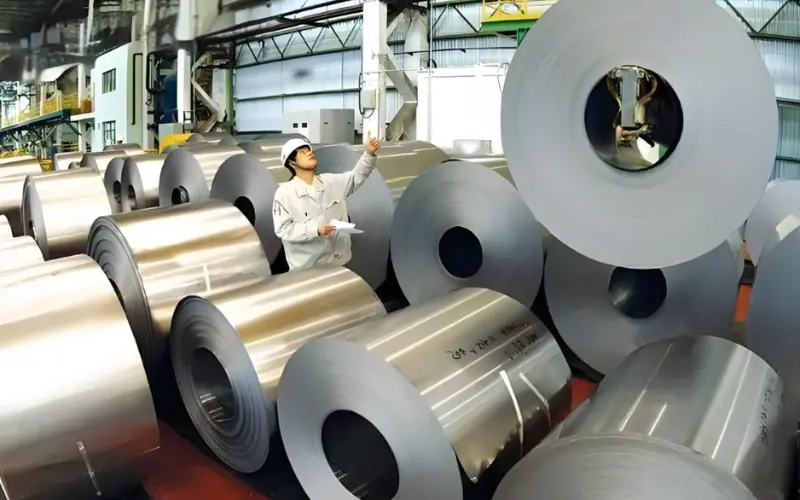
414 stainless steel is a high-strength alloy with excellent wear resistance and moderate corrosion protection. This article explains its composition, key properties, and applications in industries that require durability, such as aerospace and heavy machinery.
What Is 414 Stainless Steel?
414 stainless steel, also called UNS S41400, is composed of approximately 88% iron, along with 12% chromium. It is a higher-strength variant of 410 stainless steel. As a martensitic grade, it offers excellent hardness and toughness. It is used for demanding applications like aerospace, heavy machinery, and manufacturing.
414 Stainless Steel Equivalents
Country/Region | Standard/Specification | Grade |
Europe | WNR | 1.4008 |
USA | UNS | S41400 |
USA | AISI | 414 |
The Chemical Composition of 414 Stainless Steel
Element | Fe | C | Cr | Mn | Si | S | P | Ni |
wt% | Balance | 0.15% max | 11.5-13.5% | 1.00% max | 1.00% max | 0.030% max | 0.040% max | 0.60% max |
The Physics Properties of 414 Stainless Steel
Property | Value (Metric) | Value (Imperial) |
Density | 7.70 g/cm³ | 0.278 lb/in³ |
Melting Point | 1440°C – 1510°C | 2624°F – 2750°F |
Thermal Conductivity | 24.9 W/m·K at 100°C | 172.5 BTU in/hr·ft²·°F |
Thermal Expansion | 11.1 µm/m·°C at 20°C | 6.2 µin/in·°F |
Electrical Conductivity | 1.3% IACS | 1.3% IACS |
Magnetic Properties | Ferromagnetic | Ferromagnetic |
The Mechanical Properties of 414 Stainless Steel
Property | Value (Metric) | Value (Imperial) |
Tensile Strength | 655-860 MPa | 95,000-125,000 psi |
Yield Strength | 415 MPa | 60,000 psi |
Brinell Hardness | 197-223 | 197-223 |
Hardness, Rockwell C (before testing) | 48 | 48 |
Rockwell Hardness (converted from Rockwell C hardness) | 459 | 459 |
Vickers Hardness (converted from Rockwell C hardness) | 487 | 487 |
Elongation | 15% | 15% |
Elastic Modulus | 200 GPa | 29,000 ksi |
The Different Forms of 414 Stainless Steel
414 stainless steel is available in various forms, which allows for versatility in different industrial applications. Here are the most common forms of 414 stainless steel:
Bars and Rods
Used extensively in machinery and structural applications, 414 stainless steel bars are available in round, flat, and hexagonal shapes. They are ideal for components like shafts, gears, and fasteners because of their machinability and strength.
Sheets and Plates
Flat products such as sheets and plates are used in environments where strength and resistance to wear are essential, including in the aerospace and heavy equipment sectors.
Tubes and Pipes
414 stainless steel is also available in tubular forms, which are utilized in mechanical systems that require strength under pressure, such as pipelines, heat exchangers, and structural supports.
Wire
414 SS wire is often used in applications where strong, flexible material is needed, like springs and fasteners.
Forged Components
Forgings are used in applications that include valve components, pump shafts, and other heavy-duty industrial components. Forged 414 stainless steel provides superior toughness.
The Applications of 414 Stainless Steel
414 stainless steel is used in various applications where a combination of strength, hardness, and moderate corrosion resistance is needed. Here are some common uses:
Aerospace Components
414 stainless steel is used in aircraft parts such as gears, shafts, and fasteners due to its high strength and toughness, even in harsh environments.
Pump and Valve Components
It is ideal for making parts like pump shafts, valve stems, and other components that require durability and wear resistance, especially in machinery.
Heavy Machinery
414 stainless steel is commonly used in heavy-duty equipment such as industrial gears and machinery components, where high strength and wear resistance are critical.
Automotive Parts
In the automotive industry, 414 stainless steel is often used for components such as crankshafts, transmission gears, and other high-stress parts that require strength and durability.
The Advantages of 414 Stainless Steel
High Strength and Hardness
- Heat Treatable: It can be heat treated, allowing for high strength and hardness levels suitable for demanding applications.
- Wear Resistance: The material’s hardness provides excellent wear resistance, making it suitable for parts subject to wear.
Improved Corrosion Resistance
- Molybdenum Addition: The inclusion of molybdenum enhances its corrosion resistance compared to standard martensitic stainless steels like 410.
- Resistance to Mild Corrosive Environments: Offers better performance in environments exposed to water, steam, and mild chemicals.
Good Machinability
- Machining: When annealed, 414 stainless steel exhibits good machinability, facilitating the manufacturing of complex parts.
- Surface Finish: 414 stainless steel can achieve a high-quality surface finish. This is beneficial for both functional components and aesthetic applications.
Versatility
- Application Range: Suitable for making shafts, valves, gears, and other mechanical components requiring a combination of strength and corrosion resistance.
- Formability: This can be forged and formed with appropriate processes, adding to its versatility in fabrication.
The Disadvantages of 414 Stainless Steel
Limited Corrosion Resistance
- Although 414 stainless steel has improved corrosion resistance compared to some martensitic steels due to its molybdenum content, it is still less resistant than austenitic stainless steels like 304 or 316.
- In environments containing chlorides or other corrosive agents, pitting and crevice corrosion are prone to occur.
Poor Weldability
- Cracking Risks: The high carbon content increases the risk of cracking in the heat-affected zone during welding.
- Need for Preheating and Post-Weld Heat Treatment: Welding requires careful control, including preheating to 200°C – 300°C and post-weld annealing, which adds complexity and cost.
Reduced Toughness and Ductility
- Brittleness: The material can be brittle, especially in the hardened condition, making it less suitable for applications requiring high toughness.
- Low Impact Resistance: Not ideal for applications subjected to sudden or impact loads.
Difficulty in Machining After Hardening
- Hardness Issues: Once heat-treated for maximum hardness, machining becomes difficult, requiring specialized tools and techniques.
- Increased Tool Wear: The hard material accelerates wear on cutting tools, increasing tooling costs.
Limited Formability
- Poor Cold Forming Capabilities: Due to its high strength and low ductility, cold forming is challenging and may lead to cracking.
- Requires Hot Working: Often needs to be formed at elevated temperatures, which complicates the manufacturing process.
Not Suitable for High-Temperature Applications
- Scaling and Oxidation: At elevated temperatures, 414 stainless steel may suffer from scaling and oxidation.
- Loss of Mechanical Properties: Prolonged exposure to high temperatures can degrade its strength and hardness.
Heat Treatment
Annealing
- The steel is heated to 820°C – 900°C (1500°F – 1650°F) and then slowly cooled to relieve internal stresses.
- Annealing is done to increase ductility and improve machinability by reducing hardness.
Hardening
- Heat the steel to 980°C – 1020°C (1800°F – 1870°F) and then rapidly cool (quenched) it in oil or air.
- Hardening increases the steel’s wear resistance and overall strength. This makes it ideal for high-stress applications like gears and shafts.
Tempering
- The material is reheated to a lower temperature, typically between 150°C – 600°C (300°F – 1110°F). The temperature range is selected by the required balance of hardness and toughness.
- Tempering reduces the brittleness caused by quenching while retaining enough hardness for durability. It also improves the steel’s impact resistance and overall toughness.
Stress Relieving
- The steel may undergo stress relieving, a process where it is heated to 540°C – 650°C (1000°F – 1200°F).
- Stress relieving reduces the risk of warping or cracking during use, especially in high-stress environments.
Sub-Critical Annealing
- This process involves heating the steel to around 650°C – 760°C (1200°F – 1400°F), which is below its critical temperature range.
- Sub-critical annealing relieves stresses and improves ductility without altering the overall mechanical properties significantly.
Normalizing
- Heat the steel to about 900°C – 950°C (1650°F – 1750°F) and then allow it to cool in the air.
- This optional treatment improves both toughness and uniformity in the steel’s microstructure, making it more suitable for further machining and processing.
Other Processing Methods of 414 Stainless Steel
Forging Process
- Before forging, the material is heated to temperatures between 1150°C and 1200°C.
- During forging, the temperature must not drop below 950°C to avoid work hardening and cracks.
- After forging, air cooling is typically used, but post-forging annealing is recommended to reduce internal stresses.
Machining
- Because of its high hardness, 414 is difficult to machine. High-strength cutting tools like carbide are recommended, with slower cutting speeds and lower feed rates.
- Proper grinding tools and cooling fluids are required to avoid overheating and surface burning during these processes.
Cold and Hot Forming
- Cold Forming: Due to its high hardness, cold forming is difficult. Intermediate annealing may be needed to prevent excessive hardening.
- Hot Forming: Hot forming is done between 950°C and 1200°C, which improves plasticity and reduces the risk of cracking.
Welding
- 414 stainless steel is prone to cracking during welding.
- Preheating to 200°C to 300°C before welding and performing post-weld annealing helps to alleviate welding stresses.
- Manual arc welding or tungsten inert gas (TIG) welding are preferred for this material.
What Are the Differences Between 414 And 304?
414 stainless steel has better strength and hardness. It is used in wear-resistant applications like gears and valves. 304 stainless steel has excellent corrosion resistance. It is used in food processing and chemical applications.
What Are the Differences Between 414 And 416?
414 stainless steel is stronger and more wear-resistant. 416 stainless steel is easier to machine. It has slightly lower corrosion resistance.
How Does 414 Stainless Steel Perform in High-Temperature Environments?
414 stainless steel performs well in moderate high-temperature environments, but its strength decreases beyond 600°C (1110°F), limiting its use in extreme heat applications.
Summary
414 stainless steel, also known as UNS S41400. Its primary advantages include good wear resistance and heat treatability. Its high strength makes it ideal for demanding applications.
At Steel Pro Group, we are committed to providing top-quality materials for high-performance industrial needs. If you are looking for reliable solutions for your projects, please visit our website or contact us for a personalized consultation and quote.
- Stainless Steel Grades
- 300 Series Stainless Steel
- 303 Stainless Steel
- 304 Stainless Steel
- 305 Stainless Steel
- 308 Stainless Steel
- 316 Stainless Steel
- 316N Stainless Steel
- 409 Stainless Steel
- 410 Stainless Steel
- 416 Stainless Steel
- 420 Stainless Steel
- 430 Stainless Steel
- 410HT And 410L Stainless Steels
- 410S Stainless Steel
- 440 Stainless Steel
- 436 Stainless Steel
- 301 Stainless Steel
- 201 Stainless Steel
- 202 Stainless Steel
- 444 Stainless Steel
- 405 Stainless Steel
- 302 Stainless Steel
- 309 Stainless Steel
- 314 Stainless Steel
- 321 Stainless Steel
- 347 Stainless Steel
- 408 Stainless Steel
- 422 Stainless Steel
- 431 Stainless Steel
- 434 Stainless Steel
- 414 Stainless Steel
- 430FR Stainless Steel
- 13-8 PH Stainless Steel
- 317 | 317L Stainless Steel
- 616 Stainless Steel
- 630 Stainless Steel
- 904L Stainless Steel
- A2 Stainless Steel
- 304 vs 304L Stainless Steel
- 304 VS 316 Stainless Steel
- 304 vs 409 Stainless Steel
- 304 vs 430 Stainless Steel
- 410 Stainless Steel vs 304
- 18/0 vs 18/10
- 18/0 Stainless Steel
- 18/8 Stainless Steel
- 18/10 Stainless Steel
Comparisons