Surface Finish
SteelPRO Group offers seven or more steel surface treatment methods to enhance durability, improve corrosion resistance, and achieve the perfect finish for every project. From polishing and brushing to electroplating, we deliver tailored solutions for all steel types.
1. Polishing
- Process Effect: For carbon steel, polishing improves smoothness but requires protective coatings for corrosion resistance. For alloy steel, it enhances surface uniformity, with passivation or coating recommended for corrosion-prone alloys. For stainless steel, it creates a smooth, reflective surface ideal for aesthetics and industrial use.
- Shapes: Flat sheets, tubes, rods, bars, structural sections, plates, complex curved surfaces, angles.
- Number: No. 3, No. 4, 1G, 2G, 4G
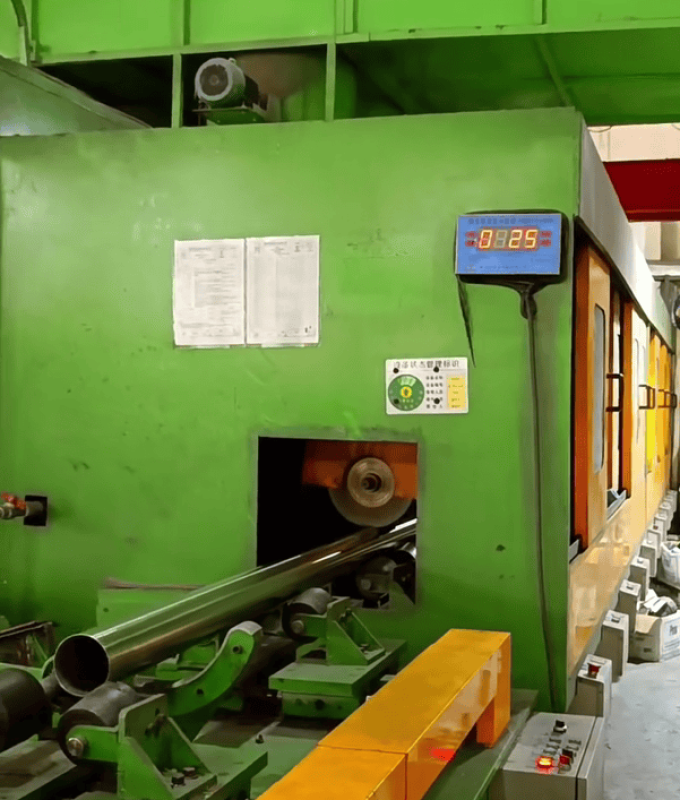
2. Brushing
- Process Effect: Carbon steel gets a textured finish but needs protective coatings to prevent rust. Alloy steel gains a satin finish for decorative purposes. Stainless steel results in a matte finish suitable for both decorative and industrial use.
- Shapes: Flat sheets, plates, pipes, tubes, rods, bars, square tubing, structural shapes, curved surfaces.
- Number: No. 4, No. 5, No. 6, 1J, 2J
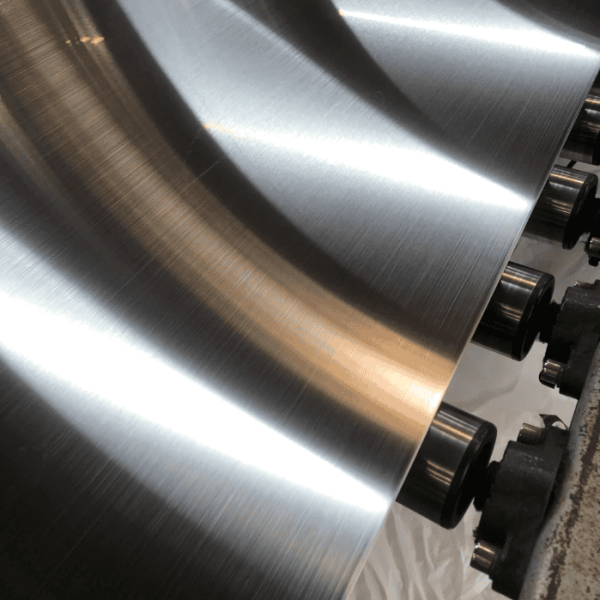
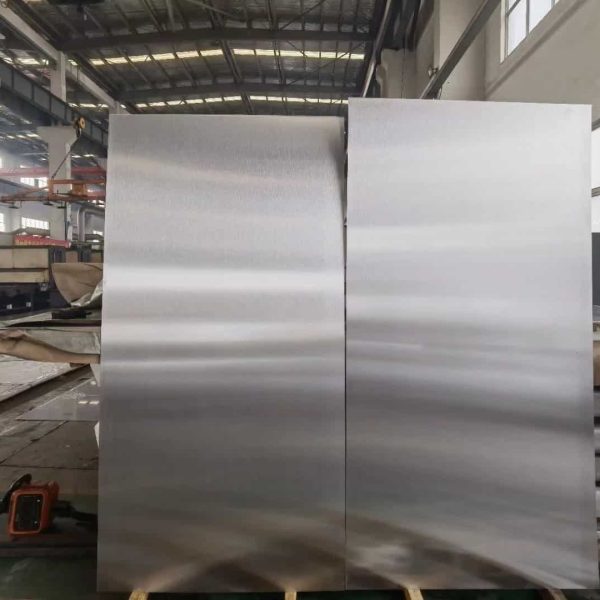
3. Passivation
- Process Effect: Carbon steel is not suitable for passivation, and electroplating or coating is recommended. Alloy steel can benefit from passivation, improving corrosion resistance. Stainless steel passivation removes contaminants and enhances corrosion resistance.
- Shapes: Pipes, tubes, fittings, fasteners, complex shapes, sheets, rods, bars.
- Number: No. 2B, No. 2D, 2B1, 2B2, 2G
4. Pickling
- Process Effect: Carbon steel needs protective coatings post-pickling to prevent corrosion. Alloy steel removes oxides and may require passivation for protection. Stainless steel restores its corrosion-resistant layer, improving durability.
- Shapes: Pipes, tubes, sheets, plates, coils, structural sections, bars, rods, fittings.
- Number: No. 1, No. 2B, No. 1D, 2F, 1G
5. Mirror Finish
- Process Effect: Carbon steel requires a protective coating after achieving a mirror finish. Alloy steel benefits from the reflective finish but needs corrosion protection. Stainless steel achieves a high-gloss finish, ideal for decorative and functional applications.
- Shapes: Flat sheets, tubes, rods, bars, plates, architectural elements, complex surfaces, decorative pieces.
- Number: No. 8, SB, 2P, 2R, 3R
6. Etching
- Process Effect: Carbon steel needs protection after etching to avoid corrosion. Alloy steel can be etched for both functional and decorative purposes, with post-etching treatments needed. Stainless steel maintains its corrosion resistance while allowing custom designs.
- Shapes: Sheets, plates, flat surfaces, tubes, rods, panels, architectural elements.
- Number: No. 5, No. 2K, 2E, 2R, 4G
7. Electroplating
- Process Effect: Carbon steel benefits from electroplating to enhance corrosion resistance. Alloy steel improves durability in harsh environments. Stainless steel typically does not require electroplating but can be used for specific purposes.
- Shapes: Small parts, fasteners, tubes, rods, plates, bars, structural shapes, sheets, fittings, intricate components.
- Number: No. 2B, No. 2D, 2F, 3A, 3B
Why Choose Us for Surface Finishing:
- Variety of Methods
We provide polishing, brushing, passivation, pickling, and more. - Custom Solutions
Tailored finishes for carbon, alloy, and stainless steel. - Advanced Equipment
High-quality, precise results for all shapes and surfaces. - Quality Assurance
Strict standards ensure durable, reliable finishes.
We also provide Coating, Mill, and custom surface treatment services.
FAQ
1. What's the best way to polish steel?
The best way to polish steel is using mechanical abrasives followed by buffing with fine compounds, ensuring smoothness and a reflective finish. For corrosion resistance, apply a protective coating afterward.
2. What is the process of brushed metal?
Brushed metal is created by using abrasive belts or pads to produce a uniform, linear texture. This process results in a matte, satin-like finish often used for decorative purposes.
3. How to passivate steel?
Passivation involves cleaning the steel’s surface with an acid solution, like nitric or citric acid, to remove contaminants and promote the formation of a corrosion-resistant oxide layer, especially on stainless steel.
4. What is an alternative to pickling stainless steel?
An alternative to pickling is mechanical cleaning (abrasive blasting or grinding) or using an acid-free solution such as citric acid for removing oxides and restoring the surface.
5. What is the difference between matte finish and mirror finish?
A matte finish is non-reflective with a smooth, dull texture, while a mirror finish is highly reflective and glossy, offering a more polished and shiny appearance.
6. What is the best way to etch metal?
The best way to etch metal is using an acid or chemical solution like ferric chloride or nitric acid, depending on the material, to create detailed patterns or designs.
7. Which metal cannot be electroplated?
Some non-conductive materials, such as plastics or ceramics, cannot be electroplated without a conductive coating. Pure metals like aluminum can also be challenging without pretreatment.
8. How durable are your post-treatment options?
Our post-treatment options, including coatings, passivation, and electroplating, offer high durability and extended corrosion resistance, designed to withstand demanding environments and ensure longevity.