Contents
410 Stainless Steel vs 304: Properties, Treatment Processes, Application
- John
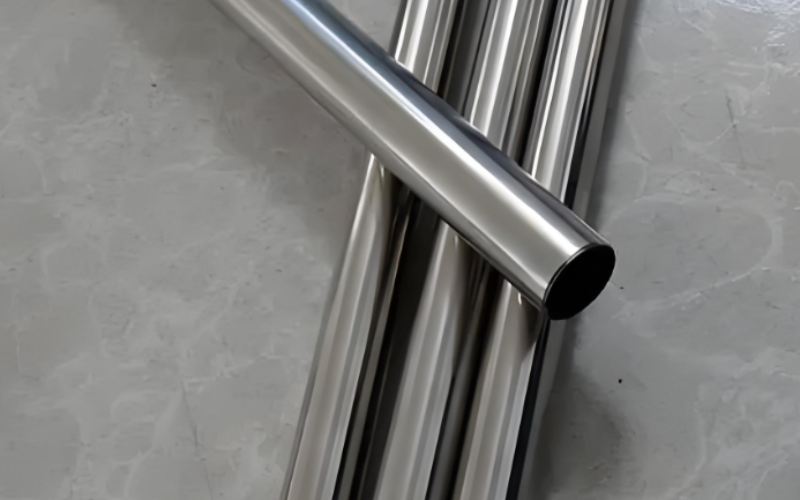
As one of the popular grades of stainless steel, 410 and 304 are often compared. 410 is recognized for its elevated toughness and durability, whereas 304 possesses excellent resistance to corrosion.
The difference between the two grades is relatively large, our blog will be in the meaning of 410 and 304, characteristics, processing, applications described in detail, no matter which industry you are in, you can easily choose the grade you need.
What is 410 Stainless Steel?
410 stainless steel is a martensitic alloy noted for its elevated hardness and moderate resistance to corrosion. It generally includes 11.5-13.5% chromium and is utilized in scenarios that demand elevated strength and resistance to wear. 410 stainless steel is commonly used in cutlery, automotive parts, and other high-strength applications.
What is 304 Stainless Steel?
304 stainless steel is an austenitic metal, often referred to as “18/8” stainless steel due to its 18% chromium and 8% nickel content. It possesses exceptional durability and resistance to corrosion, making it extensively employed in both household and industrial uses. 304 stainless steel, which meets food safety standards, is also commonly used in food processing equipment.
Click here to learn more about 304 stainless steel!
410 Stainless Steel vs 304: Properties
410 stainless steel is known for its high hardness and strength, and 304 stainless steel offers excellent corrosion resistance and strength, thanks to its chromium and nickel content.
In this section, we will compare the chemical, physical, and mechanical properties of 410 and 304 stainless steel for you. These distinct properties define their suitability for different environments and uses.
Chemical Properties of 410 vs 304 stainless steel
Compared to 410, 304 stainless steel has more chromium and nickel, offering better corrosion resistance. Both alloys have low carbon, but 410 has more, giving it higher strength and hardness.
Element | 304 Stainless Steel (%) | 410 Stainless Steel (%) |
Carbon (C) | 0.08 max | 0.15 max |
Manganese (Mn) | 2.00 max | 1.00 max |
Phosphorus (P) | 0.045 max | 0.04 max |
Sulfur (S) | 0.03 max | 0.03 max |
Silicon (Si) | 0.75 max | 1.00 max |
Chromium (Cr) | 18.0-20.0 | 11.5-13.5 |
Nickel (Ni) | 8.0-10.5 | 0.75 max |
Nitrogen (N) | 0.10 max | Not specified |
Molybdenum (Mo) | 0-0.10 | Not specified |
Corrosion Resistance
304 stainless steel provides enhanced corrosion resistance due to its higher chromium and nickel levels, making it ideal for demanding environments like food processing, chemical handling, and marine applications.
In contrast, 410 stainless steel, with lower chromium and minimal nickel, offers moderate corrosion resistance, performing well in dry or low-corrosion settings but being less effective in highly corrosive or chloride-rich environments. However, 410 is more cost-effective than 304.
Physical Properties of 410 vs 304 stainless steel
The most notable physical differences between 410 and 304 stainless steel are their thermal conductivity and magnetic properties. 410 has higher thermal conductivity and is magnetic, while 304 has lower thermal conductivity and is non-magnetic.
Property | 304 Stainless Steel | 410 Stainless Steel |
Density | 8.00 g/cm³ | 7.75 g/cm³ |
Melting Point | 1400-1450°C | 1480-1530°C |
Thermal Conductivity | 16.2 W/m·K | 24.9 W/m·K |
Thermal Expansion Coefficient | 17.2 µm/m·°C | 10.2 µm/m·°C |
Specific Heat Capacity | 500 J/kg·K | 460 J/kg·K |
Thermal Diffusivity | 4.2 mm²/s | 7.3 mm²/s |
Elastic Modulus | 193 GPa | 200 GPa |
Electrical Resistivity | 0.72 µΩ·m | 0.57 µΩ·m |
Magnetic | Non-magnetic | Magnetic |
Density
304 stainless steel is slightly denser than 410 stainless steel. This difference in density affects the overall weight of materials made from these steels, with 304 being marginally heavier.
Melting Point
410 stainless steel has a higher melting point compared to 304. This makes 410 more suitable for applications involving higher temperatures, where melting or deformation could be a concern.
Thermal Conductivity
410 stainless steel conducts heat better than 304. This makes 410 more efficient in heat transfer applications, whereas 304 is less effective in such environments.
Thermal Expansion Coefficient
304 stainless steel expands more when heated than 410. This means that 304 is more likely to change in size with temperature changes, which may need to be considered in design applications.
Specific Heat Capacity
304 stainless steel can absorb slightly more heat before increasing in temperature compared to 410. This characteristic renders 304 more efficient in scenarios where thermal stability is crucial.
Thermal Diffusivity
410 stainless steel diffuses heat faster than 304. This higher diffusivity makes 410 better for applications requiring quick heat dissipation.
Elastic Modulus
410 stainless steel is slightly stiffer than 304, indicating that it is less likely to deform under stress. This makes 410 more suitable for applications where rigidity is critical.
Electrical Resistivity
304 stainless steel has higher electrical resistivity compared to 410. This implies 304 is less conductive and might be favored in situations where electrical conductivity needs to be reduced.
Magnetic
304 stainless steel is non-magnetic, while 410 is magnetic. This difference is crucial in applications where magnetic properties are important, such as in electrical or magnetic-sensitive environments.
In summary, 410 stainless steel has a higher melting point, better thermal conductivity, and greater hardness than 304. On the other hand, 304 has a lower density, higher specific heat capacity, and is non-magnetic. These traits determine their best applications based on thermal and magnetic needs.
Mechanical Properties of 410 vs 304 stainless steel
Mechanical properties refer to how stainless steel performs under external forces. These traits are vital indicators of how the material will perform in real-world applications. Presented below is a comparison of the mechanical traits of 410 and 304.
Property | 304 Stainless Steel | 410 Stainless Steel |
Tensile Strength | 515-750 MPa (74.7-108.8 ksi) | 450-700 MPa (65.3-101.5 ksi) |
Yield Strength | 205 MPa (29.7 ksi) | 275 MPa (40 ksi) |
Vickers Hardness | 129 HV | 183 HV |
Brinell Hardness | 123 HB | 173 HB |
Rockwell Hardness | B70-B90 | C35-C40 |
Elongation | 40% | 20% |
In addition to this, there are the following differences in the mechanical properties of 410 and 304.
Strength
410 stainless steel is stronger and harder due to its martensitic structure and higher carbon content. 304 stainless steel is weaker but offers better overall toughness.
Toughness
304 stainless steel is tougher and can absorb more energy before breaking. This makes it better for applications requiring impact resistance.
Ductility
304 stainless steel is more malleable and can be formed more readily without fracturing. 410 stainless steel is less ductile and may become brittle.
Hardness
410 stainless steel is tougher and more resistant to abrasion. 304 stainless steel is softer and more prone to wear and deformation.
Impact Resistance
304 stainless steel has better impact resistance and can handle sudden impacts without cracking. 410 stainless steel may crack under high-impact loads due to its brittleness.
Fatigue Resistance
304 stainless steel resists fatigue better, making it suitable for applications with repeated stress. 410 stainless steel has lower fatigue resistance and may fail under cyclic stress.
Thermal Stability
410 stainless steel maintains its strength and hardness better at high temperatures. 304 stainless steel is more stable under varying temperatures because of its austenitic composition.
Weldability
304 stainless steel is easier to weld due to its lower carbon and higher nickel content, which reduces the risk of cracking. In comparison, 410 stainless steel is more challenging to weld because its higher carbon content can lead to cracking, often requiring post-weld treatment.
Wear Resistance
410 stainless steel excels in wear resistance due to its higher carbon content and martensitic structure, making it suitable for abrasive environments. 304 stainless steel, while durable, has lower wear resistance, making it less ideal for applications where abrasion is a major concern.
In summary, 410 stainless steel offers higher strength and hardness, while 304 stainless steel provides better toughness, ductility, and impact resistance. The selection relies on the particular mechanical requirements of the application.
Corrosion Resistance Comparison of 410 and 304 Stainless Steel
410 and 304 stainless steel offer different corrosion resistance based on their environment.
410 Stainless Steel Corrosion Resistance
410 resists corrosion in mild environments, dry air, and clean water. However, it is prone to pitting and crevice corrosion in humid or chloride-rich environments, leading to rust.
304 Stainless Steel Corrosion Resistance
304 offers better corrosion resistance in most environments, including freshwater and marine conditions. It is generally resistant to pitting and crevice corrosion, though high chloride levels can still cause issues.
In summary, 410 stainless steel is more suitable for environments with limited exposure to corrosive elements, while 304 performs better in more aggressive, chloride-rich environments.
Treatment Processes of 410 and 304 Stainless Steel
The stainless steel manufacturing process includes alloying, melting, casting, rolling, pickling, passivation, and surface treatment. Processing techniques vary for 410 and 304 stainless steels due to their different compositions and properties. Here is a comparison of their treatment methods.
Welding Technology
- 410 Stainless Steel: Welding can cause cracking due to its martensitic structure. Preheating before welding and post-weld heat treatment, such as annealing, are often required to reduce internal stresses and restore toughness.
- 304 Stainless Steel: This austenitic steel welds easily with minimal preheating. It is less prone to cracking and typically does not need additional heat treatment after welding, except in extreme conditions.
Machinability
- 410 Stainless Steel: Its high hardness can lead to rapid tool wear during machining. Heat treatment can enhance its toughness and durability, making it ideal for wear-resistant uses. High-quality tools and precise cutting parameters are essential.
- 304 Stainless Steel: Offers better machinability with easier cutting and shaping. Its ductility and toughness reduce the risk of cracking, making it ideal for creating complex parts.
Heat Treatment Processes
- 410 Stainless Steel: This can be greatly enhanced through heat treatment methods like quenching and tempering. This process boosts toughness and durability, making it ideal for high-strength and wear-resistant uses.
- 304 Stainless Steel: Generally, heat treatment is not required since its austenitic structure already provides good toughness and strength at room temperature. It remains stable in various environments.
Plastic Forming
- 410 Stainless Steel: Less suitable for plastic shaping due to its strength and resilience. It is prone to cracking during forming and is best used for simpler shapes. However, it can be manufactured into various shapes, including tubes, rods, round bars, rectangular bars, and flat bars.
- 304 Stainless Steel: Excellent for plastic forming with good ductility. It is easily stamped, bent, and shaped, making it ideal for complex parts and thin-walled structures. Like 410, it can also be produced in forms such as tubes, rods, round bars, rectangular bars, and flat bars.
410 stainless steel requires meticulous welding methods, including preheating and post-weld thermal treatment. It is harder to machine and form but benefits from heat treatment for improved strength.
304 stainless steel welds easily without extra heat treatment and is easier to machine and form due to its good ductility. These distinctions influence their appropriateness for different uses.
Application of 410 Stainless Steel vs 304
The applications of stainless steel depend on its properties and treatment methods. 410 and 304 stainless steels are employed in various sectors depending on their distinct attributes. Here is a comparison of their applications.
Application | 410 Stainless Steel | 304 Stainless Steel |
Automotive Components | Used in parts requiring high strength and wear resistance, like exhaust valves and crankshafts. | Less common in automotive; used in parts requiring good corrosion resistance. |
Cutting Tools | Perfect for knives, blades, and other cutting instruments because of its toughness. | Rarely used for cutting tools; more suited for general parts. |
Food Processing Equipment | Not typically used due to lower corrosion resistance. | Widely used in food processing equipment due to its excellent corrosion resistance. |
Medical Devices | Used for surgical blades, surgical forceps, scissors | Commonly used for surgical instruments and medical equipment because of its corrosion resistance. |
Aerospace | Employed in components that demand high strength and durability, such as landing gear parts. | Less common; used in applications where corrosion resistance is crucial but not as strength-focused. |
Construction | Used for supports and frames, railings | Used for ductwork, elevator interiors, handrails and balustrades |
Marine Applications | Rarely used due to poor corrosion resistance in saltwater. | Suitable for marine units, propellers, centrifugal pumps |
Specific Components Made from 410 Stainless Steel
Automotive Components
Used in exhaust valves, crankshafts, and camshafts for high strength and wear resistance.
Cutting Tools
Employed in knives, blades, and saws because of its toughness and edge durability.
Medical Devices
Utilized in surgical blades, dental tools, and orthopedic implants requiring high strength.
Aerospace Components
Used in landing gear components, turbine blades, and aircraft fasteners for durability and strength.
Construction Hardware
Employed in heavy-duty bolts, screws, and structural supports for increased strength and resistance to wear.
Specific Components Made from 304 Stainless Steel
Food Processing Equipment
Found in mixers, blenders, conveyors, and food storage tanks due to its corrosion resistance and sanitary properties.
Medical Instruments
Used in surgical instruments, syringes, and hospital equipment for its cleanliness and resistance to corrosion.
Kitchen Appliances
Applied in sinks, refrigerators, dishwashers, and countertops for durability and ease of cleaning.
Architectural Fixtures
Utilized in railings, supports, exterior facades, and decorative panels for its visual appeal and weather resilience.
Marine Equipment
Suitable for boat fixtures, pumps, and marine equipment due to its resistance to saltwater corrosion.
In summary, 410 stainless steel is utilized in applications demanding elevated strength and toughness, such as automotive components, cutting instruments, and aerospace parts. It is suitable for heavy-duty and wear-resistant applications.
Stainless steel 304, on the other hand, is used in applications that require excellent corrosion resistance and cleanliness, such as food processing equipment, medical devices, and kitchen utensils. It is perfect for exposure to humidity and chemicals.
Is 304 stainless steel better than 410?
304 stainless steel is often better for applications requiring high corrosion resistance, toughness, and ease of machining. 410 is better for applications needing high strength and hardness.
Is 410 stainless steel food grade?
410 stainless steel is generally not food grade because of its reduced corrosion resistance compared to 304. For food processing, 304 is preferred.
Does 410 Stainless Steel Rust?
Yes, 410 stainless steel can corrode because it has less resistance to corrosion compared to other stainless steel like 304. It is more vulnerable to corrosion in harsh environments.
What do you weld 410 stainless steel with?
410 stainless steel is commonly welded with 410 filler metal or 308L/309L fillers, depending on the application and the base material.
Is 410 Stainless Steel Magnetic?
Yes, 410 stainless steel is magnetic due to its high ferrite content. Its martensitic structure allows it to retain magnetism, especially in its hardened condition.
Can 410 stainless be used with aluminum?
It is not recommended to use 410 stainless steel with aluminum due to differences in their properties, which can cause galvanic corrosion.
Selecting the Perfect Stainless Steel for Your Needs
In conclusion, 304 is ideal for food processing and medical equipment because of its corrosion resistance. 410 is used for its strength in automotive and aerospace parts. 304 handles moisture and chemicals better, while 410 is more prone to rust and is not used for food-grade applications.
Although 304 is more expensive, its superior corrosion resistance extends the lifespan of products, making it a better long-term investment.
SteelPRO Group is a manufacturer and solution provider of specialty steels, offering customized solutions across various industries. We are specialists in the stainless steel industry. For additional details on stainless steel, please visit our blog page. If you are interested in our custom services, contact us for a quote!
- Stainless Steel Grades
- 300 Series Stainless Steel
- 303 Stainless Steel
- 304 Stainless Steel
- 305 Stainless Steel
- 308 Stainless Steel
- 316 Stainless Steel
- 316N Stainless Steel
- 409 Stainless Steel
- 410 Stainless Steel
- 416 Stainless Steel
- 420 Stainless Steel
- 430 Stainless Steel
- 410HT And 410L Stainless Steels
- 410S Stainless Steel
- 440 Stainless Steel
- 436 Stainless Steel
- 301 Stainless Steel
- 201 Stainless Steel
- 202 Stainless Steel
- 444 Stainless Steel
- 405 Stainless Steel
- 302 Stainless Steel
- 309 Stainless Steel
- 314 Stainless Steel
- 321 Stainless Steel
- 347 Stainless Steel
- 408 Stainless Steel
- 422 Stainless Steel
- 431 Stainless Steel
- 434 Stainless Steel
- 414 Stainless Steel
- 430FR Stainless Steel
- 13-8 PH Stainless Steel
- 317 | 317L Stainless Steel
- 616 Stainless Steel
- 630 Stainless Steel
- 904L Stainless Steel
- A2 Stainless Steel
- 304 vs 304L Stainless Steel
- 304 VS 316 Stainless Steel
- 304 vs 409 Stainless Steel
- 304 vs 430 Stainless Steel
- 410 Stainless Steel vs 304
- 18/0 vs 18/10
- 18/0 Stainless Steel
- 18/8 Stainless Steel
- 18/10 Stainless Steel
Comparisons