Contents
305 Stainless Steel: Definition, Composition, Properties, Applications and More
- John
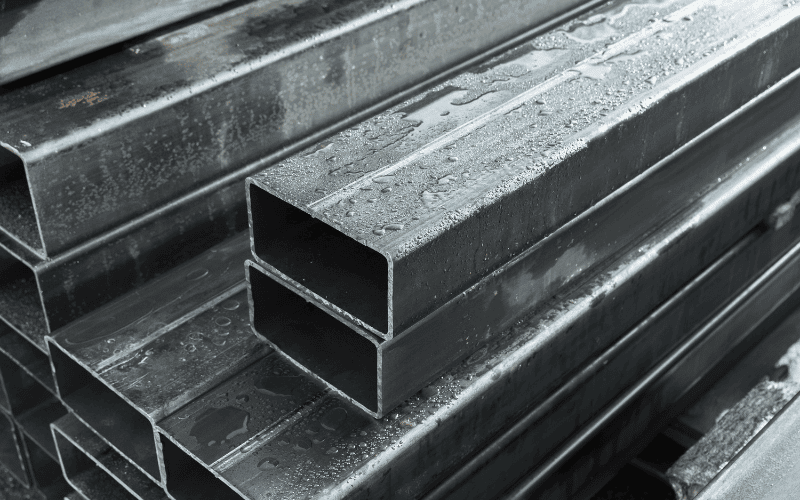
If you need a stainless steel that is easy to shape and resistant to corrosion, 305 stainless steel might be the answer. It’s widely used in industries that require both durability and workability. In this article, we’ll take a closer look at the composition, charactrises, uses, and more of 305 stainless steel.
What is 305 Stainless Steel?
305 stainless steel is a family of austenitic chromium-nickel stainless steels. It consists of 68% iron, 17-19% chromium, and 10.5-13% nickel, with small amounts of manganese, silicon, carbon, phosphorus, and sulfur.
305 stainless steel has a low work hardening rate, allowing for easier forming and drawing. It offers excellent formability and great corrosion resistance. Usually used for electronic components, kitchen equipment, household appliances, and automotive parts.
305 Stainless Steel Equivalents
There are several equivalents of 305 stainless steels depending on the standards and countries.
- AISI 305 ( American Iron and Steel Institute)
- ASTM 305 ( American Society for Testing and Materials)
- UNS S30500 ( Unified Numbering System)
- EN 1.4303 ( European Standard)
305 Stainless Steel Standards
- ASTM A240
- ASME SA240
- AMS 5514
Nominal Composition of 305 Stainless Steel
This table shows the nominal composition of 305 stainless steel.
Element | Iron | Chromium | Nickel | Manganese | Silicon | Carbon | Phosphorus | Sulfur |
Composition (%) | ~68 | 17-19 | 10.5-13 | Max 2 | Max 1 | Max 0.12 | Max 0.045 | Max 0.03 |
Physical Properties of 305 Stainless Steel
Property | Metric | Imperial |
Density | 8.03 g/cm³ | 0.290 lb/in³ |
Melting Point | 1398–1421 °C | 2550–2590 °F |
Thermal Conductivity | 14.9 W/m·K | 103 BTU·in/hr·ft²·°F |
Thermal Expansion | 17.2 × 10⁻⁶ /°C | 9.56 × 10⁻⁶ /°F |
Electrical Conductivity | 1.45 × 10⁶ S/m | 2.5% IACS |
Magnetic Properties | Non-magnetic | Non-magnetic |
Mechanical Properties of 305 Stainless Steel
Property | Typical Value |
Tensile Strength | 515–620 MPa (74.7-90 ksi) |
Yield Strength | 205–260 MPa (29.7-80 ksi) |
Brinell Hardness | 147 HB |
Rockwell Hardness | 80–90 HRB |
Vickers Hardness | 150–170 HV |
Elongation | 40% in 50 mm |
Young’s Modulus | 193 GPa (28 x 10^3 ksi) |
Advantages of 305 Stainless Steel
- Good Corrosion Resistance. 305 stainless steel resists rust and corrosion well, making it suitable for various environments, including those with moisture and chemicals.
- High Ductility. This steel can be easily formed into different shapes without cracking. It’s great for applications that require bending or deep drawing.
- Non-Magnetic. In its annealed condition, 305 stainless steel is non-magnetic, which is important for certain applications like electronics and medical tools.
- Excellent Surface Finish. It has a smooth, shiny surface, making it ideal for decorative purposes or applications where appearance matters.
Disadvantages of 305 Stainless Steel
- Lower Strength.
Compared to some other stainless steel, 305 has lower tensile strength. It may not be the best choice for very high-stress applications.
- Higher Cost.
Due to its higher nickel content, 305 stainless steel can be more expensive than other grades like 304.
- Not Suitable for High-Temperature Environments.
305 stainless steel doesn’t perform well in extreme heat, as it can lose some of its mechanical properties.
What is 305 Stainless Steel Used for?
305 stainless steel is commonly available in the forms of sheets and plates, bars and rods, wires, strips, and coils. Here is a table about the applications of 305 stainless steel.
Application | Reasons |
Kitchen Equipment | Excellent corrosion resistance |
Household Appliances | Durable and easy to clean |
Automotive Parts | High formability, suitable for trims |
Electronic Components | Precise forming, environmental resistance |
Manufacturing and Processing of 305 Stainless Steel
These processes and methods ensure that 305 stainless steel has excellent formability, strong corrosion resistance, and the ability to be used in a wide range of applications.
Manufacturing Process
- Melting and Casting
Melt raw materials, including iron, chromium, nickel, manganese, silicon, carbon, phosphorus, and sulfur in an electric arc furnace. Then the molten steel is cast into slabs.
- Hot Rolling
The slabs are heated to high temperatures (1149 to 1260°C or 2100 to 2300°F) and passed through rolling mills. This process reduces the thickness and forms the steel into sheets or plates. Rapid cooling follows to preserve the steel’s properties.
- Annealing
After hot rolling, the steel undergoes annealing by heating it to 1010 to 1121°C (1850 to 2050°F) and then rapidly cooling. Annealing relieves internal stresses and enhances ductility.
- Pickling
The annealed steel is pickled in an acid bath to remove the oxide scale formed during hot rolling and annealing. This step cleans the surface and prepares it for further processing.
- Cold Rolling
Pass the steel through rollers at room temperature. This can achieve final thickness and improve the surface finish. Cold rolling increases strength and hardness through work hardening.
- Finishing
Final finishing processes include cutting, polishing, and surface treatments to ensure the steel conforms to the required specifications for its applications.
Machining
Using slow speeds and heavy feeds to effectively machine 305 stainless steel. This helps to prevent the material from glazing during machining. Traditional machining methods are recommended due to the alloy’s higher carbon content. That provides good cutting speeds and high-quality surface finishes.
Welding
Welding 305 stainless steel can be challenging due to its hardness. Proper equipment and techniques are important to prevent cracking. Oxyacetylene welding is not recommended. Using 309L filler metal is advised to achieve optimal corrosion resistance. Special nonmagnetic clamps are often needed to protect the welding arc from oxidation and contamination.
Hot Working
Hot working of 305 stainless steel should be performed at temperatures between 1149 to 1260°C (2100 to 2300°F). Rapid cooling is required after hot working to maximize corrosion resistance. This process ensures the material retains its desirable properties while enhancing its durability.
Cold Working
305 stainless steel exhibits excellent cold-working properties because it has a low work hardening rate. This allows the steel to be easily drawn, spun, headed, and blanked. Cold working significantly enhances the material’s strength and hardness without compromising its formability.
Hardening
Standard heat treatments are ineffective for hardening 305 stainless steel. Instead, its hardness and strength are improved through cold working processes. This method effectively increases the material’s durability for a range of demanding applications.
The Difference Between 305 Stainless Steel And Other Stainless Steel Grades
This table shows the differences in the elemental composition of these stainless steel grades.
Element | 305 | 304 | 303 | 316 |
Carbon | ≤0.12% | ≤0.08% | ≤0.15% | ≤0.08% |
Manganese | ≤2.00% | ≤2.00% | ≤2.00% | ≤2.00% |
Phosphorus | ≤0.045% | ≤0.045% | ≤0.20% | ≤0.045% |
Sulfur | ≤0.03% | ≤0.03% | 0.15-0.35% | ≤0.03% |
Silicon | ≤1.00% | ≤1.00% | ≤1.00% | ≤1.00% |
Chromium | 17.0-19.0% | 18.0-20.0% | 17.0-19.0% | 16.0-18.0% |
Nickel | 10.5-13.0% | 8.0-10.5% | 8.0-10.0% | 10.0-14.0% |
Nitrogen | N/A | ≤0.10% | N/A | ≤0.10% |
304 vs 305
- 305 stainless steel has better formability due to its higher nickel content. In contrast, 304 is good for general forming but less effective for intricate shapes.
- 305 has a lower work hardening rate, making it easier to machine and form without becoming too hard. 304 hardens more quickly when worked, which increases strength but also brittleness.
- Both offer similar corrosion resistance. However, 305 costs more due to its higher nickel content.
303 vs 305
- 305 stainless steel has better formability than 303. 303 contains more sulfur, which improves machinability. 303 is less suitable for intricate forming.
- 303 has lower corrosion resistance. 305 is more expensive, while 303 is more cost-effective for applications where high machinability is needed and corrosion resistance is less critical.
316 vs 305
- 316 stainless steel is stronger and more durable due to the presence of molybdenum. It is suitable for more demanding environments.
- 316 is also more expensive than 305 because of its higher nickel and molybdenum content. 305 has a higher melting point range than 316.
- 305 is used for intricate forming, like electronic components and kitchen utensils. 316 is used in oceanic environments, pharmaceutical manufacturing, and surgical instruments.
Common Forms of 305 Stainless Steel
The following are common application forms of 305 stainless steel
Sheets and Plates
They are flat steel pieces. They have a range of thicknesses. They are used in applications like kitchen equipment, appliances, and electronic components.
Bars and Rods
They are long and solid steel. Their cross-section is circular or rectangular. They are used in manufacturing, machining, and structural applications.
Wires
Thin strands of steel are used in electronic components, springs, and wire forms. They are valued for their strength and flexibility.
Strips
Narrow, flat pieces of steel are often used in automotive parts, clamps, and brackets.
Coils
Continuous sheets or strips of steel rolled into coils. They are used in large-scale manufacturing processes where long steel lengths are required. Summary & Furthermore
Is 305 Stainless Steel Marine Grade?
No, 305 stainless steel is not considered marine grade. Marine grade stainless steel is typically 316 stainless steel. 305 is more suited for applications requiring high formability, not marine environments.
Is 305 Stainless Steel Food Grade?
Yes, 305 stainless steel is considered food grade due to its high corrosion resistance and non-reactive nature. It is suitable for food processing and kitchen equipment applications.
How About 305 Stainless Steel Screws?
305 stainless steel screws are fasteners made from 305-grade stainless steel, known for its high corrosion resistance and excellent formability.
305 stainless steel screws, due to their high nickel content, have excellent ductility. This means they can be easily formed during production and are more adaptable to stress in practical use, providing greater durability and resilience.
Summary & Furthermore
This article briefly explains the definition, composition, applications, and other important aspects of 305 stainless steel. To learn more about stainless steel or other steel types, check out our blog or contact our metal experts.
As a leading manufacturer and solutions provider of specialty steel, we deliver multi-industry application solutions and customized services with a 100% quality guarantee, committed to growing together with our customers. Visit our website to learn more, or send us a quote, and we will contact you shortly!
- Stainless Steel Grades
- 300 Series Stainless Steel
- 303 Stainless Steel
- 304 Stainless Steel
- 305 Stainless Steel
- 308 Stainless Steel
- 316 Stainless Steel
- 316N Stainless Steel
- 409 Stainless Steel
- 410 Stainless Steel
- 416 Stainless Steel
- 420 Stainless Steel
- 430 Stainless Steel
- 410HT And 410L Stainless Steels
- 410S Stainless Steel
- 440 Stainless Steel
- 436 Stainless Steel
- 301 Stainless Steel
- 201 Stainless Steel
- 202 Stainless Steel
- 444 Stainless Steel
- 405 Stainless Steel
- 302 Stainless Steel
- 309 Stainless Steel
- 314 Stainless Steel
- 321 Stainless Steel
- 347 Stainless Steel
- 408 Stainless Steel
- 422 Stainless Steel
- 431 Stainless Steel
- 434 Stainless Steel
- 414 Stainless Steel
- 430FR Stainless Steel
- 13-8 PH Stainless Steel
- 317 | 317L Stainless Steel
- 616 Stainless Steel
- 630 Stainless Steel
- 904L Stainless Steel
- A2 Stainless Steel
- 304 vs 304L Stainless Steel
- 304 VS 316 Stainless Steel
- 304 vs 409 Stainless Steel
- 304 vs 430 Stainless Steel
- 410 Stainless Steel vs 304
- 18/0 vs 18/10
- 18/0 Stainless Steel
- 18/8 Stainless Steel
- 18/10 Stainless Steel
Comparisons