Contents
416 Stainless Steel: Definition, Composition, Properties, Processing, Applications, and More
- John
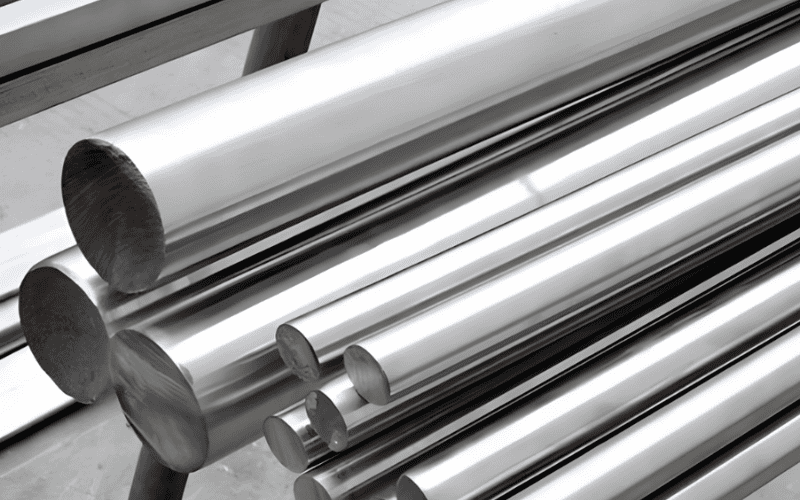
SteelPRO Group inventory now has SS 416 (UNS S41600) products in stock: plates, sheets, coils, strips, pipes, tubing, bars, rods, etc. Also, a range of surface finishes for you to choose from: No. 1, 2B, 2D, BA, No. 3, No. 4, HL, No. 8, Bead Blasted, etc.
We guarantee 100% quality. No defective products will be shipped to our customers. Contact us to customize the desired form of your products, including shape, condition, surface finish, treatment, etc.
What Is 416 Stainless Steel?
416 is a 400 series martensitic stainless steel that offers the best machinability (85%) of all stainless steel, primarily composed of chromium, manganese, and sulfur. The material complies with the ASTM A582 standard and is equivalent to EN 1.4005 (X12CrS13) and UNS S41600. Its superior machinability comes from its high sulfur content, making it especially suitable for high-speed machining operations. However, the addition of sulfur also reduces its formability, weldability, and corrosion resistance. Common applications include components such as screws, bolts, and pump shafts, where ease of machining and moderate corrosion resistance are required.
Chemical Composition of 416 Stainless Steel
The chemical composition of 416 stainless steel is listed as below:
Carbon, C | Chromium, Cr | Manganese, Mn | *Nickel, Ni | *Molybdenum, Mo | Phosphorus, P | Silicon, Si | Sulfur, S |
≤ 0.15 % | 13 % | ≤ 1.25 % | ≤1.0% | ≤ 0.60 % | ≤ 0.060 % | ≤ 1.0 % | ≥ 0.15 % |
*Nickel & *Molybdenum: additional options
Properties of 416 Stainless Steel
Here are three major reasons that make 416 stainless steel unique:
- High machinability, making it easy to cut and shape.
- Can be heat treated to increase hardness and strength.
- Good resistance to wear and tear, suitable for mechanical parts.
Physical Properties
Check the table below for the core physical properties of 416 stainless steel:
Property | Typical Value | Performance |
Density | 7.80 g/cm³ (0.282 lb/in³) | High density, strong and durable |
Melting Point | 1480-1530 °C (2700-2790 °F) | High melting point, suitable for high temperatures |
CTE, Linear (0-100°C/32-212°F) | 9.9 μm/m·°C (5.50 μin/in·°F) | Moderate thermal expansion |
Specific Heat Capacity (0-100°C/32-212°F) | 460 J/kg·K (0.110 BTU/lb·°F) | Good heat capacity, effective for heat retention |
Thermal Conductivity (at 100°C/212°F) | 24.9 W/m·K (172 BTU·in/h·ft²·°F) | Good thermal conductivity, efficient heat transfer |
Electrical Conductivity | 23% IACS (23% IACS) | Moderate electrical conductivity |
Electrical Resistivity (at 20°C/68°F) | 43 μΩ·cm (43 μΩ·cm) | Moderate electrical resistivity |
Mechanical Properties
Check the table below for the core mechanical properties of 416 stainless steel:
Temperature (°C) | Tensile Strength (MPa/ksi) | Yield Strength (MPa/ksi) | Brinell Hardness (HRB) | Rockwell Hardness (HRC) | Vickers Hardness (HV) | Elongation at Break (%) | Young’s Modulus (GPa/msi) |
150 | 1310/190 | 983/143 | 365 | 39.5 | 383 | 9 | 200/29 |
260 | 1295/187.8 | 962/140 | 360 | 39 | 378 | 9.5 | 200/29 |
370 | 1260/183 | 962/140 | 360 | 39 | 378 | 14 | 200/29 |
480 | 1185/171.9 | 962/140 | 360 | 39 | 378 | 16 | 200/29 |
540 | 1080/157 | 895/130 | 318 | 34 | 332 | 13 | 200/29 |
595 | 865/125 | 740/107 | 266 | 26 | 275 | 17 | 200/29 |
650 | 796/115 | 670/97.2 | 253 | 23.5 | 260 | 17.5 | 200/29 |
705 | 741/107 | 600/87 | 237 | 20 | 242 | 20 | 200/29 |
Chemical Properties
Check the table below for the core chemical properties of 416 stainless steel:
Chemical Property | Description | Performance |
Corrosion Resistance | Ability to resist corrosion in different environments. | Moderate; lower compared to austenitic grades like 304, better than carbon steel. |
pH Sensitivity | Response to acidic or basic environments. | Sensitive to acidic conditions; performs better in neutral or mild alkaline environments. |
Reactivity | Tendency to undergo chemical reactions. | Low reactivity in mild environments; prone to pitting in chlorides. |
Oxidation Resistance | Resistance to oxidation at elevated temperatures. | Fair; better than carbon steel but lower than higher-alloyed stainless steel. |
Passivation | Ability to form a protective oxide layer. | Moderate; forms a chromium oxide layer but less stable than higher chromium alloys. |
Combustibility | Ability to catch fire under normal conditions. | Non-combustible; does not burn under standard conditions. |
Flammability | Likelihood to ignite or support combustion. | Non-flammable; resistant to ignition in all practical industrial scenarios. |
Heat & Corrosion Resistance of 416 Stainless Steel
Heat Resistance
Grade 416 stainless steel offers moderate heat resistance but should be used cautiously at high temperatures.
It can fairly resist scaling in continuous service up to 650°C and up to 760°C under intermittent operation. However, its tensile strength, creep resistance, and stress rupture performance diminish rapidly at relatively low temperatures. Additionally, its high sulfur content increases susceptibility to hot cracking.
Therefore, 416 stainless steel is typically not recommended for high-temperature applications. It is also unsuitable for use below zero degrees, as its impact strength significantly decreases.
Corrosion Resistance
Grade 416 stainless steel has lower corrosion resistance compared to many other stainless steel grades, including austenitic, ferritic, and other martensitic grades. While its higher sulfur content enhances machinability, it also increases susceptibility to corrosion.
416 stainless steel performs well in dry and mildly corrosive environments but is not suitable for chloride or marine conditions. Its corrosion resistance is best when the steel is hardened and tempered rather than in the annealed condition.
To maintain its protective chrome oxide layer, proper surface treatment is crucial. This includes passivation, removing foreign particles, and ensuring free oxygen circulation on the surface to help prevent rust.
Processing of 416 Stainless Steel
Forming
416 stainless steel has poor formability due to its high sulfur content, which increases machinability but reduces ductility. It is prone to cracking during forming, so aggressive techniques should be avoided.
Preheating and using lubricants can help reduce the risk of cracks, but the material is better suited for machining than complex forming. If forming is necessary, post-forming heat treatment may be required to restore strength and hardness.
Welding
416 stainless steel is generally not recommended for welding due to its high sulfur content. This makes the material prone to cracking, either during or after welding. Sulfur can lead to hot cracking, while the hardening properties of the steel may cause cold cracking.
If welding is unavoidable, special precautions are needed. Preheating the steel to 200-300°C helps reduce the risk of cracking. Choosing the right filler materials is also key. For strength, low-hydrogen electrodes like grade 410 are often used. For more flexibility in the weld, austenitic stainless fillers, such as grade 308, are suitable.
It’s important to keep the heat input low during welding to avoid too much dilution with the filler metal. After welding, cooling should be done slowly to minimize stress. Post-weld treatments, such as annealing or stress relieving, may be required to restore the material’s properties.
Machining
416 stainless steel offers excellent machinability. It was specifically developed as a free-machining grade, making it the best option among the 400 series martensitic stainless steels for machining tasks. Its performance in this area is even better than grade 303, a free-machining austenitic stainless steel.
Operations like turning, drilling, and milling can be performed easily on 416 as long as the appropriate tools and machine settings are used. The best machinability is achieved when the steel is in the sub-critical annealed condition, which helps reduce wear on tools and improve precision.
Heat Treatment
416 stainless steel has moderate hardenability, meaning it can be hardened by heat treatment but only to a limited depth. Its relatively low carbon content (around 0.15%) restricts the maximum hardness achievable, which also helps to maintain core toughness.
- Full Annealing
- Heat to 815-900°C for 30 minutes.
- Cool at a rate of 30°C per hour, followed by air cooling.
- Sub-Critical Annealing
- Heat to 650-760°C.
- Air cool after heating.
- Hardening
- Heat to 925-1010°C.
- Quench in oil.
- Temper, avoiding the range of 400-580°C to prevent poor ductility.
Advantages and Disadvantages of 416 Stainless Steel
Here are the advantages and benefits of 416 stainless steel:
- Excellent machinability, making it easy to shape and cut.
- Can be heat treated to increase hardness and durability.
- High strength, allowing it to withstand heavy loads.
- Cost-effective compared to other stainless steels.
- Good corrosion resistance, suitable for mild environments.
Here are the disadvantages and limitations of 416 stainless steel:
- Lower corrosion resistance than other stainless steels like 304 or 316.
- Brittle when hardened, leading to potential cracking under high stress.
- Not ideal for marine or chloride-rich environments.
- Reduced toughness at lower temperatures, making it less suited for cold environments.
- Limited welding ability due to its high sulfur content.
Common Applications of 416 Stainless Steel
416 stainless steel is good for applications requiring good machinability, moderate corrosion resistance, and high strength, such as in screws, bolts, and gears. It is commonly used in parts that need to be easily machined.
Check the table below for a quick view of its common applications:
Industry | Application | Why It Suits |
Automotive | Gears, Shafts, Bolts, Valve Components | High machinability, corrosion resistance, good strength |
Aerospace | Valve Parts, Bushings, Bolts, Fasteners | High strength, wear resistance, corrosion resistance |
Industrial Machinery | Pump Shafts, Screws, Spindles, Bearings | Good wear resistance, machinability, heat resistance |
Medical Instruments | Surgical Tools, Dental Drills, Fasteners, Handles | Corrosion resistance, ease of sterilization, high strength |
Oil & Gas | Valve Components, Pump Shafts, Screws, Couplings | Corrosion resistance, high strength, and durability in harsh environments |
Food Processing Equipment | Blades, Screws, Nozzles, Mixer Shafts | Corrosion resistance, easy to clean, high machinability |
Equivalent Grades of 416 Stainless Steel in Different Countries and Regions
Here are some common equivalent grades of SS 416 in different countries and regions:
Country | Standard/Specification | Equivalent Grade |
EU | EN 10088-1 | X12CrS13 (1.4005) |
USA | ASTM A582/A582M | 416 |
France | NF A35-574 | Z11CF13 |
England | BS 970-1:1991 | 416S21 |
Sweden | SS 14 23 80 | 2380 |
Comparing 416 vs 304 vs 316 Stainless Steel
Check the table below for a quick comparison between them:
Property | 416 | 304 | 316 |
Type | Martensitic | Austenitic | Austenitic |
Crystal Structure | Body-Centered Cubic (BCC) | Face-Centered Cubic (FCC) | Face-Centered Cubic (FCC) |
Chemical Composition | Cr: 13%, Mn: ≤ 1.25%, S: ≥ 0.15% | Cr: 18-20%, Ni: 8-10.5% | Cr: ≤ 18%, Mo: ≤ 3%, Ni: ≤ 14% |
Corrosion Resistance | Moderate | Good | Excellent |
Strength | High | Moderate | Moderate to high |
Hardness | High | Moderate | Moderate |
Weldability | Fair to poor | Excellent | Good |
Magnetic Properties | Magnetic | Non-magnetic | Non-magnetic |
Cost | Moderate | Lower | Higher |
Applications | Cutlery, valves, surgical instruments | Kitchen equipment, piping, automotive parts | Marine, chemical processing, medical devices |
What You Might Also Concern
Now that you have a deeper understanding of 416 stainless steel, there are still some common issues that deserve your attention:
Does 416 Stainless Rust?
Yes, 416 stainless steel can rust because it has lower corrosion resistance compared to other stainless steel due to its higher sulfur content for machinability. However, it is still more resistant to rust than regular steel.
Related Reading
Will Stainless Steel Rust and How Can You Solve It?
Is 416 Stainless Steel Magnetic?
Yes, 416 stainless steel is magnetic due to its martensitic structure.
Related Reading
Is Stainless Steel Magnetic?
Is 416 Stainless Steel Food-grade?
No, 416 stainless steel is generally not food-grade because its higher sulfur content makes it more prone to corrosion. Food-grade stainless steels typically include 304 and 316, which are more resistant to corrosion and safe for food contact.
Is 416 Stainless Steel Good for Knives?
No, 416 stainless steel is not ideal for knives. It’s known for its machinability but lacks the hardness and edge retention needed for high-quality knife blades. Knives typically require harder steels like 440C or 154CM for better performance.
Is 416 Stainless Steel Better than 316?
It depends on specific needs. 316 stainless steel is generally better for corrosion resistance, especially in marine or chemical environments, while 416 stainless steel is easier to machine but has lower corrosion resistance.
What is the Difference Between 304 and 416 Stainless Steel?
304 stainless steel is an austenitic grade with excellent corrosion resistance, good weldability, and non-magnetic properties. 416 stainless steel is a martensitic grade, offering better machinability, but has lower corrosion resistance and is magnetic.
Summary & Furthermore
This article briefly explains the definition, composition, properties, processing characteristics, applications, and other important aspects of 416 stainless steel. To learn more about stainless steel or other steel types, check out our blog or contact our metal experts.
As a leading manufacturer and solutions provider of specialty steel, SteelPRO delivers multi-industry application solutions and customized services. We guarantee 100% product quality and are committed to growing together with our customers. Visit our website to learn more, or send us an inquiry. We will contact you shortly!
- Stainless Steel Grades
- 300 Series Stainless Steel
- 303 Stainless Steel
- 304 Stainless Steel
- 305 Stainless Steel
- 308 Stainless Steel
- 316 Stainless Steel
- 316N Stainless Steel
- 409 Stainless Steel
- 410 Stainless Steel
- 416 Stainless Steel
- 420 Stainless Steel
- 430 Stainless Steel
- 410HT And 410L Stainless Steels
- 410S Stainless Steel
- 440 Stainless Steel
- 436 Stainless Steel
- 301 Stainless Steel
- 201 Stainless Steel
- 202 Stainless Steel
- 444 Stainless Steel
- 405 Stainless Steel
- 302 Stainless Steel
- 309 Stainless Steel
- 314 Stainless Steel
- 321 Stainless Steel
- 347 Stainless Steel
- 408 Stainless Steel
- 422 Stainless Steel
- 431 Stainless Steel
- 434 Stainless Steel
- 414 Stainless Steel
- 430FR Stainless Steel
- 13-8 PH Stainless Steel
- 317 | 317L Stainless Steel
- 616 Stainless Steel
- 630 Stainless Steel
- 904L Stainless Steel
- A2 Stainless Steel
- 304 vs 304L Stainless Steel
- 304 VS 316 Stainless Steel
- 304 vs 409 Stainless Steel
- 304 vs 430 Stainless Steel
- 410 Stainless Steel vs 304
- 18/0 vs 18/10
- 18/0 Stainless Steel
- 18/8 Stainless Steel
- 18/10 Stainless Steel
Comparisons