Contents
Stainless Steel
- John
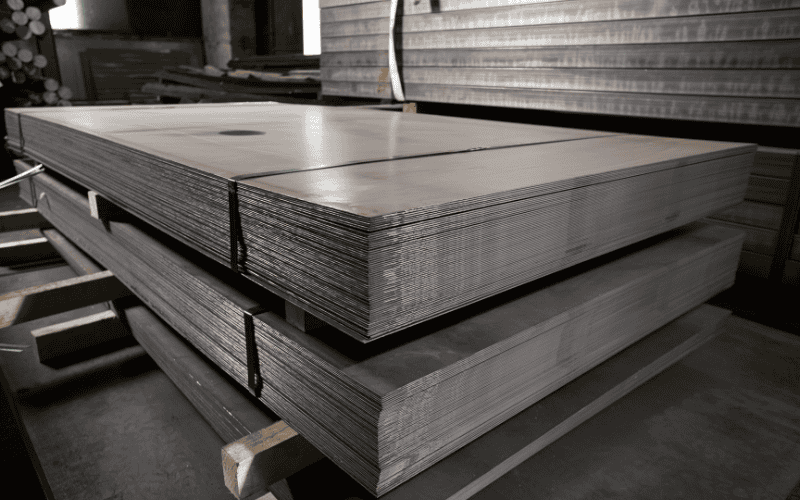
Stainless steel is categorized based on its crystal structure and composition, which influence its properties. These properties ultimately decide its suitability for various applications. In this guide, we’ll explore everything you need to know about stainless steel, from its types and grades to its properties and application. Let’s dive in!
What Is Stainless Steel?
Stainless steel, also named inox, is an alloy steel with 70-80% iron, a minimum of 10.5% chromium, and other elements like carbon. Because of the chromium, it is resistant to rusting and corrosion. Its cleanability is superior to that of aluminum and copper.
With other properties like high strength, durability, and luster, it is used in construction, automotive, medical instruments, and kitchenware. Common types include austenitic, ferritic, martensitic, and duplex.
Is Stainless Steel a Compound?
No, stainless steel is not a compound. It is an alloy, made primarily of iron, chromium, and other elements like nickel and carbon. The combination of these elements gives it unique properties, such as corrosion resistance.
What Are the Main Types of Stainless Steel?
Stainless steel is primarily categorized into five types based on its crystal structure and composition: austenitic, ferritic, martensitic, duplex, and precipitation-hardening stainless steel.
Austenitic Stainless Steel
Austenitic stainless steel features a face-centered cubic (FCC) crystal structure. Its composition includes high levels of chromium (16-26%) and nickel (10-22%), sometimes with additional small amounts of alloying elements such as molybdenum, nitrogen, titanium, and niobium.
Because it has good corrosion resistance, it is perfect for usage in corrosive conditions. Its outstanding formability and weldability make it suitable for a wide range of applications. Additionally, it maintains high toughness and ductility at all temperatures, ensuring reliable performance under different conditions. Another notable property is its non-magnetic nature when in the annealed condition.
Applications:
- Food and Beverage Equipment: It is corrosion-resistant and easy to clean.
- Kitchenware and Cutlery: For its durability and hygiene.
- Chemical Processing Equipment: Because of its capacity to withstand corrosives.
- Marine Applications: Excellent resistance to saltwater corrosion.
Ferritic Stainless Steel
Ferritic stainless steel features a body-centered cubic (BCC) crystal structure and is characterized by high chromium content (10.5-30%) with low or no nickel.
This composition gives ferritic stainless steel several notable properties. It is corrosion-resistant, particularly in mild conditions. Ferritic stainless steel is magnetic. It also exhibits better resistance to stress corrosion cracking compared to austenitic steels. However, its formability and weldability are limited compared to austenitic steels.
They contain high levels of chromium but little or no nickel, making them a more cost-effective option compared to austenitic steels. This combination of properties makes ferritic stainless steels suitable for applications where moderate corrosion resistance and magnetic properties are required without the higher costs associated with nickel.
Applications:
- Automotive Parts: Used in exhaust systems and trim.
- Industrial Equipment: Suitable for mild corrosive environments.
- Kitchen Appliances: Ferritic alloys are better for thermophysical uses like cooking utensils because they conduct heat better and expand less than austenitic stainless steel. They are durable and cost-effective for household use.
Martensitic Stainless Steel
Martensitic stainless steel has a body-centered tetragonal (BCT) crystal structure and is characterized by its higher carbon content and chromium content ranging from 11-17%, with the possibility of other alloying elements. This composition allows martensitic stainless steel to be hardened by heat treatment, giving it excellent hardness and strength. Despite having moderate corrosion resistance, it retains its magnetic properties because of its crystal structure. Because martensitic stainless steels have higher quantities of carbon than other stainless steels, they are ideal for applications that require strong wear resistance.
Applications:
- Cutlery and Surgical Instruments: Excellent strength and wear resistance.
- Fasteners: Strong and durable.
- Pump Shafts: Suitable for moderate corrosive environments.
Duplex Stainless Steel
Duplex stainless steel features a mixed crystal structure of austenitic (FCC) and ferritic (BCC) phases. It has 19-28% chromium, 4.5-8% nickel, and often includes molybdenum. This gives it the strength and corrosion resistance of both types. Its yield strength is about twice that of austenitic stainless steel. Duplex is classified into lean, standard, and super duplex based on corrosion resistance. It also has good weldability and is highly resistant to stress corrosion cracking and chloride pitting, making it ideal for demanding applications.
Applications:
- Chemical Processing Equipment
- Offshore and Marine Environments: Highly resistant to saltwater.
- Thermal Exchangers and Pressure Containers: Suitable for high-pressure applications.
Precipitation Hardening Stainless Steel
Precipitation-hardening stainless steel has a varied crystal structure, often martensitic or semi-austenitic. It is alloyed with elements such as aluminum, copper, and niobium, which enable it to be hardened through heat treatment. This stainless steel has excellent mechanical qualities and is resistant to corrosion. It is known for its ability to be significantly hardened, resulting in enhanced hardness and strength after undergoing the heat treatment process.
Applications:
- Aerospace Components: High strength and resistance to corrosion.
- Chemical Processing Equipment: Durable and reliable in harsh environments.
- High-Performance Engineering Applications: Suitable for precision parts requiring high strength.
Type | Crystal Structure | Chromium Content (%) | Nickel Content (%) | Additional Alloying Elements | Corrosion Resistance | Magnetic Properties | Formability and Weldability | Notable Properties |
Austenitic | FCC | 16-26 | 10-22 | Molybdenum, Nitrogen, Titanium, Niobium | High | Non-magnetic in annealed condition | Excellent | High toughness and ductility at all temperatures |
Ferritic | BCC | 10.5-30 | Low or None | None | Good in mild conditions | Magnetic | Limited | Cost-effective |
Martensitic | BCT | 11-17 | Low | Various | Moderate | Magnetic | Limited | Hardened by heat treatment, excellent hardness and strength |
Duplex | FCC + BCC | 19-28 | 4.5-8 | Molybdenum | High | Varies | Good | Better strength and corrosion resistance than austenitic or ferritic alone |
Precipitation Hardening | Varied (Martensitic or Semi-Austenitic) | Varied | Varied | Aluminum, Copper, Niobium | High | Varies | Good | Significantly hardened by heat treatment |
Learn About the Types of Stainless Steel!
What Are the Grades of Stainless Steel?
Stainless steel grades are classified using various global systems to ensure consistency and reliability. The AISI system uses three-digit numbers, such as 304 and 316, to denote different types of stainless steel. ASTM provides detailed standards and specifications for these materials. The EN system uses numerical and letter codes, like EN 1.4301 for AISI 304. In Japan, the JIS system includes grades like SUS304, equivalent to AISI 304.
Stainless steel grades are classified based on their chemical composition and crystal structure. These grades can be broadly classified based on families such as austenitic, ferritic, martensitic, duplex, and precipitation-hardening stainless steel. Each family has its own unique properties and typical applications.
Common types for stainless steels are 304, 316 and 430.
Austenitic Stainless Steel
The grades for austenitic steels include 300 series and 200 series.
- 201: Lower nickel content, making it less expensive than 304. Used in appliances, kitchen utensils, and automotive trim.
- 202: Similar to 201 but with better mechanical properties and corrosion resistance.
- 304: Contains 18% chromium and 8% nickel. It is known for its high corrosion resistance and formability. It is versatile and used in kitchenware, chemical containers, and architectural applications due to its good corrosion resistance and formability. Its non-magnetic state, when annealed, combined with good welding and fabrication characteristics, further enhances its utility. For instance, in the kitchen, 304 stainless steel is commonly used in sinks, cookware, cutlery, and utensils. It is also prevalent in the chemical industry for storage tanks, piping, and processing equipment, as well as in architectural paneling for building facades and railings.
- 316: Includes 16% chromium, 10% nickel, and 2% molybdenum. This composition provides superior resistance to pitting and corrosion, especially in chloride-rich environments, making it ideal for marine environments, chemical processing, and medical devices. Because 316 stainless steel contains molybdenum, it performs well in various temperatures. This makes it ideal for boat fittings, shipbuilding parts, and coastal structures. Because of its exceptional corrosion resistance and toughness, it is employed in medical applications like surgical tools, implants, and orthopedic devices.
Ferritic Stainless Steel and Martensitic Stainless Steel
The grade for ferritic and martensitic Steel is 400 series.
- 430: Contains 16-18% chromium and less than 0.12% carbon. It is known for its high corrosion resistance and formability, making it appropriate for car trim, appliances, and some kitchen equipment. Unlike austenitic grades, 430 stainless steel is magnetic and exhibits good resistance to oxidation at high temperatures. However, it has lower resistance to pitting and crevice corrosion. Common applications include decorative trim and exhaust systems in the automotive industry, interiors of dishwashers and refrigerator panels in household appliances, and various kitchen equipment such as cutlery and sinks. Additionally, 430 stainless steel is used in fuel burners, heating elements, and various architectural features.
- 410: Contains about 12% chromium and 0.15% carbon. It is widely used in cutlery, surgical tools, and fasteners due to its great strength and resistance to corrosion.
- 420: Similar to 410 but with higher carbon content, making it harder and more wear-resistant. It is utilized in cutlery, surgical instruments, and high-wear applications.
Duplex Stainless Steel
- 2205: Contains approximately 22% chromium, 5% nickel, and 3% molybdenum. Its excellent strength and resistance to chloride-induced stress corrosion cracking make it perfect for use in chemical processing, the oil and gas industry, and construction.
- 2507: Super duplex grade with higher corrosion resistance and strength, used in demanding applications like oil and gas exploration.
Precipitation Hardening Stainless Steel
- 17-4 PH: Provides high strength and hardness when subjected to heat treatment. This material is widely used in the aerospace, chemical, and petrochemical sectors.
- 15-5 PH: Similar to 17-4 PH, but offers improved toughness and corrosion resistance.
What Are the Properties of Stainless Steel?
The key properties are corrosion resistance, strength, a high melting point, low electrical conductivity, variable magnetism, wear resistance, and density.
Corrosion Resistance
Stainless steel resists corrosion due to its chromium content, which forms a protective chromium oxide layer. The corrosion resistance of this layer depends on the steel’s chemical composition, mainly chromium levels. While stainless steel can rust, this usually affects only the surface, with deeper layers protected. Four corrosion types are common: uniform, localized (pitting), galvanic, and stress corrosion cracking (SCC). These can occur if the grade is unsuitable for the environment. Nitrogen improves pitting resistance and strengthens the steel.
Here’s a introduction to the four types of corrosion:
- Uniform Corrosion: Occurs evenly across the surface, gradually thinning the material. It’s the least harmful and easiest to detect and manage.
- Localized Corrosion (Pitting): Small, deep pits form on the surface, often due to chloride exposure, which can lead to failure if unchecked.
- Galvanic Corrosion: Happens when two dissimilar metals are in contact in a corrosive environment, causing one metal to corrode faster than the other.
- Stress Corrosion Cracking (SCC): Cracks develop in the steel due to combined tensile stress and corrosive environments, often leading to sudden failure.
Strength
Stainless steel is famous for its incredible strength. For instance, 304 stainless steel has a tensile yield strength of about 210 MPa (30,000 psi) when annealed, but this can be increased to 1,050 MPa (153,000 psi) through cold working. Heat treatment can further enhance tensile yield strengths in precipitation-hardening alloys like 17-4 PH and Custom 465, reaching up to 1,730 MPa (251,000 psi).
Melting Point
Stainless steel has a high melting point, usually between 1,400 and 1,530 °C (2,550 to 2,790 °F), depending on the alloy. This enables it to retain structural integrity at high temperatures, making it ideal for applications involving extreme heat.
Conductivity
Stainless steel has lower electrical conductivity than materials like copper due to its high protective oxide coating, which limits its use in electrical applications.
Magnetism
Stainless steel’s magnetic properties vary by type. Martensitic, duplex, and ferritic stainless steels are magnetic due to their body-centered cubic structure. Austenitic stainless steels, generally non-magnetic, can develop slight magnetism as a result of work hardening.
Wear Resistance
Stainless steel demonstrates good wear resistance, making it ideal for high-friction and high-stress applications. However, austenitic stainless steel fasteners can be prone to galling, a severe form of adhesive wear. Galling can be mitigated by using dissimilar materials or lubricating threaded joints.
Density
Stainless steel has a density that typically ranges from 7.5 to 8.0 grams per cubic centimeter, contingent on the alloy composition.
Keep reading to learn more about the key properties of stainless steel.
Is Stainless Steel Homogeneous or Heterogeneous?
Stainless steel is homogeneous because its composition is uniform throughout. The elements, like iron and chromium, are evenly distributed, giving it consistent properties across the material.
Stainless Steel Shapes
Stainless steel comes in a variety of shapes, each with distinct characteristics, production methods, and applications. Below is an overview of common stainless steel shapes:
Plate
- Overview: Flat, thick steel piece. Typically thicker than 6mm.
- Subcategories: Rectangular or square.
- Processing: Produced by hot rolling; not suitable for cold rolling.
- Specifications: Thickness starts from 6mm and higher.
- Applications: Used in heavy machinery, shipbuilding, and construction.
Sheet
- Overview: Flat, thin stainless steel, thinner than a plate.
- Subcategories: Rectangular, available in various finishes.
- Processing: Cold rolling or hot rolling.
- Specifications: Thickness ranges from 0.5mm to 6mm.
- Applications: Automotive panels, appliances, and roofing.
Strip
- Overview: Narrow, thin, flat steel, usually coiled.
- Subcategories: Coiled strips in different widths.
- Processing: Cold rolled from sheet or plate.
- Specifications: Width up to 600mm.
- Applications: Springs, fasteners, and electronic components.
Pipe
- Overview: Hollow cylindrical steel used to transport fluids or gases.
- Subcategories: Seamless and welded; round.
- Processing: Extrusion for seamless, welding for others.
- Specifications: Diameter from 6mm to 600mm.
- Applications: Plumbing, oil, and gas industries.
Tube
- Overview: Similar to pipe but used structurally.
- Subcategories: Round, square, rectangular, seamless, welded.
- Processing: Seamless or welded, cold or hot rolled.
- Specifications: Diameter varies based on shape; thickness depends on application.
- Applications: Structural components, furniture, and medical devices.
Bar
- Overview: Solid piece of stainless steel in various cross-sections.
- Subcategories: Round, square, hexagonal.
- Processing: Hot rolled, sometimes cold drawn.
- Specifications: Diameter or width typically starts from 10mm.
- Applications: Shafts, fasteners, and tools.
Rod
- Overview: Long, thin cylindrical bar.
- Subcategories: Round, square.
- Processing: Hot rolled or cold drawn.
- Specifications: Diameter usually below 10mm.
- Applications: Pins, screws, and small mechanical parts.
Wire
- Overview: Thin, flexible strand of stainless steel.
- Subcategories: Round, flat, or shaped.
- Processing: Cold drawn from rods.
- Specifications: Diameter usually less than 5mm.
- Applications: Springs, cables, and woven wire mesh.
Angle Steel
- Overview: L-shaped steel, used in construction.
- Subcategories: Equal or unequal legs.
- Processing: Hot rolled or welded.
- Specifications: Leg lengths range from 20mm to 200mm.
- Applications: Structural supports, frames, and braces.
Channel Steel
- Overview: U-shaped steel for structural purposes.
- Subcategories: Standard channel, wide flange channel.
- Processing: Hot rolled.
- Specifications: Widths vary from 40mm to 400mm.
- Applications: Beams, construction frameworks.
Rebar
- Overview: Ribbed steel bar used to reinforce concrete.
- Subcategories: Smooth or deformed.
- Processing: Hot rolled.
- Specifications: Diameter ranges from 6mm to 40mm.
- Applications: Concrete reinforcement in construction.
Mesh
- Overview: Grid of stainless steel wires or bars.
- Subcategories: Woven wire mesh, welded wire mesh.
- Processing: Welding or weaving.
- Specifications: Wire diameters vary; mesh opening sizes depend on application.
- Applications: Fencing, filters, and reinforcement for concrete structures.
What Are the Applications of Stainless Steel?
There is a wide range of applications of stainless steel across various industries, including but not limited to construction, automotive, medical, kitchenware, food and beverage, chemical and petrochemical, marine, aerospace, and energy and power generation.
Construction
Stainless steel is commonly utilized in modern architecture because of its strength and resistance to corrosion. It is ideal for structural components like bridges and facades. Additionally, its durability and low reflectivity make it suitable for cladding and roofing. Public infrastructure projects also benefit from its robustness and longevity.
Automotive
Because of its resistance to heat and corrosion, stainless steel is used extensively in vehicle exhaust systems. It is also used to create a long-lasting and appealing finish in trim and moldings. Fuel tanks and structural parts benefit from its durability and safety features.
Medical
The medical field relies heavily on stainless steel due to its biocompatibility and sterilization capabilities. It is crucial for surgical instruments, implants, and various hospital equipment that require both durability and frequent sterilization.
Kitchenware
Stainless steel is widely used for kitchenware due to its durability and hygienic properties. It is widely used for cutlery, cookware, sinks, and appliances. Its rust resistance and ease of washing make it appropriate for both commercial and home kitchens.
Food and Beverage Industry
In the food and beverage industry, stainless steel is vital for maintaining cleanliness and preventing bacterial growth. It is used in storage tanks, pipelines, and processing equipment to ensure food safety standards are met and maintained.
Chemical and Petrochemical Industries
Stainless steel is essential in chemical and petrochemical production because of its corrosion resistance and ability to handle strong chemicals. It is used in storage tanks, reaction vessels, and heat exchangers, which need to handle aggressive substances and temperature fluctuations efficiently.
Marine
Stainless steel is ideal for marine environments due to its excellent seawater corrosion resistance. It is used extensively in shipbuilding for hulls and structural components, as well as in offshore oil rigs where equipment is exposed to harsh marine conditions. Additionally, stainless steel is crucial in desalination plants, making up 20-30% of the equipment.
Aerospace
The aerospace industry benefits from stainless steel’s high strength and heat resistance. It is used in structural components and fasteners to guarantee the integrity and safety of aircraft. Engine components also use stainless steel to withstand high temperatures and stresses.
Energy and Power Generation
Stainless steel is vital in the energy sector for its ability to endure extreme conditions. It is used in turbines and boilers within power plants, including nuclear facilities. Stainless steel heat exchangers are also crucial for efficiently managing thermal energy.
How Is Stainless Steel Produced?
Stainless steel production comprises multiple important procedures, including melting and casting, forming, heat treatment, descaling, cutting and machining, and adding surface treatments.
1. Melting and Casting
Raw materials, including steel scrap and alloying elements, are melted in an electric arc furnace at temperatures exceeding 2800°F for 8-12 hours. Argon gas and oxygen are injected to remove impurities. Molten steel is subsequently cast into shapes including slabs, billets, rods, and tubes for further processing.
2. Forming
The cast stainless steel is hot rolled, which involves heating and passing it through rollers to create the desired shape and thickness. Hot rolling is done at temperatures exceeding the recrystallization temperature of steel. For precise dimensions or superior surface finishes, cold rolling is used, occurring below the recrystallization temperature.
3. Heat Treatment
Stainless steel is heat treated through annealing, which involves heating it above its crystallization point and cooling it under controlled conditions. This technique reduces internal tension, softens the steel, and increases its ductility.
4. Descaling
After annealing, the steel’s oxidized surface layer is removed through chemical means such as pickling or electro-cleaning, resulting in a bright, clean finish.
5. Cutting and Machining
Stainless steel is cut and shaped into final forms using techniques such as shearing, CNC punching, or laser cutting, depending on the material’s thickness and the desired final product.
6. Applying Surface Finishes
Various surface finishes are applied to enhance the material’s appearance and corrosion resistance. This includes grinding, polishing, buffing, and sandblasting, depending on the intended application.
How to Control the Quality of Stainless Steel?
Quality control in stainless steel production involves inspections, testing, and checks. Ensuring consistency and reliability is achieved through ISO 9001 standards.
Common Quality Control Methods and Tests
Quality control in stainless steel production involves several critical steps and methods, including visual inspections, chemical analysis, mechanical testing, non-destructive testing, dimensional checks, and corrosion resistance testing.
Ensuring Consistency and Reliability
To maintain consistency and reliability, stainless steel producers implement standardized procedures and quality management systems, such as ISO 9001. These systems document processes, track performance, and improve quality control.
By employing these rigorous quality control methods, manufacturers can ensure that the stainless steel produced is of high quality, reliable, and suitable for its intended applications.
How to Maintain and Care for Stainless Steel?
Proper storage conditions are crucial to maintaining the integrity and appearance of stainless steel. Here are key guidelines for storing stainless steel to maintain its quality and extend its lifespan:
Optimal Storage Conditions
- Dry Environment: Keep stainless steel in a dry place to avoid moisture buildup, which can cause corrosion. Make sure the storage area is well-ventilated to reduce humidity levels.
- Clean Area: Keep the storage space clean and clear of dust, dirt, and other impurities that can accumulate on the stainless steel surface and cause staining or corrosion.
- Temperature Control: Avoid exposing stainless steel to extreme hot or cold temperatures, as this can cause thermal expansion and contraction, which may lead to stress and cracking over time.
Things to Avoid
- Avoid Contact with Other Metals: Do not store stainless steel in direct contact with dissimilar metals, such as carbon steel, copper, or aluminum, as this can cause galvanic corrosion. Use plastic or wooden separators to prevent direct contact.
- No Acidic or Chloride-Containing Substances: Keep stainless steel away from acidic or chloride-containing substances, such as bleach, strong acids, or salt, as these can cause pitting and crevice corrosion. If contact happens, immediately rinse with water.
- Prevent Mechanical Damage: Avoid stacking or placing heavy objects on stainless steel surfaces that could cause scratches or dents. Use protective coverings, such as plastic wraps or cloth, to shield the surfaces from physical damage.
Best Practices for Storage
- Vertical Storage: Store large stainless steel sheets or panels vertically to prevent warping or bending. Use racks designed for vertical storage to keep the sheets separated and supported.
- Use of Protective Coatings: Consider applying a protective coating or using stainless steel-specific protective sprays to create an additional barrier against environmental factors.
- Regular Inspection: Periodically inspect stored stainless steel for any signs of corrosion, staining, or damage. Early detection allows for quick intervention to address issues.
- Labeling and Documentation: Clearly label and document the storage conditions and maintenance schedule for stainless steel items to ensure they are consistently stored and cared for according to best practices.
By adhering to these guidelines, you can ensure that your stainless steel products remain in excellent condition, free from corrosion and damage, and ready for use when needed. Proper storage is critical for extending the life and functionality of stainless steel.
Want to learn how to clean stainless steel? Please read this blog.
What Is the Importance of the Weight of Stainless Steel?
The weight of stainless steel is a critical factor in various applications, influencing structural integrity, design considerations, transportation logistics, and cost efficiency.
Structural Integrity and Strength
- Load-Bearing Capacity: The weight of stainless steel directly impacts its load-bearing capacity. Heavier stainless steel components provide greater strength and are better suited for supporting large structures or heavy loads, which is crucial in construction and engineering projects such as bridges, buildings, and industrial equipment.
- Stability and Durability: In applications where stability is essential, such as in building frameworks, bridges, and large machinery, the weight of stainless steel ensures long-term durability and resistance to environmental stressors like wind, earthquakes, and thermal expansion.
Design and Manufacturing Considerations
- Material Selection: Engineers and designers must consider the weight of stainless steel when selecting materials for their projects. A balance between strength and weight is necessary to optimize performance and cost. For example, in automotive design, lighter stainless steel grades are preferred to enhance fuel efficiency while maintaining safety and durability.
- Machining and Fabrication: The weight of stainless steel affects machining and fabrication processes. Heavier materials require more robust equipment, leading to higher manufacturing costs. Precision in cutting, welding, and assembling heavier stainless steel also necessitates advanced techniques and skilled labor.
Transportation and Installation
- Logistics and Handling: The transportation of stainless steel components is significantly influenced by their weight. Heavier loads require more energy and resources to move, impacting transportation costs. Additionally, handling heavier stainless steel components necessitates specialized equipment and safety protocols during installation to prevent accidents and ensure efficiency.
- Installation Efficiency: In construction and industrial settings, the weight of stainless steel impacts the ease and speed of installation. Lighter stainless steel options can simplify installation processes, reduce labor costs, and minimize the risk of injury. For instance, in the installation of stainless steel facades or large tanks, lighter materials facilitate quicker and safer assembly.
Application-Specific Importance
- Aerospace and Automotive Industries: In industries like aerospace and automotive, reducing component weight is critical for enhancing performance and fuel efficiency. Lighter stainless steel grades help decrease the overall weight of vehicles and aircraft, leading to better fuel economy, reduced emissions, and enhanced maneuverability.
- Consumer Products: For consumer goods like appliances, kitchenware, and furniture, the weight of stainless steel affects usability and customer satisfaction. Products that are too heavy can be and cumbersome, while those that are too light may not feel durable or high-quality. Finding the right balance ensures functionality and user comfort.
Cost Efficiency and Sustainability
- Material and Production Costs: The weight of stainless steel influences material and production costs. Heavier stainless steel may be more expensive to produce and transport, affecting the overall budget of a project. Conversely, optimizing the weight can lead to significant cost savings in raw materials, manufacturing, and logistics.
- Sustainability Considerations: Lighter stainless steel options contribute to sustainability by reducing the energy required for transportation and installation. This leads to lower carbon emissions and a smaller environmental footprint, aligning with global sustainability goals.
Understanding the importance of the weight of stainless steel helps optimize material selection, design, and application, ensuring that projects benefit from the material’s strengths while minimizing costs and environmental impact.
How to Choose the Right Stainless Steel for Your Needs?
Choosing the proper stainless steel for your purpose requires evaluating several crucial aspects, including corrosion resistance, strength, formability, and cost.
Corrosion Resistance
- Environmental Conditions: Determine what kind of environment the stainless steel will be exposed to. For marine environments or areas with high chloride exposure, grades like 316 or 2205 duplex stainless steel are ideal due to their enhanced corrosion resistance.
- Chemical Exposure: For applications involving exposure to harsh chemicals, consider super austenitic grade or high-performance alloy that can withstand aggressive environments.
Mechanical Properties
- Strength and Hardness: If high strength and hardness are required, such as in cutlery or surgical instruments, martensitic grades like 410 or 420 are suitable. For applications requiring high strength with good corrosion resistance, duplex or precipitation-hardening grades like 17-4 PH are preferable.
- Ductility and Toughness: For applications requiring high ductility and toughness, especially at low temperatures, austenitic grades like 304 or 316 are recommended.
Formability and Weldability
- Ease of Fabrication: Austenitic stainless steels (e.g., 304, 316) are noted for their high formability and weldability, making them ideal for complex shapes and extensive welding applications.
- Fabrication Constraints: Ferritic and martensitic grades have limited formability and weldability compared to austenitic grades, but they may be suitable for simpler shapes and structures where these properties are not critical.
Cost Considerations
- Budget: Balance the material’s performance with your budget. While higher alloyed grades provide better performance, they also come at a higher cost. Choose a grade that meets your application’s performance requirements without exceeding your budget.
- Lifecycle Costs: Consider the total cost of ownership, including maintenance and potential replacement costs. Investing in higher-grade stainless steel might reduce long-term costs due to lower maintenance and longer service life.
Specific Applications
- Food and Beverage Industry: For applications requiring high hygiene and ease of cleaning, such as kitchenware and food processing equipment, austenitic grades like 304 or 316 are ideal.
- Construction and Architecture: For structural components and architectural finishes, consider grades that offer good aesthetic appeal and corrosion resistance, such as 304 for general use or 316 for coastal areas.
- Medical and Pharmaceutical: For medical instruments and devices, choose grades that can withstand sterilization processes and provide biocompatibility, like 316L or specialized surgical stainless steel.
Availability and Standards
- Local Availability: Ensure the chosen stainless steel grade is readily available from suppliers in your region to avoid long lead times and high shipping costs.
- Compliance with Standards: Verify that the stainless steel complies with relevant industry standards and certifications, such as ASTM, AISI, or EN standards, to ensure quality and performance.
How to Select a Stainless Steel Supplier?
Choosing the right stainless steel supplier involves evaluating potential suppliers based on several criteria and asking the supplier the right questions.
Criteria for Choosing a Reliable Supplier
- Quality of Products: Ensure the supplier meets industry standards and certifications like ISO 9001, which guarantees quality management.
- Range of Products: Look for a supplier that offers various stainless steel grades and forms (sheets, plates, bars, etc.) to meet your needs.
- Pricing: Compare prices among suppliers to ensure competitive pricing without compromising quality.
- Lead Times and Delivery: Evaluate the supplier’s ability to deliver products on time to maintain your production schedule.
- Customer Service and Support: Choose a supplier with responsive and knowledgeable customer service for technical support and issue resolution.
- Reputation and Reliability: Research reviews and testimonials from other customers to gauge the supplier’s reliability.
- Quality Control: Assess the supplier’s quality control processes to ensure materials meet required standards.
Questions to Ask Potential Suppliers
- What certifications do you hold?
- Can you provide references from other customers?
- What is your range of stainless steel grades and products?
- What are your lead times for delivery?
- Do you offer technical support and customer service?
- What is your pricing structure?
- How do you handle quality control?
You can secure a consistent supply of high-quality materials for your projects by carefully selecting your stainless steel supplier and developing a solid working relationship with them.
What is the History and Development of Stainless Steel?
The journey to stainless steel began in the early 19th century when scientists observed the corrosion-resistant properties of chromium-iron alloys. In 1913, British metallurgist Harry Brearley invented stainless steel by adding chromium to molten iron, greatly enhancing its rust and corrosion resistance.
During the 1920s and 1930s, new grades and techniques were developed, expanding the applications of stainless steel. Innovations such as the electric arc furnace and the addition of elements like nickel and molybdenum improved its properties, making it more versatile and durable. Significant milestones include the mid-20th century introduction of the argon-oxygen decarburization (AOD) process, which improved production control and quality. Recent advancements have focused on creating superalloys for specialized uses, enhancing the material’s performance in extreme conditions.
This progression of scientific discovery and technological innovation has made stainless steel an essential material in various industries, known for its durability, resistance to corrosion, and wide range of applications.
What Are the Innovations and Future Trends in Stainless Steel?
The stainless steel industry is constantly advancing with new innovations and emerging trends focused on enhancing performance, sustainability, and expanding applications.
Advanced Manufacturing Techniques
- Additive Manufacturing (3D Printing): Enables the manufacture of complicated parts with greater design flexibility and less waste.
- Nanotechnology: Enhances properties like strength, corrosion resistance, and antimicrobial effects, useful in medical devices and high-performance components.
Sustainable Practices
- Recycling and Reusability: Improving the efficiency of recycling processes and increasing the use of recycled materials to reduce environmental impact.
- Green Manufacturing: Reducing the carbon footprint through energy-efficient methods and renewable energy sources.
Enhanced Material Properties
- Improved Corrosion Resistance: Developing new alloys for better performance in harsh environments, extending product lifespan.
- High-Strength Alloys: Creating grades with higher strength and durability, beneficial for aerospace, automotive, and construction applications.
Emerging Applications
- Medical and Healthcare: Expanding use in medical implants and surgical instruments with enhanced biocompatibility and antimicrobial properties.
- Energy Sector: Vital for renewable energy systems, such as solar, wind, and geothermal, due to its durability in extreme conditions.
Future Prospects
- Smart Stainless Steel: Integrating sensors and smart technology for structural health monitoring and real-time performance data.
- Global Demand Growth: Increasing demand in emerging markets due to infrastructure development and industrialization, particularly in India and China.
What is stainless steel made of?
Stainless steel is an alloy mainly made of iron (70-80%), at least 10.5% chromium, and elements like carbon, nickel, and molybdenum. The chromium content is crucial as it forms a thin oxide layer on the steel’s surface, preventing rust and corrosion.
What toxic substance is released when welding stainless steel?
When welding stainless steel, hexavalent chromium (Cr(VI)) can be released. This substance is toxic and poses serious health risks, including respiratory issues and an increased risk of lung cancer. When welding stainless steel, it is critical to use proper ventilation and protective equipment.
Further Reading
Toxic Substances Released During Welding Stainless Steel and Preventive Measures
Will stainless steel eventually rust?
Stainless steel is extremely resistant to corrosion, but it is not totally immune. Under harsh conditions, such as prolonged exposure to saltwater or acidic environments, stainless steel can corrode or develop surface rust. Regular maintenance and proper grade selection can mitigate this risk.
Further Reading
Will Stainless Steel Rust and How Can You Solve It?
What is 18/8 stainless steel?
18/8 stainless steel is a common type of austenitic stainless steel, also known as 304 stainless steel. The “18/8” refers to its composition, containing 18% chromium and 8% nickel. This grade is highly resistant to corrosion and durable, and it is commonly used in kitchenware and food processing equipment.
How to clean stainless steel?
To clean stainless steel, use warm water and mild detergent for routine cleaning. For tougher stains, apply a baking soda and water paste. Avoid abrasive cleaners and steel wool to prevent scratches. Dry with a gentle cloth to avoid water marks. For a polished look, use a stainless steel cleanser or a vinegar and olive oil mix.
Is stainless steel magnetic?
Stainless steel’s magnetic characteristics depend on its crystal structure. Ferritic and martensitic stainless steels are magnetic due to their body-centered cubic (BCC) or body-centered tetragonal (BCT) structures. Austenitic stainless steels, like 304 and 316, are generally non-magnetic but can become slightly magnetic when cold-worked.
What’s better stainless steel or sterling silver?
The application determines whether stainless steel or sterling silver is used. Stainless steel is more durable, resistant to corrosion, and requires less maintenance, making it ideal for everyday items like kitchenware, appliances, and medical instruments.
On the other hand, sterling silver is more aesthetically pleasing and is often used in jewelry and decorative items. However, it tarnishes over time and requires more maintenance.
For practical, high-use items, stainless steel is generally the better choice. For ornamental and decorative purposes, sterling silver may be preferred.
Conclusion
Thank you for staying with us throughout this comprehensive guide to stainless steel! We’ve covered everything from its composition and types to its diverse applications and the future of this incredible material. Now that you’re well-versed in what makes stainless steel so special, it’s time to put this knowledge to use. Whether you’re selecting the right type for your next project, maintaining your stainless steel appliances, or exploring new innovations, remember that stainless steel is all about durability, versatility, and resistance. Ready to start your stainless steel journey? Let’s get to it!
- Stainless Steel Grades
- 300 Series Stainless Steel
- 303 Stainless Steel
- 304 Stainless Steel
- 305 Stainless Steel
- 308 Stainless Steel
- 316 Stainless Steel
- 316N Stainless Steel
- 409 Stainless Steel
- 410 Stainless Steel
- 416 Stainless Steel
- 420 Stainless Steel
- 430 Stainless Steel
- 410HT And 410L Stainless Steels
- 410S Stainless Steel
- 440 Stainless Steel
- 436 Stainless Steel
- 301 Stainless Steel
- 201 Stainless Steel
- 202 Stainless Steel
- 444 Stainless Steel
- 405 Stainless Steel
- 302 Stainless Steel
- 309 Stainless Steel
- 314 Stainless Steel
- 321 Stainless Steel
- 347 Stainless Steel
- 408 Stainless Steel
- 422 Stainless Steel
- 431 Stainless Steel
- 434 Stainless Steel
- 414 Stainless Steel
- 430FR Stainless Steel
- 13-8 PH Stainless Steel
- 317 | 317L Stainless Steel
- 616 Stainless Steel
- 630 Stainless Steel
- 904L Stainless Steel
- A2 Stainless Steel
- 304 vs 304L Stainless Steel
- 304 VS 316 Stainless Steel
- 304 vs 409 Stainless Steel
- 304 vs 430 Stainless Steel
- 410 Stainless Steel vs 304
- 18/0 vs 18/10
- 18/0 Stainless Steel
- 18/8 Stainless Steel
- 18/10 Stainless Steel
Comparisons