Contents
Duplex stainless steel: Definition, Groups, Composition, Properties, Applications & More
- John
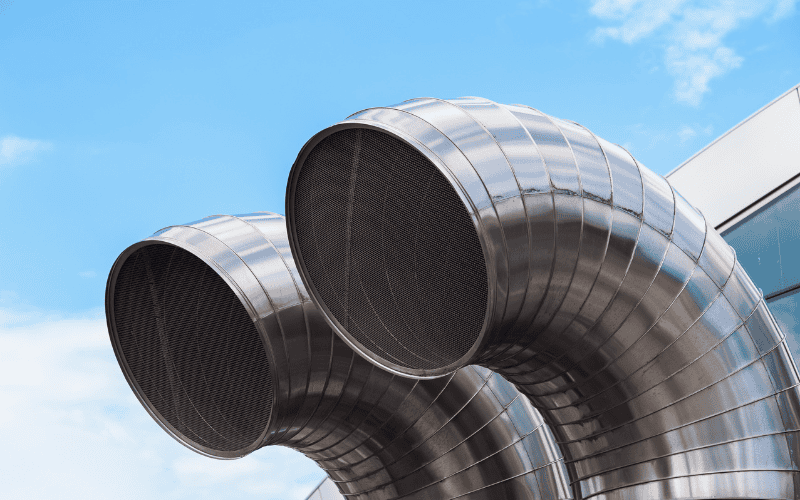
Duplex stainless steel is an important material in modern engineering. This versatile alloy is known for its dual-phase microstructure. It combines strength, corrosion resistance, and cost savings. This article will look at what makes duplex stainless steel unique, where it’s commonly used, and why it’s a top choice for many industries.
What Is Duplex Stainless Steel?
Duplex stainless steel is one of the five families of stainless steel. Its metallurgical structure is austenite and ferrite in roughly equal proportions and contains relatively high Cr and Mo. It has better corrosion resistance and higher strength than austenitic stainless steel. It is used in the offshore oil, gas, and petrochemical industry. Common grades include 2205, S39274, and S31803.
What are The Subgroups of Duplex Stainless Steels?
The duplex stainless steels are a family of grades ranging in corrosion resistance depending on the alloy content. According to alloying elements and properties, duplex stainless steel is divided into four subgroups. Each group has different pitting corrosion resistance, below we note the PREN (the pitting resistance equivalence number) range.
PREN = %Cr + 3.3 %Mo + 16 %N. The higher PREN values, the greater corrosion resistance.
Lean Duplex Stainless Grades—— (PREN range: 22-27)
Typically contains lower nickel and/or molybdenum content and higher levels of nitrogen and manganese. They have high strength, especially yield strength. They are usually used in applications such as tank construction, bridges, or tie bars. Common grades include 2101(S32101),2202(S32202) and 2304(S32304).
Standard Duplex Stainless Grades——(PREN range: 28-38)
Standard duplex stainless steels are the most used today because of their mid-range of properties. They have a chromium content of 21-25%, a molybdenum content of 2-3%, and a nitrogen content of 0.15%. Commonly in applications such as tanks, piping systems, or process vessels.
2205 (S32205) stands out as the most widely used duplex grade across various industries. It has good performance in high-pressure and highly corrosive environments due to the high yield strength and the high pitting and crevice corrosion resistance.
Super Duplex Stainless Grades——(PREN range: 38-45)
Typically contain 25% chromium, 3.5-4.0% molybdenum, and 0.25-0.27% nitrogen. They have outstanding resistance to localized pitting and crevice corrosion. They are preferred for demanding environments found in offshore oil production, chemical processing, marine applications, and offshore structures. Common grades include 2507 (S32750) and Z100 (S32760).
Hyper Duplex Stainless Grades——(PREN range: 48-57)
They have a chromium content of 26-30%, a molybdenum content of 3.5-5.0%, and a nitrogen content of 0.30-0.50%. They are the most highly alloyed within the duplex family. They are designed for extremely aggressive acid and chloride-containing environments. Currently, they are primarily available as seamless tubing. Common grades include S33207 and SAF S32707.
Common Duplex Stainless Steel Grades
2205 Duplex Stainless Steel
Duplex 2205 is the most widely used duplex stainless steel grade. It contains approximately 22% chromium, 5-6% nickel, and 3% molybdenum. Known for its excellent combination of strength and corrosion resistance.Used in various industries, including oil and gas, chemical processing, and marine environments.
2507 Duplex Stainless Steel
Duplex 2507 is a super duplex stainless steel grade. It contains about 25% chromium, 7% nickel, and 4% molybdenum. Offers enhanced corrosion resistance compared to Duplex 2205, especially in aggressive environments. Commonly used in offshore oil and gas platforms, seawater applications, and chemical processing.
2101 Duplex Stainless Steel
Duplex 2101, also known as LDX 2101, is a lean duplex stainless steel grade. It contains about 21.5% chromium, 1.5% manganese, and 0.22% nitrogen. Known for its high strength, good weldability, and excellent resistance to stress corrosion cracking.Used in various industries, including construction, transportation, and chemical processing.
2304 Duplex Stainless Steel
Duplex 2304 is duplex stainless steel with a balanced microstructure of approximately 23% chromium, 4% nickel, and 0.1% nitrogen. It offers good resistance to localized corrosion, such as pitting and crevice corrosion. Used in structural and architectural applications, as well as in marine environments.
Zeron 100 Duplex Stainless Steel
Zeron 100 is a super duplex stainless steel grade with 25% chromium, 3.5% molybdenum, and 0.25% nitrogen. It provides superior corrosion resistance in harsh environments, particularly against chloride-induced stress corrosion cracking. Commonly used in offshore oil and gas platforms, desalination plants, and chemical processing equipment.
Chemical Composition of Duplex Stainless Steel
Check the table below for the chemical composition of some common duplex stainless steels:
NAME | UNS NUMBER | C | Mn | Si | Cr | Ni | N | Cu | Mo | Group |
2202 | S32202 | 0.03 | 2.00 | 1.00 | 21.0-22.0 | 1.35-1.70 | 0.20-0.25 | 0.1-0.8 | 0.1-0.8 | Lean Duplex |
2101 | S32101 | 0.04 | 4.0-6.0 | 1 | 21.0-22.0 | 1.35-1.70 | 0.20-0.25 | 0.1-0.8 | 0.1-0.8 | |
2205 | S31803 | 0.03 | 2 | 1 | 21.0-23.0 | 4.5-6.5 | 0.08-0.20 | – | 2.5-3.4 | Standard Duplex |
S32205 | 1.4462 | 2 | 1 | 22.0-23.0 | 4.5-6.5 | 0.14-0.20 | – | 3.0-3.5 | ||
225 | S32550 | 0.04 | 1.5 | 1 | 24.0-27.0 | 4.5-6.5 | 0.10-0.25 | 1.5-2.5 | 2.9-3.9 | Super Duplex |
2507 | S32750 | 0.03 | 1.2 | 0.8 | 24.0-26.0 | 6.0-8.0 | 0.24-0.32 | 0.5 | 3.0-5.0 | |
2707 | S32707 | 0.03 | 1.5 | 0.5 | 26.0-29.0 | 5.5-9.5 | 0.30-0.50 | 1 | 4.0-5.0 | Hyer Duplex |
S33207 | – | 1.5 | 0.8 | 29.0-33.0 | 6.0-9.0 | 0.40-0.60 | 1 | 3.0-5.0 |
Duplex Stainless Steel Properties
Physical Properties
Check the table below for the physical properties of duplex stainless steels:
Physical Property | Typical Value Range |
Density | 7.8-8.0 g/cm³ |
Melting Point | 1350-1450°C |
Specific Heat Capacity | 0.4-0.6 J/(g·K) |
Thermal Conductivity | 15-20 W/(m·K) |
Electrical Conductivity | 2.0-3.0 %IACS |
Coefficient of Thermal Expansion | 11-14 µm/m·K |
Electrical Resistivity (Ω.m) | 1.0-1.2 µΩ·m |
Mechanical Properties
Check the table below for the mechanical properties of duplex stainless steels:
Physical Property | Typical Value | Typical Value |
Density | 7.8-8.0 g/cm³ | 487-500 lb/ft³ |
Melting Point | 1350-1450°C | 2462-2642°F |
Specific Heat Capacity | 0.4-0.6 J/(g·K) | 0.096-0.144 BTU/(lb·°F) |
Thermal Conductivity | 15-20 W/(m·K) | 8.7-11.6 BTU/(ft·h·°F) |
Electrical Conductivity | 2.0-3.0 %IACS | 2.0-3.0 %IACS |
Coefficient of Thermal Expansion | 11-14 µm/m·K | 6.1-7.8 µin/in·°F |
Electrical Resistivity | 1.0-1.2 µΩ·m | 1.0-1.2 µΩ·m |
One more suggestion, if your project has high requirements for mechanical properties at room temperature, you can give priority to duplex steel grades because their minimum yield stress values are twice that of austenitic stainless steel, which allows thinner sections.
Corrosion Resistance
Resistance to acids
Duplex stainless steel’s high chromium content, along with certain amounts of molybdenum and nickel, provides it with strong resistance in acidic environments.
Pitting and crevice corrosion resistance
The higher levels of chromium, molybdenum, and nitrogen give duplex stainless steel excellent performance against pitting and crevice corrosion caused by chlorides.
Stress corrosion cracking resistance
Additionally, its dual-phase structure offers an advantage in resisting chloride-induced stress corrosion cracking. When the microstructure contains more than 30% ferrite, duplex stainless steel can better withstand chloride stress corrosion cracking than 304 stainless steel.
However, due to the presence of ferrite, duplex stainless steel is susceptible to hydrogen embrittlement, which may reduce its resistance in such environments.
What Are the Pros and Cons of Duplex Stainless Steel?
Here are the advantages and benefits of martensitic stainless steel:
- Higher strength and better corrosion resistance than austenitic and ferritic stainless steels.
- Better formability under pressure than the ferritic grades and superior toughness.
- Generally requires no preheating or post-weld heat treatment, simplifying welding processes.
- Offers high strength and corrosion resistance with lower levels of costly alloying elements. This makes it cost-effective.
Here are the disadvantages and limitations:
- Compared with austenitic steels, it is more difficult to form and machine.
- Exhibit hardening and embrittlement tendencies at temperatures between 280°C to 500°C, particularly at 475°C.
- Higher initial cost compared to standard stainless steel.
What Is Duplex Stainless Steel Used for?
Common martensitic stainless steel grades and their applications are as follows:
Industry | Applications | Common Grades |
Oil and Gas | Pipes, tanks | 2205 (S32205), 2507 (S32750) |
Chemical Processing and Marine | Pipes, heat exchangers, vessels | 2205 (S32205), 2507 (S32750) |
Food Processing and Beverage | Food processing equipment | 2304 (S32304), LDX 2101 (S32101) |
Marine Engineering | Structural components, ship parts | 2507 (S32750), Z100 (S32760) |
Wastewater Treatment | Wastewater treatment equipment | 2205 (S32205), 2304 (S32304) |
Architecture and Construction | Structural components, bridges | 2205 (S32205), 2304 (S32304) |
Mining and Metallurgy | Mining equipment, metallurgical equipment | 2205 (S32205), 2507 (S32750) |
Manufacturing and Processing of Duplex Stainless steel
Essential steps in manufacturing duplex stainless steel are as follows:
Hot Working
Hot Rolling.
The cast steel is heated and passed through rollers to reduce thickness and shape it. This process improves the steel’s structure and mechanical properties.
Forging.
Forging involves compressing the heated material between dies to achieve the desired shape. This process is commonly used for thicker sections or more complex shapes.
Solution Annealing
Heat Treatment.
The steel is heated to a high temperature, typically between 1,020°C and 1,100°C, depending on the grade.
Rapid Cooling.
After heating, the steel is rapidly cooled, usually by quenching in water or air.
Cold Working (if required)
Cold Rolling.
For precise dimensions or a better surface finish, the steel may be rolled at room temperature. This step refines the steel further.
Cold Drawing.
In some cases, cold drawing may be used instead of rolling. This process pulls the steel through a die to achieve specific shapes, often used for making wire or tubes.
Final Heat Treatment
If the material has undergone significant cold working, a stress-relieving heat treatment may be performed. This involves heating the steel to a lower temperature (typically around 300°C to 400°C) to relieve internal stresses without significantly affecting the mechanical properties.
Finishing and Inspection
The steel may be cleaned and polished to remove any scale and improve its appearance and corrosion resistance.
The final product is tested for mechanical properties, corrosion resistance, and dimensions to ensure it meets standards.
Key Considerations
Precise temperature and cooling control are crucial to maintain the balance of austenitic and ferritic phases.
Proper heat treatment and cooling are necessary to prevent the formation of brittle phases that can reduce toughness and corrosion resistance.
Suggested Temperatures for Hot Forming and Annealing/Soaking
Various grades of duplex stainless steel have distinct recommended temperature ranges for hot forming and annealing/soaking:
- S32304 (1.4362)
Hot forming temperature range: 1,150 to 950 °C (2,100 to 1,740 °F)
Minimum soaking temperature: 980 °C (1,800 °F)
- S32205 (1.4462)
Hot forming temperature range: 1,230 to 950 °C (2,250 to 1,740 °F)
Minimum soaking temperature: 1,040 °C (1,900 °F)
- S32750 (1.4410)
Hot forming temperature range: 1,235 to 1,025 °C (2,255 to 1,877 °F)
Minimum soaking temperature: 1,050 °C (1,920 °F)
- S32520 (1.4507)
Hot forming temperature range: 1,230 to 1,000 °C (2,250 to 1,830 °F)
Minimum soaking temperature: 1,080 °C (1,980 °F)
- S32760 (1.4501)
Hot forming temperature range: 1,230 to 1,000 °C (2,250 to 1,830 °F)
Minimum soaking temperature: 1,100 °C (2,010 °F)
History of Duplex Stainless Steel
The 1920s: Duplex stainless steel alloys were first conceptualized, which laid the foundation.
The 1930s: The first production of duplex alloys begins. These alloys were mainly used in cast production because of their high carbon content.
Late 1960s: Metal foundries were able to produce low-carbon duplex steels with higher chromium and nickel content.
The Mid-1970s: The development of Duplex 2205 offers superior corrosion resistance. This alloy is still popular today.
Present: Continual evolution leads to diverse modern duplex stainless steel.
Other Things You Should Know About Duplex Stainless Steel
Now that you have a deeper understanding of duplex stainless steel. There are still some common issues that deserve your attention:
Does Duplex Stainless Steel Rust?
Duplex stainless steel is highly resistant to rust. But it can still rust and corrode.
Related Reading
Does Stainless Steel Rust?
Is Duplex Stainless Steel Expensive?
Duplex stainless steel can be more expensive than other types of stainless steel because it has high alloy content and is difficult to manufacture. It can also be more cost-effective because it’s stronger and has a lower nickel content.
Is Duplex Stainless Steel Magnetic?
Yes, duplex stainless steel is usually magnetic. Because its structure contains magnetic ferritic grains, it may be less magnetic than ferrite steels because it contains austenite.
Related Reading
Is Stainless Steel Magnetic?
What Is The Carbon Content of Duplex Steel?
The carbon content of duplex stainless steel is usually less than 0.04%. This low carbon content, along with high nitrogen content, helps reduce the risk of intergranular corrosion.
Is Duplex Stainless Steel Better Than 316?
Yes. Duplex stainless steel is more robust than 316. It has more resistance to chloride stress corrosion cracking.
2205 Duplex Stainless Steel VS 316
2205 duplex stainless steel offers better corrosion resistance and strength. 316 is easier to weld and provides better low-temperature toughness. 2205 is generally used in more demanding environments, while 316 is common in marine and industrial applications.
What Is The Difference Between 2205 and 2507 Duplex Stainless Steel?
Duplex stainless steel 2507 has better strength, corrosion resistance, and hardness than 2205. Its strength is also higher. But duplex stainless steel 2205 costs less.
Summary & Furthermore
This article briefly explains the definition of duplex stainless steel, its composition, properties, grades, applications, and other important aspects. To learn more about stainless steel or other steel types, check out our blog or contact our metal experts.
As a leading manufacturer and solutions provider of specialty steel, we deliver multi-industry application solutions and customized services with a 100% quality guarantee, committed to growing together with our customers. Visit our website to learn more, or send us a quote, and we will contact you shortly!
- Stainless Steel Grades
- 300 Series Stainless Steel
- 303 Stainless Steel
- 304 Stainless Steel
- 305 Stainless Steel
- 308 Stainless Steel
- 316 Stainless Steel
- 316N Stainless Steel
- 409 Stainless Steel
- 410 Stainless Steel
- 416 Stainless Steel
- 420 Stainless Steel
- 430 Stainless Steel
- 410HT And 410L Stainless Steels
- 410S Stainless Steel
- 440 Stainless Steel
- 436 Stainless Steel
- 301 Stainless Steel
- 201 Stainless Steel
- 202 Stainless Steel
- 444 Stainless Steel
- 405 Stainless Steel
- 302 Stainless Steel
- 309 Stainless Steel
- 314 Stainless Steel
- 321 Stainless Steel
- 347 Stainless Steel
- 408 Stainless Steel
- 422 Stainless Steel
- 431 Stainless Steel
- 434 Stainless Steel
- 414 Stainless Steel
- 430FR Stainless Steel
- 13-8 PH Stainless Steel
- 317 | 317L Stainless Steel
- 616 Stainless Steel
- 630 Stainless Steel
- 904L Stainless Steel
- A2 Stainless Steel
- 304 vs 304L Stainless Steel
- 304 VS 316 Stainless Steel
- 304 vs 409 Stainless Steel
- 304 vs 430 Stainless Steel
- 410 Stainless Steel vs 304
- 18/0 vs 18/10
- 18/0 Stainless Steel
- 18/8 Stainless Steel
- 18/10 Stainless Steel
Comparisons