Contents
317 | 317L Stainless Steel: Forms, Composition, Properties, Application, Process and All
- John
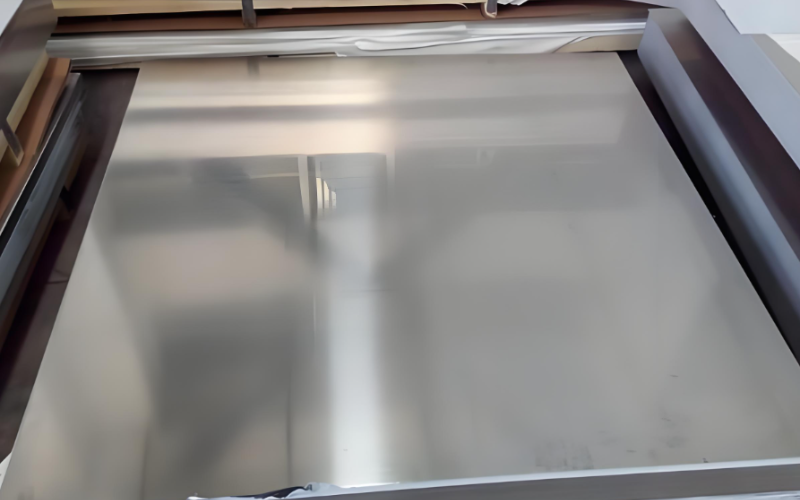
We will introduce to you in detail the composition, properties, application fields, processing methods, advantages and disadvantages of 317 stainless steel and explain its low-carbon version 317L stainless steel. In addition, we will compare the differences between 304, 316 and 317 stainless steel to help you better choose the right material.
What is 317 Stainless Steel?
317 stainless steel, an austenitic alloy, boasts heightened concentrations of chromium, nickel, and molybdenum, imparting superior corrosion resistance, especially in chloride-rich environments. It has found widespread usage across various industries, such as chemical processing, pulp and paper production, marine engineering, as well as food processing.
Equivalent Grades of 317 Stainless Steel
- UNS: S31700
- EN: X3CrNiMo18-12-3 (1.4449)
- JIS: SUS317
317 Standards
- ASTM A240
- ASTM A276
- ASTM A312
- ASTM A479
Chemical Composition of 317 Stainless Steel
317 stainless steel contains high levels of chromium, nickel and molybdenum, which provides excellent corrosion resistance and strong mechanical properties.
Element | Composition Range |
Carbon (C) | ≤ 0.08% |
Manganese (Mn) | ≤ 2.00% |
Silicon (Si) | ≤ 1.00% |
Chromium (Cr) | 18.0% – 20.0% |
Nickel (Ni) | 11.0% – 15.0% |
Molybdenum (Mo) | 3.0% – 4.0% |
Nitrogen (N) | ≤ 0.10% |
Sulfur (S) | ≤ 0.03% |
Phosphorus (P) | ≤ 0.045% |
Properties of 317 Stainless Steel
Key Features
The key features of 317 stainless steel are its excellent corrosion resistance, strength and machinability, making it an excellent performer in demanding environments.
Corrosion Resistance: The high content of chromium and molybdenum makes 317 stainless steel extremely resistant to chloride corrosion environments, especially in acidic environments such as sulfuric acid and hydrochloric acid.
Strength: The tensile strength and yield strength of 317 stainless steel are higher than ordinary stainless steels, which enables it to maintain good structural integrity even under high temperature conditions.
Oxidation Resistance: 317 stainless steel exhibits exceptional oxidation resistance in high-temperature settings, enabling it to maintain stability without undergoing oxidation or degradation even at temperatures reaching 1600°F (870°C).
Physical Properties of 317 Stainless Steel
Property | Metric | Imperial |
Density | 7.99 g/cm³ | 0.289 lb/in³ |
Thermal Conductivity (at 100°C) | 16.2 W/m·K | 9.4 BTU·in/hr·ft²·°F |
Electrical Resistivity (at 20°C) | 85 microhm-cm | 33.5 microhm-in |
Melting Point | 1371 – 1421 °C | 2500 – 2590 °F |
Specific Heat (32-212°F) | 0.50 kJ/kg·K | 0.12 BTU/lb·°F |
Thermal Expansion (32-212°F) | 16.0 µm/m·K | 8.9 in/in·°F |
These chemical properties give 317 stainless steel excellent thermal and electrical properties, especially in high temperature applications and electrical resistance environments.
Mechanical Properties of 317 Stainless Steel
Property | Metric | Imperial |
Tensile Strength | 620 MPa | 89900 psi |
Yield Strength | 275 MPa | 39900 psi |
Elongation | 35% | 35% |
Hardness (Rockwell B) | Max 95 | Max 95 |
Modulus of Elasticity (Tension) | 193 GPa | 28 x 10³ ksi |
Modulus of Elasticity (Torsion) | 77 GPa | 11.2 x 10³ ksi |
The mechanical properties of 317 stainless steel make it an ideal choice for many industrial applications that require high strength and toughness, especially in high pressure and high temperature environments.
Forms of 317 Stainless Steel
SteelPRO Group offers a wide variety of 317 stainless steel including:
- 317 Stainless steel plates, sheets, coils, wires
- 317 Stainless steel bars (round, square, flat), rods, angles, channels, pipes (seamless and welded), tubes (seamless and welded)
- 317 Stainless steel fittings, flanges, billets, forgings
We also provide customized size and processing services to meet your various needs.
Applications of 317 Stainless Steel
317 stainless steel is well suited for a variety of critical applications due to its ability to withstand highly corrosive environments, especially those containing chlorides or sulfur compounds..
Chemical and Petrochemical Processing: The excellent resistance to pitting and crevice corrosion of 317 stainless steel makes it very suitable for equipment in chemical plants that are often exposed to acidic and chlorine-containing environments, such as tanks, heat exchangers and pipelines.
Pulp and Paper Industry: The production of paper involves the use of highly corrosive chemicals, including chlorine compounds. 317 stainless steel is widely used in this industry for processing equipment, where resistance to acidic environments is crucial.
Food and Beverage Processing: 317 stainless steel is commonly found in food processing plants, where hygiene and corrosion resistance are critical due to the exposure to organic acids and cleaning agents.
Marine Environments: Components exposed to saltwater and marine environments benefit from the enhanced corrosion resistance of 317 stainless steel, which reduces the risk of pitting caused by chlorides.
Power Generation: In power plants, particularly fossil and nuclear stations, 317 stainless steel is used in condensers and heat exchangers due to its ability to withstand both high temperatures and corrosive environments.
Pros and Cons of 317 Stainless Steel
Advantages
- Superior Corrosion Resistance: 317 stainless steel outperforms 304 and 316 stainless steels in environments containing chlorides and acidic compounds.
- High Temperature Strength: This alloy maintains its strength and structural integrity even in high-temperature conditions, making it suitable for applications in heat exchangers and power plants.
- Good Formability: Despite its high strength, 317 stainless steel can be easily formed and shaped, which makes it ideal for various manufacturing processes.
Disadvantages
- Higher Cost: The increased cost of 317 stainless steel compared to 304 and 316 grades is attributed to its higher concentrations of nickel and molybdenum.
- Limited Performance in Certain Acids: While it performs exceptionally well in many corrosive environments, 317 stainless steel is not the best choice for applications involving strong oxidizing acids, such as concentrated nitric acid.
What are the Processing Methods of 317 Stainless Steel?
The processing of 317 stainless steel involves several techniques that allow it to be formed, welded, and treated for a variety of applications. Understanding these processes is important for ensuring the material performs as expected in its intended use.
Forming
317 stainless steel can be formed by cold working and hot working. Due to its good ductility, it can maintain mechanical properties during drawing, stamping and forming.
Welding
317 stainless steel has good weldability, but due to its high molybdenum content, it may be necessary to use low-carbon welding materials or molybdenum-containing filler materials to reduce the corrosion sensitivity of the weld. Conventional fusion welding and resistance welding methods can be used, including manual welding (such as TIG and MIG welding) and automated welding.
Annealing treatment can be performed after welding to eliminate stress and carbide precipitation that may occur in the heat-affected zone and prevent corrosion at the weld.
Cutting
317 stainless steel has high hardness and strong wear resistance. When cutting, a lower cutting speed is required, using carbide tools or high-speed steel tools. Plasma cutting, laser cutting and mechanical cutting (such as shearing or sawing) can be used for processing.
During the cutting process, care should be taken to prevent overheating of the heat-affected zone to avoid affecting the corrosion resistance of the material.
Hot Working
317 stainless steel has good plasticity and ductility at high temperatures and is suitable for hot forming processes such as forging and rolling.
Forging: between 927°C and 1204°C (1700°F and 2200°F), with 1177°C (2150°F) being the recommended temperature for forging.
Rapid cooling is required after hot working to maintain the corrosion resistance of the material. Avoid prolonged exposure to temperatures between 540°C and 760°C, as this may result in material degradation.
Cold Working
317 stainless steel has good cold working properties, although significant work hardening occurs during processing. Cold forming operations including cold rolling, cold drawing and bending can be performed.
The hardness and strength of the material after cold working increase, but the ductility decreases. To restore its toughness and ductility, appropriate intermediate annealing can be performed.
Heat Treatment
317 stainless steel can restore its corrosion resistance and toughness through solution treatment, but cannot be hardened by heat treatment.
Solution annealing is the main heat treatment method, which heats the material to 1010°C to 1121°C (1850°F to 2050°F) and then quenches it rapidly.
Rapid cooling helps prevent intergranular corrosion, especially for the treatment of weld areas.
Surface Treatment
317 stainless steel can be supplied in a variety of surface finishes, depending on the application. Common finishes include:
- No. 1 Finish: A rough finish used where a smooth surface is not necessary.
- 2B Finish: A bright, smooth finish achieved by cold rolling and annealing.
- BA (Bright Annealed) Finish: A glossy finish used for decorative or clean applications.
What is the Difference Between 304, 316, and 317 Stainless Steel?
The key differences between 304, 316, and 317 stainless steels are in their molybdenum content, which enhances resistance to pitting and crevice corrosion, particularly in chloride-rich environments.
Grade | Mo (%) | Corrosion Resistance | Applications |
304 | None | Basic corrosion resistance | General-purpose, household items |
316 | 2 – 3 | Better resistance to chlorides | Chemical, marine, medical |
317 | 3 – 4 | Superior resistance to chlorides | Chemical, paper, marine |
What is 317L Stainless Steel?
317L stainless steel, as the carpet version of 317, is austenitic and has excellent corrosion resistance, especially in chloride-containing and acidic environments. Its low-carbon design reduces the risk of carbide precipitation after welding and enhances resistance to intergranular corrosion. It is suitable for use under high temperature and highly corrosive conditions, such as chemical, marine, food processing and other industries.
Equivalent Grades of 317L Stainless Steel
- UNS: S31703
- EN: X2CrNiMo18-15-4 (1.4438)
- JIS: SUS317L
317 Standards
- ASTM A479
- ASTM A240
- ASTM A276
- ASTM A312
- ASTM A182
317L Chemical Composition
Element | Composition Range |
Carbon (C) | ≤ 0.03% |
Manganese (Mn) | ≤ 2.00% |
Silicon (Si) | ≤ 1.00% |
Chromium (Cr) | 18.0% – 20.0% |
Nickel (Ni) | 11.0% – 15.0% |
Molybdenum (Mo) | 3.0% – 4.0% |
Nitrogen (N) | ≤ 0.10% |
Sulfur (S) | ≤ 0.03% |
Phosphorus (P) | ≤ 0.045% |
Forms of 317L Stainless Steel
SteelPRO Group offers a wide range of 317L stainless steel products, including:
- 317L stainless steel plates, coils, sheets, wires
- 317L stainless steel round bars, square bars, flat bars, angles, channels, pipe, tubing, seamless and welded tubes
- 317L stainless steel fittings, flanges, billets and forgings
We also provide customers with customized sizes and processing services to meet various special application requirements.
Welding of 317L Stainless Steel
With excellent welding performance, 317L is weldable by regular welding methods such as fusion welding, resistance welding, and so on. Due to its low carbon content, no carbide precipitation will occur during welding, thus avoiding intergranular corrosion, so post-weld heat treatment is usually not required.
When welding, it is recommended to use AWS E317L or ER317L filler metal that matches the base material to ensure the best corrosion resistance and welding effect.
What is the Difference Between 316, 316L, and 317L Stainless Steel?
The main differences between 316, 316L and 317L are the molybdenum content and corrosion resistance.
317L contains more molybdenum, making it more corrosion resistant than 316 and 316L in harsh chloride and acid environments. The low carbon content of 316L prevents intergranular corrosion when welding, while 317L has the same low carbon advantage and performs better in highly corrosive environments.
Is 317L Magnetic?
In its annealed state, 317L stainless steel exhibits non-magnetic properties. However, following cold working or welding processes, it may develop slight magnetic characteristics, although these are typically not significant enough to compromise the majority of its applications.
317 & 317L Stainless Steel Manufacturer
SteelPRO Group is a 317 and 317L stainless steel manufacturer and supplier, providing high-quality customizable steel parts and reliable after-sales services.
By choosing us as your trusted partner, you will benefit from our more than 17 years of manufacturing experience, more than 1 million tons of annual production capacity, and 100% quality commitment. We offer factory direct prices, a full range of specifications and sufficient inventory, ensure timely delivery, and support customized solutions to meet your various needs.
Contact us now or continue browsing our blog to explore your exclusive solution.
- Stainless Steel Grades
- 300 Series Stainless Steel
- 303 Stainless Steel
- 304 Stainless Steel
- 305 Stainless Steel
- 308 Stainless Steel
- 316 Stainless Steel
- 316N Stainless Steel
- 409 Stainless Steel
- 410 Stainless Steel
- 416 Stainless Steel
- 420 Stainless Steel
- 430 Stainless Steel
- 410HT And 410L Stainless Steels
- 410S Stainless Steel
- 440 Stainless Steel
- 436 Stainless Steel
- 301 Stainless Steel
- 201 Stainless Steel
- 202 Stainless Steel
- 444 Stainless Steel
- 405 Stainless Steel
- 302 Stainless Steel
- 309 Stainless Steel
- 314 Stainless Steel
- 321 Stainless Steel
- 347 Stainless Steel
- 408 Stainless Steel
- 422 Stainless Steel
- 431 Stainless Steel
- 434 Stainless Steel
- 414 Stainless Steel
- 430FR Stainless Steel
- 13-8 PH Stainless Steel
- 317 | 317L Stainless Steel
- 616 Stainless Steel
- 630 Stainless Steel
- 904L Stainless Steel
- A2 Stainless Steel
- 304 vs 304L Stainless Steel
- 304 VS 316 Stainless Steel
- 304 vs 409 Stainless Steel
- 304 vs 430 Stainless Steel
- 410 Stainless Steel vs 304
- 18/0 vs 18/10
- 18/0 Stainless Steel
- 18/8 Stainless Steel
- 18/10 Stainless Steel
Comparisons