Contents
316N Stainless Steel: Definition, Composition, Properties, Applications, Processing and More
- John
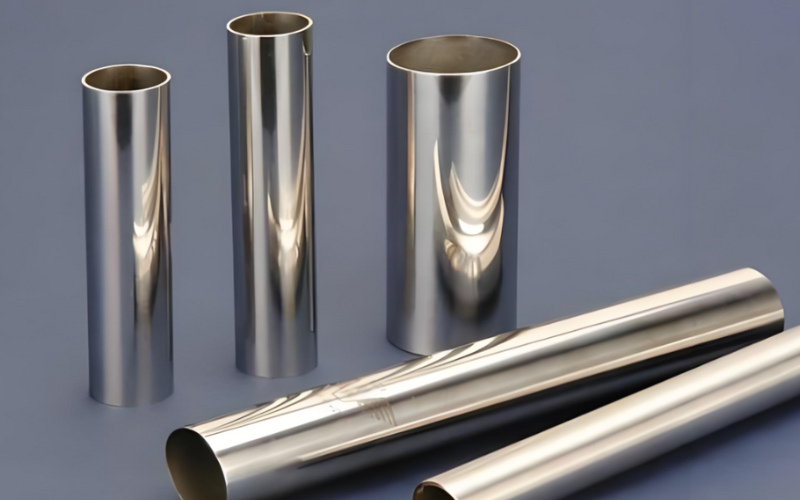
Among the various types of stainless steels, 316N stands out due to its superior mechanical properties and enhanced resistance to high-temperature environments. This article delves into the detailed aspects of 316N stainless steel, covering its definition, chemical composition, properties, applications, processing methods, and comparison with other types such as 316 and 316L.
What is 316N Stainless Steel?
316N stainless steel is a molybdenum-containing austenitic stainless steel used primarily in industrial, construction and transportation applications. It is easily formed and welded and has excellent corrosion resistance, but will suffer from surface corrosion in warm seawater. Due to the increased nitrogen content, it has a higher tensile strength than conventional 316 grade stainless steel.
Equivalent Grades of 316N Stainless Steel
- UNS: S31651
- DIN: 1.4429
- EN: X2CrNiMo17-12-3
- JIS: SUS 316LN
Standards of 316N Stainless Steel
- ASTM A240
- ASTM A276
- EN 10088-2
- JIS G4303
Chemical Composition of 316N Stainless Steel
The chemical composition of 316N stainless steel is as follows:
Element | Composition Range |
Carbon (C) | ≤ 0.08% |
Manganese (Mn) | ≤ 2.00% |
Silicon (Si) | ≤ 1.00% |
Chromium (Cr) | 16.0% – 18.0% |
Nickel (Ni) | 10.0% – 14.0% |
Molybdenum (Mo) | 2.0% – 3.0% |
Nitrogen (N) | 0.10% – 0.20% |
Sulfur (S) | ≤ 0.03% |
Phosphorus (P) | ≤ 0.045% |
Properties of 316N Stainless Steel
Key Features
316N stainless steel offers several key features that make it suitable for a range of demanding applications.
- High Tensile Strength: Due to its nitrogen content, 316N exhibits superior strength compared to standard 316 stainless steel, especially at elevated temperatures.
- Good Ductility: 316N maintains excellent ductility despite its high strength and is applicable to a wide range of moulding processes.
- Corrosion Resistance: Like other 316-grade steels, 316N shows excellent resistance to corrosion in a wide variety of environments, including exposure to chlorides and saltwater.
- Excellent Weldability: This material can be welded using all standard welding methods, and post-weld annealing is not necessary in most cases.
- Non-Magnetic in Annealed State: Stainless steel 316N in the annealed condition is non-magnetic, but during cold working it becomes slightly magnetic.
Physical Properties
The chemical properties of 316N stainless steel include its response to corrosion, heat, and other environmental factors:
Physical Property | Value |
Maximum Corrosion Temperature | 410°C (770°F) |
Melting Range | 1400°C – 1440°C |
Thermal Conductivity | 15 W/m-K |
Specific Heat Capacity | 470 J/kg-K |
Electrical Resistivity | 8.5E – 7Ω·m |
Density | 7.9 g/cm³ |
Mechanical Properties
The mechanical properties of 316N stainless steel are crucial for its performance in high-stress environments:
Mechanical Property | Value |
Tensile Strength (UTS) | 550 – 620 MPa |
Yield Strength | 240 MPa |
Elongation | 30 – 35% |
Hardness (Rockwell B) | 95 (Max) |
Poisson’s Ratio | 0.27 – 0.30 |
Modulus of Elasticity | 196 GPa |
Forms of 316N Stainless Steel
After undergoing the various processing methods, 316N stainless steel is available in a wide range of product forms to suit different industrial applications.
- Plates and Sheets: Used in construction, chemical processing, and marine industries due to their corrosion resistance and ease of fabrication.
- Pipes and Tubes: Common in petrochemical and pharmaceutical industries for transporting corrosive substances. Welded and seamless pipes are available in different sizes.
- Bars and Rods: Used in manufacturing mechanical components such as fasteners, shafts, and structural supports.
- Fittings and Flanges: Often used in piping systems, these components are manufactured from 316N stainless steel to provide strong, corrosion-resistant connections.
- Coils and Strips: These forms are ideal for applications requiring precision and consistency, such as in automotive, aerospace, and electronics industries.
Application of 316N Stainless Steel
316N stainless steel is widely used in industries where both strength and corrosion resistance are paramount.
Chemical and Petrochemical Processing: 316N is ideal for use in processing plants that handle corrosive substances such as chemicals, acids, and salts.
Marine Environments: It has become the preferred choice for marine applications due to its excellent resistance to seawater corrosion.
Food and Beverage Processing: The corrosion resistance of 316N stainless steel also makes it suitable for use in equipment for food and beverage production, where hygiene and resistance to cleaning agents are important.
Pharmaceutical Industry: 316N is used in pharmaceutical processing equipment for its chemical resistance and ease of cleaning.
Heat Exchangers: Its high thermal conductivity and mechanical strength at elevated temperatures make 316N perfect for heat exchangers.
Architectural Components: For structures exposed to marine environments or industrial pollution, 316N offers durability and aesthetics.
Aircraft Industry: It is used in components that require high strength and corrosion resistance in the aircraft industry.
Pros and Cons of 316N Stainless Steel
Advantages
- High strength due to nitrogen addition
- Excellent corrosion resistance, especially in chloride environments
- Good ductility and formability
- Non-magnetic in annealed state
- Excellent weldability
Disadvantages
- Higher cost compared to other stainless steels like 304
- Slight magnetism when cold worked
- Under certain conditions, such as warm seawater, it is more susceptible to surface corrosion than 316L
What Are the Processing Methods of 316N Stainless Steel?
The mechanical properties, corrosion resistance and surface finish of 316N stainless steel can be enhanced through proper processing techniques such as welding, heat treatment and surface treatment.
Forming
316N stainless steel has excellent formability and is suitable for a range of manufacturing processes such as bending, rolling and stamping. The nitrogen content in 316N helps to retain ductility while enhancing its strength, allowing it to be formed into complex shapes without the risk of cracking or breaking.
Cold Forming: Cold forming processes, such as cold rolling or cold drawing, can be used to enhance the strength and hardness of 316N. Cold working increases the alloy’s yield strength while also introducing slight magnetism to the material. Common products made through cold forming include wires, sheets, and rods.
Hot Forming: Hot forming, where the material is heated to a high temperature (above its recrystallization point), is used when significant deformation is required. After hot forming, 316N is typically annealed to restore its original ductility and corrosion resistance.
Welding
Welding is one of the most common processing methods for stainless steels, including 316N. One of the benefits of 316N stainless steel is its excellent weldability, allowing it to be joined by all standard fusion methods such as Gas Tungsten Arc Welding (GTAW), Gas Metal Arc Welding (GMAW), and Shielded Metal Arc Welding (SMAW).
Fusion Welding: 316N can be welded without the need for pre-heating, which reduces the risk of thermal cracking. Post-weld annealing is generally not required for thin sections, as 316N exhibits minimal sensitization (which can lead to intergranular corrosion) due to its low carbon content. However, for thicker sections, post-weld heat treatment may be recommended to relieve internal stresses.
Laser and Electron Beam Welding: These advanced welding techniques can also be applied to 316N stainless steel, especially in industries such as aerospace and automotive manufacturing where precision and minimal thermal distortion are required.
Resistance Welding: Techniques like spot welding and seam welding are commonly applied to stainless steels. In resistance welding, heat is produced by running an electrical current through the material, leading to localized melting at the joint area. This process is particularly effective for joining thin sheets of 316N stainless steel.
Forging
Forging is another essential processing method used to shape stainless steel products. For 316N stainless steel, the forging temperature typically ranges between 1150°C and 1260°C (2100°F to 2300°F).
Open Die Forging: The process is to heat the steel to a certain temperature to make it pliable and then hammer it into the desired shape. The material is worked between large flat dies, which shape the metal in rough forms such as billets or bars.
Closed Die Forging: This process, also named compression die forging, is used to create more precise and complex shapes like gears, shafts, and fittings. The metal is placed in a die shaped like the final product, and as it is compressed, it fills the cavity to take on the exact shape.
After forging, annealing is often necessary to improve the material’s ductility and restore its corrosion resistance.
Hardening
316N stainless steel is non-hardenable through traditional heat treatment methods. Unlike martensitic stainless steels, 316N does not undergo phase transformations that would allow it to be hardened through heating and quenching.
However, cold working processes such as cold rolling or drawing can significantly increase the hardness and strength of 316N. Cold working induces strain hardening, which enhances the tensile strength of the material, though it may slightly reduce its ductility. Additionally, cold working can lead to the formation of slight magnetism in the material, which is otherwise non-magnetic in its annealed state.
Heat Treatment
Heat treatment is a crucial processing step in stainless steel manufacturing to refine the material’s microstructure and mechanical properties.
Annealing: For 316N stainless steel, the typical annealing temperature is between 1010°C and 1120°C (1850°F to 2050°F), followed by rapid cooling to restore the material’s ductility and remove internal stresses caused by cold working. Annealing also improves the steel’s resistance to corrosion by dissolving carbides that could otherwise lead to intergranular corrosion. In the annealed condition, 316N stainless steel is non-magnetic.
Stress Relieving: Stress relieving is performed at temperatures between 800°C and 900°C (1470°F and 1650°F) to eliminate residual stresses that can negatively affect the product and is typically applied to 316N stainless steel after heavy forming or welding operations.
Solution Treatment: Solution treatment is the heating of steel to high temperatures followed by rapid cooling to retain alloying elements in solution. It can restore the corrosion resistance of steel, particularly after exposure to high temperatures during processing.
Surface Treatment
Surface treatments are applied to 316N stainless steel to enhance its aesthetic appeal, improve corrosion resistance, or prepare it for further processing.
Pickling: Pickling is a surface treatment method used to remove oxide scales and impurities formed during hot working or welding. It involves dipping the material in an acid solution to clean the surface and restore the passive chromium oxide layer that protects against corrosion.
Passivation: The material’s corrosion resistance can be further enhanced by the passivation process, in which the steel is treated with a mild oxidising acid, such as nitric acid, to strengthen the naturally occurring chromium oxide layer on the steel’s surface.
Polishing: Mechanical polishing can be applied to improve the surface finish of 316N stainless steel, especially for applications where cleanliness is important, such as in food processing or pharmaceutical industries. Polishing also enhances the steel’s resistance to surface corrosion.
Electropolishing: Electropolishing removes a thin layer of material from the surface of stainless steel through an electrochemical process. It improves corrosion resistance, creates a smooth, shiny surface, and removes small imperfections that could harbor bacteria or contaminants.
What Is the Difference between 316 and 316N?
316N stainless steel differs from 316 primarily due to the addition of nitrogen in the alloy. This addition increases the tensile strength of 316N while retaining ductility or corrosion resistance. As a result, 316N is often chosen for applications where strength is a critical factor, especially in high-temperature environments.
- Strength: 316N has higher strength than 316 due to its nitrogen content.
- Ductility: Both alloys offer good ductility, but 316N’s strength advantage gives it an edge in demanding applications.
- Corrosion Resistance: 316N performs better in high stress environments, although both materials exhibit excellent corrosion resistance.
316N vs 316L
316N and 316L are similar in many respects, but they have distinct differences:
- Carbon Content: 316L has a lower carbon content (≤0.03%) compared to 316N (≤0.08%). This makes 316L more resistant to sensitization, which is beneficial in welding applications.
- Strength: 316N offers higher strength than 316L due to its nitrogen content.
- Corrosion Resistance: 316L is more resistant to intergranular corrosion in welded sections, while 316N offers better overall strength.
Is 316N Stainless Steel Magnetic?
No. 316N stainless steel is generally considered non-magnetic in the annealed condition, however, if it undergoes significant cold working or deformation it may exhibit slight magnetism.
Will 316N Stainless Steel Rust?
Although 316N is considered a “marine grade stainless steel”, it still has limited corrosion resistance in these harsh conditions. In warm chloride environments, pitting and crevice corrosion will occur above about 60°C, and stress corrosion cracking will occur, which will appear as brown staining. Chemical attack in highly acidic environments may also affect it.
Get Satisfactory Stainless Steel!
By understanding its composition, properties, and processing methods, you can take advantage of 316N stainless steel and apply it to a wide range of applications from petrochemical processing to architectural design. If you need to purchase 316N stainless steel and other steel materials, please feel free to contact us for high-quality products at a great price. If you want to learn more about stainless steel, click here to browse our blog.
- Stainless Steel Grades
- 300 Series Stainless Steel
- 303 Stainless Steel
- 304 Stainless Steel
- 305 Stainless Steel
- 308 Stainless Steel
- 316 Stainless Steel
- 316N Stainless Steel
- 409 Stainless Steel
- 410 Stainless Steel
- 416 Stainless Steel
- 420 Stainless Steel
- 430 Stainless Steel
- 410HT And 410L Stainless Steels
- 410S Stainless Steel
- 440 Stainless Steel
- 436 Stainless Steel
- 301 Stainless Steel
- 201 Stainless Steel
- 202 Stainless Steel
- 444 Stainless Steel
- 405 Stainless Steel
- 302 Stainless Steel
- 309 Stainless Steel
- 314 Stainless Steel
- 321 Stainless Steel
- 347 Stainless Steel
- 408 Stainless Steel
- 422 Stainless Steel
- 431 Stainless Steel
- 434 Stainless Steel
- 414 Stainless Steel
- 430FR Stainless Steel
- 13-8 PH Stainless Steel
- 317 | 317L Stainless Steel
- 616 Stainless Steel
- 630 Stainless Steel
- 904L Stainless Steel
- A2 Stainless Steel
- 304 vs 304L Stainless Steel
- 304 VS 316 Stainless Steel
- 304 vs 409 Stainless Steel
- 304 vs 430 Stainless Steel
- 410 Stainless Steel vs 304
- 18/0 vs 18/10
- 18/0 Stainless Steel
- 18/8 Stainless Steel
- 18/10 Stainless Steel
Comparisons