Contents
347 Stainless Steel: Composition, Properties, Applications, Forms, Processing, Comparison, and More
- John
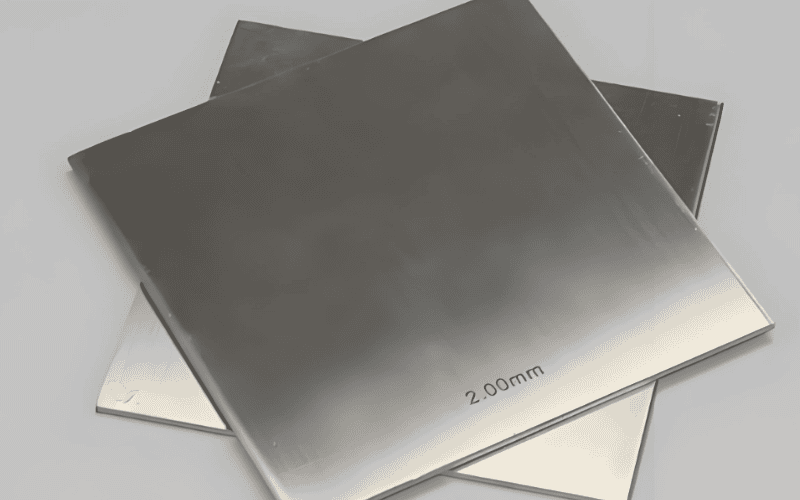
In this article, we’ll take a deep dive into the composition, properties, applications, pros and cons, forms, and processing of 347 stainless steel while comparing it to other popular stainless steels like 316, 304, and 321. Whether you’re a manufacturer, engineer, or supplier, understanding the benefits of 347 stainless steel will help you make the best material choice for your project.
What is 347 Stainless Steel?
347 stainless steel is an austenitic chromium-nickel stainless steel alloy stabilized with niobium (columbium) to prevent the precipitation of chromium carbides. This alloy stands out for its excellent resistance to intergranular corrosion at high temperatures, especially in the 800-1500°F range. It is commonly used in chemical processing, high temperature exhaust systems and boiler piping.
347 stainless steel equivalent grades
- UNS S34700
- WNR 1.4550
- DIN X10CrNiNb18-9
- BS 347S17
- SAE 30347
347 stainless steel standard
ASTM A240, ASTM A182, ASTM A276, ASTM A312, ASTM A358, ASTM A403
Chemical Composition of 347 Stainless Steel
Element | Composition Range |
Carbon (C) | ≤ 0.08% |
Manganese (Mn) | ≤ 2.00% |
Silicon (Si) | ≤ 1.00% |
Chromium (Cr) | 17.0% – 19.0% |
Nickel (Ni) | 9.0% – 13.0% |
Sulfur (S) | ≤ 0.030% |
Phosphorus (P) | ≤ 0.045% |
Niobium (Nb) + Tantalum (Ta) | 10x C min – 1.0% max |
347 Stainless Steel Properties
Key Features
High-Temperature Stability: Can withstand prolonged exposure to high temperatures (up to 1500°F/816°C) without losing mechanical integrity.
Resistance to Intergranular Corrosion: The niobium stabilization prevents carbide precipitation, avoiding sensitization and degradation in corrosive environments.
Superior Weldability: It can be easily welded using most standard methods, with little need for post-weld heat treatment.
Excellent creep strength: It has strong resistance to creep deformation under long-term high stress conditions.
Physical Properties
Property | Value |
Density | 7.7 – 8.03 g/cm³ (0.278 – 0.290 lb/in³) |
Melting Point | 1371 – 1400°C (2500 – 2550°F) |
Thermal Conductivity | 16.3 W/m·K (212°F) |
Coefficient of Thermal Expansion | 10.5 x 10⁻⁶/°C (20-600°C) |
Electrical Resistivity | 72 µΩ·cm (20°C) |
Specific Heat | 500 J/kg·K (0 – 100°C) |
Mechanical Properties
Property | Value |
Tensile Strength (UTS) | 515 MPa min (75 ksi min) |
Yield Strength (0.2% Offset) | 205 MPa min (30 ksi min) |
Elongation | 40% min |
Hardness (Brinell) | 201 max |
Hardness (Rockwell B) | 95 max |
Modulus of Elasticity | 190 – 210 GPa (27557 – 30458 ksi) |
Poisson’s Ratio | 0.27 – 0.30 |
Creep Strength (at 750°C) | 38 – 39 MPa (5510 – 5660 psi) |
Rupture Strength (at 750°C) | 38 – 39 MPa (5510 – 5660 psi) (100,000 hours) |
Impact Toughness (Charpy V-notch) | 60 J (Longitudinal) / 40 J (Transverse) |
Fatigue Strength (Rotating Bending, at 20°C) | 240 MPa (34.8 ksi) |
Forms of 347 Stainless Steel
The 347 stainless steel we offer is available in a variety of product forms, all of which have excellent mechanical properties and corrosion resistance to meet different industrial needs.
Bars: 347 stainless steel bars are mainly used for structural components, shafts, fasteners and machined parts. These bars are available in various shapes, including round, square and hexagonal.
Sheets and Plates: 347 stainless steel sheet and plate are ideal for applications like chemical processing equipment and heat exchangers. Their thin and flat form makes them easy to cut, bend and process into the required shape. 347 stainless steel sheets are thicker than sheets and are used in heavy-duty applications such as pressure vessels, heat shields and boiler components.
Tubes and Pipes: Tubes made of 347 stainless steel are commonly used in petrochemical, aerospace and power generation. They can transport liquids and gases under extreme conditions.
Round Bars: Round bar forms are widely used in aerospace, construction and mechanical components, with high strength and resistance to stress deformation.
Coil, Wire & Foil: Due to their flexibility and durability, these fine forms can be used in complex applications such as aerospace components, wires, and even decorative applications.
Mesh, Wire Mesh & Screen: Used in filtration systems, screens, and separators, 347 stainless steel mesh or wire mesh is highly resistant to corrosion and retains its strength at high temperatures. This makes it ideal for Chemical and oil refineries and food processing.
Castings: 347 stainless steel can also be cast into a variety of shapes for industrial components that require complexity and high resistance to high temperatures and corrosion.
Welding Rods and Filler Rods: Welding rods made from 347 stainless steel are designed to join components under high temperature conditions without the risk of intergranular corrosion.
Applications of 347 Stainless Steel
Thanks to its unique properties, 347 stainless steel is applied in industries that demand high-temperature resistance and corrosion durability.
Aerospace Components: Including air exhaust systems, collector rings and other components at high temperature exposure.
Chemical Processing: Well suited to handle corrosive materials and maintain structural integrity when exposed to harsh environments.
Food Processing Equipment: Its non-magnetic, corrosion-resistant properties make it suitable for food handling equipment and storage tanks.
Boiler Tubes and Heat Exchangers: Used where temperatures can exceed 1000°F, 347 stainless steel ensures long-lasting performance in extreme heat.
Power Generation: Steam piping, heat shields, and turbines benefit from 347’s ability to maintain strength at elevated temperatures.
Pros and Cons of 347 Stainless Steel
Advantages
- Excellent High-Temperature Performance: Suitable for long-term service in high-heat environments.
- Prevents Sensitization: Niobium stabilization prevents carbide precipitation and is associated with a reduced risk of intergranular corrosion.
- Good Weldability: Can be welded without losing its corrosion resistance properties.
- Non-Magnetic in Annealed Condition: Suitable for applications where magnetism could be a concern.
Disadvantages
- Higher Cost: More expensive than common grades like 304 and 316 due to niobium content.
- Lower Machinability: With a machinability rating of approximately 36%, it is harder to machine than other stainless steels.
- Limited Chloride Resistance: Not suitable for chloride-heavy environments, such as marine applications, where pitting and crevice corrosion may occur.
What are the Processing Methods of 347 Stainless Steel?
Forming
347 stainless steel offers good formability, similar to other austenitic steels. It can be shaped using various forming processes, such as deep drawing and stamping. However, it may require higher force due to its strength.
Welding
347 stainless steel is highly suitable for welding, with excellent resistance to intergranular corrosion after welding, thanks to its niobium stabilization.
- Common welding methods include TIG, MIG, and resistance welding.
- Post-weld heat treatment is usually not required, but 347 filler metals are recommended to maintain similar properties at the weld joint.
Cutting
Standard cutting methods for 347 stainless steel include:
- Plasma cutting
- Laser cutting
- Water jet cutting
- Mechanical methods like sawing
Due to its higher hardness, carbide-tipped tools are recommended for precision cutting and extended tool life.
Hot Working
347 stainless steel can be forged and hot worked with good results, but it requires precise temperature control.
- Forging temperature: Typically between 1150°C to 1250°C (2100°F to 2300°F).
- Hot rolling is also effective, but the material should be reheated above 980°C (1800°F) to maintain ductility.
- Air cooling or water quenching is used after hot working to stabilize the microstructure.
Cold Working
Cold working is feasible for 347 stainless steel, but it hardens faster than some other austenitic grades, requiring intermediate annealing during extensive deformation processes like cold rolling, bending, or drawing.
- Work hardening increases its strength and toughness, and annealing may be needed to restore ductility.
Heat treatment
Annealing and stress relief are commonly used heat treatment processes for 347 stainless steel to restore the ductility of the material or eliminate internal stress.
Annealing: 1010°C to 1193°C (1850°F to 2000°F). Rapid cooling after annealing (usually water quenching) can prevent the precipitation of chromium carbides, thereby improving its corrosion resistance.
Stress Relief: Usually in the range of 800°C to 870°C (1470°F to 1600°F). It can effectively avoid stress corrosion cracking and keep the structural integrity of the material.
Solution Treatment: Usually in the range of 1065°C to 1150°C (1950°F to 2100°F). Rapid cooling is required after solution treatment, usually using water quenching, to prevent intergranular corrosion and sensitization.
Age Hardening: The material is hardened through the cold working process, and then its strength can be further increased at moderate temperatures through aging treatment. The temperature for aging typically falls within a range of less than 800°C (or 1470°F).
Surface treatment
Surface treatment can improve the corrosion resistance and appearance of 347 stainless steel. Common surface treatment methods include:
- Polishing: used to improve the surface finish, often used in decorative and hygienic applications.
- Pickling and passivation: Pickling can remove the surface oxide layer and welding residues, and passivation forms a dense oxide protective layer through chemical treatment to further improve corrosion resistance.
- Sandblasting: Use iron-free sand or glass beads for sandblasting to eliminate surface defects and microcracks and ensure surface uniformity.
- Brushing and grinding: Surface residues, rust and oxides can be effectively removed by brushing or grinding, thereby enhancing surface corrosion resistance.
Difference between 347 and Other Grades
What is the difference between 316 and 347 stainless steel?
347 has superior high-temperature performance than 316 stainless steel, thanks to its niobium stabilization, which prevents sensitization and intergranular corrosion at high temperatures, but 316 is better suited to resist pitting in corrosive environments, especially those containing chloride.
What is the difference between SS 347 and 304 stainless steel?
304 stainless steel is the most commonly used stainless steel, and is well suited for general-purpose applications such as kitchen equipment and food processing, but it lacks the stability required for environments above 800°F (427°C). 347 contains niobium, which resists intergranular corrosion and is suitable for high-temperature service. While 304 is a more economical choice for everyday use, 347 is the preferred choice for high temperatures and corrosive environments.
347 vs. 321
Both 347 and 321 are stabilized austenitic stainless steels designed to resist sensitization, but they differ in their stabilizing elements – niobium for 347 and titanium for 321 stainless steel. The niobium stabilization of 347 provides enhanced stability, so 347 is often chosen for more demanding, high-temperature applications.
347 Stainless steel vs. 4140 Alloy Steels
Designed for high temperature and corrosive environments, 347 is an austenitic stainless steel with excellent resistance to oxidation and intergranular corrosion. 4140 is a low-alloy steel known for its high strength and toughness, but lacks the corrosion resistance of stainless steels. 347 excels in chemical processing, aerospace, and high-temperature applications, while 4140 is better suited for mechanical parts that require high strength, such as gears and shafts.
Is 347 Stainless Steel Magnetic?
In its annealed state, 347 stainless steel is generally non-magnetic. However, cold working or severe deformation may induce slight magnetic properties due to the formation of martensitic structures.
Does 347 Stainless Steel Rust?
Due to its high chromium content and stabilization with niobium, 347 stainless steel is highly resistant to rust and corrosion. But it will, as with all stainless steels, suffer from localized pitting or crevice corrosion at high chloride concentrations.
347 Stainless Steel Manufacturer: Why Choose SteelPRO Group?
SteelPRO Group is a leading 347 stainless steel supplier, stockist and manufacturer in China.
Choose us for your 347 stainless steel needs and take advantage of our industry-leading expertise, product range and services.
Global expertise in stainless steel: With years of experience, SteelPRO Group offers high-performance 347 stainless steel materials for a variety of industries, from aerospace to chemical processing.
Comprehensive product range: We supply 347 stainless steel in various forms, including bars, plates, sheets, tubes, coils and more.
Uncompromising quality: All our products are ISO certified and meet international standards for consistency, strength and reliability.
Competitive pricing: We offer the most competitive prices in the market without sacrificing quality.
Fast turnaround and delivery: Whether you require a small or large order, we offer timely delivery to ensure your project stays on track.
Contact SteelPRO Group today to get a quote and experience the quality of our premium 347 stainless steel.
- Stainless Steel Grades
- 300 Series Stainless Steel
- 303 Stainless Steel
- 304 Stainless Steel
- 305 Stainless Steel
- 308 Stainless Steel
- 316 Stainless Steel
- 316N Stainless Steel
- 409 Stainless Steel
- 410 Stainless Steel
- 416 Stainless Steel
- 420 Stainless Steel
- 430 Stainless Steel
- 410HT And 410L Stainless Steels
- 410S Stainless Steel
- 440 Stainless Steel
- 436 Stainless Steel
- 301 Stainless Steel
- 201 Stainless Steel
- 202 Stainless Steel
- 444 Stainless Steel
- 405 Stainless Steel
- 302 Stainless Steel
- 309 Stainless Steel
- 314 Stainless Steel
- 321 Stainless Steel
- 347 Stainless Steel
- 408 Stainless Steel
- 422 Stainless Steel
- 431 Stainless Steel
- 434 Stainless Steel
- 414 Stainless Steel
- 430FR Stainless Steel
- 13-8 PH Stainless Steel
- 317 | 317L Stainless Steel
- 616 Stainless Steel
- 630 Stainless Steel
- 904L Stainless Steel
- A2 Stainless Steel
- 304 vs 304L Stainless Steel
- 304 VS 316 Stainless Steel
- 304 vs 409 Stainless Steel
- 304 vs 430 Stainless Steel
- 410 Stainless Steel vs 304
- 18/0 vs 18/10
- 18/0 Stainless Steel
- 18/8 Stainless Steel
- 18/10 Stainless Steel
Comparisons