Contents
Alloy 616 | AISI 616 | AISI 422 Stainless Steel
- John
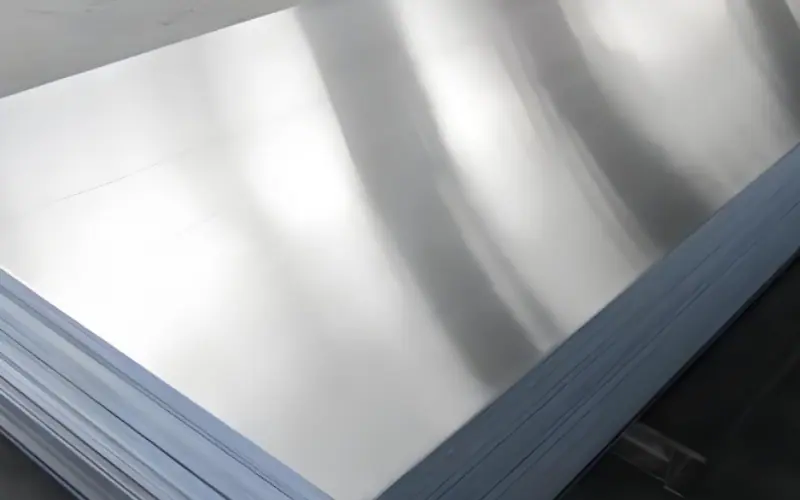
616 stainless steel is a martensitic alloy known for its exceptional performance in high-temperature environments. In this blog, we explore the composition and properties of 616 stainless steel. We also highlight its advantages, limitations, and applications, helping you select the best options for your project.
What Is 616 Stainless Steel?
AISI 616 stainless steel, also known as Alloy 616 or UNS S42200, is martensitic stainless steel. It is recognized for its strength and heat resistance. It can be hardened through heat treatment. AISI 616 performs well at elevated temperatures, maintaining properties up to 1200°F. Common applications include jet engines, steam turbines, and high-temperature bolts.
616 Stainless Steel Equivalents (AMS 5655)
- AISI 422
- UNS S42200
- ASTM A565 Grade 616
- EN 1.4935
Chemical Composition of 616 Stainless Steel
Here is a table summarizing the chemical compositions of 616 stainless steel:
Element | Fe | Cr | Mo | W | V | C | Mn | Si | P | S | Ni |
wt (%) | 81.9-85.8 | 11.0-12.5 | 0.9-1.25 | 0.9-1.25 | 0.2-0.3 | 0.20-0.25 | 0.5-1.0 | 0-0.5 | 0-0.025 | 0-0.025 | 0.5-1.0 |
Physical Properties of 616 Stainless Steel
Here is a table listing the physical properties of 616 stainless steel:
Property | Metric Value | Imperial Value |
Density | 7.9 g/cm³ | 490 lb/ft³ |
Melting Point | 1480-1510 °C | 2700-2750 °F |
Thermal Conductivity | 24 W/m·K | 14 BTU/h·ft·°F |
Thermal Expansion | 10 µm/m·K | – |
Electrical Conductivity | 4.7% IACS | 5.3% IACS for specific weight |
Magnetic Properties | Ferromagnetic | Ferromagnetic |
Mechanical Properties of 616 Stainless Steel
Here is the table summarizing the mechanical properties of 616 stainless steel:
Property | Typical Value |
Tensile Strength | 910-1080 MPa (130-160 ksi) |
Yield Strength | 670-870 MPa (97-130 ksi) |
Brinell Hardness | 260-330 |
Rockwell Hardness | 21 |
Vickers Hardness | 223 |
Elongation | 15-17% |
Elastic Modulus | 200 GPa (28 x 10⁶ psi) |
Other Properties of 616 Stainless Steel
Heat Resistance
Heat resistance is the most critical property of 616 stainless steel. It is specifically engineered for high-temperature applications. It can operate continuously at 1200°F (650°C) without losing its strength. Its chromium and molybdenum content help resist scaling and oxidation, ensuring durability in extreme temperatures. It is well-suited for components like turbines and jet engines.
Corrosion Resistance
616 stainless steel, offers moderate corrosion resistance. Its chromium content (11-12.5%) helps protect the surface from rust and scaling in mildly corrosive environments. But it isn’t as resistant as other grades like 316 stainless steel
Workability
616 stainless steel offers moderate workability. While it can be machined and formed, it is more challenging to work with compared to austenitic stainless steels due to its higher hardness and strength.
Common Applications of 616 Stainless Steels
The common applications of 616 stainless steel are mainly in environments that require high strength and heat resistance. Here are its primary uses:
Industry | Application | Characteristics |
Aerospace | Turbine blades | High strength, heat resistance |
Automotive | Exhaust systems | Corrosion resistance |
Energy | Valves | Wear resistance, durability |
Oil and Gas | Pump components | High-temperature stability |
Manufacturing | Machine parts | Hardening capability |
Power Generation | High-temperature bolted joints | High strength, thermal stability |
The Pros and Cons of 616 Stainless Steels
Here are the advantages of 616 stainless steel:
- High Heat Resistance
616 stainless steel can operate at temperatures up to 1200°F (650°C), making it ideal for high-temperature applications like turbine blades, jet engines, and other aerospace components.
- Good Mechanical Strength
The alloy exhibits excellent tensile and yield strength, maintaining mechanical performance in both room-temperature and high-temperature environments.
- Good Wear Resistance
Due to its high hardness, particularly after heat treatment, 616 stainless steel offers excellent wear resistance, which is essential in high-friction environments.
Here are the disadvantages of 616 stainless steel:
- Limited Corrosion Resistance
616 stainless steel offers moderate corrosion resistance due to its chromium content but is not suitable for highly corrosive or marine settings.
- Difficult Machinability After Hardening
Once heat-treated, 616 stainless steel becomes very hard, making machining difficult. Specialized tools and techniques are required to cut or shape it effectively in this hardened state. However, it is easier to machine in its annealed condition.
- Limited Cold Workability
616 stainless steel is hard to deform through cold working processes (like cold rolling or forming), especially after it has been heat-treated. The material’s high hardness at room temperature limits its ability to be shaped or formed in cold conditions.
The Processing Methods of 616 Stainless Steel
Hot Working
Hot working is the process of deforming and shaping metals at temperatures above their recrystallization point, allowing the material to be easily formed without breaking.
Forging
Heat the steel to 1700-2150°F (927-1177°C) and compress using hammers or presses.
This process shapes complex parts like turbine blades and improves the steel’s grain structure.
Rolling
Heat the steel to the same temperature range and pass through rollers to reduce its thickness, forming it into plates or bars.
Rolling enhances the strength and grain refinement of the material.
Extruding
Heated to 1700-2150°F (927-1177°C), the steel is pushed through a die to create uniform profiles such as rods or tubes.
This process is employed for more complex shapes that are difficult to achieve through conventional processes.
Heat Treatment
The heat treatment process for 616 stainless steel is crucial to enhancing its mechanical properties, particularly hardness, strength, and wear resistance.
Annealing
Heat the steel to 790-850°C (1450-1560°F) and hold it at this temperature to ensure even heating. Then cool slowly in the air.
This process relieves internal stresses and softens the steel, making it easier to machine
Hardening
Heat the steel to the quenching temperature of 1000-1065°C.
Once the steel reaches the desired temperature, it should be quenched rapidly using oil or air, depending on the thickness of the part. Thicker parts generally require oil quenching to cool them fast enough.
Tempering
Reheat to 540-650°C (1000-1200°F) depending on the desired hardness and strength. Hold at this temperature for a specified time, followed by air cooling.
After quenching, the steel is very brittle and needs tempering to restore toughness.
Stress Relieving
After hardening, stress relieving can be applied by heating to 200-300°C (390-570°F) to reduce residual stresses.
Machine
Processes include turning, milling, and drilling, to achieve the desired shape.
For machining AISI 422, it is recommended to use carbide cutting tools or tools with coatings like TiN or TiAlN for their durability and reduced friction.
Effective cooling methods, such as cutting fluids, are crucial for managing heat and improving surface quality.
Summary
616 stainless steel, also known as AISI 422, is an alloy designed for high-temperature performance and wear resistance. It is an ideal material for turbines, jet engines, and heat exchangers.
At Steel Pro Group, we are committed to providing top-quality materials for high-performance industrial needs. If you are looking for reliable solutions for your projects, please visit our website or contact us for a personalized consultation and quote. We’re here to help you make the best material choice for your specific requirements!
- Stainless Steel Grades
- 300 Series Stainless Steel
- 303 Stainless Steel
- 304 Stainless Steel
- 305 Stainless Steel
- 308 Stainless Steel
- 316 Stainless Steel
- 316N Stainless Steel
- 409 Stainless Steel
- 410 Stainless Steel
- 416 Stainless Steel
- 420 Stainless Steel
- 430 Stainless Steel
- 410HT And 410L Stainless Steels
- 410S Stainless Steel
- 440 Stainless Steel
- 436 Stainless Steel
- 301 Stainless Steel
- 201 Stainless Steel
- 202 Stainless Steel
- 444 Stainless Steel
- 405 Stainless Steel
- 302 Stainless Steel
- 309 Stainless Steel
- 314 Stainless Steel
- 321 Stainless Steel
- 347 Stainless Steel
- 408 Stainless Steel
- 422 Stainless Steel
- 431 Stainless Steel
- 434 Stainless Steel
- 414 Stainless Steel
- 430FR Stainless Steel
- 13-8 PH Stainless Steel
- 317 | 317L Stainless Steel
- 616 Stainless Steel
- 630 Stainless Steel
- 904L Stainless Steel
- A2 Stainless Steel
- 304 vs 304L Stainless Steel
- 304 VS 316 Stainless Steel
- 304 vs 409 Stainless Steel
- 304 vs 430 Stainless Steel
- 410 Stainless Steel vs 304
- 18/0 vs 18/10
- 18/0 Stainless Steel
- 18/8 Stainless Steel
- 18/10 Stainless Steel
Comparisons