Contents
Stainless Steel Melting Point: Measurement, Influencing Factors, and Importance
- John
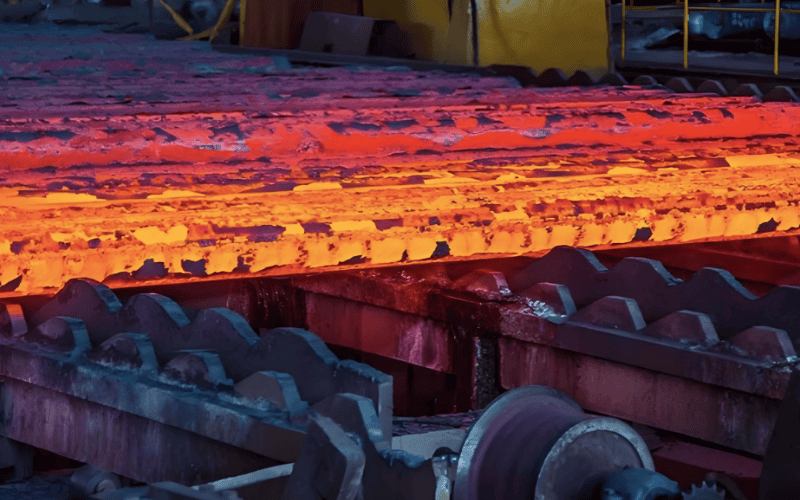
This article covers the measurement methods, influencing factors, and importance of stainless steel melting point. We compare the melting points of different stainless steel grades, and introduce methods for melting stainless steel. Correctly understanding the melting point of stainless steel can help us ensure the quality and stability of stainless steel products, and can also help us choose the right material for processing and application.
What is the Stainless Steel Melting Point?
The stainless steel melting point refers to the temperature at which stainless steel changes from solid to liquid under a given pressure, usually between 1400°C and 1530°C. The melting point is related to the stability and performance of the material in a high temperature environment and is crucial to the processing and application of stainless steel.
How to measure the Stainless Steel Melting Point?
Different measurement methods have different applicability and accuracy. The following are several commonly used melting point measurement methods and their detailed descriptions.
Capillary method
The capillary method is a traditional and commonly used melting point measurement method, suitable for the measurement of high-purity materials. The sample is placed in a thin-walled capillary tube and placed next to a heating source, while a precision thermometer is used to monitor the temperature change. During the heating process, the temperature rises by 1°C per minute until the material is completely melted. The temperature at this time is the melting point.
Differential thermal analysis (DTA)
Differential thermal analysis is a high-precision melting point measurement technique suitable for melting point measurement of complex alloys. During the heating process, the heat flow changes of the sample are recorded to accurately determine the melting point and phase transition temperature.
Thermomechanical analysis (TMA)
Thermomechanical analysis determines the melting point by measuring the dimensional changes of the material during heating. The expansion or contraction data of the material during heating can be used to infer the melting point. This method is suitable for observing the deformation characteristics of the material during heating.
Scanning Electron Microscope (SEM)
SEM is suitable for determining the melting point of complex alloys. This method can indirectly infer the melting point by observing the changes in the microstructure of the material at high temperatures and comparing the microstructure at different temperatures.
Factors Affecting the Stainless Steel Melting Point
The melting point of stainless steel is affected by many factors, including its chemical composition, crystal structure, heat treatment, and impurities.
Alloy composition
Stainless steel is mainly composed of iron, chromium, and nickel. Other alloying elements such as molybdenum, titanium, and vanadium also affect the melting point.
Nickel: Adding nickel will lower the melting point of stainless steel because nickel has a lower melting point.
Molybdenum: Increases the high temperature resistance of stainless steel while increasing the melting point.
Titanium and niobium: Stabilize the crystal structure of stainless steel, improve melting point and durability.
Crystal structure
The crystal structure of stainless steel has a significant effect on the melting point. The main crystal structures include:
- Face-centered cubic structure (FCC): Such as austenitic stainless steel (304, 316), this structure is stable at high temperatures, but has a low melting point.
- Body-centered cubic structure (BCC): Such as ferritic stainless steel (430), this structure has a higher melting point and is suitable for high temperature applications.
Heat treatment and processing technology
Heat treatment processes such as annealing and quenching will change the microstructure of stainless steel, thereby affecting its melting point.
- Annealing: The crystal structure of the material is relaxed by heating and slow cooling. It usually does not significantly change the melting point, but it will increase the ductility and toughness of the material.
- Quenching: Rapid cooling can increase the hardness and strength of the material, but has little effect on the melting point.
Impurities and additives
Impurities such as sulfur and phosphorus will reduce the melting point of stainless steel and may cause the material performance to deteriorate. Additives such as titanium and niobium can increase the melting point and improve the stability and durability of the material.
Sulfur: Makes the material embrittled and lowers the melting point.
Titanium: Stabilizes the crystal structure of the material and increases the melting point.
Melting Points of Different Stainless Steel Types
Stainless steel comes in many different types and grades, and the melting point of each type varies due to its chemical composition and structure.
Austenitic stainless steel melting point
The melting point of austenitic stainless steel, such as grades 304 and 316, typically ranges between 1400°C to 1450°C (2550°F to 2640°F).
This range can vary slightly depending on the specific alloy composition, but austenitic stainless steels generally have similar melting points due to their high chromium and nickel content.
Ferritic stainless steel melting point
The melting point of ferritic stainless steel, such as grade 430, typically ranges between 1425°C to 1510°C (2597°F to 2750°F).
Ferritic stainless steels generally have higher melting points compared to austenitic stainless steels due to their lower nickel content and different crystal structure.
Martensitic stainless steel melting point
The melting point of martensitic stainless steel, such as grades 410 and 420, typically ranges between 1400°C to 1450°C (2550°F to 2640°F).
Martensitic stainless steels have a similar melting range to austenitic grades, but their composition and microstructure (higher carbon content and less nickel) affect their specific melting characteristics.
Duplex stainless steel melting point
The melting point of duplex stainless steel typically ranges between 1350°C to 1400°C (2460°F to 2550°F).
Duplex stainless steels, which are a mix of austenitic and ferritic phases, have slightly lower melting points compared to pure austenitic or ferritic stainless steels due to their unique microstructure and alloy composition.
Precipitation hardening melting point
The melting point of precipitation hardening stainless steel, such as 17-4 PH, typically ranges between 1400°C to 1450°C (2550°F to 2640°F).
Precipitation hardening steels combine high strength with good corrosion resistance, and their melting points are similar to other stainless steels, influenced by their alloying elements like chromium and nickel.
Why is the Stainless Steel Melting Point Important?
What temperature will destroy stainless steel?
1000°C (1832°F): At this temperature, the tensile strength of stainless steel begins to decrease significantly. Although the melting point of stainless steel is much higher than this temperature, prolonged exposure to high temperatures may result in a reduction in the strength of the material and affect its service life.
Exceeding the melting point: When stainless steel reaches or exceeds its melting point, the material will completely melt and lose its original physical properties. At this point, stainless steel no longer has the strength and structural stability of a solid, which can lead to equipment failure or material damage.
Importance of Melting Point
Processing and Manufacturing: During the processing and manufacturing of stainless steel, understanding the melting point can accurately control the temperature to avoid overheating or overcooling, ensuring the quality and performance of the product.
High Temperature Applications: In industries involving high temperature applications, such as aerospace, chemical and construction industries, choosing the right materials and processes is essential to ensure the long-term stability of the product. Knowledge of melting point can help engineers choose the most suitable materials to ensure reliability and durability under extreme temperature conditions.
Melting Point of Stainless Steel Applications
Different grades of stainless steel perform differently in various applications, and melting point plays a particularly important role in these applications.
Construction and Engineering
In construction and engineering projects, choosing stainless steel with the right melting point can improve the stability and safety of the structure. Knowing the melting point of the material can help designers ensure durability and reliability in high-temperature environments.
Chemical and Pharmaceutical Industries
Generally speaking, stainless steels with higher melting points usually have better corrosion resistance. This is because high melting points are often associated with higher levels of corrosion-resistant elements such as chromium and nickel in the alloy. In highly corrosive environments such as chemical industries, stainless steels with higher melting points can better resist erosion by corrosive media and extend the service life of equipment.
Aerospace
The aerospace industry requires extremely high temperature performance from its materials. Knowing the melting point of stainless steel can help choose the right material to ensure reliability under extreme temperature conditions. For example, duplex stainless steel and high-alloy stainless steel perform well in high-temperature and high-pressure environments.
Stainless Steel Melting Points Chart
Grade | Melting Point Range (°C) | Melting Point Range (°F) |
201 | 1400-1450 | 2552-2642 |
301 | 1400-1420 | 2552-2598 |
303 | 1400-1420 | 2552-2598 |
304 | 1400-1450 | 2552-2642 |
304L | 1400-1420 | 2552-2598 |
316 | 1375-1470 | 2507-2678 |
316L | 1375-1400 | 2507-2552 |
321 | 1400-1425 | 2552-2597 |
410 | 1425-1500 | 2597-2732 |
413 | 1480-1530 | 2700-2794 |
416 | 1480-1530 | 2700-2794 |
420 | 1450-1510 | 2642-2750 |
430 | 1480-1530 | 2700-2790 |
440 | 1370-1480 | 2500-2700 |
440C | 1370-1480 | 2500-2700 |
446 | 1425-1510 | 2597-2750 |
630 | 1370-1420 | 2500-2598 |
2205 | 1425-1525 | 2597-2777 |
904L | 1400-1450 | 2552-2642 |
What Temp Does 304 Stainless Melt?
304 stainless steel is one of the most commonly used stainless steels, with a melting point range of 1400°C to 1450°C.
What Temp Does 316 Stainless Melt?
With a melting point range of 1375°C to 1400°C, 316 stainless steel is a molybdenum-containing austenitic stainless steel . It has high corrosion resistance, especially in chloride-containing environments.
What is 18-8 stainless steel melting point?
The melting point of 18-8 stainless steel (which is another name for 304 stainless steel) is typically in the range of 1400°C to 1450°C (2550°F to 2640°F).
How to Melt Stainless Steel?
Melting stainless steel is a critical step in the manufacturing process, and ensuring the quality of the melting process directly affects the performance of the final product. Here are the basic steps and techniques for melting stainless steel:
Melting technology
Electric arc furnace: Use an electric arc furnace to heat the metal above its melting point, and generate high temperatures through the electric arc to melt the stainless steel. This method is suitable for large-scale production.
Induction furnace: Use electromagnetic induction to heat stainless steel, which is suitable for precision processing and small-batch production. The heating method of the induction furnace is more uniform, which helps to accurately control the melting process.
Furnace temperature control
Precise control: In the melting process the control of temperature is extremely critical. If the temperature is too high, it may lead to oxidation or uneven melting of stainless steel, while if it is too low, it may lead to incomplete melting. Therefore, high-precision temperature control equipment is required to keep the furnace temperature within the appropriate range.
Safety measures
Protective equipment: Wear appropriate protective equipment, such as heat-resistant coveralls and goggles, when melting stainless steel to protect the operator from the heat and molten metal.
Melting environment: Ensure that the melting environment is well ventilated to remove harmful gasses and prevent molten metal from splashing and causing danger.
Melting Point of Metals Chart
Metal | Melting Point (°C) | Melting Point (°F) |
Aluminum | 660°C | 1220°F |
Copper | 1085°C | 1985°F |
Gold | 1064°C | 1947°F |
Iron | 1538°C | 2800°F |
Lead | 327°C | 621°F |
Magnesium | 650°C | 1202°F |
Nickel | 1455°C | 2651°F |
Platinum | 1768°C | 3215°F |
Silver | 961°C | 1763°F |
Stainless Steel (304) | 1400°C – 1450°C | 2550°F – 2640°F |
Titanium | 1668°C | 3034°F |
Zinc | 420°C | 788°F |
Carbon Steel | 1425°C – 1540°C | 2600°F – 2800°F |
What temperature does steel melt?
Steel typically melts at temperatures between 1425°C to 1540°C (2600°F to 2800°F), depending on its composition.
- Carbon steel melts around 1425°C to 1540°C.
- Stainless steel melts at slightly lower or higher temperatures depending on the alloy, with 304 stainless steel melting around 1400°C to 1450°C (2550°F to 2640°F).
What metal has the highest melting point?
The metal with the highest melting point is tungsten (W), with a melting point of 3422°C (6192°F). Tungsten’s extremely high melting point makes it ideal for use in high-temperature applications, such as light bulb filaments, rocket engine nozzles, and other components exposed to extreme heat.
Get Satisfactory Stainless Steel!
Knowing the melting point of stainless steel helps ensure stability and safety. SteelPRO Group is committed to providing you with high-quality stainless steel products to meet your different application needs. If you would like to learn more about our products or customize special specifications, please check out our blog or feel free to contact us.
- Stainless Steel Grades
- 300 Series Stainless Steel
- 303 Stainless Steel
- 304 Stainless Steel
- 305 Stainless Steel
- 308 Stainless Steel
- 316 Stainless Steel
- 316N Stainless Steel
- 409 Stainless Steel
- 410 Stainless Steel
- 416 Stainless Steel
- 420 Stainless Steel
- 430 Stainless Steel
- 410HT And 410L Stainless Steels
- 410S Stainless Steel
- 440 Stainless Steel
- 436 Stainless Steel
- 301 Stainless Steel
- 201 Stainless Steel
- 202 Stainless Steel
- 444 Stainless Steel
- 405 Stainless Steel
- 302 Stainless Steel
- 309 Stainless Steel
- 314 Stainless Steel
- 321 Stainless Steel
- 347 Stainless Steel
- 408 Stainless Steel
- 422 Stainless Steel
- 431 Stainless Steel
- 434 Stainless Steel
- 414 Stainless Steel
- 430FR Stainless Steel
- 13-8 PH Stainless Steel
- 317 | 317L Stainless Steel
- 616 Stainless Steel
- 630 Stainless Steel
- 904L Stainless Steel
- A2 Stainless Steel
- 304 vs 304L Stainless Steel
- 304 VS 316 Stainless Steel
- 304 vs 409 Stainless Steel
- 304 vs 430 Stainless Steel
- 410 Stainless Steel vs 304
- 18/0 vs 18/10
- 18/0 Stainless Steel
- 18/8 Stainless Steel
- 18/10 Stainless Steel
Comparisons