Contents
Exploring PVD Stainless Steel: The Future of Durable and Stylish Coatings
- John
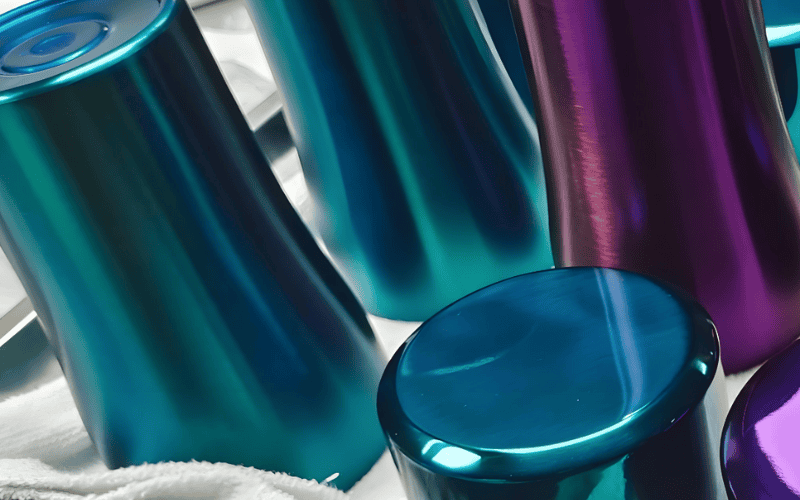
PVD (Physical Vapor Deposition) stainless steel is renowned for its enhanced durability and aesthetic appeal. This advanced coating process applies a thin, hard layer to stainless steel, improving its resistance to scratches, corrosion, and wear. This article introduces PVD Stainless Steel, covering its properties, pros and cons, key characteristics, and applications.
What Is PVD Stainless Steel?
PVD stainless steel is stainless steel coated with a thin, durable layer using Physical Vapor Deposition (PVD). PVD costing can enhance the steel’s appearance, add color, and increase its resistance to scratches and corrosion. PVD stainless steel is commonly used in watches, appliances, and architectural materials for its strength and visual appeal.
What Are The Properties of PVD Coating?
Here is a summary of PVD coating properties:
- High Hardness
PVD coatings have a hard surface, often over 2000 HV, which increases wear resistance.
- Low Friction
The coating reduces friction, improving performance in moving parts.
- Corrosion Resistance
PVD coatings protect surfaces from corrosion caused by moisture or chemicals.
- Strong Adhesion
The coating bonds tightly to the substrate, preventing peeling or flaking.
- High-Temperature Stability
PVD coatings can withstand temperatures above 500°C without degrading.
Check the table to reference the key performance data of PVD coatings:
Property | Typical Values |
Vickers Hardness | 1500 to 3000 HV |
Coefficient of Friction | 0.1 to 0.6 |
Thickness | 1 to 5 micrometers (µm) |
Adhesion Strength | 60 N or higher (measured via Scratch Test) |
Oxidation Temperature | 400°C to 800°C |
What Is PVD Stainless Steel Used For?
PVD stainless steel is versatile and useful. Here are the common applications of PVD stainless steel.
Application | Reason |
Watches and Jewelry | Shiny and scratch-resistant |
Kitchen Appliances | Modern look and protection against damage |
Building Materials | Stylish appearance and weather protection |
Automotive Parts | Tougher and more attractive |
Cutlery and Tools | Stays sharp and resists rust |
Electronics | Scratch-free and premium look |
Medical Instruments | Strong, clean, and rust-resistant |
What Are The Pros and Cons of PVD Coating?
Here are the advantages of PVD Stainless Steel.
- Enhanced Durability
The PVD coating adds a tough, protective layer to the stainless steel. It makes it more resistant to scratches, wear, and everyday damage.
- Corrosion Resistance
PVD stainless steel has great corrosion resistance. This makes it appropriate for use both indoors and outdoors.
- Improved Hardness
The PVD coating increases the surface hardness of the stainless steel. It provides extra protection against impacts and abrasion.
- Low Maintenance
PVD coating is simple to clean and maintain. The coating helps prevent fingerprints and smudges. It keeps the surface looking pristine with minimal effort.
- Biocompatibility
Certain PVD coatings applied to stainless steel, such as titanium nitride, are biocompatible, making them suitable for medical implants and instruments.
- Environmentally
FriendlyThe PVD process is environmentally friendly. Because it doesn’t use harmful chemicals and generates minimal waste.
Here are the disadvantages of PVD Stainless Steel.
- Higher Cost
PVD stainless steel can be more expensive than untreated stainless steel due to the additional coating process.
- Complexity in Repairs
It is hard to repair the damaged coating, and the entire piece may need to be recoated.
- Thickness Limitation
The PVD coating is very thin, so while it adds surface protection, it doesn’t significantly increase the overall structural strength of the stainless steel.
- Limited Resistance to Extreme Conditions
PVD coatings have limited resistance to extreme conditions, and in very harsh environments, like high temperatures or corrosive chemicals, they may degrade over time.
Durability of PVD Coated Stainless Steel
PVD stainless steel is well known for its excellent durability. The PVD coating makes the surface harder, so it resists scratches and wear much better than untreated stainless steel. Here are some questions that can help you understand its durability.
How Long Does PVD Stainless Steel last?
For most applications, PVD stainless steel can maintain its appearance and performance for 10 to 15 years or even longer. Extreme environments or intensive use may reduce its lifespan.
Does PVD Plating Wear off?
PVD plating is very durable. But it can wear off over time, typically if exposed to severe environments or heavy use.
Does PVD Coating Peel off?
In general, PVD coatings are very stable and unlikely to peel under normal conditions. If the underlying material is damaged or the coating is not applied correctly, peeling can occur.
Is PVD Coating scratch-proof?
It is highly scratch-resistant. Generally, everyday items like keys or coins won’t scratch easily. But with significant force or a sharp object, it can still get scratched.
Will PVD tarnish?
PVD stainless steel has resistance to tarnishing. The coating is designed to be stable and resistant to reactions that cause tarnishing.
Maintenance and Care
Your PVD stainless steel will keep its appearance longer and last more time. Here are the simple steps.
- Clean Regularly. Wipe the surface with a soft, damp cloth to remove dust and fingerprints. If necessary, use gentle soap, but stay away from strong chemicals.
- Avoid Abrasives. Avoid scratching the coating. Please do not use abrasive cleaners, scrub pads, or steel wool.
- Dry Completely. Finished cleaning, dry the surface with a soft cloth and avoid water spots and streaks.
- Handle with Care. Watch out for sharp objects or rough surfaces that might scratch your PVD coating.
- Store Properly. When not being used, store PVD-coated items in a dry location, staying away from direct sunlight and extreme temperatures.
Related Reading
How to Remove Scratches From Stainless Steel?
How to Manufacture PVD Stainless Steel?
Surface Preparation
Clean and polish the stainless steel surface. Ensure contaminants are free. This step is important for the coating to adhere correctly.
PVD Coating Process
Place the prepared stainless steel in a vacuum chamber. Inside the chamber, the coating material (often metals like titanium, zirconium, or chrome) is vaporized using high temperatures or plasma. Then the vaporized material will condense onto the stainless steel surface, forming a thin, even coating.
Cooling and Finishing
The stainless steel is gradually cooled down after coating. It may undergo additional finishing processes, like polishing, to achieve the desired appearance.
Quality Control
The coated stainless steel is inspected for coating thickness, adhesion, and overall quality to ensure it meets the required standards.
PVD Coating Process
Vacuum Environment
The PVD process occurs within a vacuum chamber. Creating a vacuum is essential to prevent contamination and allow the coating material to vaporize effectively.
Target Material Vaporization
Inside the chamber, a solid coating material, often metals like titanium, zirconium, or chromium, is heated to a high temperature or bombarded with ions (plasma) until it vaporizes into a gas.
Coating Deposition
The vaporized material travels through the vacuum and condenses onto the surface of the stainless steel, forming a thin, uniform layer. This layer bonds to the steel at a molecular level, ensuring a strong, durable coating.
Control of Thickness and Composition
The thickness of the coating and its composition can be precisely controlled by adjusting the process parameters, such as temperature, pressure, and the type of material used.
Cooling and Solidification
Once the desired coating thickness is achieved, the coated stainless steel is allowed to cool, solidifying the new layer and locking in its properties.
Different Colors of PVD Stainless Steel
Different colors of PVD stainless steel can be produced depending on the materials used in the coating process and the required finish. Here are some common coatings.
PVD Coating Type | Color | Key Uses |
Titanium Nitride (TiN) | Gold/Yellowish | Jewelry, watches, tools |
Zirconium Nitride (ZrN) | Golden | Decorative applications |
Titanium Carbonitride (TiCN) | Gray/Dark Gray | Cutting tools, auto parts |
Chromium Nitride (CrN) | Silver/Metallic | Appliances, auto components |
Diamond-Like Carbon (DLC) | Black/Dark | High-performance items |
There are also many various colors and finishes, such as rose gold, blue, or rainbow effects can be customized by PVD coatings.
PVD Coating VS Electroplating
Durability
PVD coatings are generally more durable than electroplating.
Thickness
With strong protection, PVD coatings are thinner, usually between 0.5 to 5 micrometers, while electroplating can be thicker.
Cost
PVD tends to cost more than electroplating because of the sophisticated technology and equipment needed. However, the longer lifespan of PVD can offset the higher initial cost.
Environmental Impact
PVD is more environmentally friendly since it doesn’t use harmful chemicals or produce significant waste.
Adhesion Strength
PVD coatings bond strongly to the surface and are less likely to peel or flake off compared to electroplating.
Aesthetic Options
PVD provides a wider range of colors and finishes, including vibrant gold, black, and rainbow effects. Electroplating offers fewer color options, typically silver, gold, or nickel.
Which Stainless Steels Are Appropriate for PVD?
Most types of stainless steel can be PVD-coated. Some grades of stainless steel are well-suited for PVD coating.
- 304 Stainless Steel:
This is one of the most commonly used stainless steels, known for its good corrosion resistance and mechanical properties. PVD coating can further enhance its surface hardness and decorative appeal. That makes it popular for appliances, architecture, and consumer products.
- 316 Stainless Steel:
316 stainless steel provides great corrosion resistance, especially in marine environments or chemical applications. PVD coating improves its surface wear resistance and scratch resistance, making it ideal for high-end watches, jewelry, and medical devices.
- 430 Stainless Steel:
This ferritic stainless steel is costless while still providing good corrosion resistance. PVD coating enhances its aesthetics and surface hardness. It is commonly used in kitchen appliances and decorative panels.
- 410 Stainless Steel:
This is a martensitic stainless steel known for its good strength and hardness but with lower corrosion resistance. PVD coating can improve its surface finish and durability. That makes
it suitable for applications like cutlery and industrial components.
- 201 Stainless Steel:
This economical stainless steel has lower nickel content and slightly lower corrosion resistance than 304. PVD coating can enhance its durability and aesthetic appeal. It is commonly used in decorative items and household appliances.
Other Things About PVD Stainless Steel
Can PVD Coating Be Repaired?
PVD coating cannot be easily repaired.
For minor scratches, PVD coating can sometimes be polished to reduce their visibility.
For deep damage or severe wear, the coating cannot be repaired and requires full recoating.
Can PVD Be Recoated?
Yes. PVD can be recoated, but the original coating must first be completely removed before a new layer is applied. This process requires specialized equipment and is typically done by professionals.
PVD Stainless Steel VS Stainless Steel
PVD stainless steel is more scratch-resistant and offers more color options than regular stainless steel. It requires less maintenance but is more expensive. The PVD process is also more eco-friendly.
Regular stainless steel is easier to repair, PVD coated surfaces are harder to fix.
Summary & Furthermore
This article briefly explains the definition, properties, applications, and other important aspects of PVD stainless steel. To learn more about stainless steel or other steel types, check out our blog or contact our metal experts.
As a leading manufacturer and solutions provider of specialty steel, we deliver multi-industry application solutions and customized services with a 100% quality guarantee, committed to growing together with our customers. Visit our website to learn more, or send us a quote, and we will contact you shortly!
- Stainless Steel Grades
- 300 Series Stainless Steel
- 303 Stainless Steel
- 304 Stainless Steel
- 305 Stainless Steel
- 308 Stainless Steel
- 316 Stainless Steel
- 316N Stainless Steel
- 409 Stainless Steel
- 410 Stainless Steel
- 416 Stainless Steel
- 420 Stainless Steel
- 430 Stainless Steel
- 410HT And 410L Stainless Steels
- 410S Stainless Steel
- 440 Stainless Steel
- 436 Stainless Steel
- 301 Stainless Steel
- 201 Stainless Steel
- 202 Stainless Steel
- 444 Stainless Steel
- 405 Stainless Steel
- 302 Stainless Steel
- 309 Stainless Steel
- 314 Stainless Steel
- 321 Stainless Steel
- 347 Stainless Steel
- 408 Stainless Steel
- 422 Stainless Steel
- 431 Stainless Steel
- 434 Stainless Steel
- 414 Stainless Steel
- 430FR Stainless Steel
- 13-8 PH Stainless Steel
- 317 | 317L Stainless Steel
- 616 Stainless Steel
- 630 Stainless Steel
- 904L Stainless Steel
- A2 Stainless Steel
- 304 vs 304L Stainless Steel
- 304 VS 316 Stainless Steel
- 304 vs 409 Stainless Steel
- 304 vs 430 Stainless Steel
- 410 Stainless Steel vs 304
- 18/0 vs 18/10
- 18/0 Stainless Steel
- 18/8 Stainless Steel
- 18/10 Stainless Steel
Comparisons