Contents
What Is Stainless Steel Made of: Key Elements and Their Impact on Performance
- John
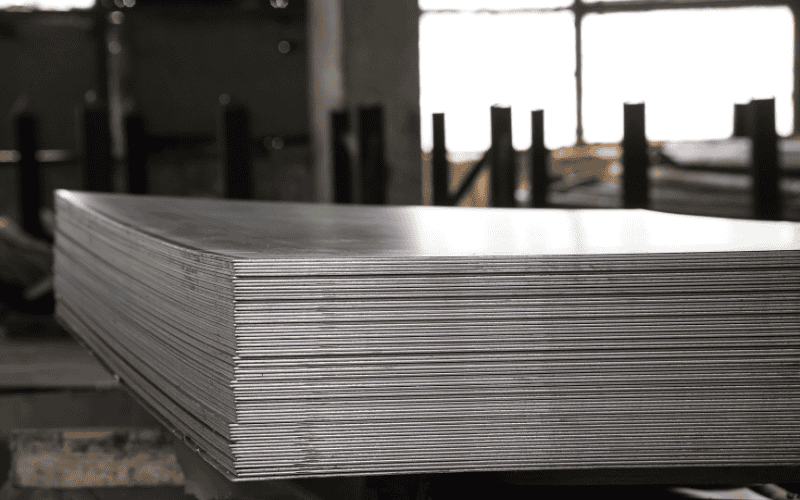
Stainless steel is versatile and commonly used with its excellent corrosion resistance and strength. Its composition primarily includes iron, along with key elements such as chromium, nickel, molybdenum, carbon, manganese, silicon, and nitrogen. Each of these factors contributes significantly to the performance of stainless steel. Understanding these components is essential to selecting the right type of stainless steel for construction, automobiles, medical devices, and kitchenware.
What Is the Key Composition in Stainless Steel and How Do They Impact Performance?
Stainless steel is an alloy made largely of iron, with various other elements added to enhance its properties. The key elements in stainless steel include iron, chromium, nickel, molybdenum, carbon, manganese, silicon, and nitrogen. Each element affects the steel’s properties, such as corrosion resistance, strength, and ductility.
Iron (Fe)
- Content: Bulk of the composition.
- Impact: Provides basic strength and structural support. However, iron is prone to rust and corrosion, which is mitigated by adding other elements.
- Common in: All stainless steels.
Chromium (Cr)
- Content: Minimum 10.5%, typically between 16%-26%.
- Impact: Key to corrosion resistance by forming a protective chromium oxide layer on the steel surface. Higher chromium levels improve overall corrosion resistance.
- Common in: All stainless steels, especially austenitic (304, 316) and ferritic (430) grades.
Nickel (Ni)
- Content: Ranges from 8%-20%.
- Impact: Enhances ductility, formability, and corrosion resistance, particularly in acidic environments. Nickel also stabilizes the austenitic structure, making the steel non-magnetic.
- Common in: Austenitic stainless steels (304, 316).
Molybdenum (Mo)
- Content: 2%-3%.
- Impact: Increases resistance to pitting and crevice corrosion, especially in chloride environments. Also improves strength at high temperatures.
- Common in: Grades like 316 and duplex stainless steel.
Carbon (C)
- Content: Less than 0.1% in most grades, but can be higher (up to 1.2%) in martensitic steels.
- Impact: Increases hardness and strength, but too much carbon can reduce corrosion resistance by forming chromium carbides.
- Common in: Martensitic (410, 420) and some austenitic grades.
Manganese (Mn)
- Content: Typically 1%-2%.
- Impact: Acts as a deoxidizer and improves toughness, wear resistance, and hardenability. Manganese is also crucial in free-machining stainless steels.
- Common in: Austenitic and duplex grades.
Silicon (Si)
- Content: Around 1%.
- Impact: Improves oxidation resistance, particularly at high temperatures, and enhances strength by maintaining structural integrity under thermal stress.
- Common in: High-temperature stainless steel (e.g., furnace components).
Nitrogen (N)
- Common in: Duplex and austenitic grades.
- Content: Up to 0.2%.
- Impact: Increases strength and resistance to stress corrosion cracking, particularly in duplex and austenitic grades. It also improves weldability.
Other Chemical Composition in Stainless Steel
Phosphorus (P), sulfur (S), titanium (Ti), and niobium (Nb) are essential in stainless steel for optimizing properties like strength, corrosion resistance, and machinability. Though in small amounts, they significantly impact performance and durability.
Phosphorus (P)
- Content: 0.03% – 0.045%
- Impact: Enhances strength and work-hardening but reduces corrosion resistance. It increases stress corrosion cracking risk, especially in welded areas. High phosphorus levels cause brittleness in low temperatures and promote cracking during welding.
- Common in: Lower grades of stainless steel and free-machining types (e.g., 430F).
Sulfur (S)
- Content: Below 0.03%-0.04%
- Impact: Improves machinability by forming sulfides that reduce tool wear and friction, but also increases susceptibility to pitting and stress corrosion. High sulfur content causes brittleness at high temperatures and weakens weld strength.
- Common in: 303 stainless steel (free-machining grades).
Titanium (Ti)
- Content: 0.5% – 1.0%
- Impact: Forms titanium carbides, preventing chromium carbide formation and enhancing intergranular corrosion resistance. Refines grain structure, improving strength and toughness. Also improves weld quality but may reduce material purity due to inclusions.
- Common in: Grades like 321 and 347 for improved corrosion resistance and weldability.
Niobium (Nb)
- Content: 0.1% – 0.5%
- Impact: Forms niobium carbides, preventing chromium carbide formation and enhancing resistance to intergranular corrosion. Strengthens stainless steel through precipitation hardening, improving high-temperature performance, though it may cause inclusions.
- Common in: Precipitation-hardening grades (e.g., 17-4 PH) and grade 347 for enhanced corrosion resistance.
Controlling chemical element ratios in stainless steel is vital for optimizing properties like strength and corrosion resistance. Small variations can significantly impact performance, making precise proportioning essential.
What Is the Composition of Different Types of Stainless Steel and How Do These Compositions Affect Performance?
Various types of stainless steel exist, each with a unique composition that defines its properties and suitability for specific applications. The primary types of stainless steel include austenitic, ferritic, martensitic, duplex, and precipitation-hardening stainless steel. Each type has distinct elements in its composition, impacting its performance in terms of strength, corrosion resistance, and formability.
The Composition of Austenitic Stainless Steel
Austenitic stainless steels are the most widely used type of stainless steel, known for their excellent corrosion resistance, formability, and weldability. They typically contain high levels of chromium (16-26%) and nickel (6-22%). The addition of nickel stabilizes the austenitic structure, making the steel non-magnetic and enhancing its ductility and toughness. Molybdenum is often added (2-3%) to improve protection against pitting and crevice corrosion. Common applications include kitchen appliances, chemical processing equipment, and architectural structures.
The Composition of Ferritic Stainless Steel
Ferritic stainless steels have higher chromium content (10.5-30%) and lower nickel levels than austenitic steels. They are magnetic and provide effective corrosion resistance, especially in moderate environments. The lack of significant nickel content makes them less expensive. Ferritic steels have moderate formability and are used in applications such as automotive exhaust systems, industrial equipment, and kitchen utensils. These steels are generally less ductile than austenitic steels but exhibit good resistance to stress corrosion cracking.
The Composition of Martensitic Stainless Steel
Martensitic stainless steels have significant carbon content(0.1-1.2%), which provides exceptional hardness and strength. They contain moderate chromium levels (12-18%) and are magnetic. These steels can be heat-treated to achieve various levels of hardness and strength, making them suited for applications that require wear resistance and high strength, such as cutlery, surgical instruments, and turbine blades. However, martensitic steels exhibit lower corrosion resistance compared to austenitic and ferritic steels.
The Composition of Duplex Stainless Steel
Duplex stainless steels have a mixed microstructure of austenite and ferrite, typically in equal proportions. They contain high levels of chromium (19-32%) and moderate amounts of nickel (1-8%), along with molybdenum (up to 5%) and nitrogen. This combination makes duplex steels stronger and more resistant to stress corrosion cracking and pitting than austenitic or ferritic steels on their own. Common applications include chemical processing, oil and gas industries, and marine environments.
The Composition of Precipitation-Hardening Stainless Steel
Precipitation-hardening stainless steels are engineered to attain high strength via heat treatment. They contain chromium (15-17%), nickel (4-7%), and other elements such as aluminum, copper, and niobium. These steels undergo a heat treatment process that precipitates fine particles within the metal matrix, significantly increasing strength and hardness. Precipitation-hardening steels are used in aerospace, defense, and high-performance engineering applications where high strength and good corrosion resistance are required.
Category | Grade | Composition Summary | Key Characteristics |
Austenitic Stainless Steel | 304 | Chromium (18-20%), Nickel (8-10.5%), Carbon (≤0.08%) | Excellent corrosion resistance, non-magnetic, high formability and weldability. Common in kitchen appliances and piping. |
316 | Chromium (16-18%), Nickel (10-14%), Molybdenum (2-3%), Carbon (≤0.08%) | Enhanced corrosion resistance to chlorides, ideal for marine applications and chemical processing equipment. | |
Ferritic Stainless Steel | 430 | Chromium (16-18%), Carbon (≤0.12%) | Magnetic, moderate corrosion resistance, affordable. Commonly used in automotive trims and kitchen utensils. |
409 | Chromium (10.5-11.75%), Nickel (≤0.5%), Carbon (≤0.08%) | Magnetic, lower corrosion resistance, suitable for exhaust systems and high-temperature applications. | |
Martensitic Stainless Steel | 410 | Chromium (11.5-13.5%), Carbon (≤0.15%) | Heat-treatable, strong, and hard. Used in cutlery, tools, and surgical instruments. |
420 | Chromium (12-14%), Carbon (0.15-0.4%) | High hardness, wear-resistant, commonly used in cutlery and surgical instruments. | |
Duplex Stainless Steel | 2205 | Chromium (22-23%), Nickel (4.5-6.5%), Molybdenum (3-3.5%), Nitrogen (≤0.2%) | High strength, excellent resistance to stress corrosion cracking and pitting. Used in oil, gas, and marine sectors. |
2507 | Chromium (24-26%), Nickel (6-8%), Molybdenum (3-5%), Nitrogen (≤0.3%) | Superior corrosion resistance, especially in chloride environments. Ideal for offshore and chemical processing. | |
Precipitation-Hardening Stainless Steel | 17-4 PH | Chromium (15-17.5%), Nickel (3-5%), Copper (3-5%), Niobium (0.15-0.45%) | High strength, good corrosion resistance, achieved through heat treatment. Used in aerospace and defense industries. |
15-5 PH | Chromium (14-15.5%), Nickel (3.5-5.5%), Copper (2.5-4.5%), Niobium (0.15-0.45%) | Excellent toughness and high strength, used in high-performance mechanical components. |
Composition Differences Between Stainless Steel and Non-Stainless Steel
Non-stainless steel generally refers to carbon steel or alloy steel, both of which lack the essential chromium content for corrosion resistance. The key compositional differences are as follows:
Non-Stainless Steel (e.g., Carbon Steel)
- Carbon (C): Higher carbon content, typically ranging from 0.1% to 2%, which increases hardness and strength. However, it can make the steel more brittle if not properly balanced.
- Manganese (Mn): Used to enhance strength and hardness, typically between 0.3% and 1%.
- Silicon (Si): Improves strength, usually found in amounts between 0.1% and 0.5%.
- Phosphorus (P) and Sulfur (S): Present as impurities, and their levels are kept low (below 0.05%) as they can reduce toughness and weldability.
Stainless Steel
- Chromium (Cr): Minimum 10.5%, provides excellent corrosion resistance by forming a passive oxide layer that prevents rust.
- Nickel (Ni): Added in many stainless steels (8%-20%) to improve ductility, toughness, and resistance to acids.
- Molybdenum (Mo): Typically 2%-3%, enhances resistance to pitting and crevice corrosion, especially in chloride environments.
- Lower Carbon Content: Generally less than 0.1% to prevent carbide formation that reduces corrosion resistance.
Benefits of Composition Differences
- Corrosion Resistance: Stainless steel’s high chromium and nickel content gives it superior resistance to rust and corrosion, making it ideal for harsh environments, like marine or chemical settings. In contrast, non-stainless steel is prone to rust when exposed to moisture.
- Strength and Hardness: Carbon steel’s higher carbon content makes it harder and stronger than stainless steel in many applications, but it also tends to be more brittle and less ductile, making it less ideal for applications requiring flexibility.
- Machinability: Stainless steel, especially free-machining grades, has better resistance to wear and tear, though carbon steel can be easier to machine in its lower grades due to the absence of high chromium and nickel content.
These differences highlight the versatility of stainless steel for corrosion-resistant and durable applications, while non-stainless steel offers greater strength and hardness at lower costs.
Is Stainless Steel 100% Steel?
No, stainless steel is not 100% steel. It is an alloy composed primarily of iron (like traditional steel) but also contains key elements such as chromium, nickel, and sometimes molybdenum. These additional elements give stainless steel its enhanced properties, like corrosion resistance.
Does Stainless Steel Rust?
Stainless steel can rust, but it is highly resistant to rust compared to regular steel. The chromium content (at least 10.5%) forms a protective oxide layer on the surface, preventing rust in most environments. However, in extreme conditions like high salinity or acidity, stainless steel can still corrode or develop surface rust.
Is There BPA in Stainless Steel?
No, stainless steel does not contain BPA (Bisphenol A). BPA is a chemical used in some plastics and resins, but stainless steel is free from BPA and is considered safe for food and beverage storage, making it a popular choice for cookware and water bottles.
What Are The Ingredients In Stainless Steel?
Stainless steel primarily consists of iron, with key elements such as chromium, nickel, molybdenum, carbon, manganese, silicon, and nitrogen added to enhance its properties. These elements provide good properties like corrosion resistance, strength, and ductility.
What Is The Best Composition Of Stainless Steel?
The best composition of stainless steel depends on the intended application. Austenitic stainless steels (with high chromium and nickel content) are commonly used for corrosion resistance and formability. For high strength and hardness, martensitic stainless steels (with higher carbon content) are suitable. Duplex stainless steel balances strength and corrosion resistance.
Is There Lead In Stainless Steel?
No, there is no lead in stainless steel. It is composed primarily of iron, chromium, nickel, and other elements that enhance its properties, but lead is not one of them. Stainless steel is considered safe and is often used in applications requiring sanitation and cleanliness, such as cookware and medical instruments.
Conclusion
Understanding the composition of stainless steel and its key elements helps in choosing the right type for specific applications. Each element, from chromium to nitrogen, adds unique properties that make stainless steel versatile and durable. Knowing the composition helps you choose between the corrosion resistance of austenitic, the strength of martensitic, or the balanced properties of duplex stainless steel. Stainless steel’s adaptability ensures it remains a vital material across various industries, providing long-lasting and reliable results.
- Stainless Steel Grades
- 300 Series Stainless Steel
- 303 Stainless Steel
- 304 Stainless Steel
- 305 Stainless Steel
- 308 Stainless Steel
- 316 Stainless Steel
- 316N Stainless Steel
- 409 Stainless Steel
- 410 Stainless Steel
- 416 Stainless Steel
- 420 Stainless Steel
- 430 Stainless Steel
- 410HT And 410L Stainless Steels
- 410S Stainless Steel
- 440 Stainless Steel
- 436 Stainless Steel
- 301 Stainless Steel
- 201 Stainless Steel
- 202 Stainless Steel
- 444 Stainless Steel
- 405 Stainless Steel
- 302 Stainless Steel
- 309 Stainless Steel
- 314 Stainless Steel
- 321 Stainless Steel
- 347 Stainless Steel
- 408 Stainless Steel
- 422 Stainless Steel
- 431 Stainless Steel
- 434 Stainless Steel
- 414 Stainless Steel
- 430FR Stainless Steel
- 13-8 PH Stainless Steel
- 317 | 317L Stainless Steel
- 616 Stainless Steel
- 630 Stainless Steel
- 904L Stainless Steel
- A2 Stainless Steel
- 304 vs 304L Stainless Steel
- 304 VS 316 Stainless Steel
- 304 vs 409 Stainless Steel
- 304 vs 430 Stainless Steel
- 410 Stainless Steel vs 304
- 18/0 vs 18/10
- 18/0 Stainless Steel
- 18/8 Stainless Steel
- 18/10 Stainless Steel
Comparisons