Contents
Stainless Steel Finishes: A Comprehensive Guide
- John
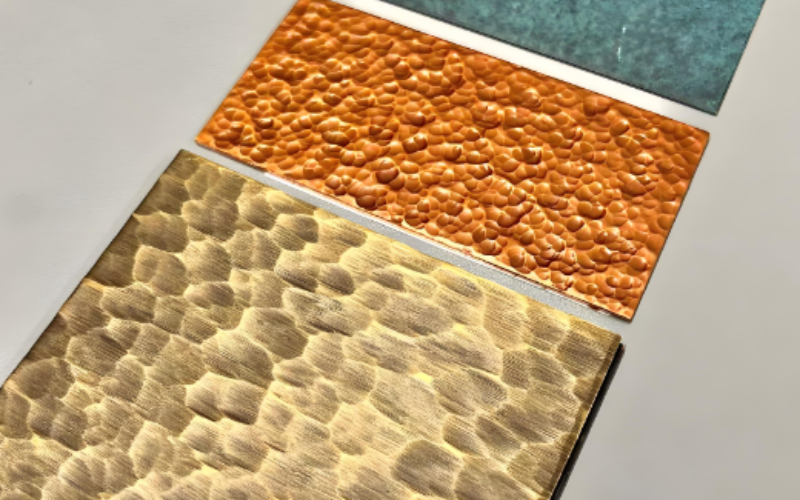
The finish of stainless steel not only enhances its aesthetic appeal but also improves the material’s surface properties, making it more durable. Different surface treatments can be applied to meet the demands of various challenging conditions, making it crucial to select the right treatment.
If you’re looking to customize surface treatments with SteelPro Group, we recommend reading this article to understand the subtle differences between each treatment, ensuring that our offerings align with your expectations. Additionally, if you’re unsure which surface treatment best fits your needs, this article will help clarify your options.
What Is Stainless-Steel Surface Finish?
A stainless-steel surface finish refers to the texture or smoothness of the metal’s surface, achieved through various mechanical or chemical processes. It is influenced by the treatment method, the steel’s composition, and the working environment as well as contaminants.
A proper surface finish enhances the metal’s durability, corrosion resistance, and appearance, making it suitable for specific environments or uses.
There are several industry standards for stainless steel surface finishes, such as those from ASTM, ISO, and EN, which define the quality, texture, and performance of these finishes to ensure consistency and suitability for various industrial applications.
What is the Surface Roughness of Stainless Steel?
The surface texture of stainless steel refers to the tiny imperfections on the metal’s exterior, usually quantified as Ra (mean roughness). It is influenced by factors like the finishing process, the type of stainless steel, and the tools used. Common Ra values for stainless steel range from 0.1 to 3.2 micrometers, depending on the level of smoothness required for the application.
Higher Ra values can lead to increased susceptibility to corrosion, as rougher surfaces may trap contaminants and moisture. Smaller Ra measurements, which signify smoother surfaces, are frequently applied in sectors such as food production and pharmaceuticals due to their improved corrosion resistance. Testing shows that stainless steel with high surface roughness suffers significant damage during polishing, while low roughness steel remains relatively unaffected.
3 Major Stainless Steel Finishes
Stainless steel surface treatments are typically divided into three primary groups depending on the process and intended function: mill finishes, brushed and polished finishes, and bright annealed (BA) and temper rolled (TR) finishes. These treatments vary in surface feel, look, and functionality, making them appropriate for a range of industrial and commercial uses.
Mill Finishes
Mill finishes are the standard finishes applied directly during stainless steel production, offering basic surface smoothness without further treatment. They are practical and commonly applied in situations where aesthetics are not the main focus. Listed below are the primary forms of mill finishes:
No. 1 Finish
- Surface: Coarse, uneven texture with a non-reflective, matte appearance. A visible scale or oxide layer may be present from the hot rolling process.
- Process: Hot rolling, annealing, descaling.
- Common Grades: 304, 316
- Applications: Furnace parts, tanks, structural components, boilers, heavy machinery, and heat-resistant equipment.
No. 2B Finish
- Surface: Smooth, uniform, and semi-reflective, with a light sheen that enhances cleanliness. No visible imperfections, making it suitable for areas requiring a cleaner appearance. 2B is the most common mill finish, with a smooth surface and slight gloss.
- Process: Cold rolling, annealing, pickling, light rolling pass.
- Common Grades: 304, 316, 430
- Applications: Food processing equipment, chemical containers, pharmaceutical equipment, kitchen appliances, architectural elements, and medical instruments.
No. 2D Finish
- Surface: Non-reflective, dull, and flat with a uniform texture. Less smooth than the No. 2B finish, often with a faint grain pattern but no reflective shine.
- Process: Cold rolling, annealing, pickling. (no light rolling pass)
- Common Grades: 304, 430
- Applications: Chemical plants, heat exchangers, industrial equipment, piping, furnace parts, and refrigeration units.
No. 2H Finish
- Surface: Hardened, smooth, with slight texture variation due to cold rolling. Stronger and more rigid compared to other mill finishes, with limited reflectivity.
- Process: Cold rolling, hardening
- Common Grades: 301, 304
- Applications: Automotive parts, springs, fasteners requiring higher strength, structural supports, pressure vessels, and aerospace components.
Brushed and Polished Finishes
Brushed and polished treatments are obtained via mechanical methods that improve the surface’s smoothness and visual attractiveness. These finishes have a more refined appearance compared to mill finishes and are commonly used in decorative or visible applications. Below are the main types of brushed and polished finishes:
No. 3 Finish
- Surface: Coarse but smoother than mill finishes, with a visible grain pattern created by abrasive belts. The surface is uniform and has a satin-like appearance but is not highly reflective.
- Process: Polished with abrasive belts of a grain size around 100–120 grit.
- Common Grades: 304, 316
- Applications: Kitchen equipment, elevator panels, architectural trim, and food processing equipment.
No. 4 Finish
- Surface: Even and non-reflective, featuring a subtle, directional grain design. It is among the most favored finishes due to its neat appearance and low upkeep.
- Process: Polished with finer abrasive belts, typically 150–180 grit.
- Common Grades: 304, 316, 430
- Applications: Appliances, kitchen surfaces, escalators, sinks, medical devices, and signage.
No. 6 Finish
- Surface: Dull, satin-like appearance with less visible grain than the No. 4 finish. This finish has more of a soft sheen and provides a smoother texture.
- Process: Polished with fine abrasive belts, followed by Tampico brushing.
- Common Grades: 304, 316
- Applications: Architectural elements, furniture, kitchen utensils, and interior design features.
No. 7 Finish
- Surface: Highly reflective with a near-mirror appearance but still shows some fine polishing lines. Achieves a high level of shine without being fully reflective.
- Process: Polished with fine abrasive belts, followed by buffing.
- Common Grades: 304, 316
- Applications: Elevator doors, automotive trim, architectural panels, and decorative components.
No. 8 (Mirror) Finish
- Surface: Ultra-smooth, highly reflective mirror finish with no visible grain lines. This finish is polished to perfection and is often used for its premium, glossy appearance.
- Process: Refined using progressively finer abrasives, then completed with thorough buffing.
- Common Grades: 304, 316
- Applications: Mirrors, ornamental trim, luxury architectural projects, and high-end appliances.
Satin Finish
- Surface: Satin finish has a smooth, non-reflective surface with a fine-grain texture. It provides a soft sheen without the high reflectivity of mirror finishes.
- Process: Using abrasive belts or brushes, typically between 120 to 320 grit, depending on the required smoothness.
- Common Grades: 304, 316, 430
- Applications: Kitchen appliances, architectural elements, elevators, and interior design for surfaces, handrails, fixtures, and automotive trim.
Bright Annealed (BA) and Temper Rolled (TR) Finishes
Bright annealed (BA) and temper rolled (TR) finishes are created through specific thermal and mechanical processes to achieve a highly reflective or smooth surface. These finishes are typically used in applications that require a sleek appearance and enhanced corrosion resistance. Below are the main types of BA and TR finishes:
Bright Annealed (BA) Finish
- Surface: Smooth, highly reflective, and mirror-like. This finish is obtained by heat-treating in a regulated environment to avoid oxidation, producing a shiny, spotless surface without any scaling.
- Process: Cold rolling, followed by annealing in an oxygen-free environment. (typically in a vacuum or inert gas atmosphere)
- Common Grades: 304, 316, 430
- Applications: Reflective surfaces in architectural applications, household appliances, kitchen equipment, and food processing equipment.
2R Finish
- Surface: Similar to BA finish but with a more consistent and uniform mirror-like appearance. The surface is extremely smooth and reflective.
- Process: Cold rolling, bright annealing, and skin pass rolling for additional smoothness
- Common Grades: 304, 316
- Applications: High-end appliances, chemical tanks, pharmaceutical equipment, and laboratory environments.
Temper Rolled (TR) Finish
- Surface: Smooth, uniform, and with a semi-reflective finish. The surface is flatter and harder due to the temper rolling process, which enhances the steel’s strength and toughness.
- Process: Cold rolling followed by temper rolling to increase hardness and flatness
- Common Grades: 301, 304, 316
- Applications: Automotive parts, springs, structural components, and industrial applications requiring higher strength and durability.
Special Stainless Steel Finishes
In addition to the three main categories of finishes, there are special surface treatments designed to enhance specific properties of stainless steel. These treatments are used to improve corrosion resistance, durability, cleanliness, or surface aesthetics, making stainless steel more suitable for specialized applications.
Blasting
- Surface: Matte or textured, with a uniform finish depending on the abrasive material used.
- Process: Abrasive blasting with substances such as sand, glass beads, or steel particles.
- Common Grades: 304, 430, 201
- Applications: Architectural panels, industrial machinery, piping, automotive components, decorative finishes
Electropolishing
- Surface: Smooth, bright, and reflective, with enhanced corrosion resistance and cleanliness.
- Process: Electrochemical polishing, removal of a thin layer, microscopic smoothing
- Common Grades: 316L, 304L, 904L
- Applications: Pharmaceutical equipment, food processing equipment, medical devices, cleanroom components, sanitary fittings
Chromizing
- Surface: Hard, corrosion-resistant, slightly reflective with a chromium-enriched outer layer.
- Process: Diffusion of chromium into the surface, heat treatment, surface hardening
- Common Grades: 410, 420, 310
- Applications: Turbine blades, industrial machinery, wear-resistant components, cutting tools, aerospace parts
Chequered Finish
- Surface: Raised, patterned surface with a checkerboard or diamond-shaped texture for enhanced grip and aesthetic appeal.
- Process: Rolling, pressing, imprinting, polishing.
- Common Grades: 304, 316, 430
- Applications: Flooring, stair treads, walkways, ramps, elevators, vehicle footplates, and decorative elements in architecture.
Colored Finish
- Surface: Smooth or textured surface with a vibrant, colored appearance for aesthetic enhancement.
- Process: Electroplating, anodizing, PVD coating, painting.
- Common Colors: Black, gold, bronze, blue, green, red, purple, rainbow.
- Common Grades: 304, 316, 430
- Applications: Decorative panels, interior design, household appliances, automotive parts, architectural features.
The Most Popular Finishes for Different Shapes
Stainless steel surface finishes vary depending on the shape of the material. Different forms like pipes, tubing, coils, wires, sheets, plates, bars, rods, and cables require specific finishing processes to optimize their performance for particular applications.
Stainless Steel Pipe
- Common Process: Brushing, polishing, or blasting
- Features: Smooth, uniform surface for enhanced corrosion resistance, often used in plumbing and industrial systems
Stainless Steel Tubing
- Common Process: Electropolishing, passivation
- Features: Bright, smooth interior for hygiene, suitable for medical, pharmaceutical, and food processing applications
Stainless Steel Coil
- Common Process: Annealing, temper rolling
- Features: Consistent, smooth surface with excellent flexibility, frequently utilized in the automotive and building sectors
Stainless Steel Wire
- Common Process: Drawn, bright annealed
- Features: Smooth, bright finish for electrical conductivity, corrosion resistance, and strength
Stainless Steel Sheet
- Common Process: No. 2B, No. 4, bright annealed, mirror finish
- Features: Available in various finishes from matte to reflective, used in architectural and industrial applications
Stainless Steel Plate
- Common Process: No. 1 finish, hot rolling
- Features: Coarse surface with high strength, suitable for heavy industrial uses like construction and shipbuilding
Stainless Steel Bar
- Common Process: Brushed, ground, or polished
- Features: Even surface for mechanical parts, applied in production, construction, and ornamental uses
Stainless Steel Rod
- Common Process: Polished, passivated
- Features: High strength and smooth finish, used in fasteners and industrial machinery
Stainless Steel Cable
- Common Process: Bright drawn, passivation
- Features: Corrosion-resistant, flexible, and strong, used in rigging, architecture, and transportation industries
The above are just some of the common surface finishing methods for various stainless steel shapes. However, you can also customize other surface treatments based on your specific requirements to achieve the desired performance and appearance.
Comparison of Different Stainless Steel Finishes Chart
Stainless steel surface finishes vary in appearance, durability, and maintenance costs. Each finish offers different benefits depending on the application. Presented is a comparison of the three primary varieties of stainless steel surface treatments.
Criteria | Mill Finishes | Brushed and Polished Finishes | Bright Annealed (BA) and Temper Rolled (TR) Finishes |
Appearance | Matte, rough, non-reflective surface. | Satin or smooth with visible grain lines. | Highly reflective, mirror-like, or semi-reflective surface. |
Durability & Scratch Resistance | Durable but can scratch easily due to rough texture. | Moderately durable, scratches are visible but less noticeable on brushed surfaces. | Very durable, high resistance to scratches, especially in tempered finishes. |
Corrosion Resistance | Good, but rough surfaces may trap contaminants. | Better corrosion resistance due to smoother surfaces. | Excellent corrosion resistance with very smooth surfaces. |
Maintenance | Low maintenance, appearance not a priority. | Moderate, needs regular cleaning to avoid dirt in grain lines. | Low, easy to clean, but needs care to avoid scratches. |
Cost | Lower cost, minimal finishing. | Medium cost, more processing involved. | Higher cost, due to extra finishing steps. |
How to Choose the Right Finish for Your Application
Consider the Environment
If your use case is in a tough setting, such as close to the sea or in industrial zones, select a finish with strong corrosion resistance. Bright annealed finishes are ideal for environments with moisture or chemicals due to their smooth surface.
Focus on Appearance
For visible or decorative applications, polished or brushed finishes offer a clean, refined look. A No. 4 finish is a popular choice for its smooth, satin appearance. If you need a mirror-like shine, go for a No. 8 or bright annealed finish.
Think About Durability
For high-traffic areas or where surfaces are likely to face wear and tear, consider finishes that are scratch-resistant. Temper rolled finishes provide extra durability, while brushed finishes can hide small scratches better than smooth, reflective surfaces.
Factor in Maintenance
If ease of cleaning is important, choose a smooth surface finish like bright annealed, which is easy to wipe down. Brushed finishes may require more regular maintenance to prevent dirt from accumulating in the grain.
Budget Considerations
If cost is a concern, mill finishes are often the most affordable. However, for applications that need a more refined appearance or better durability, investing in polished or bright annealed finishes can provide long-term savings by reducing maintenance and replacement costs.
Surface Cleaning and Maintenance Tips for Stainless Steel Finishes
Correct cleaning and upkeep can prolong the lifespan and look of stainless steel surfaces. Different environments, such as industrial or home use, require specific care.
Industrial Environment
In industrial settings, stainless steel is exposed to harsher conditions, such as chemicals and heavy use.
- Use mild detergents or specialized stainless steel cleaners to remove dirt and grime.
- For tougher stains, use non-abrasive cleaners or diluted vinegar.
- Regularly clean to prevent buildup, especially in brushed or rough finishes that may trap contaminants.
- Refrain from using steel wool or harsh tools that may damage the surface and cause corrosion.
Home Environment
For home use, such as kitchen appliances or decorative surfaces, maintenance is simpler.
- Wipe surfaces with a soft cloth and warm water for daily cleaning.
- Use a mild soap or stainless steel cleaner for fingerprints or smudges.
- Polish with a microfiber cloth to maintain a shiny appearance, especially for polished finishes.
- Steer clear of strong chemicals or rough sponges that could harm the surface.
Which is the most suitable coating for stainless steel?
PVD (Physical Vapor Deposition) coating is highly suitable for stainless steel, offering enhanced durability and corrosion resistance.
What makes stainless steel shiny again?
Polishing with a fine abrasive or using a stainless steel cleaner can restore the shine to stainless steel.
What coating prevents stainless steel from rusting?
Electropolishing or passivation are common coatings/treatments that prevent stainless steel from rusting by enhancing its corrosion resistance.
How to restore blackened stainless steel?
Use a stainless steel cleaner or a mixture of baking soda and water to clean and buff the blackened areas, then polish to restore the original appearance.
Click here to learn how to clean stainless steel.
What finish is closest to stainless steel?
A satin or brushed finish is closest to the natural look of stainless steel, providing a smooth, matte appearance.
Custom Surface Finishing Now
Choosing the right stainless steel finish is important for getting the look and durability you need. Whether it’s for decorative panels, industrial equipment, or home appliances, understanding the finishes helps you make the best decision.
SteelPRO Group offers customized surface finishing services to meet your specific requirements, whether for sheets or bars. From blasting, and polishing, to corrosion-resistant treatments, we can handle it all! Tell us your requirements, and we will assist in ensuring your project’s success. For more information on stainless steel surface finish, please contact our experts for the best quotes!
- Stainless Steel Grades
- 300 Series Stainless Steel
- 303 Stainless Steel
- 304 Stainless Steel
- 305 Stainless Steel
- 308 Stainless Steel
- 316 Stainless Steel
- 316N Stainless Steel
- 409 Stainless Steel
- 410 Stainless Steel
- 416 Stainless Steel
- 420 Stainless Steel
- 430 Stainless Steel
- 410HT And 410L Stainless Steels
- 410S Stainless Steel
- 440 Stainless Steel
- 436 Stainless Steel
- 301 Stainless Steel
- 201 Stainless Steel
- 202 Stainless Steel
- 444 Stainless Steel
- 405 Stainless Steel
- 302 Stainless Steel
- 309 Stainless Steel
- 314 Stainless Steel
- 321 Stainless Steel
- 347 Stainless Steel
- 408 Stainless Steel
- 422 Stainless Steel
- 431 Stainless Steel
- 434 Stainless Steel
- 414 Stainless Steel
- 430FR Stainless Steel
- 13-8 PH Stainless Steel
- 317 | 317L Stainless Steel
- 616 Stainless Steel
- 630 Stainless Steel
- 904L Stainless Steel
- A2 Stainless Steel
- 304 vs 304L Stainless Steel
- 304 VS 316 Stainless Steel
- 304 vs 409 Stainless Steel
- 304 vs 430 Stainless Steel
- 410 Stainless Steel vs 304
- 18/0 vs 18/10
- 18/0 Stainless Steel
- 18/8 Stainless Steel
- 18/10 Stainless Steel
Comparisons