Contents
Mill Finish Stainless Steel Explain
- John
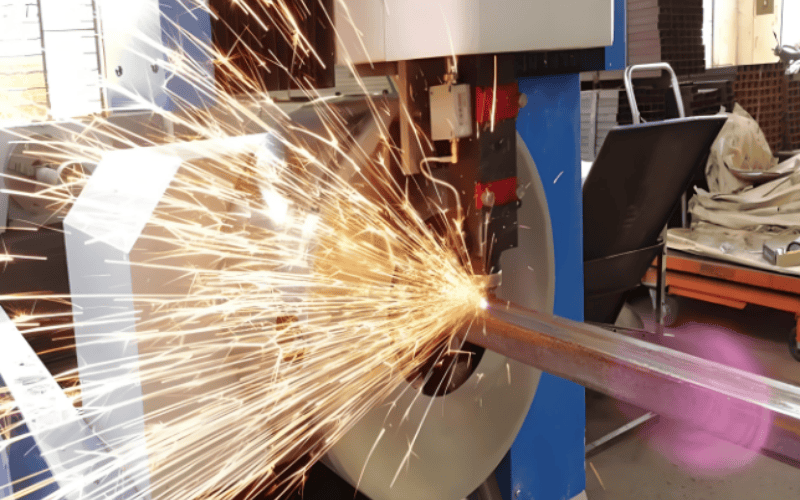
Understanding the basic concepts of milling, the machining process, and how it compares to other surface treatments is essential to choosing the right stainless steel for your application. In this article, we will delve into the details of rolled surface stainless steel, its general process, the characteristics of rolled stainless steel, applications, and maintenance. We will also compare rolled surfaces to brushed and polished surfaces.
What is Mill Finish Stainless Steel?
Finished stainless steel is the original finish stainless steel has after it is manufactured in the factory and is the most basic form of surface treatment. It has not undergone additional polishing or treatment and has a dull, matte appearance with slight texture variations resulting from the rolling process. This finish is favored for its industrial beauty, durability, and cost-effectiveness.
General Process of Milling
The milling process can be divided into several main stages, each of which has an important impact on the final surface effect:
Raw material preparation: The milling process begins with the selection of raw materials. High-quality stainless steel sheets or strips are usually selected as the base material to ensure the performance of the final product.
Preliminary heat treatment: The initial heat treatment stage involves a hot rolling process, which is usually performed under high temperature conditions and aims to reduce the thickness of the metal material through heating and rolling, and effectively eliminate the accumulated stress inside it.
Cold rolling: Cold rolling is performed on the basis of hot rolling to further reduce the thickness of the material and improve its surface finish. The surface after cold rolling is usually smoother, but still retains the original texture and characteristics.
Pickling and annealing: Pickling is used to remove surface oxides and impurities, while annealing helps to improve the mechanical properties of the metal. These two steps can ensure that the milled surface has good corrosion resistance and stability during use.
Surface treatment: The surface flatness needs to be corrected after milling to ensure product quality.
Quality inspection: Milled stainless steel needs to be inspected to check the finish, accuracy and appearance to ensure compliance with standards.
Types of Mill Finishes
Due to the process and application characteristics, milling types can be divided into the following types.
No. 1 Finish
No. 1 finish is manufactured by hot rolling, annealing and pickling. It is the roughest and least reflective finish, characterized by a dark, non-uniform appearance. This finish is primarily used in applications where aesthetic appearance is not a priority, such as furnace parts, gas turbines, and industrial boilers.
No. 2D Finish
No. 2D finish is manufactured by cold rolling, annealing, and pickling. It results in a smooth, non-reflective matte surface. This finish is suitable for applications requiring a clean, non-reflective surface, such as automotive exhaust systems, chemical equipment, and roofing accessories.
No. 2B Finish
The No. 2B finish is similar to the No. 2D finish but includes an additional light temper pass through polished rolls, giving it a smooth, somewhat reflective surface. It is the most widely used mill finish for its versatility and is commonly found in kitchen equipment, pharmaceutical equipment, and architectural applications.
Bright Annealed (BA) Finish
Bright annealing (BA) treatment is to anneal stainless steel in a specific atmosphere to avoid oxidation and directly produce a high-gloss, mirror-smooth surface without additional polishing. This surface treatment is often used in decoration, kitchenware and medical surgical instruments.
No. 0 Finish
No. 0 Finish is a stainless steel surface treated by hot rolling and annealing. No. 0 Finish has a rough surface, usually with scale, and is mainly used in industrial applications where surface finish is not required, such as structural parts and parts in high temperature environments.
2H Finish
2H surface treatment is a stainless steel surface obtained after cold rolling hardening. Smooth and reflective, it is ideal for applications where high strength and hardness are required, such as springs and high-strength parts.
2Q Finish
2Q Finish is a stainless steel surface treatment method that is cold rolled, quenched and tempered. 2Q Finish has a smooth surface with high strength and good reflectivity, and is suitable for applications that require high strength and high corrosion resistance, such as knives and wear-resistant parts.
2M Finish
2M Finish is a decorative stainless steel surface obtained by cold rolling and pattern rolling. The surface of 2M Finish has a unique visual effect and is often used for architectural decoration, interior decoration and other applications that require a beautiful appearance.
2B Finish vs No.4 Finish
Attribute | 2B Finish | No. 4 Finish |
Outward | Smooth, slightly reflective | Brushed, with visible parallel lines |
Application | cookers, small storage tanks and pharmaceutical equipment | Kitchen appliances, hospital equipment, food processing equipment |
Cost | Generally lower than No. 4 finish | Higher due to additional brushing process |
Suitable Stainless Steels for Milling
Mill finish is suitable for various grades of stainless steel, including:
304/304L Stainless steel: Widely used due to its balance of strength, corrosion resistance, and affordability.
316/316L stainless steel: Resistant to corrosion by chlorides and industrial solvents. 316 is preferred in marine and harsh chemical environments.
430 stainless steel: Economical and used in applications where moderate corrosion resistance is sufficient, such as in indoor environments and mild industrial conditions.
Mill Finish Stainless Steel Forms
Here are the common forms of mill finish stainless steel:
Mill finish stainless steel plate: Thick, flat pieces used in structural applications and heavy machinery.
Mill finish stainless steel sheet: Thinner than plates, used for lighter applications, including automotive and appliance manufacturing.
Mill finish stainless steel bar: Available in various shapes (round, square, hexagonal); used for construction, machining, and fabrication.
Mill finish stainless steel tube: Hollow, cylindrical shapes used in various applications, including construction, plumbing, and automotive.
Mill finish stainless steel pipe: Specifically designed for transporting fluids and gases; often used in plumbing and industrial applications.
Characteristics of Mill Finish Stainless Steel
Compared with other surface treatment methods such as polishing and brushing, the surface effect of milling is relatively basic, but its economy and practicality make it the first choice in many applications.
Economical
Milling is a basic surface treatment method with a lower cost than polishing or mirror treatment. Suitable for projects that require large-scale production and have limited budgets. Due to its simple processing process, milling can effectively control production costs.
Original appearance
The milled surface usually maintains the natural texture of the metal without additional brightening treatment. Although this treatment does not provide a high degree of finish, it provides a basis for subsequent processing or decoration.
Stable performance
The honed surface is rugged and wear-resistant for harsh environments. The lack of a highly polished surface means honed stainless steel requires minimal maintenance and cleaning.
Wide range of applications
Milling treatment is suitable for various types of stainless steel materials and is the basic treatment method for many industrial applications. It is broadly applied in various fields such as construction, automotive, chemical and food processing.
Applications of Mill Finish Stainless Steel
Construction engineering: Milled surfaces are often used for structural components and decorative materials due to their corrosion resistance and strength, which can meet the durability requirements of building structures. Common applications include building support frames, exterior wall panels and decorative strips.
Automotive industry: In automobile manufacturing, milled stainless steel is used as a base material to produce various automotive parts. These parts include exhaust systems, body frames and internal structural parts. The milled surface can withstand high temperatures and mechanical wear, and is a common material in the automotive industry.
Chemical industry: Milled stainless steel is often used in chemical reactors, pipelines, storage tanks and other equipment because the milled stainless steel has excellent chemical corrosion resistance, ensuring long-term and stable operation of the equipment.
Home appliances: In the home appliance industry, milled stainless steel is used to manufacture parts such as refrigerator shells and washing machine inner drums. Due to the durability and basic corrosion resistance of the milled surface, it can meet the basic requirements of home appliances for materials.
Food processing: In food processing equipment, milled stainless steel is used to make various food processing machinery and containers. The corrosion resistance and cleanliness of the milled surface make it an ideal choice for the food processing industry.
How to Maintain Mill Finish Stainless Steel?
Maintaining milled stainless steel can extend its service life and maintain a good appearance, mainly including the following points.
- Regular cleaning: Use a mild detergent and a soft cloth to clean the milled surface regularly to remove dirt and stains. Avoid using strong acid or strong alkaline detergents to prevent damage to the surface.
- Prevent corrosion: Avoid contact with strong acids or strong alkalis to prevent corrosion. Although milled stainless steel has good corrosion resistance, it may still corrode if exposed to corrosive environments for a long time. Keeping the stainless steel surface away from corrosive substances can extend its service life.
- Avoid scratches: Avoid scratching the surface with hard objects to prevent scratches and wear. Milled surfaces are relatively rough and easily scratched by hard objects, resulting in surface damage. Use soft cloths and non-abrasive cleaning tools to effectively avoid scratches.
- Regular inspections: Check the surface condition regularly and deal with possible corrosion or damage problems in a timely manner to ensure the long-term use of stainless steel materials.
Mill Finish vs Brushed & Polished Finishes
Mill finish, brushed finish, and polished finish have distinct differences in appearance, maintenance, cost, durability, and applications.
Mill finish has a dull, matte appearance with slight texture variations and requires minimal maintenance. It is more cost-effective due to fewer processing steps and offers high durability. This type of finish is often suitable for industrial, construction, and marine applications.
On the other hand, brushed finish provides a smooth surface with visible brush lines and a satin-like sheen. It requires regular cleaning to maintain its appearance, and the cost is higher due to additional processing. The durability of brushed finish is moderate, and it is commonly used in kitchen appliances, architectural elements, and automotive trim.
Polished finish has a bright, mirror-like shine and requires frequent cleaning and care to maintain its appearance. It is the most expensive option due to extensive processing. While polished finishes are prone to scratches and smudges, they are often used for decorative elements, high-end appliances, and architectural features.
Related Reading
How to Clean Stainless Steel?
What Is Surface Roughness?
Surface roughness is a measure of the texture of a surface, usually measured in microns (µm). Surface roughness affects how easily the steel can be cleaned, its frictional properties, and its ability to resist corrosion. Commonly used parameters include:
RA (Average Roughness): Indicates the average surface roughness, which is a commonly used parameter in North America. It describes the smoothness of the surface by calculating the average value of the high and low points of the surface. The smaller the RA value, the smoother the surface.
Rz (Mean Roughness Depth): Indicates the maximum peak-to-valley depth of the surface, which is a commonly used parameter in Europe. It describes the roughness of a surface by measuring the depth between the highest and lowest points on the surface. The larger the Rz value, the rougher the surface.
What Is the RA of Mill Finish Stainless Steel?
The Ra (Roughness Average) of mill finish stainless steel typically ranges from about 0.8 to 3.2 micrometers (32 to 125 microinches). This roughness can vary depending on the specific processing and finishing methods used.
Stainless Steel Finishes Chart
In addition to Mill Finish, Brushed Finish, and Polished Finish, there are many other types of surface finishes for stainless steel, each with unique characteristics and areas of application.
Finish Type | Description | Application |
Mill Finish | Standard finish with a rough surface, typically used as the starting point for other finishes. | General fabrication and construction. |
Brushed Finish | Soft, linear texture created by brushing with abrasive pads. | Appliances, fixtures, and decorative applications. |
Polished Finish | Highly reflective surface achieved through buffing. | High-end applications, jewelry, and decorative items. |
Satin Finish | Smooth, low-reflectivity surface with minimal texture. | Architectural elements and kitchen equipment. |
Bead Blasted Finish | Non-directional matte texture created by blasting with beads. | Architectural decoration and art installations. |
Electropolished Finish | Highly reflective and smooth surface from electrochemical polishing. | Medical instruments and food processing equipment. |
Etched Finish | Decorative patterns etched into the surface. | Architectural panels and decorative trims. |
Colored Finish | Surface colored through PVD and other technologies for rich visual effects. | Interior design and decorative products. |
Textured Finish | Patterned texture created by rolling or pressing. | Elevator interiors and building facades. |
Passivated Finish | Enhanced corrosion resistance achieved by removing free iron. | Chemical equipment and medical devices. |
Matte Finish | Non-reflective surface created by grinding or sandblasting. | Industrial applications and automotive parts. |
What is the Best Surface Treatment Type for Stainless Steel?
Choosing the best stainless steel surface treatment requires considering many factors depending on the specific application and requirements.
Application requirements: Select the appropriate surface treatment according to the specific application requirements. For example, architectural decoration may require Brushed Finish, while food processing equipment may be more suitable for 2B Finish.
Budget constraints: Select an economical treatment method based on the project budget. For example, Mill Finish is a suitable choice for projects with limited budgets.
Appearance requirements: Select a bright or smooth treatment method based on the requirements for appearance. For example, decorative parts that require a high visual effect can choose Polished Finish.
Durability requirements: Selection of appropriate treatments for corrosion resistance and mechanical properties. For example, chemical equipment may require No. 4 Finish to improve corrosion resistance.
Get Satisfactory Stainless Steel!
If you’re wondering about mill finish stainless steel products, or wondering if a certain finish is right for you, SteelPRO Group is here to help. Click here to learn more about stainless steel, or contact our sales team today to discuss your project requirements.
- Stainless Steel Grades
- 300 Series Stainless Steel
- 303 Stainless Steel
- 304 Stainless Steel
- 305 Stainless Steel
- 308 Stainless Steel
- 316 Stainless Steel
- 316N Stainless Steel
- 409 Stainless Steel
- 410 Stainless Steel
- 416 Stainless Steel
- 420 Stainless Steel
- 430 Stainless Steel
- 410HT And 410L Stainless Steels
- 410S Stainless Steel
- 440 Stainless Steel
- 436 Stainless Steel
- 301 Stainless Steel
- 201 Stainless Steel
- 202 Stainless Steel
- 444 Stainless Steel
- 405 Stainless Steel
- 302 Stainless Steel
- 309 Stainless Steel
- 314 Stainless Steel
- 321 Stainless Steel
- 347 Stainless Steel
- 408 Stainless Steel
- 422 Stainless Steel
- 431 Stainless Steel
- 434 Stainless Steel
- 414 Stainless Steel
- 430FR Stainless Steel
- 13-8 PH Stainless Steel
- 317 | 317L Stainless Steel
- 616 Stainless Steel
- 630 Stainless Steel
- 904L Stainless Steel
- A2 Stainless Steel
- 304 vs 304L Stainless Steel
- 304 VS 316 Stainless Steel
- 304 vs 409 Stainless Steel
- 304 vs 430 Stainless Steel
- 410 Stainless Steel vs 304
- 18/0 vs 18/10
- 18/0 Stainless Steel
- 18/8 Stainless Steel
- 18/10 Stainless Steel
Comparisons