Contents
436 Stainless Steel: Composition, Properties, Applications, Processes and More
- John
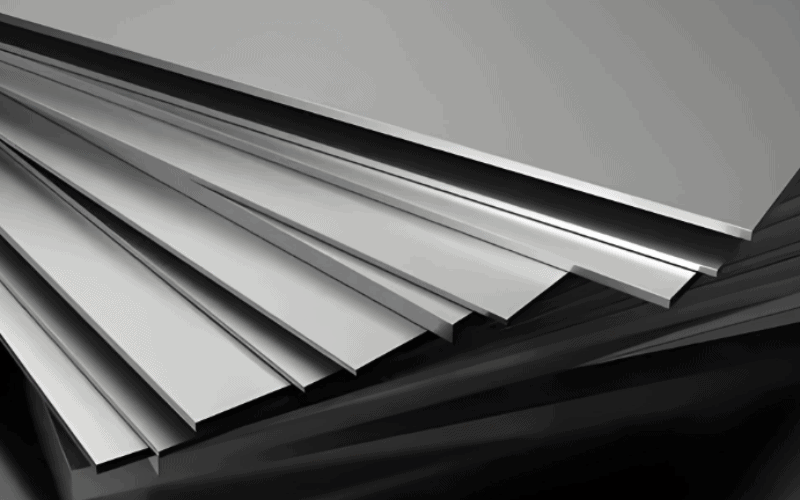
We will present in detail the chemical composition, physical and mechanical properties, product types, advantages and disadvantages, typical applications, and processing methods of 436 stainless steel to help you fully understand the advantages and application prospects of this versatile alloy.
What is 436 Stainless Steel?
436 is a ferritic stainless steel consisting primarily of iron and chromium that has excellent corrosion resistance and good formability. As an improvement of 430 and 434, it reduces the “drawing” or “wrinkling” phenomenon during forming by adding molybdenum and niobium, while enhancing the resistance to oxidation and high temperature. It is ideal for industries like automotive, aerospace and construction.
436 stainless steel equivalent grades
Just like many alloys, 436 stainless steel has several equivalents based on regional or international standards.
- UNS: S43600
- SAE: 51436
- JIS: SUS 436
436 stainless steel standard
ASTM A240, ASME SA240, AMS 5503
Chemical Composition of 436 Stainless Steel
Element | Composition Range |
Carbon (C) | ≤ 0.12% |
Manganese (Mn) | ≤ 1.00% |
Silicon (Si) | ≤ 1.00% |
Chromium (Cr) | 16.0% – 18.0% |
Nickel (Ni) | ≤ 0.50% |
Molybdenum (Mo) | 0.75% – 1.25% |
Sulfur (S) | ≤ 0.030% |
Phosphorus (P) | ≤ 0.040% |
Titanium (Ti) | ≤ 0.75% |
- Molybdenum (Mo): Molybdenum further increases corrosion resistance, particularly when exposed to chloride-containing environments such as brine or de-icing salts.
- Columbium (Nb): The addition of columbium (niobium) improves the alloy’s resistance to roping or ridging during forming processes. It also helps stabilize the alloy and prevent the formation of carbides that can weaken its structure.
- Carbon (C): A low carbon content is important in maintaining the stainless steel’s corrosion resistance by minimizing the formation of chromium carbides, which can lead to intergranular corrosion.
436 Stainless Steel Properties
Key Features
Corrosion Resistance: 436 stainless steel offers excellent corrosion resistance in environments containing chlorides and mild acids, making it ideal for use in automotive exhaust systems and other challenging environments.
Formability: The alloy’s formability is one of its main advantages, as it can be stretched, bent or shaped into forms with no loss of structural integrity.
Magnetic: As a ferritic stainless steel, 436 is magnetic when annealed and cold rolled.
Oxidation Resistance: With the addition of molybdenum, 436 stainless steel can withstand high temperatures without scaling.
Weldability: 436 stainless steel is highly weldable, and its performance during welding is improved by the addition of columbium, which minimizes the risk of intergranular corrosion at the weld joints.
Physical Properties
Property | Details |
Density | 7.74 g/cm³ |
Melting Range | 1427 – 1510°C |
Specific Heat Capacity | 0.460 J/g-°C (0-100°C) |
Thermal Conductivity | 23.9 W/m-K (at 100°C)26.0 W/m-K (at 500°C) |
Coefficient of Thermal Expansion | 10.4 × 10⁻⁶ µm/m-°C (0-100°C) |
Electrical Resistivity | 23.68 µΩ-cm (at 20°C) |
Magnetic Permeability | 400 – 700 |
Mechanical Properties
Property | Details |
Ultimate Tensile Strength | 77 ksi (531 MPa) |
Yield Strength (0.2% Offset) | 53 ksi (365 MPa) |
Elongation in 2 inches | 22% |
Hardness (Rockwell B) | 89 Rb (maximum) |
Modulus of Elasticity | 29 × 10³ ksi (200 GPa) |
Reduction of Area | 77% |
Tensile Strength at Elevated Temperature | 134 MPa (at 650°C) 66 MPa (at 760°C) 34 MPa (at 870°C) |
Yield Strength at Elevated Temperature | 114 MPa (at 650°C)52 MPa (at 760°C)28 MPa (at 870°C) |
Forms of 436 Stainless Steel
436 Stainless steel is produced in various forms, each suitable for a specific use. The versatility of these forms makes the alloy popular in various industries.
- Coil: Available in large quantities, stainless steel coils are commonly used in continuous manufacturing processes, where long lengths of material are needed.
- Strip: Narrow strips of 436 stainless steel are used in precision applications, such as in the automotive and aerospace industries.
- Foil: Ultra-thin foils are often required in electronics or other applications where material thickness must be kept to a minimum.
- Sheet and Plate: Sheet and plate are used to manufacture larger components in a wide range of thicknesses that can be cut or formed into a variety of shapes.
- Wire: Stainless steel wire is used in welding applications and to produce fine components for a variety of industrial uses.
Applications of 436 Stainless Steel
Due to its combination of formability, corrosion resistance, and heat resistance, 436 stainless steel is used in a wide range of industries.
Automotive Industry: A primary use for 436 Stainless Steel is in automotive exhaust systems because of its corrosion and temperature resistance.
Aerospace Industry: 436 Stainless Steel is used in components such as exhaust pipes and clamps which need high strength and oxidation resistance, especially in high temperature environments.
Architectural Applications: 436 stainless steel is used in architectural screens and other decorative structures. It resists corrosion while maintaining an attractive appearance, making it a popular option for outdoor structures.
Household Appliances: The alloy’s corrosion resistance and formability make it ideal for use in sinks, countertops, and other kitchen appliances.
Electrical and Heat-Resistant Components: With its efficient thermal conductivity, it is ideal for use in heat exchangers and other components that require efficient heat transfer.
Pros and Cons of 436 Stainless Steel
Advantages
- Excellent Corrosion Resistance: Thanks to its chromium and molybdenum content, 436 stainless steel performs exceptionally well in environments that contain chlorides, acids, and other corrosive elements.
- Good Formability: The alloy enables complex shapes to be made easily without the risk of severe cracking or fracture.
- High-Temperature Resistance: Withstanding temperatures up to 870°C, it is ideal for use in automotive exhaust systems and other high-temperature environments.
- Weldability: 436 stainless steel can be welded using common welding techniques, and the addition of columbium reduces the risk of intergranular corrosion at weld seams.
- Cost-Effective: Compared to austenitic stainless steels, 436 offers a more affordable option for industries looking to balance performance with cost.
Disadvantages
- Susceptible to Roping: Although the addition of columbium reduces the tendency for ridging or roping, it can still occur during forming processes if not carefully managed.
- Not Suitable for Marine Environments: Despite its enhanced corrosion resistance, 436 stainless steel is not recommended for use in environments with constant exposure to seawater.
- Magnetic: While the magnetic properties of 436 stainless steel can be beneficial in some applications, they may pose challenges in environments that require non-magnetic materials.
Processing Methods of 436 Stainless Steel
Forming
- Cold Forming: 436 stainless steel offers good formability, especially for applications involving bending and stamping. It can be used in deep drawing and complex shapes without cracking, due to its higher ductility compared to some other ferritic grades.
- Deep Drawing: Due to its formability, 436 is widely used in deep-drawn parts such as automotive components and kitchen sinks.
Welding
- Weldability: 436 stainless steel can be welded using common methods such as TIG, MIG, and resistance welding. It is less prone to grain growth and intergranular corrosion due to its stabilized composition with niobium (columbium) or titanium.
- Precautions: Post-weld heat treatment or annealing may be required to avoid embrittlement and to maintain corrosion resistance in welded areas.
Cutting
- Laser Cutting: 436 stainless steel can be cut using laser methods, particularly effective for thin sections, allowing for clean and precise cuts.
- Plasma Cutting: This method works well for thicker sections but may introduce heat-affected zones.
- Mechanical Cutting: Shearing, sawing, or water jet cutting can be used for 436 stainless steel, especially when avoiding heat impact is necessary for maintaining corrosion resistance.
Hot Working
- Hot Forging: Forging of 436 stainless steel should be done at temperatures between 1100°C and 1200°C (2012°F to 2192°F). After forging, annealing is required to relieve internal stresses and restore ductility.
- Hot Rolling: Hot rolling can also be performed at elevated temperatures, but similar to forging, annealing is required afterward to soften the material and enhance corrosion resistance.
- Hot Bending: For applications requiring bending at high temperatures, it can be formed, but controlled cooling is essential to avoid cracking.
Cold Working
- Cold Rolling: 436 stainless steel responds well to cold rolling, which improves its surface finish and mechanical properties. However, it may need intermediate annealing if significant deformation occurs to prevent cracking.
- Cold Drawing: Wire and tubing can be drawn from 436 stainless steel, with care taken to prevent excessive hardening.
- Cold Bending: Due to its good ductility, 436 can be cold bent into desired shapes, but for tight bends or complex shapes, annealing might be required to restore formability.
Heat Treatment
- Annealing: Annealing should be performed at 760°C to 815°C (1400°F to 1500°F), followed by rapid cooling to prevent excessive grain growth and maintain mechanical properties. Annealing is often done after cold working to restore ductility.
- Stress Relieving: Stress-relieving can be performed at lower temperatures to reduce internal stresses from forming or welding without affecting the microstructure.
- Hardening: Like other ferritic stainless steels, 436 cannot be hardened by heat treatment; strength improvements are primarily achieved through cold working.
Surface Treatment
- Pickling and Passivation: After welding or hot working, pickling is necessary to remove surface oxide layers, and passivation helps enhance corrosion resistance by removing surface contaminants.
- Polishing: 436 stainless steel can be mechanically polished to achieve smooth, reflective finishes, which is common in decorative and automotive applications.
- Electropolishing: This method can be used to remove surface imperfections, creating a smooth, bright finish while enhancing corrosion resistance.
436 Stainless Steel Manufacturer – SteelPRO Group
SteelPRO Group is a top manufacturer of 436 stainless steel and a preferred partner for sourcing high-performance 436 stainless steel products because of its commitment to quality, sustainability, and customer satisfaction.
Comprehensive Product Line: SteelPRO Group offers 436 stainless steel in a variety of forms, including coils, plates, strips, and wires.
Advanced Manufacturing Processes: The company utilizes cutting-edge technology and sophisticated manufactured processes to provide assurance that each product meets strict standards of quality and reliability for the industry.
Rigorous Quality Control: SteelPRO Group’s stringent quality controls ensure that all 436 stainless steel products provide consistent performance even in demanding environments. Each product is inspected to meet or exceed customer expectations.
Sustainability and Efficiency: The SteelPRO Group is focused on sustainable production practices that minimize waste and energy use while adhering to modern environmental standards.
Customization and Flexibility: SteelPRO Group can customize its products to specific project requirements, offering flexibility in size, finish, and packaging to ensure customers receive the products they need.
Industry Expertise and Support: SteelPRO Group has a deep understanding of the industries it serves and provides expert technical support to help customers select the right materials for their applications.
- Stainless Steel Grades
- 300 Series Stainless Steel
- 303 Stainless Steel
- 304 Stainless Steel
- 305 Stainless Steel
- 308 Stainless Steel
- 316 Stainless Steel
- 316N Stainless Steel
- 409 Stainless Steel
- 410 Stainless Steel
- 416 Stainless Steel
- 420 Stainless Steel
- 430 Stainless Steel
- 410HT And 410L Stainless Steels
- 410S Stainless Steel
- 440 Stainless Steel
- 436 Stainless Steel
- 301 Stainless Steel
- 201 Stainless Steel
- 202 Stainless Steel
- 444 Stainless Steel
- 405 Stainless Steel
- 302 Stainless Steel
- 309 Stainless Steel
- 314 Stainless Steel
- 321 Stainless Steel
- 347 Stainless Steel
- 408 Stainless Steel
- 422 Stainless Steel
- 431 Stainless Steel
- 434 Stainless Steel
- 414 Stainless Steel
- 430FR Stainless Steel
- 13-8 PH Stainless Steel
- 317 | 317L Stainless Steel
- 616 Stainless Steel
- 630 Stainless Steel
- 904L Stainless Steel
- A2 Stainless Steel
- 304 vs 304L Stainless Steel
- 304 VS 316 Stainless Steel
- 304 vs 409 Stainless Steel
- 304 vs 430 Stainless Steel
- 410 Stainless Steel vs 304
- 18/0 vs 18/10
- 18/0 Stainless Steel
- 18/8 Stainless Steel
- 18/10 Stainless Steel
Comparisons